瓶盖模具设计

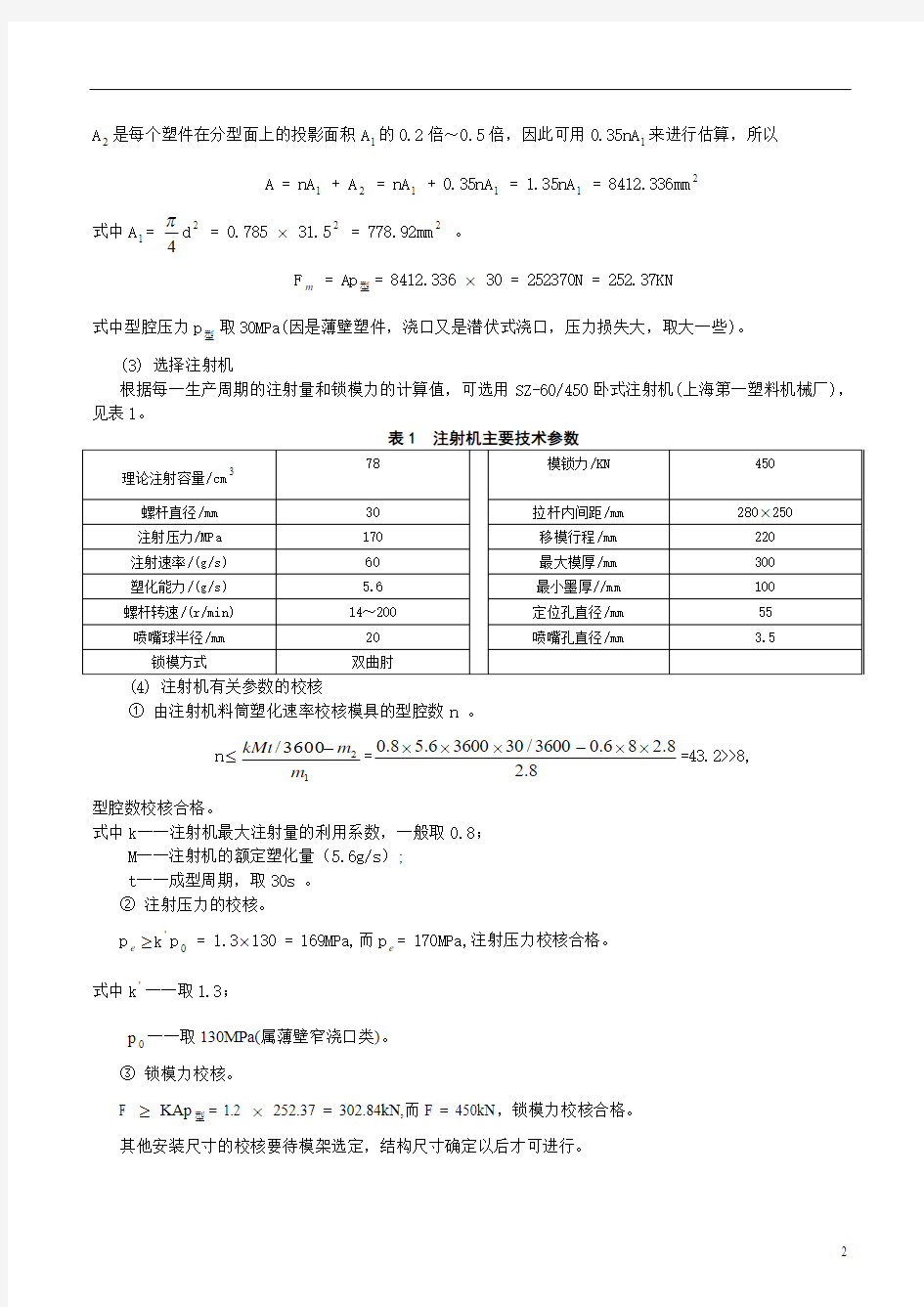
瓶盖塑料模具设计
摘要
1 瓶盖塑料模具设计
1.1拟定模具的结构形式
1.1.1 塑件成型工艺性分析
该塑件是一塑料瓶盖,如图1所示,塑件壁厚属薄壁塑件,生产批量大,材料为聚乙烯(PE,在高密度聚乙烯中掺入了部分低密度聚乙烯,改善塑件的柔韧性),成型工艺性很好,可以注射成型。
1.1.2 分型面位置的确定
根据塑件结构形式,分型面选在瓶盖的底平面,如图2所示。
1.1.3 确定型腔数量和排列方式
(1) 型腔数量的确定
该塑件精度要求不高,又是大批大量生产,可以采用一模多腔的形式。考虑到模具制造费用,设备运转费低一些,初定为一模八腔的模具形式。
(2) 型腔排列形式的确定
该塑件有两圈内螺纹,要使螺纹型芯从塑件上脱出,必须设计一套自动螺纹的齿轮传动结构,并且型腔的分布圆直径和齿轮分布圆直径相吻合,若采用一模八腔,型腔分布圆直径就相当大了,这样模具结构尺寸就比较大,加上齿轮传动系统,模具结构复杂,制造费用也很高。但该塑件螺纹的牙型不高,且呈圆弧
形牙,内侧突起与直径的比例约为5.26%(
6.
266.
26
28-?100% = 5.26%)。因为所用材料为聚乙烯,材料弹性模量比较小,材质硬度不高,课采取强制脱模的方式,这也是注塑厂成型这种类型瓶盖的常用方法。因此本设计采用推件板推出的强制推脱方法,型腔的排列方式采用双列直排,如图2所示。
1.1.4 模具结构形式的确定
从上面分析中可知,本模具拟采用一模八腔,双列直排,推件板推出,流道采用平衡式,浇口采用潜伏式浇口或侧浇口,定模不需要设置分型面,动模部分需要一块型芯固定板和支撑板,因此基本上可确定模具结构形式为A型带推件板的单分型面注射模。
1.1.5 注射机型号的选定
(1) 注射量的计算
通过计算或Pro/E建模分析,塑件质量m
1为2.8g,塑件体积V
1
=
ρ
1
m
=
91
.0
8.2 = 3.077cm3,流道凝料的
质量m
2
还是个未知数,课按塑件质量的0.6倍来估算。从上述分析中确定为一模八腔,所注射量为
M = 1.6nm
1
= 1.6 ?8?2.8 = 35.84g 。
(2)塑件和流道凝料在分型面上的投影面积及所需锁模力的计算
流道凝料(包括浇口)在分型面上的投影面积A
2
,在模具设计前是个未知值,根据多型腔模的统计分析,
A 2是每个塑件在分型面上的投影面积A
1
的0.2倍~0.5倍,因此可用0.35nA
1
来进行估算,所以
A = nA
1
+ A
2
= nA
1
+ 0.35nA
1
= 1.35nA
1
= 8412.336mm2
式中A
1=
4
π
d2 = 0.785 ? 31.52 = 778.92mm2。
F
m
= Ap
型
= 8412.336 ? 30 = 252370N = 252.37KN
式中型腔压力p
型
取30MPa(因是薄壁塑件,浇口又是潜伏式浇口,压力损失大,取大一些)。
(3) 选择注射机
根据每一生产周期的注射量和锁模力的计算值,可选用SZ-60/450卧式注射机(上海第一塑料机械厂),见表1。
表1 注射机主要技术参数
(4) 注射机有关参数的校核
①由注射机料筒塑化速率校核模具的型腔数n 。
n≤
12
3600 /
m m
kMt-=
8.2
8.2
8
6.0
3600
/
30
3600
6.5
8.0?
?
-
?
?
?
=43.2>>8,
型腔数校核合格。
式中k──注射机最大注射量的利用系数,一般取0.8;
M──注射机的额定塑化量(5.6g/s);
t──成型周期,取30s 。
②注射压力的校核。
p e ≥k'p
= 1.3?130 = 169MPa,而p
e
= 170MPa,注射压力校核合格。
式中k'──取1.3;
p
──取130MPa(属薄壁窄浇口类)。
③锁模力校核。
F ≥KAp型= 1.2 ?252.37 = 302.84kN,而F = 450kN,锁模力校核合格。
其他安装尺寸的校核要待模架选定,结构尺寸确定以后才可进行。
1.2 浇注系统的设计
1.2.1 主流道设计
(1) 主流道尺寸
根据所选注射机,则主流道小端尺寸为
d = 注射机喷嘴尺寸 + (0.5~1)= 3.5+0.5 = 4mm
主流道球面半径为
SR = 喷嘴球面半径 + (1~2)= 20 + 2 = 22mm
(2)主流道衬套形式
本设计虽然是小型模具,但为了便于加工和缩短主流道长度,衬套和定位圈还是设计成分体式,主流道长度取40mm,约等于定模板的厚度(见图3)。衬套如图5所示,材料采用T10A钢,热处理淬火后表面硬度为53HRC~57HRC 。
(3) 主流道凝料体积
q 主 =
12
h
π
(D2 + Dd + d2) =
12
40π
(6.12 + 6.1 ? 4 + 42) = 812mm3≈0.8cm3
(4) 主流道剪切速率校核
由经验公式
.
γ=
3
3.3
n
R
q
π
γ = 1840.19 = 1840s1- < 5 ? 103s1-
式中 q
γ = q
主
+ q
分
+ q
塑件
= 0.8 + 2.772 + 8?3.077 = 28.188cm3
R n =
2
2
/)1.6
4(+ =
2
05
.5 = 0.2525cm
主流道剪切速率偏小主要是注射量小、喷嘴尺寸偏大,使主流道尺寸偏大所致。
1.2.2 分流道设计
(1) 分流道布置形式
分流道应能满足良好的压力传递和保持理想的填充状态,使塑料熔体尽快地经分流道均衡的分配到各个型腔,因此,采用平衡式分流道,如图4所示。
(2) 分流道长度
第一级分流道 L
1
= 50mm
第二级分流道 L
2
= 10mm
第三级分流道 L
3
= 15.5mm
(3) 分流道的形状、截面尺寸以及凝料体积
①形状及截面尺寸。
为了便于机械加工及凝料脱模,本设计的分流道设置在分型面上定模一侧,截面形状采用加工工艺性比较好的梯形截面。梯形截面对塑料熔体及流动阻力均不大,一般采用下面经验公式来确定截面尺寸,即
B = 0.2654m·4L= 0.26544
8.2??50= 1.996mm
根据参考文献[1]取B = 4mm 。
H =
32B = 3
2
?4 = 2.67mm ,取H = 3mm 分流道L 1截面形状如图5所示。
从理论上L 2、L 3分流道可比L 1截面小10%,但为了刀具的统一和加工方便,在分型面上的分流道采用一样的截面。
② 凝料体积。
分流道长度 L =(50 + 10 ? 2 + 15.5 ? 4)?2 = 264mm
分流道截面积 A = 2
3
4+?3 = 10.5mm 2
凝料体积 q 分= 264 ? 10.5 = 2772mm 3
= 2.772cm 3
(4) 分流道剪切速率校核 采用经验公式?
γ =
3
3.3n
R q π= 2.39 ? 103S 1-在5?102~5?103
之间,剪切速率校核合格。 式中q =
t v = 1
41v ? = 4 ? 3.077 = 12.3cm 3 R n = 3
2
2c
A π= 0.1755cm 式中 t ──注射时间,取1s;
A ──梯形面积(0.105cm 2
);
c ──梯形周长(1.3cm )。 (5) 分流道的表面粗糙度
分流道的表面粗糙度Ra 并不要求很低,一般取0.8μm ~1.6μm 即可,在此取1.6μm,如图5所示。
1.2.3 浇口的设计
根据外部特征,外观表面质量要求比较高,应看不到明显的浇口痕迹,圆周上布满了防滑直纹,因此采用潜伏式浇口,在开模时浇口自行剪断,几乎看不到浇口的痕迹。对于这类小型薄壁塑件,几乎所有工厂都是这样做的(个别工厂在盖的顶部采用点浇口),若采用侧浇口,不太符合工程实践。
(1) 潜伏式浇口尺寸的确定 由经验公式得
d = nk 4A = 0.6 ? 0.2724A = 1.1mm
式中 A = dh π+ πr 2
= 2.69.456mm 2
(塑件的表面积);
n ──塑料材料系数取0.6;
k ──塑件壁厚的函数值取0.272 。
浇口截面形状如图6所示,浇口先取φ0.8,在试模式根据填充情况再进行调整。 (2)浇口剪切速率的校核 由点浇口的经验公式得
.
γ =
34R q π = 3
)
04.0(14.3077.34??= 61244.488s 1-= 6.1 ? 104s 1
- .
γ为104s 1-~105s 1-,剪切速率校核合格。
1.2.4 冷料穴的设计
(1) 主流道冷料穴
如图7所示,采用半球形,并采用球形头拉料杆,该拉料杆固定在动模固定板上,开模时利用凝料对球头的包紧力使主流道凝料从主流道衬套中脱出。
(2) 分流道冷料穴
在分流道端部加长5mm(约1.5d 0)作分流道冷料穴。
1.3 成型零件的设计
模具中确定塑件几何形状和尺寸精度的零件称为成型零件。在本设计中成型零件就是成型盖外表面的凹模,成型内表面的螺纹型芯(凸模)。
1.3.1成型零件的结构设计
(1) 凹模(型腔)
瓶盖圆周上均匀分布着防滑直纹,若凹模制成整体式,则直纹用机械加工方法很困难(没有退刀位置),若制成一个电极来加工防滑直纹,成本也比较高。整体模板都要用价格较贵重的模具钢,维修也不方便。因此,瓶盖圆周部分若采用局部嵌入式凹模,上述存在的问题能够很方便地得到解决,如图8所示,嵌件外径尺寸按经验
]
2[,取44mm(壁厚7mm)。
(2) 型芯
型芯是一个带有两圈螺纹的、且牙型不高的整体式型芯,如图9所示。
1.3.2 成型零件钢材的选用
瓶盖是大批量生产,成型零件所选用钢材耐磨性和抗疲劳性能应该良好;机械加工性能和抛光性能也应良好。因此构成型腔的嵌入式凹模钢材选用SM1 。
定模板构成瓶盖顶部花纹、文字部分,成型时有料流的冲刷,但没有脱模时塑件的摩擦,因此采用55钢调质(定模板材质可和模架厂协商)。
螺纹型芯因为是采用强制脱模,磨损比较厉害,采用硬度比较高的模具钢Gr12MoV,淬火后表面硬度为58HRC ~62HRC 。
1.3.3 成型零件工作尺寸的计算
(1)型腔径向尺寸
L M
= [(1 + s)L s -?χ]z
δ+0= 31.9860104
.00+
式中 s ──塑件平均收缩率s = 2
035
.0015.0+=0.025;
L s ──塑件外径尺寸(取31.5); χ──修正系数(取0.58);
?──塑件公差值(查塑件公差表,取0.52);
z δ──制造公差,(取?/5)。 (2)螺纹型芯径向尺寸
① 螺纹型芯大径
d 大M = [(1 + s)d 大s + ?
中]o
z
δ-= 28.850
03.0- 式中 d 大s ──塑件内螺纹大径基本尺寸(取28); ?
中
──塑件内螺纹中径公差(取制造公差z δ的5倍);
z δ──中径制造公差,根据参考文献[1]中的表9.4-10(取0.03)。 ② 螺纹型芯小径
d 小M = [(1 + s)d 小s + ?
中]o
z δ-= 27.4150
03.0-
式中d 小s ──塑件内螺纹小径基本尺寸(取26.6)。
③ 螺距工作尺寸
T M = t S (1 + s) ±
2
z
δ = 4.61 ± 0.015
式中t S ──塑件内螺纹螺距(取4.5)。
(3) 型腔深度尺寸
H M = [(1 + s)h - ?χ]0
z δ-= 18.72088
.00+
式中 h ──塑件高度最大尺寸(取18.5);
χ──修正系数(取0.56);
?──塑件公差值,查塑件公差表(取0.44)。
(4)型芯高度尺寸
h m = [(1 + s)H + ?χ]0
z δ-= 17.6570080.0-
式中H ──塑件高度最小尺寸(取17); χ──修正系数(取0.58);
?──塑件公差值,查塑件公差表(取0.40)。
注:瓶盖螺纹是一个非标准型螺纹,螺距4.5,牙型高度比较小,在螺纹结构设计上,适合于强制脱模,所以螺纹中径和标准相差很大,就不做计算了,瓶盖在使用中满足要求。
1.3.4 成型零件强度及支撑板厚度计算
(1) 型腔侧壁厚度(按组合式圆筒形凹模计算)
]
1[
S = r (rp
E rp
E p p
25.175.0-+δδ)2
1= 15.75(30
75.1525.1101.2016.03075.1575.0101.2016.055??-????+??)2
1
= 18.24mm
式中 p ──型腔压力(取30MPa ); E ──材料弹性模量(取2.1?105
MPa );
P δ──根据注射塑料品种,模具刚度计算许用变形量。
P δ = 25i 1 = 25?0.6232 = 15.58μm ≈0.016mm
式中i 1 = 0.35W 5
1 + 0.001W = 0.35 ? 15.755
1 + 0.001?15.75 = 0.6232μm;
W ──型腔半径。
型腔侧壁是采用嵌件,嵌件单边厚选7mm,两型腔之间受力是大小相等、方向相反的,在和模状态下不会产生变形,因此两型腔之间壁厚只要满足结构设计的条件就可以了。型腔与模板周边的距离由模板外形尺寸来确定,因模板平面尺寸比型腔布置的尺寸要大得多((200-115)/2 = 42.5 > 18.24),所以完全满足强度和刚度的要求。
(2) 支撑板厚度
支撑板厚度和所选模架两垫块之间的跨度有关,根据前面的型腔布置,模架应选在200?250这个大类范围之内,垫块之间的跨度大约为140mm,根据型腔布置及型芯对支撑板的压力,就可计算得到支撑板的厚度,即
T = 0.54L (P
EL l pl δ121)31
= 0.54 ? 140(027.0250101.252.4923305????)31
= 35.5mm
式中p δ──支撑板刚度计算许用变形量,p δ= 25 i 1= 25?1.08 = 27μm = 0.027mm,
i 1= 0.35 ? W 5
1 + 0.001 ? W = 0.35 ?1405
1 + 0.001 ? 140 = 1.08μm; L ──两垫块之间的距离(约为140);
W ──影响模具变形的最大尺寸,若圆筒形是r 或h,若矩形是L ; L 1──支撑板长度,取250mm;
1l 、2l ──8个型芯投影到支撑板上的面积。
单件型芯所受压力的面积为
A 1 =
4
π
d 21 = 0.785 ? 282 = 615.44mm 2
8个型芯的面积为
1l ? 2l = 8 A 1 = 4923.52 mm 2
此支撑板厚度计算尺寸为35.5,对于小型模具还可以减小一点,可利用两根推板导柱来对支撑板进行支撑,这样支撑板厚度可近似为
n T = 〔
1
1
+n 〕34T = (111+)34
? 35.5 = 14mm 因此,支撑板厚度可取得稍薄一点,取标准厚度32 。
1.4 模架的确定
根据型腔的布局可看出,型腔嵌件分布尺寸为115 ? 195,有根据型腔侧壁最小厚度为18.24,再考虑
到导柱、导套及连接螺钉布置应占的位置和采用推件板推出等各方面问题,确定选用模架序号为5号(200
? L = 200 ? 250)
,模架结构为A4的形式,如图10所示。 各模板尺寸的确定。 1. A 板尺寸
A 板是定模型腔板,塑件高度18.5,在模板上还要开设冷却水道,冷却水道离型腔应有一定的距离,因此A 板厚度取40mm 。 2.
B 板尺寸
B 板是凸模(型芯)固定板,凸模的成型部分直径为φ28,因此B 板厚度取32mm 。
3. C 板块尺寸
垫块 = 推出行程 + 推板厚度 + 推杆固定板厚度 + (5~10)= 18.5 + 20 + 15 +(5~10)=58.5~63.5 根据计算,垫块厚度C 取63。
上述尺寸确定之后,就可以确定模架序号为5号,模面为200 ? 250,模架结构形式为A4的标准模架。 从选定模架可知,模架外形尺寸:宽? 长?高 = 200 ? 250 ?237。 模具平面尺寸200 ? 250 < 280 ?250(拉杆间距),合格;模具高度237,100 < 237 < 300合格;模具开模所需行程 = 17.6(型芯高度)+ 18.5(塑件高度)+(5~10)= (41.1~46.1)< 200(注射机开模行程),合格;其他各参数在前面校核均合格,所以本模具所选注射机完全满足使用要求。
1.5 排气槽的设计
瓶盖成型型腔比较小,约为 3.1cm 3
,注射时间约为1s,采用的是潜伏浇口向型腔顶部倾斜,塑料熔体先充满型腔顶部,然后充满周边下部,这样型腔顶部不会造成憋气现象,气体会沿着分型面和型芯与推件之间的轴向间隙向外排出。如果对于中大型塑件一定要通过计算,开设一定量的排气槽,方可保证产品质量。
1.6 脱模推出机构的设计
推件板推出过程中,为了减小推件板与型芯的摩擦,采用如图11所示结构,推件板与型芯间留0.2mm ~0.25mm 的间隙,本设计中取0.2mm,并用锥面配合,以防止推件板因偏小而板溢料。
1.7 温度调节系统的设计
冷却系统的计算很麻烦,在此只进行简单的计算,在单位时间内塑料熔体凝固时所放出的热量应等于冷却水所带走的热量,模具温度设为40℃。
1.7.1 冷却水的体积流量
V q =
)(2111θθρ-c WQ = )
255.26(187.410104.60513.032-???? = 0.00522m 3/min = 5.2 ? 103- m 3
/min 式中 W ──单位时间(每分钟)内注入模具中的塑料质量(kg/min ),按每分钟注射2次,即
28.188cm 3
?0.91(g/cm 3
)?2次/min = 51.3g/min = 0.0513 g/min;
Q 1──单位质量的塑件在凝固时所放出的热量,PE 为6.4 ? 102
kJ/kg;
ρ──冷却水的密度(1000kg/m 3);
C 1──冷却水的比热容(4.187kJ/(kg ·℃));
θ1──冷却水出口温度(26.5℃);
θ
2
──冷却水入口温度(25℃)。
1.7.2 冷却管道直径
为使冷却水处于湍流状态,查资料
]
3[取d = 8mm 。
1.7.3 冷却水在管道内的流速
由式 s m d q v V /72.160
)1000/8(14.3102.54423
2=????==-π 大于最低流速1.66m/s,达到湍流状态,所选管道直径合理。
1.7.4 冷却管道孔壁与冷却水之间的传热膜系数
查参考文献[1]中的表9.8-5取f = 7.22(水温为30℃时),因此
22
.08
.032.08.0/(3.26463)
1000/8()72.110(22.76.3)(6.3m kJ d v f h =??==ρ·h ·℃) 1.7.5 冷却管道的总传热面积
222
152********.0]
2/)255.26(40[3.26463104.60513.06060mm m h WQ A ==+-????=?=θ
1.7.6 模具上应开设的冷却水孔数
1250
148.35224
≈?==
dL A n π 从计算结果看,因塑件小,单位时间注射量小,所需冷却水道也比较小,但一定水道对模具来说是不可取的(冷却不均匀)。
根据注塑厂的生产经验,在强制脱模的情况下,型芯必须冷却,型芯纵向分两排布置,若是采用串联水道,势必造成型芯温度较大,因此两排型芯应分别采用两条进水道,在注射工艺过程中,根据具体情况确定采用并联水道还是串联水道。在定模部分的流道凝料也应得到冷却,可开设一条往返水道,模外胶管串联,水道流量大小可根据注射时具体工艺情况进行调整,水孔开设见装配图。
矿泉水瓶瓶盖注塑模设计论文
前言 随着中国当前的经济形势的日趋好转,在“实现中华民族的伟大复兴”口号的倡引下,中国的制造业也日趋蓬勃发展;而模具技术已成为衡量一个国家制造业水平的重要标志之一,模具工业能促进工业产品生产的发展和质量提高,并能获得极大的经济效益,因而引起了各国的高度重视和赞赏。在日本,模具被誉为“进入富裕的原动力”,德国则冠之为“金属加工业的帝王”,在罗马尼亚则更为直接:“模具就是黄金”。可见模具工业在国民经济中重要地位。我国对模具工业的发展也十分重视,早在1989年3月颁布的《关于当前国家产业政策要点的决定》中,就把模具技术的发展作为机械行业的首要任务。 近年来,塑料模具的产量和水平发展十分迅速,高效率、自动化、大型、长寿命、精密模具在模具产量中所战比例越来越大。注塑成型模具就是将塑料先加在注塑机的加热料筒内,塑料受热熔化后,在注塑机的螺杆或活塞的推动下,经过喷嘴和模具的浇注系统进入模具型腔内,塑料在其中固化成型。 本次设计的主要任务是矿泉水瓶盖注塑模具的设计。之所以选择这个设计题目的主要有两方面意义:1、瓶盖是带内螺纹的塑件要求设计时要充分考虑到脱模的方式方法,多分型面结构以及点浇口方式的模具结构设计方法;2、瓶盖属中小型件在我们的日常生活中有一定的普遍性和代表性,为今后的实用性模具设计奠定了基础以更好的服务模具制造业服务社会。 本次设计的主要目的:了解模具设计的方法与内容;掌握各类型模具的基本结构以及各零部件与非标准件的设计;熟悉模具材料的性能与应用以及加工方法与加工手段;熟练应用各种模具设计软件,包括CAD、CAXA、Pro/E等;了解模具的发展状况与发展方向。希望通过本次设计为今后的工作奠定一个良好的基础。 1.塑件的工艺分析 1.1塑件的型工艺分析 该塑料制品为瓶盖,其塑件的结构以及表面形状较为简单,整个塑件呈筒状,整个塑件高达12mm,外径为28mm,壁厚1mm。作为实用零件对其尺寸公差没有太严格的要求,故在本次设计中可以忽略此方面的考虑,以降低模具的加工制造成本。且塑件本身壁厚较小、均匀,适合于大批大量的注塑模具生产。塑件图如下所示: 塑件图:
一模一腔点浇口顶板顶出开水瓶盖模具设计
武汉工程大学 塑料模具设计课程设计说明书 课题名称:一模一腔点浇口顶板顶出开水瓶盖模具设计专业班级:09高材03班 学生学号:0902020323 学生姓名: 学生成绩: 指导教师:刘仿军 课题工作时间:2013-01-08至2013-01-13 武汉工程大学教务处
课程设计任务书 一、设计题目 小组同学(每组人数不超过4人)自己选定熟悉的塑料制品作为模具课程设计题目(控制题目难度在两周内完成) 二、课题条件 1、利用图书馆资料,进行必要的文献调研; 2、利用现有模具教具、生活现场取得的制品进行设计; 3、可提供计算机进行模具设计绘图、说明书编写等工作。 三、设计任务 1、根据选定的塑料件,确定制品的原材料品种,及制品的尺寸精度要 求。 2、小组讨论确定完成制品模具设计的程序,可以参照附件一。 3、小组讨论确定该制品模具的基本结构组成及时间进度安排。 4、电脑或手工绘制模具装配图,要求模具结构合理,功能完备。 (1)如果两视图不能表达清楚的,需附加三视图、局部剖视图等; (2)模具装配图上应标注所有零件的件号、名称; (3)模具装配图上应有明细表,内容:件号、数量、材料、热处理状态、硬度、规格、备注等内容。 5、绘制非标准零件图,尺寸标注完全合理(包括配合尺寸) 6、撰写设计说明书,应书写本设计过程中设计结果及参数选用等内容。 四、设计说明书内容 1、制品使用要求及原材料的工艺性和成型性能; 2、模腔数目确定,分型面的选择,成型零部件设计,合模导向机构,
浇注系统类型的确定及脱模方式的设计,温度调节系统的布排; 3、校核注射模与注射机规格的适应性; 4、标注参考资料。
的模具二次顶出
的模具二次顶出 GE GROUP system office room 【GEIHUA16H-GEIHUA GEIHUA8Q8-
二次顶出机构 一般情况下,从模具中取出成品,无论是采用单一或者是多元件的顶出机构,其顶出动作都是一次完成。但是,由於成品的形状特殊,或者是量产时的要求,如果在一次顶出後,成品仍然在模穴中,或者是无法自动脱落时,就需要再增加一次顶出动作。这样的顶出动作设计,称为二次顶出。 二次顶出,能够让顶出流程顺畅化,对於某些顶出行程需求较大的产品,利用二次顶出可以减少顶针在顶出时施加的力量,避免顶出时造成产品上的缺陷。 二次顶出机构,简单来说,可以分为下列三大类: 一、单顶针板组合的二次顶出机构 二、双顶针板组合的二次顶出机构 三、气动/液压的二次顶出机构 一、单顶针板组合的二次顶出机构 所谓单顶针板组合,就是一般常见的单套顶针板组合(上顶针板及下顶针板各一),由於仅有单套的顶针板组合,因此射出机顶出的动作仅提供传统的一次顶出;另一次顶出就必须配合其他的模具机构设计(例如弹簧)来进行。
单顶针板的二次顶出机构,可以分成下列几类: 1. 公母模板弹开式 2. 公母模板拉开式 3. 顶针板组合机构 4. 浮动模仁 以下,将根据各种不同的设计,提供参考的设计图面。 公母模板弹开式二次顶出 第一段顶出发生在公母模板开启时。弹簧将模板(或局部模仁)顶出一小段距离。 第二段顶出由顶针板作动,利用顶针将产品顶离模穴。 利用弹簧完成二次顶出,在模具结构上是最简单的方法,需要额外加工的部分也很少。但是,弹簧的缺点(弹性疲乏),也是这种顶出方式的缺点。随时注意弹簧是否能够顺利动作,以及检查第一段顶出的顶出行程,是避免模具机构失效的安全措施。
塑料瓶盖注射模具设计
四川理工学院成人教育学院 毕业设计(论文) 题目―塑料瓶盖注塑模具设计 教学点重庆科创职业学院 专业机械设计制造及自动化 年级 2011级 姓名姚爽 指导教师唐建敏
定稿日期: 2013年4月 25 日
四川理工学院成人教育学院毕业设计(论文)任务书
设计(论文)要求(1)了解中国塑料模具的进展 (2)塑件分析及行腔数目的决定和排布(3)注塑机的选着及注射量的计算 (4)了解XS-ZY-125型注射机的要紧参数(5)成型零件的设计及推出机构的设计(6)冷却系统设计及后期的校核 参考资料(1)王树勋.注塑模具设计与制造有用技术[M].华南理工大学出版社,1996.78-99. (2)王孝培.塑料成型工艺及模具简明手册[M]. 北京:机械工业出版社,2000.56-67. (3)唐志玉.塑料挤塑模与注塑模优化设计[M]. 北京:机械工业出版社,2004.78-87. (4)万林.有用塑料注射模设计与制造[M]. 北京:机械工业出版社,2000.45-65 注:此表由指导教师填写后发给学生,学生按此表要求开展毕业设计 (论文)工作。
塑料瓶盖注塑模具设计 摘要 塑料制品具有原料来源丰富,价格低廉,,性能优良等特点。它在电脑、手机、汽车、电机、电器、仪器仪表、家电和通讯产品制造中具有不可替代的作用,应用极其广泛。注射成形是成形热塑件的要紧方法,因此应用范围专门广。 注射成形是把塑料原料放入料筒中通过加热熔化,使之成为高黏度的流体,用柱塞或螺杆作为加压工具,使熔体通过喷嘴以较高压力注入模具的型腔中,通过冷却、凝固时期,而后从模具中脱出,成为塑料制品。 本产品是日常应用的塑料瓶盖,且有用性强。该产品设计为大批量生产,故设计的模具要有较高的注塑效率,浇注系统要能够自动脱模,此外为保证塑件表面质量采纳侧浇口,因此选用单分型面注射模,侧浇口自动脱模结构。模具的型腔选择一模四腔结构,浇注系统采纳侧浇口成形,推出形式为推件板推出机构完成塑件的推出。塑件的工艺性能要求注塑模中有冷却系统,因此在模具设计中也进行了设计。本次的设计查阅了大量的专业资料和书籍,丰富了设计过程。 关键词:注射成型,侧浇口,型芯
瓶盖模具设计
瓶盖塑料模具设计 摘要 1 瓶盖塑料模具设计 1.1拟定模具的结构形式 1.1.1 塑件成型工艺性分析 该塑件是一塑料瓶盖,如图1所示 ,塑件壁厚属薄壁塑件,生产批量大,材料为聚乙烯(PE,在高密度聚乙烯中掺入了部分低密度聚乙烯,改善塑件的柔韧性),成型工艺性很好,可以注射成型。 1.1.2 分型面位置的确定 根据塑件结构形式,分型面选在瓶盖的底平面,如图2所示。 1.1.3 确定型腔数量和排列方式 (1)型腔数量的确定 该塑件精度要求不高,又是大批大量生产,可以采用一模多腔的形式。考虑到模具制造费用,设备运转费低一些,初定为一模八腔的模具形式。 (2) 型腔排列形式的确定 该塑件有两圈内螺纹,要使螺纹型芯从塑件上脱出,必须设计一套自动螺纹的齿轮传动结构,并且型腔的分布圆直径和齿轮分布圆直径相吻合,若采用一模八腔,型腔分布圆直径就相当大了,这样模具结构尺寸就比较大,加上齿轮传动系统,模具结构复杂,制造费用也很高。但该塑件螺纹的牙型不高,且呈圆弧形牙,内侧 突起与直径的比例约为5.26%( 6. 266. 26 28-?100% =5.26%)。因为所用材料为聚乙烯,材料弹性模量比较小,材质硬度不高,课采取强制脱模的方式,这也是注塑厂成型这种类型瓶盖的常用方法。因此本设计采用推件板推出的强制推脱方法,型腔的排列方式采用双列直排,如图2所示。 1.1.4 模具结构形式的确定 从上面分析中可知,本模具拟采用一模八腔,双列直排,推件板推出,流道采用平衡式,浇口采用潜伏式浇口或侧浇口,定模不需要设置分型面,动模部分需要一块型芯固定板和支撑板,因此基本上可确定模具结构形式为A型带推件板的单分型面注射模。 1.1.5 注射机型号的选定 (1) 注射量的计算 通过计算或Pro/E建模分析,塑件质量m 1为2.8g,塑件体积V 1 = ρ 1 m = 91 .0 8.2= 3.077cm3,流道凝料的 质量m 2 还是个未知数,课按塑件质量的0.6倍来估算。从上述分析中确定为一模八腔,所注射量为 M = 1.6nm 1 = 1.6 ?8?2.8 = 35.84g 。 (2)塑件和流道凝料在分型面上的投影面积及所需锁模力的计算 流道凝料(包括浇口)在分型面上的投影面积A 2 ,在模具设计前是个未知值,根据多型腔模的统计分析,
吐血奉献,多年的注塑模具设计经验总结,绝对转载
今天闲着没事来论坛看看,听说这个论坛比较不错。看完几个帖子后,我实在是坐不住了,我闲暇的时候也曾经浏览过很多关于模具结构的论坛。但看来看去,总是那些东西。很少有人能把真正设计模具的要点指出来。 我是从事注塑模具结构设计的,曾经设计过家电,汽车,电子产品类的模具。设计水平不见得很高,只是干过的活比较多比较杂而已。今天刚好闲着没事,跟大家共同讨论下关于注塑模具结构设计的问题。 首先我们拿到了一个产品后,先不要急着分模,最重要的一件事就是先检查产品结构,包括拔模,厚度等模塑型问题。当然这些对于一个刚刚从事模具结构设计的人来说,可能是比较困难的。因为他们可能不知道如何才是比较适合模具设计用的产品,这些没关系,只是自己日常积累的一个过程。当你分析完产品的拔模,壁厚,以及在出模方向有倒扣的地方后,你基本上已经知道了模具分型面的走向,以及浇口的位置,当然这些最终还是要跟客户确认的。 有人说,是不是我分析好了产品结构后,就可以开始设计模具了呢,答案当然是NO。要想在设计时少走弯路,一些关于影响模具结构的项目是一定要确认好的。具体内容如下:1,客户用来生产的注塑机的吨位及型号类型,这个确认不好,你就没法确认你模具的浇口套的入口直径以及定位圈的直径,顶出孔的大小跟位置,还有注塑机能伸进模具内的深度,甚至模架的大小,闭合高度等等。你辛辛苦苦的设计好了一套用油缸抽芯的模具结构,你也颇有成就感,可模具到了客户那里没法生产,因为客户那里只有电动注塑机,而且没另外加中子,估计那时你会有种欲哭无泪的感觉。2,客户注塑机的码模方式,一般常用的是压板码模,螺丝码模,液压码模,磁力码模等等。这个确认好了,你才知道你设计模具时,到底需不需要设计码模螺丝过孔或者码模槽。3,刚才我们分析后的产品的问题点,以及产品夹线,产品材料及收缩率。不要想当然的认为PP的塑料收缩率就一定是1.5%,这个一定要跟客户确认好,要知道他们最终用于生产的材料是什么牌号的,有没有添加什么改性材料等等。 有条件时,最好能熟知产品的装配关系以及产品的用途等等,这些信息对于将来的模具结构设计是非常有帮助的。因为了解了这些,你就知道哪些是外观面,哪些是非外观,哪些地方的拔模角度是可以随便加大的,哪些地方是不能改的。甚至包括一些产品的结构,如果你了解了产品的实际装配关系以及用途,你就知道哪些倒扣结构是可以取消或改成另外一种简单形式的。一定要牢记,做模具的过程就是把复杂问题简单化的过程。常看到一些人以做了一套多么多么复杂的结构而感到骄傲自豪,我觉得那是非常得无知。因为很多产品工程师可能会由于自身的经验问题,设计了一些不太合理的结构,如果作为下游工序,不能帮他们指正的话,他们可能永远都觉得那样设计是没问题的。那我们产品工程师的进步就会非常的缓慢。 4,模具水路外接参数,油路外接参数,电路外接参数,气路外接参数。只有在设计之前了解了客户这些要求之后,你才能有预见性的设计水路油路气路,别到时辛辛苦苦设计好了模具,后来发现客户需要在模具内部串联油路,那时你再改动,估计会累个半死,因为你水路,顶杆,螺钉什么的都好不容易排好了位。像这四路的设计顺序一般是先保证油路,因为油路要分布平衡,特指需要油缸顶出的模具结构,如果油路不平衡的话,油缸顶出的动作就会有先后,容易顶出不平衡。当然也可以采用齿轮分油器,但那样就更复杂了.其次是水路,因为水路要保证冷却效果,分布不均会影响产品质量及模具寿命。最后才是气路跟电路。在模具上的放置顺序是,最靠近TOP方向的是电路,然后是水路,
塑料碗注射模具设计方案
塑料碗注射模具设计方案 第一章塑件结构及成形工艺性分析 1.1 分析塑件使用材料的种类及工艺特征 该塑件材料选用PP PP 聚丙烯典型应用围: 汽车工业(主要使用含金属添加剂的PP:挡泥板、通风管、风扇等),器械(洗碗机门衬垫、干燥机通风管、洗衣机框架及机盖、冰箱门衬垫等),日用消费品(草坪和园艺设备如剪草机和喷水器等)。 化学和物理特性: PP是一种半结晶性材料。它比PE要更坚硬并且有更高的熔点。由于均聚物型的PP 温度高于0℃以上时非常脆,因此许多商业的PP材料是加入1~4%乙烯的无规则共聚物或更高比率乙烯含量的钳段式共聚物。共聚物型的PP材料有较低的热扭曲温度(100℃)、低透明度、低光泽度、低刚性,但是有有更强的抗冲击强度。PP的强度随着乙烯含量的增加而增大。PP的维卡软化温度为150℃。由于结晶度较高,这种材料的表面刚度和抗划痕特性很好。PP不存在环境应力开裂问题。通常,采用加入玻璃纤维、金属添加剂或热塑橡胶的方法对PP进行改性。PP的流动率MFR围在1~40。低MFR的PP材料抗冲击特性较好但延展强度较低。对于相同MFR的材料,共聚物型的强度比均聚物型的要高。由于结晶,PP的收缩率相当高,一般为1.8~2.5%。并且收缩率的方向均匀性比PE-HD 等材料要好得多。加入30%的玻璃添加剂可以使收缩率降到0.7%。均聚物型和共聚物型的PP材料都具有优良的抗吸湿性、抗酸碱腐蚀性、抗溶解性。然而,它对芳香烃(如苯)溶剂、氯化烃(四氯化碳)溶剂等没有抵抗力。PP也不象PE那样在高温下仍具有抗氧化性。 聚丙烯(PP)是常见塑料中较轻的一种,其电性能优异,可作为耐湿热高频绝缘材
啤酒瓶盖起子模具设计说明书
第一章冲压机工艺性分析及冲裁方案的确定 工件名称:啤酒瓶盖起子模具设计 生产批量:大批量 材料:60Mn 工件简图:如下图所示 此工件只有落料和冲孔两个工序,材料为60Mn,60Mn是优质碳素结构钢,强度,硬度,弹性和淬透性稍高,具有良好的冲压性能,适合冲裁,工件结构相对简单,有一个7mm的孔和一个不规则的孔;孔与孔,孔与边缘之间的距离也满足要求,最小壁厚为4mm,工件的尺寸全部为自由公差,可看作IT13级,尺寸精度较低,普通冲裁完全能满足要求。 冲裁工艺方案的确定: 该工件包括落料.冲孔两个基本工序,可以有以下三种工艺方案。 方案一:采用单工序模生产。 方案二:采用复合模生产。 方案三:采用级进模生产。 方案一:单工序模生产。模具结构简单,但需要两道工序两幅模具,成本较高而生产效率低,难以满足中批量生产要求。 方案二:复合模生产。之需呀一副模具,工作的精度及生产效率都较高,但冲压后成品保留在模具上,在清理模具上的物料时会影响冲压速度,操作方便。 方案三:级进模生产。也只需要一副模具,生产效率高,操作方便,工作精度也能满足要求。 通过上述三种方案的分析比较,该件的冲压生产采用方案三为佳。 第二章主要设计计算 2.1排样方案的确定及计算 设计级进模,首先要设计条料的排样图,啤酒瓶盖起子的形状具有一头大一头小的特点,直排样时材料利用率低,对于批量生产的零件,特别是零件材料较贵,为了节省材料,提高材料的利用率,应采用直对排样。如图2-1所示的排样方法,设计成隔位冲压,可显著地减少废料,隔位冲压就是将第一遍冲压以后的条料水平方向旋转180,再冲第二遍,在第一次冲裁的间隙中冲裁出第二部分工件。搭边值取2mm和2.2mm,条料宽度为125mm和44mm,一个步距的材料利用率为52%。
酒瓶盖注射模具设计
:余至彬专业:机械设计与制造班级:设计一班学号:2 设计题目:酒瓶盖塑料模 塑料件简图: 塑料件主要技术要求: 1.材料:ABS,米黄色 2.年产量:200万件 3.未注公差:φ30, φ44按MT2标注,其余按MT5计算,并且尺寸按入体原 则标注; 4.其他技术要求:型腔脱模斜度为1°,型芯脱模斜度为0.5°,外表面粗糙度 Ra<1.6,无缺陷,表面无特殊要求,所有过渡处有0.2圆角。
1 酒瓶盖塑件的工艺分析 1.1 塑件成形工艺分析 如图1-1为塑料酒瓶盖的二维工程图及实体图,单位mm。 图1-1 塑件图 产品名称:酒瓶盖 产品材料:丙烯ABS 塑件材料特性:ABS塑料(丙烯腈—丁二烯—苯乙烯共聚物)是在聚苯乙烯分子中导入了丙烯腈、丁二烯等异种单体后成为的改性共聚物,也可称改性聚苯乙烯,具有比聚苯乙烯更好的使用和工艺性能。ABS是一种常用的具有良好的综合力学性能的工程塑料。ABS塑料为无定型塑料,一般不透明。ABS无毒、无味,成形塑
件的表面有较好的光泽。ABS 具有良好的机械强度,特别是抗冲击强度高。ABS 还具有一定的耐磨性、耐寒性、耐油性、耐水性、化学稳定性和电性能。ABS 的缺点是耐热性不高,并且耐气候性较差,在紫外线作用下易变硬发脆。 塑件材料成形性能:使用ABS 注射成型塑料制品时,由于其熔体黏度较高,所需的注塑成型压力较高,因此塑件对型芯的包紧力较大,故塑件应采用较大的脱模斜度。另外熔体黏度较高,使ABS 制品易产生熔接痕,所以模具设计时应尽量减少浇注系统对料流的阻力。ABS 易吸水,成型加工前应进行干燥处理。在正常的成型条件下,ABS 制品的尺寸稳定性较好。 产品数量:年产量200万件 塑件颜色:米黄色 查文献得: 塑件材料物理性能: 密度:305.1~02.1cm g 收缩率:%7.0~%4.0 熔点: 60~93℃ 热变形温度:93℃ 材料力学性能: 拉伸强度:MPa 63 拉伸弹性模量:GPa 9.2 弯曲强度:MPa 97 弯曲弹性模量:GPa 0.3 缺口冲击强度:20.6m KJ
手表包装盒内芯塑料注射模具设计
手表包装盒内芯塑料注射模具设计 摘要 本论文介绍了手表包装盒内芯塑料注射模具的设计与制造方法。该注射模采用了1模2腔的结构。 塑料模具的设计和制造水平反应了机械设计和加工水平,模具的设计已应用了当代先进的设计手段,如CAD、CAM、CAE的逐渐广泛使用,使模具的设计效率大大提高,快速成型技术的应用及现代加工技术的使用如高档加工中心、特种加工技术的使用使模具的制造精度越来越高,加工周期越来越短。各行各业对模具的要求量与日俱增,我国的模具行业蒸蒸日上,正需要大量的模具设计与制造技术的人才。 通过参观,查阅资料,计算,用PRO/E 、CAD等软件绘图进行塑料零件的注射模具设计,我熟悉并掌握了塑料零件注射设计全过程,能够根据不同的塑料材料的性能,塑料的结构特点,选择恰当的模具结构,并掌握了模具主要零件的强度计算及每一个零件的尺寸确定,掌握了材料的选择热处理要求及其制造工艺知识,通过该设计,检查了自己的外语翻译及理解能力,能熟练运用计算机进行设计和绘图。通过本次设计后,我能够完全独立完成中等难度以上塑料注射模具设计,并能在选材,结构设计等方面进行环保、经济技术分析。 简言之,本论文就是将人们常见的手表包装盒的内芯作为设计模型,将塑料注射模具的相关知识作为依据,阐述塑料注射模具的设计全过程。 关键词:塑料;注射模具;设计
The design of plastic injection mold about the core of Watch box Abstract This paper describes the design of plastic injection mold and the methods of manufacturing about core box watches.The structure of one mold and two cavity was use in this injection mold . Plastic mold design and manufacturing level reflects the level of mechanical design and processing,The contemporary-art instruments has been applied to the mold, such as CAD,CAM,CAE are use of the progressive with widespread, so that the efficiency of mold design are greatly improved, The application of the technologies about rapid prototyping and modern processing such as high-end machining centers and the technology of special processing enable the precision of manufacture to grow. processing cycles becoming shorter andshorter.The requirements of various industries on the amount of mold are growing with the success of China's mold industry, is in need of a large number of people about mold design and manufacturing skills. Through visiting, accessing to information, computing, using drawing software such as PRO / E, CAD to do the design the injection mold about the plastic parts, I am familiar with and mastered the whole process of the design of the injection mold about plastic parts,I can depend on the performance of plastic materials,the characteristics of plastic structural, to select the appropriate mold structure, and be able to calculate the strength of the main parts and determine the size of each part , have the knowledge about the require of heat treatment in choice of materials and manufacturing processes, through the design, inspect the proficiency of the translation and understanding to foreign languag with own can design and graphics quickly in the use of computer. Through this design, I can be totally independent to finish the design of plastic injection mold which is more than the middle difficulty, I be able to protecte environment and analysis the technical of economic in material and structural design. In short, the core of watch box what people often look was as a design model in this paper and the knowledge related- plastic injection mold was as the basis to describe the design process of the plastic injection mold . Key words: plastics; injection mold; design
注射模设计说明
一塑件原材料选用与性能分析 1分析制件材料的使用性能 ABS属热塑性非结晶型塑料,不透明。ABS由丙烯晴、丁二烯、苯乙烯共聚而成的,这三种组分各自的特性,使ABS具有良好的综合力学性能。 ABS无毒、无味,呈微黄色,成型的制件有较好的光泽,密度为1.02~1.05g/cm3。ABS有极良好的机械强度和一定的耐磨性、耐寒性、耐油性、化学稳定性和电气性能。ABS有一定的硬度和尺寸稳定性,易于成型加工,经过调色可配成任何颜色。 2 分析塑料成型工艺性能 ABS属于无定形塑料,流动性中等;升温时黏度增高,所以成型压力较高,故制件的脱模斜度宜稍大;ABS易吸水,成型加工前应进行干燥处理,预热干燥80~100℃,时间2~3h;ABS易产生熔接痕,模具设计时应注意尽量减小浇注系统对料流的阻力。 该产品为某电工产品外壳,要求具有一定的强度、刚度、耐热和耐磨损等性能,中等精度,外表面无瑕疵、美观、性能可靠,同时还必须满足绝缘性。采用ABS材料,产品的使用性能基本能满足要求,但在成型时,要注意选择合理的成型工艺。 二塑件结构与质量分析 1 塑件的尺寸精度分析 从零件图上分析,该零件总体形状为长方形,该零件重要尺寸如:等的尺寸精度为MT2~MT3级(查GB/T 14486-2008中常用材料模塑件尺寸公差登等级选用表),未标注公差的尺寸为自由尺寸,可按MT5级塑料件精度查取公差值(可
查GB/T 14486-2008中模塑件尺寸公差表)。 2 塑件表面质量分析 该塑件是某电工产品外壳,要求外表美观、光洁无毛刺、无缩痕,表面粗糙度可取Ra0.8,而塑件部没有较高的粗糙度要求,模具制造和成型工艺容易保证。 3 塑件结构工艺性分析 此塑件外形为方形壳类零件,腔体为25mm深,壁厚均匀2mm,外形尺寸适中,塑件成型性能良好,脱模斜度选为1°; 4 侧孔和侧凹 该塑件在宽度/长度方向有三个通孔,因此模具设计时必须设置侧向分型抽芯机构。 5 塑件的体积和质量计算 根据零件的三维模型,利用三维软件直接可查询到塑件的体积为:V=31.180cm3 故塑件的质量W=V·ρ=32.115g(ABS塑料密度按1.03g/cm3) 三注塑成型机的选择 初选注射机规格通常依据注射机允许的最大注射量、锁模力及塑件外观尺寸等因素确定。 1 依据最大注射量初选设备 ①单个塑件体积 V=31.180cm3 ②由于塑件尺寸不大,结合模具设计要求,采用一模两腔,加上浇注系统凝料体积(初步估算约为34cm3) ③塑件成型每次需要注射量:
塑料注射模具设计说明书
引言 本说明书为机械塑料注射模具设计说明书,是根据塑料模具手册上的设计过程及相关工艺编写的。本说明书的内容包括:目录、课程设计指导书、课程设计说明书、参考文献等。 编写本说明书时,力求符合设计步骤,详细说明了塑料注射模具设计方法,以及各种参数的具体计算方法,如塑件的成型工艺、塑料脱模机构的设计。 本说明书在编写过程中,得到….老师和同学的大力支持和热情帮助,在此谨表谢意。 由于本人设计水平有限,在设计过程中难免有错误之处,敬请各位老师批评指正。 设计者:朱海 2009年11月11日
课程设计指导书 一、题目: 塑料套筒材料:ABS 二、明确设计任务,收集有关资料: 1、了解设计的任务、内容、要求和步骤,制定设计工作进度计划 2、将Pro/E零件图转化为CAD平面图,并标好尺寸 3、查阅、收集有关的设计参考资料 4、了解所设计零件的用途、结构、性能,在整个产品中装配关系、技术要求、生产批量 5、塑胶厂车间的设备资料 6、模具制造技能和设备条件及可采用的模具标准情况 三、工艺性分析 分析塑胶件的工艺性包括技术和经济两方面,在技术方面,根据产品图纸,只要分析塑胶件的形状特点、尺寸大小、尺寸标注方法、精度要求、表面质量和材料性能等因素,是否符合模塑工艺要求;在经济方面,主要根据塑胶件的生产批量分析产品成本,阐明采用注射生产可取得的经济效益。 1、塑胶件的形状和尺寸: 塑胶件的形状和尺寸不同,对模塑工艺要求也不同。 2、塑胶件的尺寸精度和外观要求: 塑胶件的尺寸精度和外观要求与模塑工艺方法、模具结构型式及制造精度等有关。 3、生产批量 生产批量的大小,直接影响模具的结构型式,一般大批量生产时,可选用一模多腔来提高生产率;小批量生产时,可采用单型腔模具等进行生产来降低模具的制造费用。 4、其它方面 在对塑胶件进行工艺分析时,除了考虑上诉因素外,还应分析塑胶件的厚度、塑料成型性能及模塑生产常见的制品缺陷问题对模塑工艺的影响。 四、确定成型方案及模具型式:
塑料螺纹瓶盖模具设计
第1期(总第131期)机械管理开发 2013年2月No.1(SUM No.131)MECHANICAL MANAGEMENT AND DEVELOPMENT Feb.2013 0引言 制品为医用药瓶的瓶盖,具有两圈半连续的内螺纹,螺纹大径:50mm ,螺 距:3mm 。制品外表面有 数个半圆柱形的阻滑纹,成型时可起止转作用,止转高度大于螺纹高度,如图1。材料是高密度聚乙烯,属于结晶型热塑性塑料,熔体流动性能好,易于 注塑成型。下面谈一些成型模具设计和使用方面的经验。 1 模具工作过程 1 2 3 4 5 6 78A A B B 9282726252423222120 1-密封圈;2-定位圈;3-浇口套;4-球头拉料杆;5-定模板;6-齿条;7-凹模板;8-型芯压板;9-凹模底板;10、18-锥齿轮;11、30、34-导套;12-动模板;13-轴承座;14-轴承端盖;15-密封圈;16-齿轮;17-轴;19-动 模底板;20-轴承;21-轴;22-中心齿轮;23、26、27-轴套;24-型芯齿轮;25-螺纹型芯;28-止转镶块;29-内六角螺栓;31、36-导柱;32-弹簧; 33-限位钉;35-水嘴 图2模具结构图 模具的结构如图2[1,2] ,采用点式浇口,一模两腔,螺纹型芯成型内螺纹,利用开模力脱模。经过合模、注塑、保压和冷却后开模,在弹簧32的作用下,A 分型面先分型,用分流道末端的斜面拉断点浇口,利用球头拉料杆4将凝料拉出脱落,在A 分型面分型凹模后退的同时,齿条也随之后退,当齿条端部的凸肩与定模接触时,齿条停止运动,齿轮16在开模力作用下开始转动,通过锥齿轮10、18和中心齿轮22,驱动两个型芯齿轮24转动,从而带动螺纹型芯25转动,型芯被轴套27和 型芯压板8压住只能原地旋转,这样制件沿型芯轴向 脱出。直到限位钉33的头部受到凹模7的阻挡,凹模 停止运动。B 分型面开始快速分型, 制品自由跌落,完成一次成型过程。2脱模系统设计 制件螺纹要求精度较高,采用旋转脱模方式,即采用螺纹型芯旋转,制品后退的方式。考虑到要尽量使模具的结构紧凑、成本低,应该利用开模力作为旋转动力。脱模系统主要由三根轴、一对圆柱齿轮、一对锥齿轮和两对齿轮-齿条构成。轴17两端用滚动轴承支撑,受力均匀并且转动阻力小。轴21上装有锥齿轮,一端用滚动轴承支撑,另一端装有中心齿轮22,由于空间小采用了一端有凸缘的铜轴套23,既能承受径向力,又可承受轴向力。同样螺纹型芯25也用一对轴套26、27支撑。中心齿22与型芯齿轮24的齿数比为2.5:1,锥齿轮18与锥齿轮10的齿数比为2:1,齿条长度大于制品脱出时齿轮16滚动的长度。镶块28成型瓶盖外表面的阻滑纹并在脱模时起止转作用,为方便凹模的加工,做成镶块嵌在凹模中。3脱模过程分析 脱模时螺纹型芯只旋转,制件后退,由凹模止转,螺纹型芯与制件之间是螺纹副关系。正是依据这个原理,制件才能顺利脱模。动定模之间的开模速度与制件脱出速度要很好的配合,才可以达到既能止转又能将制件从凹模脱出的效果。设动定模之间的开模速度为v 1,制件脱出的速度为v 2,当v 1>v 2时,就意味着B 分型面以很快的速度打开,而制品与型芯还没有完全脱开,这时止转长度减小或完全没有了,制品就会部分或全部包在型芯上不能顺利脱出。反过来如果 v 1<v 2, 即制件已经从型芯上脱出,但B 分型面还没有打开,分型面之间没有能容纳制件的空间,制品会遭到 破坏。当v 1=v 2时, 动定模之间的开模距离与制件脱出的长度相适应,制件脱出时既不会受到干涉,又不会失去止转无法脱落,因此,v 1=v 2是制品顺利脱模而又保证质量的条件。 在模具结构设计中,如何保证v 1=v 2, 图3是脱模机构的原理图,由齿条、齿轮Z 1,一对锥齿轮Z 2与Z 3、中 收稿日期:2012-07-16 作者简介:刘俊萍(1957-),女,山东章丘人,副教授,本科,研究方向:塑料成型机械。 塑料螺纹瓶盖模具设计 刘俊萍 (太原理工大学机械工程学院,山西 太原 030024) 摘要:通过对塑料螺纹瓶盖的结构分析,设计出了一套成型模具。重点对制品脱出过程进行了分析,推导出动、 定模之间的开模速度与制件旋出速度之间的关系,阐述了实际应用中采取的措施,对同类模具设计有参考价值。关键词:双分型面;螺纹脱出;注塑模中图分类号:TM161+.23 文献标识码:A 文章编号:1003-773X (2013)01-0021-02 图1塑料瓶盖· ·21
实训设计_饮料瓶瓶盖注射模具设计说明
模具课程设计 饮料瓶瓶盖注射模设计 一塑料的工艺性分析 1.塑件的原材料分析 塑料的品种:PE(聚乙烯)。成型特征:结晶型塑料,吸湿性小,流动性较好,溢边值为0.02mm左右,流动性对压力变化敏感,加热时间长则易发生分解,冷却速度快,必须充分冷却。设计模具时要冷却料穴和冷却分流。收缩率大,方向明显,易变形,扭曲结晶度及模具冷却条件对收缩率影响大,应控制模温。易用变压注射,料温要均匀,否则会增加应力,使收缩不均匀和方向性明显。 2.塑料的尺寸精度分析 影响塑料制品的尺寸精度的主要因素是材料的收缩和模具的制造误差。查教材上表2-11得此材料的收缩率为1.5%~2%。塑料制品的公差也可通过教材上表2-12查得,塑料的精度等级选择7级精度。 3.塑件的表面质量分析
塑件外表面要求粗糙度较低,表面光滑,表面要求低点。 4.塑件结构的工艺性分析 结构简图如图所示 瓶盖主体外侧均匀分布120个增大摩擦力的防滑筋,瓶盖顶部有商标名称ZSM的字样。瓶盖下部有一防伪圈与瓶盖主体通过8个直径为1mm高1mm的小圆柱相连,防伪圈侧有8个均匀分布长为3mm直径为1.5mm的半圆形凸台。瓶盖部有螺呀为半圆形的螺纹及高为4mm截面直径为1mm的防伪圈与瓶子径严密配合,而高为1mm,截面直径1mm的防伪圈与瓶子外径严密配合防止漏水。 综上所述可采用注射成型加工。 二确定成型设备选择与模塑工艺规程编制 1.计算塑件体积和质量 V=3.05 M=2.9g 选择注射机为SZ-30
理论注射容积为373 cm,实际注射质量为33g,螺杆直径为26 mm,塑化能力 3.6g/s,注射压力170MPa 螺杆转速10~160r/min,螺杆行程70 mm,锁模力为320KN,拉杆有效间距300300 ?2 mm,模板行程110 mm,模具最小厚度80 mm,模具最大 ?,顶出行程厚度110 mm,最大开距220 mm,模扳尺寸400400 50 mm,喷嘴半径为12 mm,高为2 mm。 2.确定成型工艺参数 查教材表2-1得注射成型机类型为柱塞式,密度为 0.91~0.943 kg dm,计算收缩率S=1.5~3.6,预热温度为 / o 70~80C,时间为t为1~2h,料简温度:后段为o 140~160C,前段为170~200o C,模具温度35~55o C,注射压力为P为60~100 MP, a 注射时间为15~60s,保压时间为0~3s,冷却时间为15~60 s,成型总周期为40~130 s,使用注射机类型为螺杆,柱塞均可。 三.注射模的结果设计 1.分型面的选择 瓶盖沿圆周仅通过8个小圆柱防伪圈相连,采用两个半圆的哈夫块来成型防伪圈。结合素件结果特点,塑件,塑件成型后必然留在型芯上,故模具分型面设在防伪圈与瓶盖主体之间截面轮廓最大部位,与开模方向垂直 2.型腔数目的确定及型腔的排列 瓶盖作为包装容器大批量生产,宜采用一模多腔,考虑现有注射机的锁模力,注射量及瓶盖的精度和经济性目标,确定为模腔4,
模具二次顶出结构详解
二次頂出 一般情況下,從模具中取出成品,無論就是採用單一或者就是多元件得頂出機構,其頂出動作都就是一次完成。但就是,由於成品得形狀特殊,或者就是量產時得要求,如果在一次頂出後,成品仍然在模穴中,或者就是無法自動脫落時,就需要再增加一次頂出動作。這樣得頂出動作設計,稱為二次頂出。 二次頂出,能夠讓頂出流程順暢化,對於某些頂出行程需求較大得產品,利用二次頂出可以減少頂針在頂出時施加得力量,避免頂出時造成產品上得缺陷。 二次頂出機構,簡單來說,可以分為下列三大類: 一、單頂針板組合得二次頂出機構 二、雙頂針板組合得二次頂出機構 三、氣動/液壓得二次頂出機構 一、單頂針板組合得二次頂出機構 所謂單頂針板組合,就就是一般常見得單套頂針板組合(上頂針板及下頂針板各一),由於僅有單套得頂針板組合,因此射出機頂出得動作僅提供傳統得一次頂出;另一次頂出就必須配合其她得模具機構設計(例如彈簧)來進行。 單頂針板得二次頂出機構,可以分成下列幾類: 1、公母模板彈開式 2、公母模板拉開式 3、頂針板組合機構 4、浮動模仁 以下,將根據各種不同得設計,提供參考得設計圖面。 公母模板彈開式二次頂出
第一段頂出發生在公母模板開啟時。彈簧將模板(或局部模仁)頂出一小段距離。 第二段頂出由頂針板作動,利用頂針將產品頂離模穴。
利用彈簧完成二次頂出,在模具結構上就是最簡單得方法,需要額外加工得部分也很少。但就是,彈簧得缺點(彈性疲乏),也就是這種頂出方式得缺點。隨時注意彈簧就是否能夠順利動作,以及檢查第一段頂出得頂出行程,就是避免模具機構失效得安全措施。 公母模板彈開式二次頂出有幾種變形 1、彈簧推動模板改為彈簧推動『頂出入子』 上圖所示,就是利用彈簧推動整塊模板。實際應用時,可以根據產品得造型,改為推動頂出入子。例如下圖,這樣可以減少彈簧每次推動所需要克服得重量,增加彈簧得壽命。 2、如果第一段頂出得行程不需要很長,利用優力膠代替彈簧也就是一種可行得方法。 優力膠就是一種人工橡膠發泡製成得材料,它得壓縮比例不高,大約只有1/3;不能像線圈彈簧一樣,壓縮比例可以達到1/2。在硬度上它與氣壓彈簧有一點相似,就就是越壓到底越硬,但就是它在更短得行程內會增加得更硬。它得疲勞強度也不如線圈彈簧,但只要適度得潤滑,仍然可以維持很久。 優力膠比較麻煩得問題就是對溫度非常得敏感,在低溫時會變硬,在高溫時會變軟。使用者在使用上必須特別注意其壽命,模具維護時記得檢查並且更換有問題得材料。 公母模板拉開式二次頂出 雖然利用彈簧,可以在開模後進行脫料板得頂出,但就是對於大型模座來說,彈簧得力量就是不夠得。因此,有其她得機構來處理這樣得問題。 這種機構,我們稱為Tension Links,如下圖
扳手塑件塑料注射模具设计
* * * * 学院毕业设计(论文) 题目_扳手塑件塑料注射模具设计 姓名__*****__ 系(部)_机电工程系__ 专业机械制造与自动化 指导教师__*__*__ 2008年5月26 日
摘要 本设计主要是针对扳手的模具设计,通过对塑件进行工艺的分析和比较,最终设计出一副注塑模。该设计从产品结构工艺性,具体模具结构出发,对模具的浇注系统、模具成型部分的结构、顶出系统、冷却系统、注塑机的选择及有关参数的校核、都有详细的设计,同时并简单的编制了模具的加工工艺。通过整个设计过程表明该模具能够达到此塑件所要求的加工工艺。根据题目设计的主要任务是香皂盒注塑模具的设计。也就是设计一副注塑模具来生产香皂盒塑件产品,以实现自动化提高产量。针对香皂盒的具体结构,该模具是侧浇口的单分型面注射模具。 同时,在设计过程中,通过查阅大量资料、手册、标准、期刊等,结合教材上的知识也对注塑模具的组成结构(成型零部件、浇注系统、导向部分、推出机构、排气系统、模温调节系统)有了系统的认识,拓宽了视野,丰富了知识,为将来独立完成模具设计积累了一定的经验。 关键词:塑料,模具,分型面,注射机
Abstract This design is mainly directed against the soap box die design, through the technology of plastic parts for analysis and comparison, the final design an injection mold. The design process from the product structure, the structure of the specific die, die casting, mold forming part of the structure, the roof system, cooling system, the choice of injection molding machines and related parameters of the check, have the detailed design, And the establishment of a simple mold processing technology. Through the entire design process that the mold plastic parts can achieve this by the requirements of the processing technology. According to Title Design's main task is to soap box injection mold design. Which is designed to produce an injection mold plastic parts soap box products, so as to improve the automation of production. Soap box for the concrete structure, the die is the side gate of the single type of injection molds. At the same time, in the design process, through access to vast amounts of data, manuals, standards, periodicals, etc., with materials on the knowledge of the injection mold of the structure (forming parts, casting, direction of the launch, the exhaust system, Die-conditioning) system with the understanding, broaden the horizons and enrich the knowledge, complete independence for the future die design has accumulated some experience. Key words:plastic, molds, type face, injection machine