普通车床主轴变速箱设计
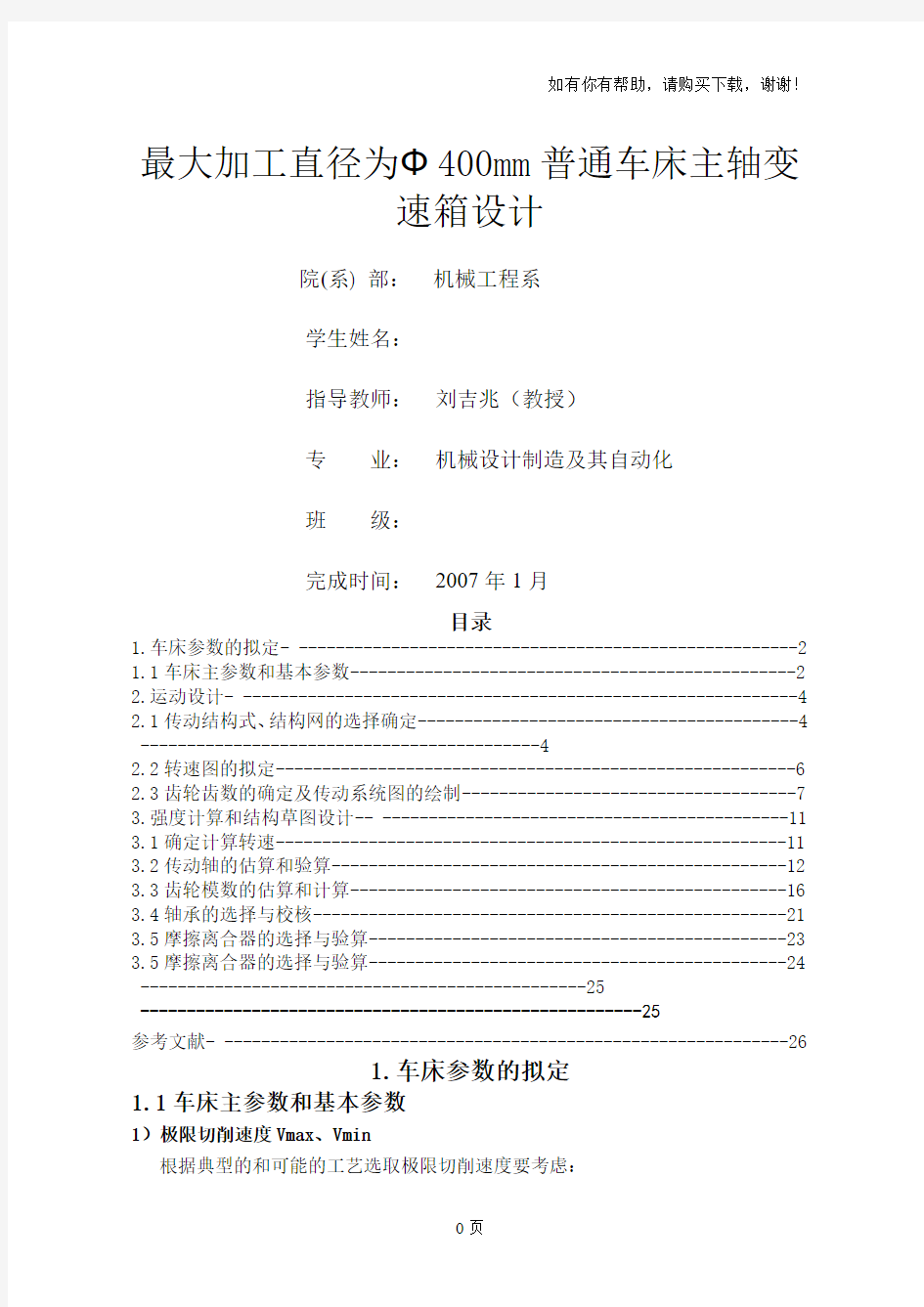

最大加工直径为Ф400mm普通车床主轴变
速箱设计
院(系) 部:机械工程系
学生姓名:
指导教师:刘吉兆(教授)
专业:机械设计制造及其自动化
班级:
完成时间:2007年1月
目录
1.车床参数的拟定- ------------------------------------------------------2
1.1车床主参数和基本参数------------------------------------------------2
2.运动设计- ------------------------------------------------------------4 2.1传动结构式、结构网的选择确定-----------------------------------------4 -------------------------------------------4
2.2转速图的拟定--------------------------------------------------------6
2.3齿轮齿数的确定及传动系统图的绘制------------------------------------7
3.强度计算和结构草图设计-- --------------------------------------------11 3.1确定计算转速-------------------------------------------------------11 3.2传动轴的估算和验算-------------------------------------------------12 3.3齿轮模数的估算和计算-----------------------------------------------16 3.4轴承的选择与校核---------------------------------------------------21 3.5摩擦离合器的选择与验算---------------------------------------------23 3.5摩擦离合器的选择与验算---------------------------------------------24 ------------------------------------------------25
------------------------------------------------------25
参考文献- -------------------------------------------------------------26
1.车床参数的拟定
1.1车床主参数和基本参数
1)极限切削速度Vmax、Vmin
根据典型的和可能的工艺选取极限切削速度要考虑:
允许的切速极限参考值如下:
根据给出条件,取Vmax=150 m/min 螺纹加工和铰孔时取 Vmin=4 m/min
2)主轴的极限转速
计算车床主轴极限转速时的加工直径,按经验分别取K=0.5,Rn=0.25。则主轴极限转速应为:
取标准数列数值,即m ax n =1250r/min
在min n 中考虑车螺纹和铰孔时,其加工的最大直径应根据实际加工情况选取50mm 左右。
min n =
8.3140
14.34
10001000max min =??=d v πr/min
取标准数列数值,即min n =28r/min
转速范围Rn=
min
max
n n 转速范围Rn=min max n n =28
1250
=44.64r/min
取41.1=? Z=41
.1lg 64
.44lg 1lg lg 1+=+
?n R =12 考虑到设计的结构复杂程度要适中,故采用常规的扩大传动。并选级数Z=12,各级转速数列可直接从标准的数列表中查出,按标准转速数列为:
28,40,56,80,112,160,224,315,450,630,900,1250 3)主轴转速级数Z 和公比Φ 已知
Rn=min
max n n
Rn=ΦZ-1
且Z=2a x3b
a 、
b 为正整数,即Z 应可以分解为2和3的因子,以便用2、3联滑移齿轮实现变速。
取Z=12级 则Z=223?
m ax n =1250 m in n =28 Rn=min
max
n n =44.64
综合上述可得:主传动部件的运动参数
1250max =n m in n =28 Z=12 Φ=1.41
4)主电机功率——动力参数的确定
合理地确定电机功率N ,使机床既能充分发挥其性能,满足生产需要,又不致使电机经常轻载而降低功率因素。
中型普通车床典型重切削条件下的用量 刀具材料:YT15工件材料45号钢,切削方式:车削外圆 查表可知:切深a p =3.5mm 进给量f(s)=0.35mm/r 切削速度V=90m/min 功率估算法用的计算公式 a 主切削力:
Fz=1900apf 0.75=190035.05.3??0.75=3026N
b 切削功率:
N 切=
61200V F Z KW=61200
90
3026?KW=4.45KW
c 估算主电机功率:
N=
总切ηN =8
.045.4=5.5KW 可选取电机为:Y132S-4额定功率为5.5KW ,满载转速为1440r/min.
2.运动设计
2.1传动结构式、结构网的选择确定
级数为Z 的传动系统由若干个顺序的传递组组成,各传动组分别有Z1、Z2、Z3、…个传动副.即
Z=Z 1Z 2Z 3…
传动副数由于结构的限制以2或3为适合,即变速级数Z 应为2和3的因子: 即
Z=2a ?3b
实现12级主轴转速变化的传动系统可以写成多种传动副的组合: 1) 12=3×4 2) 12=4×3 3) 12=3×2×2 4) 12=2×3×2
5) 12=2×2×3
按照传动副“前多后少”的原则选择Z=3×2×2这一方案,但主轴换向采用双向片式摩擦离合器结构,致使Ⅰ轴的轴向尺寸过大,所以此方案不宜采用,而应先择12=2×3×2。
方案4)是比较合理的 12=2×3×2
2.1.2 传动系统扩大顺序的安排
12=2×3×2的传动副组合,其传动组的扩大顺序又可以有6种形式: 1) 12=21×32×26 2) 12=21×34×22 3) 12=23×31×26 4) 12=26×31×23 5) 12=22×34×21 6) 12=26×32×21
根据级比指数分配要“前密后疏”的原则,应选用Z=12×23×62这一方案,然而对于我们所设计的结构将会出现两个问题:
第一变速组采用降速传动时,由于摩擦离合器径向结构尺寸限制,使得Ⅰ轴上的齿轮直径不能太小,Ⅱ轴上的齿轮则会成倍增大。这样,不仅使Ⅰ-Ⅱ轴间中心距加大,而且Ⅰ-Ⅱ轴间的中心距也会辊大,从而使整个传动系统结构尺寸增大。这种传动不宜采用。
如果第一变速组采用升速传动,则Ⅰ轴至主轴间的降速传动只能同后两个变速组承担。为了避免出现降速比小于允许的杉限值,常常需要增加一个定比降速传动组,使系统结构复杂。这种传动也不是理想的。
如果采用Z=32×13×62这一方案则可解决上述存在的问题。
2.1.3 绘制结构网
图2.1结构网
2.1.4 传动组的变速范围的极限值
齿轮传动最小传动比Umin ≥1/4,最大传动比Umax 2≤,决定了一个传动组的最大变速范围rmax=umax/umin 8≤。
因此,要按照下表,淘汰传动组变速范围超过极限值的所有传动方案。 极限传动比及指数X,X ,值为:
正常连续的顺序扩大组的传动的传动结构式为: Z=Z1[1]?Z2[Z1]?Z3[Z1?Z2] 最后扩大组的变速范围
按照r 8≤原则,导出系统的最大级数Z 和变速范围R n 为:
表2.2
最后扩大组的传动副数目Z3=2时的转速范围远比Z3=3时大
因此,在机床设计中,因要求的R 较大,最后扩大组应取2更为合适。
同时,最后传动组与最后扩大组往往是一致的。安装在主轴与主轴前一传动轴的具有极限或接近传动比的齿轮副承受最大扭距,在结构上可获得较为满意的处理,这也就是最后传动组的传动副经常为2的另一原因。
2.2 转速图的拟定
运动参数确定以后,主轴各级转速就已知,切削耗能确定了电机功率。在此基础上,选择电机型号,确定各中间传动轴的转速,这样就拟定主运动的转速图,使主运动逐步具体化。
1)电机功率N :
中型机床上,一般都采用三相交流异步电动机作为动力源。 根据机床切削能力的要求确定电机功率:
N=5.5KW
2) 电机转速d n :
选用时,要使电机转速d n 与主轴最高转速m ax n 和I 轴转速相近或相宜,以免采用过大的升速或过小的降速传动。
d n =1440r/min
3)分配降速比:
该车床主轴传动系统共设有四个传动组其中有一个是带传动。根据降速比分配应“前慢后快”的原则以及摩擦离合器的工作速度要求,确定各传动组最小传动比。
u 总=m in n /E n =28/1440=1/51.4
分配总降速传动比时,要考虑是否增加定比传动副,以使转速数列符合标准和有利于减小齿数和减小径向与轴向尺寸,必须按“前慢后快”的原则给串联的各变速器分配最小传动比。
a 决定轴Ⅲ-Ⅳ的最小降速传动比主轴上的齿轮希望大一些,能起到飞轮的作用,所以最后一个变速组的最小降速传动比取极限1/4,公比ψ=1.41,1.414=4,因此从
Ⅳ轴的最下点向上4格,找到Ⅲ上对应的点,连接对应的两点即为Ⅲ-Ⅳ轴的最小传动比。
b 决定其余变速组的最小传动比根据“前慢后快”的原则,轴Ⅱ-Ⅲ间变速组取umin=1/ψ3,即从Ⅲ轴向上3格,同理,轴Ⅰ-Ⅱ间取u=1/ψ3,连接各线。
c 根据个变速组的传动比连线按基本组的级比指数x 0=3,第一扩大组的级比指数x 1=1,第二扩大组的级比指数x 3=6,画出传动系统图如2.2所示
图2.2转速图
2.3 齿轮齿数的确定及传动系统图的绘制
可用计算法或查表确定齿轮齿数,后者更为简便,根据要求的传动比u 和初步定出的传动副齿数和Z S ,查表即可求出小齿轮齿数。 选择时应考虑:
1.传动组小齿轮应保证不产生根切。对于标准齿轮,其最小齿数[]min min Z Z ≥=17
2.齿轮的齿数和Z S 不能太大,以免齿轮尺寸过大而引起机床结构增大,一般推荐齿
数和Z S ≤100-120,常选用在100之内。 3.同一变速组中的各对齿轮,其中心距必须保证相等。
4.保证强度和防止热处理变形过大,齿轮齿根圆到键槽的壁厚
5. 保证主轴的转速误差在规定的范围之内。
图2.3 齿轮的壁厚
2.3.2 变速传动组中齿轮齿数的确定
1)确定齿轮齿数 1. 用计算法确定第一个变速组中各齿轮的齿数 Z j +Z j ’=Z S
Z j /Z j ’ =u j 其中
Z j ——主动齿轮的齿数 Z j ’——被动齿轮的齿数 u j ——一对齿轮的传动比 Z S ——一对齿轮的齿数和
为了保证不产生根切以及保证最小齿轮装到轴上或套筒上具有足够的强度,最小齿轮必然是在降速比最大的传动副上出现。 把Z 1的齿数取大些: 取Z 1=Z min =20则
Z 2=
85
.2/12021 u Z =58 齿数和Z S =Z 1+Z 2=20+58=78 同样根据公式
Z 3=4Z =39 2. 用查表法确定第二变速组的齿数
a 首先在u 1、u 2、u 3中找出最小齿数的传动比u 1
b 为了避免根切和结构需要,取Z min =24
c 查表找到u 1=1/1.413的倒数2.82的行找到Z min =24查表最小齿数和为92
d 找出可能的齿数和Z S 的各种数值,这些数值必须同时满足各传动比要求的齿轮齿数
能同时满足三个传动比要求的齿数和有
Z S =92 96 99 102
e 确定合理的齿数和
Z S =102 依次可以查得
Z 5=27 Z 6=75 Z 7=34 Z 8=68 Z 9=42 Z 10=60
同理可得其它的齿轮如下表所示:
由于确定的齿轮齿数所得的实际转速与传动设计的理论转速难以完全相符,需要验算主轴各级转速,最大误差不得超过±10(ψ-1)%。
主轴各级实际转速值用下式计算
n实=n E×(1-ε)×u a×u b×u c×u d
其中
ε——滑移系数ε=0.2
u a u b u c u d分别为各级的传动比12/45
转速误差用主轴实际转速与标准转速相对误差的绝对值表示
⊿n=|
实际标准
实际n n
n
∣≤±10(ψ-1)%
n实1=1440×0.625×0.98×0.35×0.35×0.25=27.8
⊿n=∣(27.8-28)/28∣=0.7%
同样其他的实际转速及转速误差如下:
表2.4
3)齿轮的布置
为了使变速箱结构紧凑以及考虑主轴适当的支承
距离和散热条件,其齿轮的布置如下图2.4所示。
4)绘制主传动系统图
按照主传动转速图以及齿轮齿数绘制主传动系统
图如下2.5所示
图
2.4 齿轮结构的布置
图2.5主传动系统图
3 .强度计算和结构草图设计
3.1 确定计算转速
n
j
=nminψz/3-1
z=12
n
j
=nminψ3
=28×2.82=79r/min
Ⅲ轴上的6级转速分别为:112、160、224、315、450、630r/min.主轴在79r/min 以上都可以传递全部功率。 Ⅲ轴经Z 13-Z 14传递到主轴,这时从112r/min 以上的转速全部功率,所以确定最低转速112r/min 为Ⅲ轴的计算转速。按上述的方法从转速图中分别可找到计算转速:Ⅱ轴为315r/min,Ⅰ轴为900r/min,电动机轴为1440r/min.
Z 10安装在Ⅲ轴上,从转速图可见Z 10齿轮本身有6种转速,其要传递全部的功率的计算转速为112r/min 。
同样可以确定其余齿轮的转速如下表3.1所示:
表3.1
3.2传动轴的估算和验算
传动轴直径按扭转刚度用下列公式估算传动轴直径:
4
]
[94?j n N
d = mm 其中:N —该传动轴的输入功率
ηd N N =KW
N d —电机额定功率;
η—从电机到该传动轴之间传动件的传动效率的乘积
j n —该传动轴的计算转速r/min
][?—每米长度上允许的扭转角(deg/m),可根据传动轴的要求选取如表3.2
所示
表3.2
对于一般的传动轴,取][?=1.5
28.596.05.5=?==ηd N N KW j n =900 r/min
5.285
.11000
40090028
.591
4
1=??=d mm
取321=d mm
25.5995.096.05.52=??==ηd N N KW j n =425 r/min
4
25
.1100040031525
.591
??=d =37 mm
取362=d
20.599.0995.096.05.53=???==ηd N N KW j n =150 2.425
.11000
40015020
.591
4
3=??=d mm
采用花键轴结构,即将估算的传动轴直径d 减小7%为花键轴的直径,在选相近的标准花键。
d 1’=29.3×0.93=27.0 d 2’=34.5×0.93=32.0 d 3’=42.2×0.93=40.0
查表可以选取花键的型号其尺寸)741144(-??-GB b d D Z 分别为
1d 轴取 6-28×32×7
2d 轴取 8-32×36×6
3d 轴取 8-42×46×80
3.2.2 主轴的设计与计算
主轴组件结构复杂,技术要求高。安装工件的主轴参与切削成形运动,此,它的精度和性能性能直接影响加工质量(加工精度与表面粗糙度)。 1)主轴直径的选择
查表可以选取前支承轴颈直径
D 1=90 mm
后支承轴颈直径
D 2=(0.7~0.85)D 1=63~77 mm
选取
D 2=70 mm
2)主轴内径的选择
车床主轴由于要通过棒料,安装自动卡盘的操纵机构及通过卸顶尖的顶杆必须是空心轴。
确定孔径的原则是在满足对空心主轴孔径要求和最小壁厚要求以及不削弱主轴刚度的要求尽可能取大些。
推荐:普通车床d/D(或d 1/D 1)=0.55~0.6 其中
D ——主轴的平均直径,D=(D 1+D 2)/2 d 1——前轴颈处内孔直径
d=(0.55~0.6)D=44~48 mm
所以,内孔直径取45mm 3)前锥孔尺寸
前锥孔用来装顶尖或其它工具锥柄,要求能自锁,目前采用莫氏锥孔。选择如下: 莫氏锥度号取5号 标准莫氏锥度尺寸 大端直径 D=44.399 4)主轴前端悬伸量的选择
确定主轴悬伸量a 的原则是在满足结构要求的前提下,尽可能取小值。 主轴悬伸量与前轴颈直径之比a/D=0.6~1.5
a=(0.6~1.5)D 1=54~135 mm
所以,悬伸量取100mm 5)主轴合理跨距和最佳跨距选择
根据表3-14 见《金属切削机床设计》计算前支承刚度A K 。 前后轴承均用3182100系列轴承,并采用前端定位的方式。 查表 4
.111700D K A ?=
A K =1700×901.4
=9.26×105
N/mm 因为后轴承直径小于前轴承,取
4.1=B
A
K K K B =6.61×105
N/mm
其中
B
A
K K 为参变量 综合变量3
a K EI
A =
η
其中
E ——弹性模量,取E=2.0×105 N/mm 2
I ——转动惯量,I=π(D 4-d 4)/64=3.14×(804-454)=1.81×106mm 4
3a K EI A =η =3
56
5100
1026.91081.1100.2????? =0.3909
由图3-34中,在横坐标上找出η=0.3909的点向上作垂线与4.1=B
A
K K 的斜线相交,由交点向左作水平线与纵坐标轴相交,得L 0/a=2.5。
所以最佳跨距L 0
L 0=2.5a=2.5×100=250 mm 又因为合理跨距的范围
L 合理=(0.75~1.5)L 0=187.5~375 mm
所以取L=260 mm 6)主轴刚度的验算
对于一般机床主轴,主要进行刚度验算,通常能满足刚度要求的主轴也能满足强度要求。
对于一般受弯矩作用的主轴,需要进行弯矩刚度验算。主要验算主轴轴端的位移y 和前轴承处的转角θA 。
图3.1 主轴支承的简化
切削力 Fz=3026N
挠度 y A =EI a L a F z 3)
(2+
=6
521081.1100.23)
100260(1003026????+??
=0.01
[y]=0.0002L=0.0002×260=0.052 y A <[y]
倾角 θA =EI
a L Fa 6)
32(+
=6
510
181100.26)10032602(1003026?????+??? =0.00011
前端装有圆柱滚子轴承,查表[θA ]=0.001rad θA <[θA ] 符合刚度要求。
3.2.3 主轴材料与热处理
材料为45钢,调质到220~250HBS ,主轴端部锥孔、定心轴颈或定心圆锥面等部位局部淬
硬至HRC50~55,轴径应淬硬。
3.3 齿轮模数的估算和计算
根据齿轮弯曲疲劳的估算:
3
32j
zn N
m ≥ωmm 齿面点蚀的估算:
3
370j
n N
A ≥mm 其中j n 为大齿轮的计算转速,A 为齿轮中心距。 由中心距A 及齿数1z 、2z 求出模数:2
12z z A
m j +=
mm 根据估算所得ωm 和j m 中较大的值,选取相近的标准模数。 1)齿数为32与64的齿轮
N=5.28KW
85.1425
3228
.5323
=?≥ωm mm
= 5.85425
28
.53703
=mm 212z z A m j +=
78.164
325
.852=+?=mm
取模数为2
2)齿数为56与40的齿轮
54.1850
5628
.5323
=?≥ωm mm
=681850
28
.53703
=mm 212z z A m j +=
42.140
5668
2=+?=mm
取模数为2
3)齿数为27与75的齿轮 N=5.25KW
48.21507525
.5323
=?≥ωm mm
=121150
25
.53703
=mm 212z z A m j +=
37.275
27121
2=+?=mm
取模数为2.5
4)齿数为34与68的齿轮 N=525KW
29.2212
6825
.5323
=?≥ωm mm
=8.107212
25
.53703
=mm 212z z A m j +=
11.268
348
.1072=+?=mm
取模数为2.5
5)齿数为42与60的齿轮 N=5.25KW
12.2300
6025
.5323
=?≥ωm mm
3
370j
n N
A ≥=1.9630025.53703
=mm 212z z A m j +=
88.160
421.962=+?=mm
取模数为2.5
6)齿数为23与91的齿轮
N=5.20KW
32.2150
9120
.5323
=?≥ωm mm
=0.121150
20
.53703
=mm
212z z A m j +=
12.291
230
.1212=+?=mm
取模数为2.5
7)齿数为76与38的齿轮
N=5.20KW 46.21507620
.5323
=?≥ωm mm
=6.120150
20
.53703
=mm 212z z A m j +=
12.238
766
.1202=+?=mm
取模数为2.5
3.3.2 齿轮模数的验算
结构确定以后,齿轮的工作条件、空间安排、材料和精度等级等都已确定,才可能核验齿轮的接触疲劳和弯曲疲劳强度值是否满足要求。 根据齿轮的接触疲劳计算齿轮模数公式为:
3
2
2
1321][)1(16300j
j m S j n i z N K K K K i m σψ±=mm
根据齿轮的弯曲疲劳强度计算齿轮模数公式为:
]
[275
1321ωωσj m s n Y z N
K K K K m ψ=mm
式中:N---计算齿轮传递的额定功率
J N --计算齿轮(小齿轮)的计算转速r/min
m ψ---齿宽系数m
b
m =ψ,m ψ常取6~10;
1z ---计算齿轮的齿数,一般取传动中最小齿轮的齿数;
i ---大齿轮与小齿轮的齿数比,11
2
≥=z z i ;“+”用于外啮合,“-”号用于内啮合;
Ks ---寿命系数,q N n r K K K K Ks =;………………………………………3.5
T K ---工作期限系数,m
T C nT
K 0
60=;………………………………………3.6
齿轮等传动件在接触和弯曲交变载荷下的疲劳曲线指数m 和基准循环次数Co n---齿轮的最低转速r/min;
T---预定的齿轮工作期限,中型机床推荐:T=15000~20000h;
n K ---转速变化系数 N K ---功率利用系数
q K ---材料强化系数。幅值低的交变我荷可使金属材料的晶粒边界强化,起着
阻止疲劳细缝扩展的作用;
S K (寿命系数)的极限min max ,S S K K
当min min max S S S S S K K K K K K =<≥时,取时,则取;
1K ---工作情况系数。中等冲击的主运动:1K =1.2~1.6; 2K ---动载荷系数 3K ---齿向载荷分布系数
Y----齿形系数;
][ωσ、][j σ---许用弯曲、接触应力MPa
1)齿数为32与64的齿轮
28.5=N KW
64322=?==mz d mm
节圆速度85.260000
850
6460000
=??=
=
ππn
d V m/s
由表8可得:取精度等级为7级 。 2K =1.2 2.11=K 由表9得:3K =1
n K =0.71 60.0=w K 78.0=q K
由表可知 max K K S > 所以 取Ks=0.6
由表11 许用应力知,可取齿轮材料为45 整淬
][ωσ=1100MPa ][j σ=320MPa
由表10可知 可查得 Y=0.45 所以 模数取2适合要求。
同样可以校核其它齿轮的模数也符合要求。
3.4 轴承的选择与校核
机床传动轴常用的滚动轴承有球轴承和滚锥轴承。在温升。空载功率和噪音等方面,球轴承都比滚锥轴承优越。而且滚锥轴承对轴的刚度、支承孔的加工精度要求
都比较高,异常球轴承用得更多。但滚锥轴承的内外圈可以公开。装配方便,间隙容易调整。所以有时在没有轴向力时,也常采用这种轴承。选择轴承的型式和尺寸,首先取决于承载能力,但也要考虑其它结构条件。即要满足承载能力要求,又要符合孔的加工工艺,可以用轻、中、或重系列的轴承来达到支承孔直径的安排要求。花键轴两端装轴承的轴颈尺寸至少有一个应小于花键的内径,一般传动轴承选用G 级精度。
在传动轴上选择6200系列的深沟球轴承,其具体的型号和尺寸如下表3.3所示
表3.3
主轴的前轴承选取3182100系列双列向心短圆柱滚子轴承。这种轴承承载能力大,内孔有1:12锥度,磨擦系数小,温升低,但不能承受轴向力,必须和能承受轴向力的轴承配合使用,因此整个部件支承结构比较复杂。
图3.1
3.4.3 轴承间隙调整
为了提高主轴回转精度和刚度,主轴轴承的间隙应能调整。把轴承调到合适的负间隙,形成一定的预负载,回转精度和刚度都能提高,寿命、噪声和抗振性也有改善。预负载使轴承内产生接触变形,过大的预负载对提高刚度没有明显效果,而磨损发热量和噪声都会增大,轴承寿命将因此而降低。
调整结构形式如下图所示:
图3.2 调整说明:
转动调整螺母,使内圈向大端移动。
特点:结构简单。移动量完全靠经验,一旦调整过紧,难以把内圈退回。 1) 滚动轴承的疲劳寿命验算 或()N C F K K K K f f C l Hn Hp A n
h
j ≤=
h L —额定寿命 (h) C —额定动载荷(N) j C —动载荷(N)
T —滚动轴承的许用寿命(h),一般取10000~15000(h) ε—寿命指数,对球轴承 ε=3 ,对滚子轴承ε=10/3
n f —速度系数,ε
c
n n f 3100
= n —轴承的计算转数 r/min h f —寿命系数, ε
500
h
h L f = A K —使用系数 功率利用系数—Hp K
Hn K —转化变化系数 l K —齿轮轮换工作系数 F —当量动负荷(N)
2)滚动轴承的静负荷验算
0000C F K C j ≤= j C 0—静负荷 (N) 0C —额定静负荷 (N)
K —安全系数
F —当量静载荷 (N)
取其中较大值或r a F F F Y F X F =+=00000 径向负荷—r F (N)
0X 、0Y —静径向,轴向系数
校验第Ⅰ根轴上的轴承 T=10000h
查轴承样本可知,6205轴承的基本额定动载荷
C =212000N 3=ε j n =850 r/min 34.0850
3100
=?=ε
n f
1.1=A K Hn K =096 Hp K =0.8 l K =0.8
=3
30268.08.096.01.134.021*******???
???????
=)(h T ≥
同样可以较核其它轴承也符合要求。
3.5 摩擦离合器的选择与验算
j M ≥K max M =Kx9550
j
ny
n Nm 式中
j M —离合器的额定静力矩(Kgm) K —安全系数
max M —运转时的最大负载力矩
查《机械设计手册》表,取K=2 η=0.96 则f M ≥K max M = 850
96
.05.595500.29550???=?
?j n N K η=118.8 Nm 根据结构需要采用轴装式摩擦片,摩擦片的内径d 应比安装在轴的轴径大2~6mm,
取d=35mm
尺寸如下表3.4所示
表3.4
式中:f-----摩擦片间的摩擦系数; [p]----许用压强MPa ;
D------摩擦片内片外径 mm ; d-------摩擦片外片内径 mm ;
v K ----速度修正系数; z K -----接合面数修正系数;
m K -----接个次数修正系数; K------安全系数。
分别查表
06.0=f []0.1=P ~1.2 90=D mm d =35mm 94.0=V K 85.0=Z K =m K 1.0
=10
摩擦片总数为(z+1)片,即11片,根据具体情况设内为6片,外5片。 计算轴向压力Q
=3.14×1.0×2125×94.02
45
90?-
=5073N
参考文献
[1] 机床主轴变速箱设计指导 清华大学曹金榜等主编 [2] 机床设计图册 东方纺织工学院等主编 [3] 机床设计手册 《机床设计手册》编写组主编 [4] 金属切削机床概论 (教材) [5] 金属切削机床设计 (教材)
车床主轴箱设计说明书
中北大学 课程设计任务书 15/16 学年第一学期 学院:机械工程与自动化学院 专业:机械设计制造及其自动化 学生姓名:王前学号:1202014233 课程设计题目:《金属切削机床》课程设计 (车床主轴箱设计) 起迄日期:12 月21 日~12 月27 日课程设计地点:机械工程与自动化学院 指导教师:马维金讲师 系主任:王彪 下达任务书日期: 2012年12月21日
课程设计任务书
课程设计任务书
目录 1.机床总体设计 (5) 2. 主传动系统运动设计 (5) 2.1拟定结构式 (5) 2.2结构网或结构式各种方案的选择 (6) 2.2.1 传动副的极限传动比和传动组的极限变速范围 (6) 2.2.2 基本组和扩大组的排列顺序 (6) 2.3绘制转速图 (7)
2.5确定带轮直径 (8) 2.6验算主轴转速误差 (8) 2.7 绘制传动系统图 (8) 3.估算传动件参数确定其结构尺寸 (10) 3.1确定传动见件计算转速 (10) 3.2确定主轴支承轴颈尺寸 (10) 3.3估算传动轴直径 (10) 3.4估算传动齿轮模数 (10) 3.5普通V带的选择和计算 (11) 4.结构设计 (12) 4.1带轮设计 (12) 4.2齿轮块设计 (12) 4.3轴承的选择 (13) 4.4主轴主件 (13) 4.5操纵机构、滑系统设计、封装置设计 (13) 4.6主轴箱体设计 (13) 4.7主轴换向与制动结构设计 (13) 5.传动件验算 (14) 5.1齿轮的验算 (14) 5.2传动轴的验算 (16) 5.3花键键侧压溃应力验算 (19)
车床主轴箱课程设计12级转速
目录 一、机床总体设计---------------------------------------------------------------------2 1、机床布局--------------------------------------------------------------------------------------------2 2、绘制转速图-----------------------------------------------------------------------------------------4 3、防止各种碰撞和干涉-----------------------------------------------------------------------------5 4、确定带轮直径--------------------------------------------------------------------------------------5 5、验算主轴转速误差--------------------------------------------------------------------------------5 6、绘制传动系统图-----------------------------------------------------------------------------------6 二、估算传动件参数确定其结构尺寸-------------------------------------------7 1、确定传动见件计算转速--------------------------------------------------------------------------7 2、确定主轴支承轴颈尺寸--------------------------------------------------------------------------7 3、估算传动轴直径-----------------------------------------------------------------------------------7 4、估算传动齿轮模数--------------------------------------------------------------------------------8 5、普通V带的选择和计算-------------------------------------------------------------------------8 三、机构设计--------------------------------------------------------------------------10 1、带轮设计-------------------------------------------------------------------------------------------10 2、齿轮块设计----------------------------------------------------------------------------------------10 3、轴承的选择----------------------------------------------------------------------------------------10 4、主轴主件-------------------------------------------------------------------------------------------10 5、操纵机构-------------------------------------------------------------------------------------------10 6、滑系统设计----------------------------------------------------------------------------------------10 7、封装置设计----------------------------------------------------------------------------------------10 8、主轴箱体设计-------------------------------------------------------------------------------------11 9、主轴换向与制动结构设计----------------------------------------------------------------------11 四、传动件验算-----------------------------------------------------------------------11 1、齿轮的验算----------------------------------------------------------------------------------------11 2、传动轴的验算-------------------------------------------------------------------------------------13 五、设计感想--------------------------------------------------------------------------15 六、参考文献--------------------------------------------------------------------------16
普通车床的主轴箱部件设计最大加工直径250mm最高1440最低90公比1.41
目录 一.设计目的 (2) 二、设计步骤 (2) 1.运动设计 (2) 1.1已知条件 (2) 1.2结构分析式 (2) 1.3 绘制转速图 (4) 1.4 绘制传动系统图 (6) 2.动力设计 (6) 2.1 确定各轴转速 (6) 2.2 带传动设计 (7) 2.3 各传动组齿轮模数的确定和校核 (9) 3. 齿轮强度校核 (11) 3.1校核a传动组齿轮 (12) 3.2 校核b传动组齿轮 (13) 3.3校核c传动组齿轮 (14) 4. 主轴挠度的校核 (15) 4.1 确定各轴最小直径 (15) 4.2轴的校核 (16) 5. 主轴最佳跨距的确定 (16) 5.1 选择轴颈直径,轴承型号和最佳跨距 (17) 5.2 求轴承刚度 (17) 6. 各传动轴支承处轴承的选择 (18) 7. 主轴刚度的校核 (19) 7.1 主轴图: (19) 7.2 计算跨距 (19) 三、总结 (20) 四、参考文献 (20)
一.设计目的 通过机床主运动机械变速传动系统得结构设计,在拟定传动和变速的结构方案过程中,得到设计构思、方案分析、结构工艺性、机械制图、零件计算、编写技术文件和查阅技术资料等方面的综合训练,树立正确的设计思想,掌握基本的设计方法,并具有初步的结构分析、结构设计和计算能力。 二、设计步骤 1.运动设计 1.1已知条件 [1]确定转速范围:主轴最小转速nnim(r/min)=90r/min、nmax (r/min)=2000r/min 主电动机转速(r/min)=1440、P(kw)=4kw [2]最大加工直径φ=250mm [3]确定公比:41 ? .1 = [4]转速级数:10 z = 1.2结构分析式 因为我们的级数是10级,为了实现10级,本次设计中,我打算按12级的主轴箱来计算,让里面其中两组数据一样,最终达到10级
CM6132机械系统设计课程设计精密车床主轴箱与变速箱系统设计说明
目录 绪论 (1) 1.概述 (5) 1.1机床主轴箱课程设计的目的 (5) 1.2设计任务和主要技术要求 (5) 1.3操作性能要求 (6) 2.技术参数确定与方案设计 (6) 2.1原始数据 (6) 2.2开展CM6132功能原理设计 (6) 3.运动设计 (7) 3.1确定转速极速 (7) 3.1.1计算主轴最高转速 (9) 3.1.2计算主轴最低转速 (10) 3.1.3确定主轴标准转速数列 (11) 3.2主电动机的选择 (12) 3.3变速结构的设计 (14) 3.3.1 主变速方案拟定 (14) 3.3.2 拟定变速结构式 (14) 3.3.3拟定变速结构网 (15) 3.3.4 验算变速结构式 (16)
3.4绘制转速图 (17) 3.5 齿轮齿数的估算 (20) 3.6 主轴转速误差 (23) 4.动力设计 (26) 4.1电机功率的确定 (26) 4.2确定各轴计算转速 (26) 4.3 带轮的设计 (27) 4.4传动轴直径的估算 (30) 4.5齿轮模数的确定 (33) 4.6主轴轴颈的直径 (36) 4.6.1主轴悬伸量a (36) 4.6.2主轴最佳跨距0L 的确定和轴承的选择 (36) 4.6.3主轴组件刚度验算 (37) 5. 结构设计 (38) 5.1齿轮的轴向布置 (39) 5.2传动轴及其上传动元件的布置 (40) 5.2.1 I 轴的设计 (42) 5.2.2 II 轴的设计 (42) 5.2.3 III 轴的设计 (42) 5.2.4 带轮轴的设计 (42) 5.2.5 Ⅳ轴的设计 (43) 5.2.6主轴的设计 (43) 5.2.7 主轴组件设计 (43) 5.3齿轮布置的注意问题 (44)
《金属切削机床》课程设计--C616型车床主轴箱设计(全套图纸)
目录 全套图纸加174320523 各专业都有 1.概述和机床参数确定 (1) 1.1机床运动参数的确定 (1) 1.2机床动力参数的确定 (1) 1.3机床布局 (1) 2.主传动系统运动设计 (2) 2.1确定变速组传动副数目 (2) 2.2确定变速组的扩大顺序 (2) 2.3绘制转速图 (3) 2.4确定齿轮齿数 (3) 2.5确定带轮直径 (3) 2.6验算主轴转速误差 (4) 2.7绘制传动系统图 (4) 3.估算传动件参数确定其结构尺寸 (5) 3.1确定传动转速 (5) 3.2确定主轴支承轴颈尺寸 (6) 3.3估算传动轴直径 (6) 3.4估算传动齿轮模数 (6) 3.5普通V带的选择和计算 (7) 4.结构设计 (8) 4.1带轮设计 (8) 4.2齿轮块设计 (8) 4.3轴承的选择 (9) 4.4主轴组件 (9) 4.5操纵机构、滑系统设计、封装置设计 (9) 4.6主轴箱体设计 (9)
4.7主轴换向与制动结构设计 (9) 5.传动件验算 (10) 5.1齿轮的验算 (10) 5.2传动轴的刚度验算 (12) 5.3花键键侧压溃应力验算 (16) 5.4滚动轴承的验算 (16) 5.5主轴组件验算 (17) 6. 主轴位置及传动示意图 (20) 7.总结 (20) 8.参考文献 (21) 1.概述 1机床课程设计的目的 机床课程设计,是在金属切削机床课程之后进行的实践性教学环节。其目的在于通过机床运动机械变速传动系统的结构设计,使学生在拟定传动和变速的结构的结构方案过程中,得到设计构思,方案分析,结构工艺性,机械制图,零件计算,编写技术文件和查阅技术资料等方面的综合训练,树立正确的设计思想,掌握基本的设计方法,并培养学生具有初步的结构分析,结构设计和计算能力。轻型车床是根据机械加工业发展需要而设计的一种适应性强,工艺范围广,结构简单,制造成本低的万能型车床。它被广泛地应用在各种机械加工车间,维修车间。它能完成多种加工工序;车削内圆柱面,圆锥面,成形回转面,环形槽,端面及内外螺纹,它可以用来钻孔,扩孔,铰孔等加工。 1.1 机床运动参数的确定 (1)确定公比φ及Rn 已知最低转速n min =45rpm,最高转速n max =1980rpm,变速级数Z=12,则公比: φ= (n max /n min )1/(Z-1) =(1980rpm/45rpm)1/(12-1)≈1.41 转速 调整范围: Rn=n max /n min =44 (2)求出转速系列 根据最低转速45r/min,最高转速max n=1980r/min,公比φ=1.41,按《金属切屑机床》(戴曙编)表7-1选出标准转速数列: 2000 1400 1000 710 500 355 250 180 125 90 63 45 1.2机床动力参数的确定 已知电动机功率为N=4kw,根据《金属切削机床简明手册》(范云涨、陈兆年编)表11-32选择主电动机为Y112M-4,其主要技术数据见下表1: 表1 Y90L-4技术参数
#C6136机床主轴箱设计说明书14896
C6136型机床主轴箱课程设计说明书系别:交通和机械工程学院 专业:机械设计制造及其自动化 班级:机械10-4班 姓名:富连宇 学号:1008470434 吗 指导老师:赵民 目录 一、设计目的 (1) 二、机床主要技术要求 (1) 三、确定结构方案 (1) 四、运动设计 (1) 4.1确定极限转速 (1) 4.2拟订结构式 (1) 4.3绘制转速图 (2) 4.4 确定齿轮齿数 (2) 4.5 验算主轴转速误差: (3) 4.6 绘制传动系统图 (3) 五、动力设计 (3) 5.1 V带的传动计算 (3) 5.2各传动轴的估算 (4) 5.3齿轮模数确定和结构设计: (5) 5.4摩擦离合器的选择和计算: (6) 5.5结构设计 (7) 六、齿轮强度校核 (8) 6.1、各齿轮的计算转速 (8) 6.2、齿轮校核 (9) 七、主轴刚度校核 (9) 八、主轴最佳跨度确定 (10) 8.1计算最佳跨度 (10) 8.2校核主轴挠度 (10) 8.2主轴图:(略)见附图2 (10) 九、各传动轴支持处轴承选用 (10) 十、键的选择和校核 (10) 1)、轴IV的传递最大转矩 (10) 十一、润滑和密封 (11) 十二、总结 (11) 十三、参考文献 (11) 十四、附 (12)
一、设计目的 通过机床主运动机械变速传动系统得结构设计,在拟定传动和变速的结构方案过程中,得到设计构思、方案分析、结构工艺性、机械制图、零件计算、编写技术文件和查阅技术资料等方面的综合训练,树立正确的设计思想,掌握基本的设计方法,并具有初步的结构分析、结构设计和计算能力。可使我们学会理论联系实际的工作方法,培养独立工作的能力;学会基本的设计的方法;熟悉手册、标准、资料的运用;加强机械制图、零件计算、编写技术文件的能力,学会设计说明书的编写。为接下去的毕业设计、毕业论文积累经验。 二、机床主要技术要求 [1]车床类型为C6136型车床主轴变速箱(采用机械传动结构)。 [2]加工工件最大直径:360mm [3]加工工件最大长度:1500mm [4] 主轴通孔直径:40-50mm [5]主轴前锥孔:莫式5号 [6]主轴采用三相异步电机 [7]主电动机功率为n电额:4kw [8]转速nmin:33.5r/min mmax:1700 r/min n额:1000r/min [9]主轴变速系统实现正传12级变速,反转6级变速(采用摩擦离合器) 三、确定结构方案 [1] 主轴传动系统采用V带、齿轮传动; [2]传动形式采用集中式传动; [3]主轴换向制动采用双向片式摩擦离合器和带式制动器; [4]变速系统采用多联滑移齿轮变速。 四、传动方案 4.1确定极限转速 转速n min:33.5r/min n max:1700 r/min n额:1000r/min 4.2拟订结构式 1)确定变速组传动副数目: 传动副中由于结构的限制以2或3为合适,即变速级数Z应为2和3的因子,为实现12级主轴转速变化的传动系统可以以下多种传动副组合: ①12=3x2x2 ②12=2x2x3 ③12=2ⅹ3ⅹ2等 18级转速传动系统的传动组,选择传动组安排方式时,考虑到机床主轴箱的具体结构、装置性能,主轴上的传动副数主轴对加工精度、表面粗糙度的影响很大,因此主轴上的齿轮少些为好。按照1 符合变速级数、级比规律 2 传动件前多后少3 结构网前密后疏4 第二扩大组变速范围r=8满足变速范围要求
普通车床主轴箱课程设计
课程设计 课程名称:金属切削机床 学院:机械工程学院 专业:机械设计制造及其自动化姓名:学号: 年级:任课教师: 2011年 1月15 日 贵州大学机械工程学院
目录 目录 (2) 一、绪论 (4) 二、设计计算 (5) 1机床课程设计的目的 (5) 2机床主参数和基本参数 (5) 3操作性能要求 (5) 三、主动参数的拟定 (6) 1确定传动公比 (6) 2主电动机的选择 (6) 四、变速结构的设计 (6) 1主变速方案拟定 (6) 2变速结构式、结构网的选择 (7) 1. 确定变速组及各变速组中变速副的数目 (7) 2. 变速式的拟定 (7) 3. 结构式的拟定 (7) 4. 结构网的拟定 (8) 5. 结构式的拟定 (8) 6. 结构式的拟定 (9) 7. 确定各变速组变速副齿数 (10) 8. 绘制变速系统图 (11) 五、结构设计 (12) 1.结构设计的内容、技术要求和方案 (12) 2.展开图及其布置 (12) 3.I轴(输入轴)的设计 (12) 4.传动轴的设计 (13) 5.主轴组件设计 (14) 1. 内孔直径d (14) 2. 轴径直径 (15) 3. 前锥孔直径 (15) 4. 主轴悬伸量a和跨距 (15) 5. 主轴轴承 (15) 6. 主轴和齿轮的联接 (16) 7. 润滑和密封 (16) 8. 其它问题 (16) 六、传动件的设计 (17) 1带轮的设计 (17)
2传动轴直径的估算 (20) 1 确定各轴计算转速 (20) 2传动轴直径的估算 (21) 3各变速组齿轮模数的确定 (22) 4片式摩擦离合器的选择和计算 (25) 七、本文工作总结 (27) 参考文献 (28) 致谢 (29)
最新CA6140普通车床主轴变速箱设计及主轴箱设计说明书汇总
C A6140普通车床主轴变速箱设计及主轴箱 设计说明书
目录 1 绪论 (1) 1.1 课题研究背景及选题意义 (1) 1.1.1课题的背景 (1) 1.1.2课题的目的 (5) 1.2 完成的内容 (5) 2 参数拟定 (6) 2.1 主电机动力参数的确定 (6) 2.2 运动设计 (7) 2.2.1确定主轴极限转速 (7) 2.2.2确定转速范围n R定公比 确定主轴转速数例: (8) 3 传动设计 (8) 3.1 传动方案拟定 (8) 3.1.1传动组和传动副数的确定 (9) 3.2 传动结构式的选择 (10) 3.2.1基本组和扩大组的确定 (10) 3.2.2分配总降速比 (11) 3.3 带轮直径和齿轮齿数的确定及转速图拟定 (12) 3.3.1确定皮带轮动直径 (12) 3.3.2确定齿轮齿数 (13) 3.3.3画出转速图如下[1]: (15) 3.3.4验算转速误差 (15) 3.4 齿轮的计算转速的确定及传动系统的拟定的计算转速 (17) 3.4.1确定各轴和齿轮 (17) 3.4.2由转速图拟定传动系统图 (18)
4 传动件的估算和验算 (19) 4.1齿轮模数的估算和设计 (19) 4.1.1 计算各轴传动的功率 (19) 4.1.2 计算传动轴齿轮模数 (20) 4.1.3 计算各轴之间的中心距 (22) 4.2 三角带传动的计算 (22) 4.2.1计算皮带尺寸[6] (22) 4.3 传动轴的估算和齿轮尺寸的计算 (24) 4.3.1确定各轴的直径 (24) 4.3.2 计算各齿轮的尺寸[6] (25) 5 各部件结构设计 (27) 5.1 皮带轮及齿轮块设计 (27) 5.1.1 皮带及皮带轮的设计 (27) 5.1.2 齿轮及齿轮块设计 (28) 5.2 轴承的选择及箱体设计 (28) 5.2.1各轴承的选择 (28) 5.2.2 主轴及箱体设计 (28) 5.3 密封结构及润滑 (29) 6 主轴组件的验算 (30) 6.1验算主轴轴端的位移a y (30) 6.2 前轴承的转角及寿命的验算 (32) 6.2.1 验算前轴承处的转角Q (32) 6.2.2 验算前支系寿命 (33) 6.3 箱体设计 (34) 总结 (34) 致谢 (36)
JCK6136数控车床主轴箱和床身部件设计
毕业设计(论文) 设计(论文)题目: JCK6136 数控车床设计 -主轴箱和床身部件 学院名称:机械工程学院 专业:机械设计制造及其自动化 班级: 姓名: 指导教师: 定稿日期:
JCK6136数控车床主轴箱和床身部件设计 任务书 1.设计(论文)拟解决的主要问题 ?通过调研和分析小组共同确定机床的传动方案、总体布置形式;完成给定机械部分的详细结构设计,设计的各部分间能有机结合,相互协调;小组共同整个机床的装配图和机械部分的大部分图样。 ?加强综合训练,全面提高工程应用能力和开发创新能力,培养相互协作配合的团队精神。 ?重点解决主轴箱部件设计有关的技术问题。 2.设计(论文)的主要内容和基本要求 ?技术参数:床身最大回转直径:360mm,拖板最大回转直径:≥190mm,最大加工长度:1000mm,主轴转速:36~1800r/min(高低挡无级变速),主轴锥孔MT6;径纵向进给最大速度:4m/min,横向进给最大速度:4m/min。主电机功率5.5Kw。 ?设计任务: 机床总装配图、部件装配图、主要自制件零件图,总图量不小于3 张A0。 开题报告、文献综述、外文翻译、设计计算书各一份。 ?设计要求: 图样全部用计算机绘制,符合最新制图标准;投影正确,表达完整,布局合理。 注重工作性能和结构、装配工艺性;外观造型,力求简洁、明快;功能满足,实用可靠。 理论分析完整清楚;设计推导简要;计算正确可靠。避免冗长,杜绝抄袭。
摘要 数控技术水平的高低和数控设备拥有的多少已成为衡量个国家工业现代化的重要标志。数控机床作为机电一体化的典型产品,在机械制造.中发挥着巨大的作用,很好地解决了现代机械制造中结构复杂、精密、批量小、多变零件的加工问题,且能稳定产品的加工质量,大幅度提高生产效率。但是,发展数控技术的最大障碍就是添置设备的初期投资大,这使许多中小型企业难以承受。如果淘汰大量的普通机床,而去购买昂贵的数控机床,势必造成巨大的浪费。因此,普通机床的数控化改造大有可为。 通过对JCK6136普通车床的数控改造,使其加工精度明显提高,定位准确可靠,操作方便,性能价格比高。这种方法对中小企业设备的数控改造有一定的借鉴与推广作用。本次改造主要针划车床的主轴系统、刀架系统、进给系统、反馈环节、电器控制柜及数控系统进行了改造,改造方法简单、改造操作步骤便于实施。 关键词:车床;数控;改造;进给系统;主轴;传动系统。
563_C6140普通车床主轴变速箱设计
摘要 车床主要是为了进行车外圆、车端面和镗孔等项工作而设计的机床。车削很少在其他 种类的机床上进行,而且任何一种其他机床都不能像车床那样方便地进行车削加工。由于 车床还可以用来钻孔和铰孔,车床的多功能性可以使工件在一次安装中完成几种加工。因 此,在生产中使用的各种车床比任何其他种类的机床都多。 车床的基本部件有:床身、主轴箱组件、尾座组件、溜板组件、丝杠和光杠。 主轴箱安装在内侧导轨的固定位置上,一般在床身的左端。它提供动力,并可使工件 在各种速度下回转。它基本上由一个安装在精密轴承中的空心主轴和一系列变速齿轮(类 似于卡车变速箱)所组成。通过变速齿轮,主轴可以在许多种转速下旋转。大多数车床有 8~12种转速,一般按等比级数排列。而且在现代机床上只需扳动2~4个手柄,就能得到全 部转速。一种正在不断增长的趋势是通过电气的或者机械的装置进行无级变速。 由于机床的精度在很大程度上取决于主轴,因此,主轴的结构尺寸较大,通常安装在 预紧后的重型圆锥滚子轴承或球轴承中。主轴中有一个贯穿全长的通孔,长棒料可以通过 该孔送料。主轴孔的大小是车床的一个重要尺寸,因此当工件必须通过主轴孔供料时,它 确定了能够加工的棒料毛坯的最大尺寸。 关键字:车床;主轴箱组件;主轴;无级变速 I
Abstract Lathes are machine tools designed primarily to do turning, facing and boring, V ery little turning is done on other types of machine tools, and none can do it with equal facility. Because lathes also can do drilling and reaming, their versatility permits several operations to be done with a single setup of the work piece. Consequently, more lathes of various types are used in manufacturing than any other machine tool. The essential components of a lathe are the bed, headstock assembly, tailstock assembly, and the leads crew and feed rod. The headstock is mounted in a foxed position on the inner ways, usually at the left end of the bed. It provides a powered means of rotating the word at various speeds . Essentially, it consists of a hollow spindle, mounted in accurate bearings, and a set of transmission gears-similar to a truck transmission—through which the spindle can be rotated at a number of speeds. Most lathes provide from 8 to 18 speeds, usually in a geometric ratio, and on modern lathes all the speeds can be obtained merely by moving from two to four levers. An increasing trend is to provide a continuously variable speed range through electrical or mechanical drives. Because the accuracy of a lathe is greatly dependent on the spindle, it is of heavy construction and mounted in heavy bearings, usually preloaded tapered roller or ball types. The spindle has a hole extending through its length, through which long bar stock can be fed. The size of maximum size of bar stock that can be machined when the material must be fed through spindle. Key words: Lathes? headstock assembly? variable speed?
CA6140机床主轴箱的设计
文档来源为:从网络收集整理.word版本可编辑.欢迎下载支持. 目录 第一章引言 第二章机床的规格和用途 第三章机床主要参数的确定 第四章传动放案和传动系统图的拟定 第五章主要设计零件的计算和验算 第六章结论 第七章参考资料编目
第一章引言 普通车床是车床中应用最广泛的一种,约占车床类总数的65%,因其主轴以水平方式放置故称为卧式车床。 CA6140型普通车床的主要组成部件有:主轴箱、进给箱、溜板箱、刀架、尾架、光杠、丝杠和床身。 主轴箱:又称床头箱,它的主要任务是将主电机传来的旋转运动经过一系列的变速机构使主轴得到所需的正反两种转向的不同转速,同时主轴箱分出部分动力将运动传给进给箱。主轴箱中等主轴是车床的关键零件。主轴在轴承上运转的平稳性直接影响工件的加工质量,一旦主轴的旋转精度降低,则机床的使用价值就会降低。 进给箱:又称走刀箱,进给箱中装有进给运动的变速机构,调整其变速机构,可得到所需的进给量或螺距,通过光杠或丝杠将运动传至刀架以进行切削。 丝杠与光杠:用以联接进给箱与溜板箱,并把进给箱的运动和动力传给溜板箱,使溜板箱获得纵向直线运动。丝杠是专门用来车削各种螺纹而设置的,在进行工件的其他表面车削时,只用光杠,不用丝杠。同学们要结合溜板箱的内容区分光杠与丝杠的区别。 溜板箱:是车床进给运动的操纵箱,内装有将光杠和丝杠的旋转运动变成刀架直线运动的机构,通过光杠传动实现刀架的纵向进给运动、横向进给运动和快速移动,通过丝杠带动刀架作纵向直线运动,以便车削螺纹。 第二章机床的规格和用途 CA6140机床可进行各种车削工作,并可加工公制、英制、模数和径节螺纹。 主轴三支撑均采用滚动轴承;进给系统用双轴滑移共用齿轮机构;纵向与横向进给由十字手柄操纵,并附有快速电机。该机床刚性好、功率大、操作方便。 第三章主要技术参数 工件最大回转直径: 在床面上………………………………………………………-----……………400毫米在床鞍上…………………………………………………………-----…………210毫米工件最大长度(四种规格)……………………………----…750、1000、1500、2000毫米主轴孔径…………………………………………………-----……………………… 48毫米主轴前端孔锥度…………………………………………-----…………………… 400毫米主轴转速范围: 正传(24级)…………………………………………----…………… 10~1400转/分反传(12级)……………………………………---…-……………… 14~1580转/分加工螺纹范围:
最大加工直径为250mm普通车床主轴箱部件设计
XX大学 课程设计(论文) 最大加工直径为250mm的普通车床的主轴箱部件设计 所在学院 专业 班级 姓名 学号 指导老师 年月日
摘要 本设计着重研究机床主传动系统的设计步骤和设计方法,根据已确定的运动参数以变速箱展开图的总中心距最小为目标,拟定变速系统的变速方案,以获得最优方案以及较高的设计效率。在机床主传动系统中,为减少齿轮数目,简化结构,缩短轴向尺寸,用齿轮齿数的设计方法是试算,凑算法,计算麻烦且不易找出合理的设计方案。本文通过对主传动系统中三联滑移齿轮传动特点的分析与研究,绘制零件工作图与主轴箱展开图及剖视图。 关键词:传动系统设计,传动副,结构网,结构式,
目录 摘要 (2) 目录 (3) 第1章绪论 (5) 1.1 课程设计的目的 (5) 1.2课程设计的内容 (5) 1.2.1 理论分析与设计计算 (5) 1.2.2 图样技术设计 (5) 1.2.3编制技术文件 (5) 1.3 课程设计题目、主要技术参数和技术要求 (5) 第2章车床参数的拟定 (7) 2.1车床主参数和基本参数 (7) 2.2车床的变速范围R和级数Z (7) 2.3确定级数主要其他参数 (7) 2.3.1 拟定主轴的各级转速 (7) 2.3.2 主电机功率——动力参数的确定 (7) 2.3.3确定结构式 (7) 2.3.4确定结构网 (8) 2.3.5绘制转速图和传动系统图 (8) 2.4 确定各变速组此论传动副齿数 (9) 2.5 核算主轴转速误差 (11) 第3章传动件的计算 (11) 3.1 带传动设计 (11) 3.2选择带型 (12) 3.3确定带轮的基准直径并验证带速 (13) 3.4确定中心距离、带的基准长度并验算小轮包角 (13) 3.5确定带的根数z (14) 3.6确定带轮的结构和尺寸 (14)
变速车床主轴箱设计及实物制作(8级)
8级变速车床主轴箱设计及实物制作 机械设计制造及其自动化 【摘要】作为主要的车削加工机床,普通车床被广泛的应用于机械加工行业中。本文主要针对8级变速车床主轴箱的设计进行说明,共包括运动设计、动力设计和结构设计三个部分。设计的主要内容有机床主要参数的确定,传动方案和传动系统图的拟定,最后通过对车床主轴箱零件进行计算、校核从而完成此机床主轴箱的设计。在结构设计中主要是主轴箱的传动设计,根据已给定的条件,即主轴转速来设计主传动系统。实际工作时,操纵变速手柄,通过拨叉拨动主轴箱中的滑移齿轮在轴上移动,实现变速。 【关键词】8级变速;主轴箱;设计 Design of the 8-Level Speed Spindle Box & the Model Making Mechanical Design, Manufacturing and Automation Major Abstract:As major turning machines, universal lathe is used widely in mechanical processing industry. In this paper, it focuses on the design of 8-level speed spindle box, and it includes three parts that motion design, dynamic design and structure design. The main contents of this design is to determine the main parameters, transmission scheme and drive system drawing of the machine tool, and finally complete the design of the spindle box by calculating and checking the parts of the spindle box. The main structure design is the design of transmission , under the given conditions, that is, according to spindle speed design the main drive system. Practically working, it control variable speed handles to achieve different speed through the fork that bring along the sliding gear moving on the axis[1]. Key words:8-level speed; spindle box; design
机床主轴箱课程设计18级转速 参考资料
1.概述 (4) 1.1机床主轴箱课程设计的目的 (4) 1.2设计任务和主要技术要求 (4) 1.3操作性能要求 (4) 2.参数的拟定 (5) 2.1确定极限转速 (5) 2.2主电机选择 (5) 3.传动设计 (6) 3.1主传动方案拟定 (6) 3.2传动结构式、结构网的选择 (6) 3.2.1确定传动组及各传动组中传动副的数目 (6) 3.2.2传动式的拟定 (7) 3.2.3结构式的拟定 (7) 4.传动件的估算 (8) 4.1三角带传动的计算 (8) 4.2传动轴的估算 (11) 4.2.1主轴的计算转速 (11) 4.2.2各传动轴的计算转速 (12) 4.2.3各轴直径的估算 (12) 4.3齿轮齿数的确定和模数的计算 (13) 4.3.1齿轮齿数的确定 (13) 4.3.2齿轮模数的计算 (15) 4.3.4齿宽确定 (20) 4.3.5齿轮结构设计 (21)
4.4带轮结构设计 (21) 4.5传动轴间的中心距 (21) 4.6轴承的选择 (22) 4.7片式摩擦离合器的选择和计算 (23) 4.7.1摩擦片的径向尺寸 (23) 4.7.2按扭矩选择摩擦片结合面的数目 (23) 4.7.3离合器的轴向拉紧力 (2424) 4.7.4反转摩擦片数 (24) 5.动力设计 (25) 5.1传动轴的验算 (25) 5.1.1Ⅰ轴的强度计算 (26) 5.1.2作用在齿轮上的力的计算 (26) 5.1.3主轴抗震性的验算 (28) 5.2齿轮校验 (31) 5.3轴承的校验 (32) 6.结构设计及说明 (33) 6.1结构设计的内容、技术要求和方案 (33) 6.2展开图及其布置 (34) 6.3I轴(输入轴)的设计 (34) 6.4齿轮块设计 (35) 6.4.1其他问题 (36) 6.5传动轴的设计 (36) 6.6主轴组件设计 (38) 6.6.1各部分尺寸的选择 (38) 6.6.2主轴轴承 (38)
车床主轴箱设计_说明书[1]概论
蚌埠学院 课程设计任务书 学院:机械工程与自动化学院 专业:机械设计制造及其自动化 学生姓名:孟清泉学号:51201012025 课程设计题目:金属切削机床课程设计 ——车床主轴箱设计 起迄日期:2015.12.7——2015.12.20 课程设计地点: 指导教师: 系主任:
蚌埠学院机械制造装备设计课程设计任务书 层次:本科专业:2012级机械设计制造与自动化 学生姓名孟清泉学号51201012025 指导教师甘瑞霞 课题类别车床主传动系统设计设计时间2015年12月7日至2015年12月20日月20日课题名称最大加工直径为400mm的普通车床的主轴箱部件设计 一、机械制造装备设计课程设计的主要内容与要求 机械制造专业学生的机械制造装备设计课程设计是其在校学习阶段的一个重要教学环节。通过课程设计的实践,综合地运用装备设计课程和其他先修课程的理论和实际知识,进一步培养与提高学生分析和解决工程实际问题的机械设计能力,使学生掌握机床主轴箱设计的一般方法和步骤,也能够培养学生的计算能力、绘图能力、文字表述能力、文献检索能力以及综合分析能力,能够使学生的工程意识和技术素质得到显著提高。 (一)原始数据: 主电动机功率3kW,最高转速,最低转速,公比 工件材料:钢铁材料;刀具材料:硬质合金 (二)设计内容 1、运动设计:根据给定的转速范围及公比确定变速级数,绘制结构网、转速图、传动系统图、计算齿轮齿数等参数。 2、动力计算:根据电机功率及转速,确定各传动件的计算转速,对主要零件(如带、齿轮、主轴、传动轴、轴承等)进行计算(初算和验算)。 3、绘制下列图纸: (1)机床主传动系统图(画在说明书上) (2)主轴箱部件展开图及主要剖面图(A0) (3)主轴零件图(A1或A0) 4、编写设计说明书一份(不少于20页)。 二、应收集的资料及主要参考文献 关慧贞,徐文骥编著.机械制造装备设计课程设计指导书.机械工业出版社.2013 陈立德主编.机械制造装备设计课程设计指导书.机械工业出版社.2007 三、进度计划及指导安排 第1周:熟悉课题,收集资料,运动设计、动力设计、绘制主轴箱部件图草图 第2周:主要零件验算、绘制主轴箱部件图、绘制主轴零件图 整理资料,编写设计说明书,准备答辩 任务书审定日期年月日指导教师(签字) 任务书下达日期年月日学生(签字)
车床主轴箱课程设计12级转速
目录 一、................................................... 机床总体设计 2 1、机床布局------------------------------------------------------------ 2 2、绘制转速图------------------------------------------------------------ 4 3、防止各种碰撞和干涉--------------------------------------------------- 5 4、确定带轮直径---------------------------------------------------------- 5 5、验算主轴转速误差----------------------------------------------------- 5 6、绘制传动系统图-------------------------------------------------------- 6 二、估算传动件参数................... 确定其结构尺寸 7 1、确定传动见件计算转速-------------------------------------------------- 7 2、确定主轴支承轴颈尺寸-------------------------------------------------- 7 3、估算传动轴直径-------------------------------------------------------- 7 4、估算传动齿轮模数----------------------------------------------------- 8 5、普通V带的选择和计算------------------------------------------------- 8 三、....................................................... 机构设计 10 1、带轮设计------------------------------------------------------------- 10 2、齿轮块设计----------------------------------------------------------- 10 3、轴承的选择----------------------------------------------------------- 10 4、主轴主件------------------------------------------------------------- 10 5、操纵机构------------------------------------------------------------- 10 6、滑系统设计----------------------------------------------------------- 10 7、封装置设计----------------------------------------------------------- 10 &主轴箱体设计---------------------------------------------------------- 11 9、主轴换向与制动结构设计---------------------------------------------- 11 四、.................................................... 传动件验算 11 1、齿轮的验算----------------------------------------------------------- 11 2、传动轴的验算--------------------------------------------------------- 13 五、...................................................... 设计感想 15