硫化促进剂的作用机理
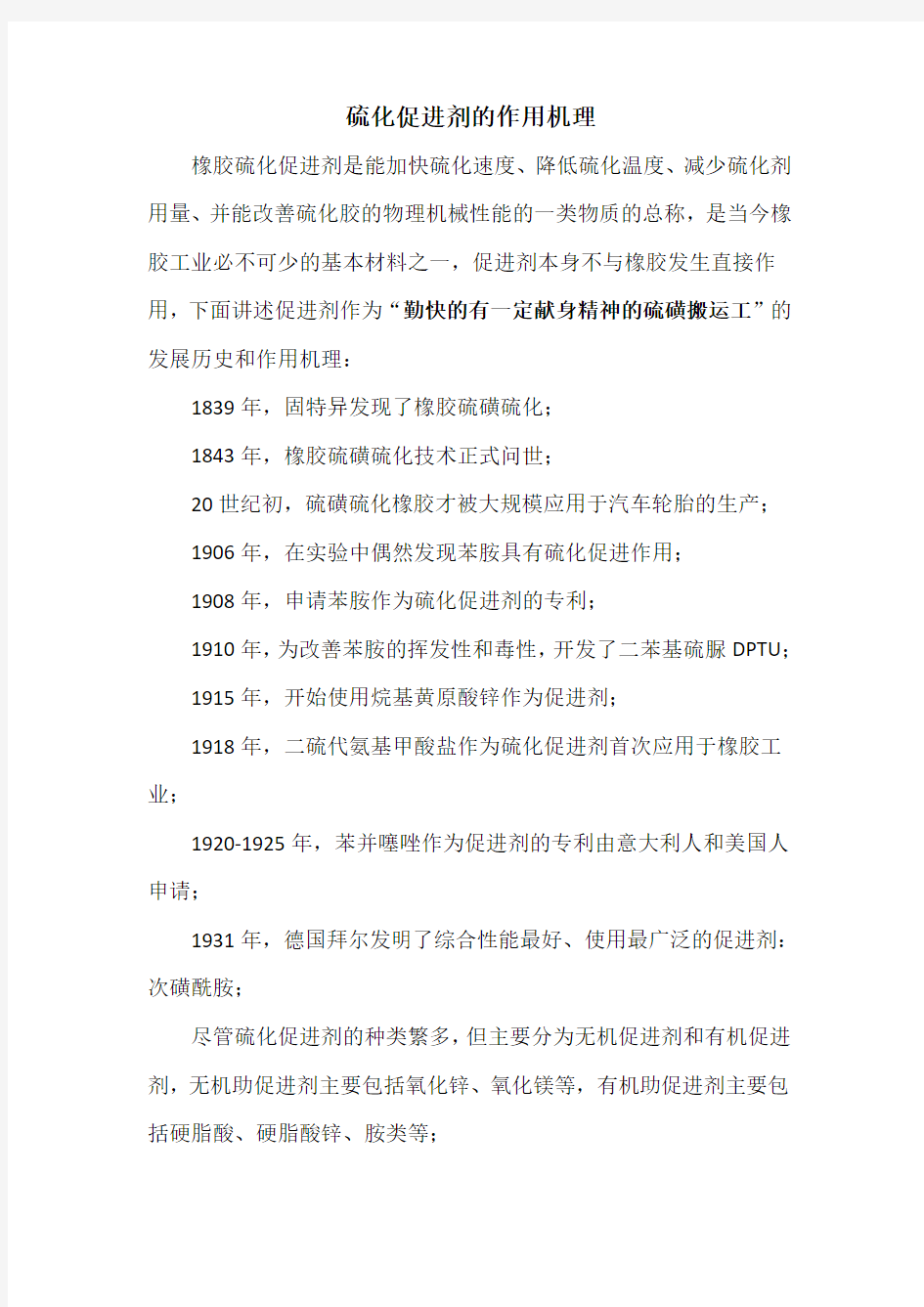

硫化促进剂的作用机理
橡胶硫化促进剂是能加快硫化速度、降低硫化温度、减少硫化剂用量、并能改善硫化胶的物理机械性能的一类物质的总称,是当今橡胶工业必不可少的基本材料之一,促进剂本身不与橡胶发生直接作用,下面讲述促进剂作为“勤快的有一定献身精神的硫磺搬运工”的发展历史和作用机理:
1839年,固特异发现了橡胶硫磺硫化;
1843年,橡胶硫磺硫化技术正式问世;
20世纪初,硫磺硫化橡胶才被大规模应用于汽车轮胎的生产;
1906年,在实验中偶然发现苯胺具有硫化促进作用;
1908年,申请苯胺作为硫化促进剂的专利;
1910年,为改善苯胺的挥发性和毒性,开发了二苯基硫脲DPTU;
1915年,开始使用烷基黄原酸锌作为促进剂;
1918年,二硫代氨基甲酸盐作为硫化促进剂首次应用于橡胶工业;
1920-1925年,苯并噻唑作为促进剂的专利由意大利人和美国人申请;
1931年,德国拜尔发明了综合性能最好、使用最广泛的促进剂:次磺酰胺;
尽管硫化促进剂的种类繁多,但主要分为无机促进剂和有机促进剂,无机助促进剂主要包括氧化锌、氧化镁等,有机助促进剂主要包括硬脂酸、硬脂酸锌、胺类等;
例如,天然橡胶单独用3质量份硫磺硫化时,硫化时间为5h,并用5质量份ZnO后缩短为4h,在并用1质量份促进剂MBT和1质量份硬脂酸,则只需20-30min即可完成硫化,并且所制得的硫化剂性能大为改善。
各类促进剂都是由不同官能基团组成的,不同基团在橡胶的硫化过程中又发挥不同影响。促进剂分子结构中含促进基团、活性基团、硫化基团,因为每种促进剂含有不同官能基,其促进活化或硫化特性也产生差异。
促进基团:结构为:R1-S-。在硫化过程中,促进剂分解出基团起促进作用,噻唑类、秋兰姆类、二硫代氨基甲酸盐类、次磺酰胺类都有这种促进基团;
活性基团:结构为:R2-N-。促进剂在硫化过程中放出胺基具有活化作用,大部分有机碱(或胺类促进剂)都有硫化促进活性作用,而且许多生物碱具有显著生理活性,如尼古丁(烟碱/1—甲基—2—(3—吡啶基)吡咯烷)、吗啡(吗啡碱)、可待因、海洛因、奎宁(金鸡纳碱)、冰毒(甲基苯丙胺)、摇头丸(亚甲基二氧苯丙胺)、K 粉(氯胺酮)等。
硫化基团:结构为:-S-S-、-S-S n-S-。在硫化时,硫载体被分解而放出活性原子硫,参与交联反应,硫载体中的含硫基团称为硫化基团。
促进剂的作用机理非常复杂,但是常规认识为:1.促进剂先均裂,生成促进剂自由基,此促进剂自由基可引发硫磺S8开环,并可与之
结合产生多硫自由基;2.上述自由基可引发橡胶分子生成自由基,由于橡胶分子中的α-亚甲基上的氢原子较活泼,因此反应主要发生在此亚甲基上,橡胶大分子链自由基与促进剂多硫自由基结合,生成连接活性多硫侧基的橡胶分子;3.这些橡胶分子多硫侧基可以裂解产生自由基,再与橡胶自由基结合,生成交联键。
在各种促进剂中,有的促进剂只有一种功能,例如MBT只有一种促进功能,而有的促进剂如TMTD具有多种功能,起活化、促进及硫化作用,从而影响硫化特性
在硫化过程中,促进剂可使橡胶的硫化反应发生很大的变化。在促进剂存在的条件下,降低了硫环的断裂活化能,由于促进剂本身的裂解,增加了体系中的自由基或离子浓度,加速了硫化链反应的引发和链增长反应,提高了硫化反应速度。
秋兰姆类促进剂的作用机理:如新材料公司已生产的TBzTD、DPTT,秋兰姆类促进剂含硫化物量高,属于超速促进剂,单用时可以直接硫化橡胶,这种体系称为无硫体系,也称硫载体或硫给予体;在硫化温度下,含硫的化合物裂解出活性硫,由于硫化物结构不同所含的硫量也不同,在硫化过程中,含硫的化合物首先分裂成自由基,再与橡胶大分子作用,按自由基链反应完成硫化作用。
二硫代氨基甲酸盐类促进剂的作用机理:如新材料公司已生产的ZBEC、ZDEC、ZDMC、ZDBC,属于超超速促进剂,使用二硫代氨基甲酸锌的混炼胶必须包含氧化锌,硬脂酸也会产生产生一些有益的效果,广泛应用于胶乳工业中。硫化体系,如果没有硫磺,这种促进剂不会
分解,在硫化温度下,含硫的化合物裂解出活性硫、可溶性锌离子,由于硫化物结构不同所含的硫量也不同,在硫化过程中,含硫的化合物首先分裂成自由基,再与橡胶大分子作用,按自由基链反应完成硫化作用。
含胺基促进剂的作用机理:这类促进剂具有中等的促进效果,与含硫促进剂机理不同,属离子型反应,胺类化合物的N-H键,在硫化温度下或其他物质的诱导作用下,很易发生离子不对称分裂,产生离子基,与橡胶大分子产生离子型的链反应,在硫化时,含胺促进剂与元素硫作用,发生氧化还原反应使交联活性增加,另一方面是多硫胺的负离子基可分裂出活性硫,参与橡胶大分子的交联。
硫化促进剂中含有促进基团、活性基团、硫化基团,同样,橡胶的硫化体系包括硫化剂、硫化促进剂和促进活性剂,一般来说橡胶的交联密度主要与橡胶的硫化剂用量多少有关,当然增加含有促进基团的促进剂用量也能以单硫键或双硫键的形式来提高交联密度,一般硫磺硫化体系中的促进剂用量较少,所以决定交联密度的大小的主要还是硫磺的用量。对于精细化工产品,一般最了解自身产品深入性质及同行业类似产品应用机理的,往往是产品下游应用企业的技术专家,对于专业的系统促进剂选用,橡胶硫化专家会根据应用性质需要来筛选结构基团。
河南连连利源新材料有限公司
黄勇
硫化促进剂MBTS
硫化促进剂MBTS(DM)工艺操作规程
目录 1、产品说明 1.1 产品名称 1.2 产品的物理及化学性质 1.3 产品质量标准 1.4 产品的用途 2、原料规格及性质 3、生产的基本原理及化学反应方程式3.1 生产的基本原理 3.2 化学反应方程式 4、工艺流程叙述 4.1 生产工艺流程方框示意图 4.2 生产工艺流程叙述 5、生产工艺条件一览表 6、可能发生的不正常现象及处理方法 7、三废及处理方法 8、吨产品消耗定额
1、产品说明 1.1产品名称:促进剂MBTS(DM) 化学名称:二硫化二苯并噻唑 分子式:C14H8N2S4 结构式:(略) 分子量:332.5 1.2产品的物理和化学性质 外观为浅黄色粉末,熔点162-180℃。溶于二硫化碳、苯、甲苯及三氯甲烷等,不溶于水、乙酸乙酯。易燃烧,其粉尘与空气混合有爆炸危险。主要用于制造轮胎、胶管、胶带、胶鞋、胶布和一般工业制品,也用于白色和浅色制品。 1.3产品质量标准:GB/T11408-2003 1.4产品的用途 作天然橡胶、合成橡胶、再生橡胶通用型促进剂。它的硫化临界温度较高(130℃),温度在140℃以上活性增加,有显著的后效性,操作安全。在G型氯丁橡胶中可作延迟剂,在W型氯丁橡胶中作硫化
改性剂。用于胶乳时,硫化速度较慢,但能减少含促进剂EZ胶乳胶料早期硫化的倾向。本品在胶料中易分散,不污染,但有苦味,不宜用于与食物接触的制品,主要用于制造轮胎、胶管、胶带、胶鞋、胶布和一般工业制品,也用于白色和浅色制品。 2、原材料规格及性质 2.1 M钠盐(2-硫醇基苯并噻唑钠盐) 分子式:C7H4NS2Na 物化性质:浅黄色透明液体,易溶于水,有碱性腐蚀,PH为10.5-10.8,。如皮肤接触立即用水清洗。 2.2 双氧水(过氧化氢) 分子式:H2O2 物化性质:无色透明液体,有微弱的特殊气味。溶于水、醇、醚,不溶于苯、石油醚。工业品呈酸性,强氧化剂,具有腐蚀性。受热易分解,禁止与易燃物、强还原剂、铜、铁、锌等活性金属粉末接触。皮肤接触本品可引起皮炎。如皮肤接触用大量水冲洗。 2.3 硫酸 分子式:H2SO4 物化性质:无色粘绸状液体,工业品规格大于92%以上。能与水混溶,稀硫酸腐蚀金属。浓硫酸与水混合时产生大量的热。稀释硫酸时,只能将浓硫酸逐渐加入水中,且不可将水加入浓硫酸中,以免发生危险。
抗硫化返原剂
抗硫化返原剂 对于配方设计人员来说,硫黄交联键的返原一直是个棘手的问题,至今仍未找到理想的解决方法。每一种新方法都要付出一定的代价,改善耐热和抗返原性能则要损害产量、加工安全和/或疲劳和撕裂性能。 要解决这个问题就必须首先讨论返原的定义。返原是多硫键的热降解,它导致交联密度下降,主链改性。返原实际上导致胶料物理性能下降,定伸应力、回弹性和其它一些性能都随返原而变劣。当胶料发生过硫硫化,或硫化胶经受无氧老化时,则容易出现返原现象。 返原现象常出现在高温硫化的NR胶料中或在适中温度下硫化时间过长的胶料中。返原的实际意义是它对硫化胶性能的影响可以利用流变仪方便地对其进行监控。产品在使用过程中的返原同样须引起配方设计者的注意。许多胶料(越野轮胎、载重轮胎、公共汽车轮胎、赛车轮胎、航空轮胎和高性能轮胎的胶料)在使用过程中的生热足以导致交联网络降解。该过程是自发展过程,因为返原降低了定伸应力,反过来又加速了热的生成,以致引起产品早期损坏或使用寿命缩短。在实验室,屈挠试验机可以检测胶料在反复屈挠周期中引起的不可逆变化。 既然性能下降并非所愿,那么提出各种方法以补偿或减轻返原效应就不足为怪了。最简单而且应用最广的就是采取低温硫化。在130℃下硫化的NR胶料不会导致硫化返原,而在更高温度下则会出现返原。但是低温硫化导致硫化时间延长,胶料在170℃下硫化到达正硫化的时间是130℃下硫化的1/16。而且该方法并不能解决产品在使用过程中的返原现象,因为交联产生的是多硫键,缺乏热稳定性。为解决返原而不降低产量,配方设计人员应用了有效或半有效硫化体系,即应用高促进剂/硫黄比或采用硫黄给予体以减少多硫键的生成数量。因为双硫键和单硫键具有更高的稳定性,所以抗返原性得到了提高。但是,这有损于胶料的焦烧安全、屈挠疲劳和强度性能。而且运用有效硫化体系硫化速度快,总硫含量低,故不适宜胶料与金属或织物的粘合。这就限制了采取低硫和硫黄给予体硫化体系的胶料在动态条件下的应用。 另一种抑制返原的方法是采取过氧化物硫化,过氧化物硫化体系产生了C—C交联键,C—C交联键键能高,从而有极高的热稳定性。因为聚合物通过C—C
常用的橡胶促进剂大全
常用的橡胶促进剂大全 根据化学结构的不同,促进剂分可以为噻唑类、秋兰姆类、次磺酰胺类、胍类、二硫代氨基甲酸盐类、醛胺类、黄原酸盐类和硫脲类等八大类。 一、噻唑类这是有机促进剂中较早的品种。属于酸性促进剂。其特点是具有较高的硫化活性,能赋予硫化胶良好的耐老化性能和耐疲劳性能。所以在橡胶工业中应用比较广泛,耗用量较大。主要品种有如下两种。(1)2硫醇基苯并噻唑商品名称为促进剂M。本品为淡黄色粉末,味极苦,无毒,贮藏稳定。为通用型促进剂,对天然橡胶及二烯类通用合成橡胶具有快速促进作用,硫化平坦性较好,硫化临界温度为125℃,混炼时有脑炎烧的可能。在橡胶中容易分散,不污染,但不适于食品用橡胶制品。用作第一促进剂的用量为1~2份,作第二促进剂的用量为0.2~0.5份。还可用于天然橡胶的塑解剂。(2)二硫化二苯并噻唑商品名称为促进剂DM。本品为淡黄色粉末,味苦,无毒,贮藏时稳定。其特性和用途与M 相似,但硫化临界温度为130℃。140℃以上活性增大,有较好的后效性,硫化操作安全。常与其它促进剂并用以提高其活性。 二、秋兰姆类这类促进剂呈酸性。属于超速促进剂。包括一硫化秋兰姆、二硫化秋兰和多硫化秋兰。二硫化秋兰姆可用于无硫黄硫化有硫化剂。作为促进剂一般用作第二促进剂,与噻唑类和次磺酰胺类促进剂并用以提高硫化速度。与次磺酰胺类促进剂并用时,能延迟胶料开始反应的时间,硫化开始以后反应又能进行得特别快,硫化胶的硫化程度也比较高。这种产用体系在低硫硫化中特别重要。采用秋兰姆促进剂的硫化胶的物理机械性能和耐老化性能受促进剂和硫黄用量比例的影响。一般来讲,硫黄用量正常,硫化胶的定伸强度较高,其它物理机械性能也比较好;当硫黄用量较低,促进用量较大时,则硫化胶的耐热老化性能可以得到改善。秋兰姆类促进剂最常用的品种是二硫化四甲基秋兰姆,商品名称为促进剂TMTD,简称促进剂TT。它既可作促进剂使用,也可作硫化剂使用。用作促进剂时用量一般为0.2~0.3份。 三、次磺酰胺类这是一类迟效性促进剂,呈酸性。具有焦烧时间长、硫化活性大的特点。硫化胶的硫化程度比较高,物理机械性能优良,耐老化性能相当好。胶料具有较宽广的硫化平坦性。由于合成橡胶的发展和大量应用及高分散性炉法炭黑的推广应用,特别需求迟效性良好的促进剂。因而该类促进剂占有相当重要的地位,成为近年来发展最快,也是最有前途的一类促进剂。目前世界上使用的各种促进剂中,遥以次横酰胺类为主,其中大量应用的有CZ、NOBS、NS 、DZ和OTOS等,它们均为硫醇基苯并噻唑的衍生物。(1)N-环己基-2-苯并噻唑次磺酰胺商品名称为促进剂CZ。本品为淡黄色粉末,稍有气味,无毒,比重为1.31~1.34,熔点不低于94℃,贮藏稳定。其硫化临界温度为138℃,兼有抗焦烧性能优良和硫化速度快的优点。本品变色轻微、为喷霜、硫化胶耐老化性能优良。一般用量为0.5~2份。(2)N-氧二乙撑-2-苯并噻唑次磺酰胺或2-(4-吗啡啉基硫代)苯并噻唑商品名称为促进剂NOBS。本品为淡黄色粉末,无毒。比重为1.34~1.40。熔点为80℃~86℃。遇热时逐渐分解,故应低温贮存。贮存时间超过6个月以上时,胶料焦烧倾秘增加,硫化临界温度在138℃以上,焦烧时间比促进剂CZ更长,操作更安全。本品在胶料中容易分散,不喷霜、变色轻微。一般用量范围为0.5~2.5份,并配以2~0.5份硫黄。(3)N-叔丁基苯并噻唑次磺酰胺商品名称为促进剂NS。本品为淡黄色粉末,有特殊气味。比重为1.29,熔点不你低于105℃。其性能和用法与促进剂CZ、基本相似,但在天然橡胶中的迟效性更大。本品变色及污染轻微。(4)N,N-二环己基-2-2苯骈噻唑次磺酰胺商品名称为促进剂DZ。本品为棕黄色粉末,无臭。比重为1.2。熔点不低于90℃。贮存稳定。本品在橡胶中分散性良好。硫化平坦性能与促进剂CZ相似。硫化胶动态物理机械性能比较好,弹性和定伸强度高。但因硫化胶有苦
抗氧剂协同作用机理
抗氧剂的协同作用 聚合物稳定化助剂种类繁多,功能各异。但大量研究结果表明,不同类型,甚至同一类型、不同品种的抗氧剂之间都有可能存在协同或对抗作用。汽巴精化(Ciba—Geigy)公司开发的Irganox B系列复合型抗氧剂的研究表明,抗氧剂之间复配得当,不仅可以提高产品性能,增强抗氧效果,还可降低成本;但如果搭配不当,不但起不到抗氧作用,可能还会加速聚合物的老化。受阻酚类抗氧剂以其抗氧效果好、热稳定性高、低毒等诸多优点近年来倍受人们关注。但抗氧剂复配是否得当直接影响抗氧效果的好坏。因此,研究抗氧剂复配时的作用机理显得尤为重要。近年来,世界各大抗氧剂的生产厂商都在致力于研究开发复合型抗氧剂,而熟知各种抗氧剂之间的协同作用机理对抗氧剂新品种开发具有重要的指导 意义 1 受阻酚类抗氧剂的作用机理 聚合物材料在高温加工或使用过程中,由于氧原子的袭击会使其发生氧化降解。经过多年的研究发现,聚合物的A动氧化过程是一系列A由基反应过程。反应初期的主要产物是由氢过氧化物在适当条件下分解成活性自由基,该自由基又与大分子烃或氧反应生成新的自由基,这样周而复始地循环,使氧化反应按自由基链式历程进行。 在聚合物中添加抗氧剂,就是为了捕捉链反应阶段形成的自由基R.和R00 .,使它们不致引起有破坏作用的链式反应;抗氧剂还能够分解氢过氧化物RO0H,使其生成稳定的非活性产物。按作用机理,抗氧剂可分为主抗氧剂和辅助抗氧剂。主抗氧剂能够与自由基R.,ROO .反应,中断活性链的增长。辅助抗氧剂能够抑制、延缓引发过程中自由基的生成,分解氢过氧化物,钝化残存于聚合物中的金属离子[1]。 作为主抗氧剂的受阻酚类抗氧剂是一类在苯环上羟基(~OH)的一侧或两侧有取代基的化合物。由于一OH受到空间障碍,H原子容易从分子上脱落下来,与过氧化自由基(ROO .)、烷氧自由基(RO.)、羟自由基(.OH)等结合使之失去活性,从而使热氧老化的链反应终止,这种机理即为链终止供体机理[2]。 在聚合物老化过程中,如果可以有效地捕获过氧化自由基,就可以终止该氧化过程。但生成过氧化自由基的反应速率极快,所以在有氧气存在的条件下,自由基捕获剂便会失效。在受阻酚类抗氧剂存在的情况下,1个过氧化自由基(R00 7)将从聚合物(RH)上夺取1个质子,打断这一系列自由基反应,这是自动氧化的控制步骤。当加入受阻酚抗氧剂时,它比那些聚合物更易提供质子,即提供了一个更加有利的反应形成酚氧自由基,这使聚合物相对稳定,不会进一步发生氧化。 除此之外,受阻酚还可以进行一些捕捉碳自由基的反应。如上式的2,4,6一自由基可以生成二聚物,而这种二聚物又可与过氧化自由基反应使其失去活性,自身则变成稳定的醌分子[2]。由于每个受阻酚可以捕捉至少2个自由基,故其抗老化的效果较好。
促进剂
促进剂M(MBT) 化学名称:2-硫醇基苯并噻唑 分子式:C7H5NS2 结构式: 分子量167.25 技术指标: 项目指标 优级品一级品二级品 外观淡黄色或白色粉末 熔点℃≥173.0 171.0 170.0 加热减量% ≤0.30 0.40 0.50 灰份%≤0.30 0.30 0.30 筛余物(150 μm) %≤ 0.0 0.10 0.10 用途: 通用型促进剂,广泛用于各种橡胶,对天然胶和一般硫黄硫化合成胶具有快速促进作用,硫化平坦性很宽。在氯丁胶和无硫硫化体系中又可作硫化延缓剂和抗焦烧剂。本品还用作天然胶的化学增塑剂。在橡胶中易分散,不污染,一般用量1-2份。 本品精制级可用作头胞类药物及其他药物的中间体。 性状: 比重1.42,有苦味。易溶于醋酸乙酯、丙酮。溶于二氯甲烷、乙醚、氯仿、乙醇等有机溶剂和碱性碳酸盐溶液中。微溶于苯,不溶于水和汽油。产品贮存稳定性两年以上。 包装: 聚丙烯编织袋或纸袋、纸桶,内衬塑料薄膜袋,净25KG/袋。
促进剂DM(MBTS) 化学名称:二硫化二苯并噻唑 分子式:C14H8N2S4 结构式: 分子量:332.46 技术指标: 项目指标 优级品一级品二级品 外观淡黄色或白色粉末 熔点℃≥170.0 165.0 160.0 加热减量% ≤0.30 0.40 0.50 灰份%≤0.30 0.50 0.70 筛余物(150 μm) %≤ 0.0 0.10 0.10 用途: 天然胶、合成胶、再生胶通用型促进剂,一般多与其他促进剂并用。适用于轮胎、胶带等制品。 性状: 味苦无毒,不溶于水。溶于酒精、乙醚等。 包装: 聚丙烯编织袋或牛皮纸袋,内衬塑料薄膜袋,净25kg/袋。 促进剂CZ(或CBS) 化学名称:N-环己基-2-苯并噻唑次磺酰胺 分子式:C13H16N2S2 结构式: 分子量:264.41 技术指标:
抗氧化剂的作用机理研究进展
抗氧化剂的作用机理研究进展 摘要:食品抗氧化剂的作用比较复杂。BHA和BHT等酚型抗氧化剂可能与油脂氧化所产生的过氧化物结合,中断自动氧化反应链,阻止氧化。抗坏血酸、异抗坏血酸及其钠盐因其本身易被氧化,因而可保护食品免受氧化。另一些抗氧化剂可能抑制或破坏氧化酶的活性,借以防止氧化反应进行。研究食品抗氧化剂的作用机理并合理使用抗氧化剂不仅可延长食品的贮存期,给生产者、经销者带来良好的经济效益,也给消费者提供可靠的商品。 关键词:抗氧化剂作用机理自由基现状前景展望 食品的变质,除了受微生物的作用而发生腐败变质外,还会和空气中的氧气发生氧化反应。食品氧化不仅会使油脂或含油脂食品氧化酸败(哈败),还会引起食品发生退色、褐变、维生素破坏,从而使食品腐败变质,降低食品的质量和营养价值,氧化酸败严重时甚至产生有毒物质,危及人体健康。防止食品氧化变质,在食品的加工和储运环节中,除采取低温、避光、隔绝氧气以及充氮密封包装等物理的方法还可以配合使用一些安全性高、效果大的食品抗氧化剂以防止食品发生氧化变质。 1 食品抗氧化剂的定义 食品抗氧化剂是指防止或延缓食品氧化,提高食品稳定性和延长食品储藏期的食品添加剂。具有抗氧化作用的物质有很多,但可用于食品的抗氧化剂应具备以下条件:①具有优良的抗氧化效果; ②本身及分解产物都无毒无害;③稳定性好,与食品可以共存,对食品的感官性质(包括色、香、味等)没有影响;④使用方便,价格便宜。[1] 2 食品抗氧化剂的分类 目前,对食品抗氧化剂的分类,按来源可分为人工合成抗氧化剂和天然抗氧化剂(如茶多酚、植酸等)。按溶解性可分为油溶性、水活性和兼溶性三类。油溶性抗氧化剂有BHA、BHT等;水溶性抗氧化剂有维生素C、茶多酚等;兼溶性抗氧化剂有抗坏血酸棕榈酸酯等。按作用方式可分为自由基吸收剂、金属离子螯合剂、氧清除剂、过氧化物分解剂、酶抗氧化剂、紫外线吸收剂或单线态氧淬灭剂等。[2] 3 食品抗氧化剂的作用机理 由于抗氧化剂种类较多,抗氧化的作用机理也不尽相同,归纳起来,主要有以下几种: 一是抗氧化剂可以提供氢原子来阻断食品油脂自动氧化的连锁反应,从而防止食品氧化变质; 二是抗氧化剂自身被氧化,消耗食品内部和环境中的氧气从而使食品不被氧化; 三是抗氧化剂通过抑制氧化酶的活性来防止食品氧化变质。 四是将能催化及引起氧化反应的物质封闭,如络合能催化氧化反应的金属离子等。[3]
橡胶硫化促进剂
橡胶硫化促进剂 简介 天然胶与合成胶用促进剂,具有宽广的硫化范围,可单独使用,或与二硫代氨基甲酸盐类、秋兰姆类、胍类和其它碱性促进剂并用。主要用于制造轮胎、胶带、胶鞋和其他工业橡胶制品。 主要产品 橡胶硫化促进剂ETU(Na-22) 、橡胶硫化促进剂DETU 、橡胶硫化促进剂ZDC(EZ) 、橡胶硫化促进剂ZDMC(PZ) 橡胶硫化促进剂ZDBC(BZ) 、橡胶硫化促进剂ZMBT(MZ) 、橡胶硫化促进剂TMTM 、橡胶硫化促进剂MBT(M)、橡胶硫化促进剂MBTS(DM) 其中橡胶硫化促进剂ETU(Na-22)又称乙烯硫脲,其详细指标如下: 分子式: C3H6N2S 结构式: 分子量: 102.17 CAS编号: 155-04-4 同类名称: Perkacit ETU,Robac 22,Rodanin S 62,Ekagom CLB 指标名称:粉料 纯度(%,≥) 98.0 外观(目测:白色粉末 初熔点(℃,≥) 195.0 终熔点(℃,≥) 195.0-200.0 加热减量(%,≤) 0.30 灰份(%,≤) 0.30 筛余物(63μm)(%,≤) 0.30 杂质(个/g) 10 性状:由乙醇中结晶的产品为针状结晶,从戊醇中结晶的产品为柱状捷径。比重1.42-1.43。熔点203-204℃。有苦味。易溶于水,溶于乙醇、甲醇、乙二醇和吡啶,不溶于丙酮、乙醇、氯仿等。
用途:本品系各种类型氯丁胶、氯磺化聚氯乙烯橡胶、氯乙醇橡胶、聚丙烯酸酯橡胶用的促进剂。适于金属氧化物作硫化剂,尤以氧化镁、氧化锌作硫化剂时效果更好。操作安全,不易燃烧。本品特别适用于54-1(W)型及通用GN型氯丁胶。在胶料中易分散、不污染、不变色。在一般制品中用量为0.25-1.5份,在54-1(W)型氯丁胶耐水制品中用量为0.2-0.5份,并要配以10-20份的一氧化铅。 包装和储存 25Kg纸塑复合袋、牛皮纸袋或集装塑料袋。储存在阴凉、干燥、通风的地方。避免阳光 橡胶硫化促进剂的定义 加入橡胶胶料后能降低硫化温度或缩短硫化时间的物质,称之为硫化促进剂。 促进剂加入胶料中,能促使硫化剂活化,从而加速硫化剂与橡胶分子间的交联反应,达到缩短硫化时间、降低硫化温度、增加产量、降低生产成本的实用效果。 橡胶硫化促进剂的分类 按硫化速度分类 超超速级:二硫代氨基甲酸盐、黄原酸盐类 超速级:秋兰姆 准超速级:噻唑、次黄酰胺类 中速级:胍类 慢速级:醛胺类、硫脲类 按酸碱性分类 酸性促进剂:噻唑、秋兰姆、二硫代氨基甲酸盐、黄原酸盐类。 碱性促进剂:胍类和醛胺类。 中性促进剂:次黄酰胺类和硫脲类。 新型促进剂 新型促进剂的实例有以下几种: 新型促进剂
八大促进剂
八大促进剂 根据化学结构不同,促进剂分可以为噻唑类、秋兰姆类、次磺酰胺类、胍类、二硫代氨基甲酸盐类、醛胺类、黄原酸盐类和硫脲类等八大类。 类型商品名称英文缩 写化学名称 胍类促进剂 D DPG 二苯胍 促进剂DT DOTG 二邻甲苯胍 促进剂 BG OTBG 邻甲苯基二胍 噻唑类促进剂 M MBT 2-硫醇基苯并噻唑 促进剂 DM MBTS 二硫化二苯并噻唑 次硫酰胺类促进剂 CZ CBS
N-环己基-2-苯噻唑基次磺酰胺 促进剂 NS TBBS N-叔丁基-2-苯噻唑基次磺酰胺 促进剂NOBS(MSA)OBS N-氧联二亚乙基-2-苯噻唑基次磺酰胺 促进剂 DZ DZ N,N-二环己基-2-苯噻唑基次磺酰胺 促进剂OTOS OTOS N-氧联二亚乙基硫代氨基甲酰-N`-氧联二亚乙次磺酰胺 秋兰姆类促进剂 TS TMTM 一硫化四甲基秋兰姆 促进剂 TT TMTD 二硫化四甲基秋兰姆 促进剂 TET TETD 二硫化四乙基秋兰姆 促进剂 TBT TBTD
二硫化四丁基秋兰姆 促进剂 TRA DPTT 四硫化双戊撑秋兰姆 促进剂 TE TE 二硫化二乙基二苯基秋兰姆 促进剂 TBzTD TBzTD 二硫化四苄基秋兰姆 二硫代氨基甲酸盐类: 促进剂PZ(ZDMC)ZnMDC 二甲基二硫代氨基甲酸锌 促进剂EZ (ZDEC)ZnEDC 二乙基二硫代氨基甲酸锌 促进剂BZ (ZDBC)ZnBDC 二丁基二硫代氨基甲酸锌 促进剂 PX ZnBzDC
乙基苯基二硫代氨基甲酸锌 促进剂 ZnBzDC ZnBzDC 二苄基二硫代氨基甲酸锌 促进剂 TeEDC TeEDC 二乙基二硫代氨基甲酸碲 促进剂 TTEE FeMDC 二甲基二硫代氨基甲酸铁 促进剂 TTUC CuMDC 二甲基二硫代氨基甲酸铜 硫代磷酸盐类 促进剂 ZDEP ZDEP 二乙基二硫代磷酸锌 促进剂 ZDBP ZDBP 二丁基二硫代磷酸锌 促进剂 ZADP
橡胶促进剂的分类
橡胶促进剂的分类 硫化促进剂简称为促进剂。凡能加快硫化反应速度,缩短硫化时间,降低硫化反应温度,减少硫化剂用量产能提高或改善硫胶有物理机械性能的配合剂,称为硫化促进剂。 应用促进剂可以提高橡胶制品的生产效率,降低产品成本,可以提高的改善制品的物理机械性能,使厚制品质量均匀,并改善制品的外观质量并使色泽鲜艳。 目前橡胶工业采用的促进剂种类很多,按其性质和化学组成可以分为两大类:无机促进剂、有机促进剂。 无机促进剂使用最早,但因促进效果小,硫化胶性能差,除在外别情况仍少量使用以外,绝大多数场合已为有机促进剂所取代。有机促进剂促进效果大,硫化特性好,硫化胶有物理机械性能优良,因而发展迅速。 随着合成橡胶品种和用途有不断发展,现有促进剂名目日益繁杂,但目前最常用的亦不过数十种。 促进剂按其化学结构、促进效果大小、以及与硫化氯反应所呈现和酸碱性分类。 根据化学结构的不同,促进剂分可以为噻唑类、秋兰姆类、次磺酰胺类、胍类、二硫代氨基甲酸盐类、醛胺类、黄原酸盐类和硫脲类等八大类。 一、噻唑类 这是有机促进剂中较早的品种。属于酸性促进剂。其特点是具有较高的硫化活性,能赋予硫化胶良好的耐老化性能和耐疲劳性能。所以在橡胶工业中应用比较广泛,耗用量较大。主要品种有如下两种。 (1)2硫醇基苯并噻唑商品名称为促进剂M。 本品为淡黄色粉末,味极苦,无毒,贮藏稳定。为通用型促进剂,对天然橡胶及二烯类通用合成橡胶具有快速促进作用,硫化平坦性较好,硫化临界温度为125℃,混炼时有脑炎烧的可能。在橡胶中容易分散,不污染,但不适于食品用橡胶制品。用作第一促进剂的用量为1~2份,作第二促进剂的用量为0.2~0.5份。还可用于天然橡胶的塑解剂。 (2)二硫化二苯并噻唑商品名称为促进剂DM。 本品为淡黄色粉末,味苦,无毒,贮藏时稳定。其特性和用途与M相似,但硫化临界温度为130℃。140℃以上活性增大,有较好的后效性,硫化操作安全。常与其它促进剂并用以提高其活性。 二、秋兰姆类 这类促进剂呈酸性。属于超速促进剂。包括一硫化秋兰姆、二硫化秋兰和多硫化秋兰。二硫化秋兰姆可用于无硫黄硫化有硫化剂。作为促进剂一般用作第二促进剂,与噻唑类和次磺酰胺类促进剂并用以提高硫化速度。与次磺酰胺类促进剂并用时,能延迟胶料开始反应的时间,硫化开始以后反应又能进行得特别快,硫化胶的硫化程度也比较高。这种产用体系在低硫硫化中特别重要。 采用秋兰姆促进剂的硫化胶的物理机械性能和耐老化性能受促进剂和硫黄用量比例的影响。一般来讲,硫黄用量正常,硫化胶的定伸强度较高,其它物理机械性能也比较好;当硫黄用量较低,促进用量较大时,则硫化胶的耐热老化性能可以得到改善。 秋兰姆类促进剂最常用的品种是二硫化四甲基秋兰姆,商品名称为促进剂TMTD,简称促进剂TT。它既可作促进剂使用,也可作硫化剂使用。用作促进剂时用量一般为0.2~0.3份。 三、次磺酰胺类 这是一类迟效性促进剂,呈酸性。具有焦烧时间长、硫化活性大的特点。硫化胶的硫化程度比较高,物理机械性能优良,耐老化性能相当好。胶料具有较宽广的硫化平坦性。由于合成橡胶的发展和大量应用及高分散性炉法炭黑的推广应用,特别需求迟效性良好的促进剂。因而该类促进剂占有相当重要的地位,成为近年来发展最快,也是最有前途的一类促进剂。
抗硫化返原剂PK 900对丁腈橡胶性能的影响
加工应用 合成橡胶工业,2008-11-15,31(6):472~474 C H I NA SY NTHETI C RUB B ER I N DUST R Y 抗硫化返原剂PK900对丁腈橡胶性能的影响 贺春江1,陈传志2,李雪春2,张宪清2,赵红祥3 (11中国铁道科学研究院金属及化学研究所,北京100081;21中国铁道科学研究院铁道部标准计量研究所, 北京100081;31河南南阳天一密封制品有限公司,河南南阳474350) 摘要:以N,N′-间甲基苯基双(3-甲基马来酰亚胺)(简称PK900)作过氧化二异丙苯的交联助 剂,研究了其对丁腈橡胶(NBR)硫化胶耐热性、耐溶剂性和物理机械性能的影响。结果表明,加入PK 900可以提高N BR硫化胶的交联密度,改善NBR硫化胶的耐热性和耐溶剂性;虽然物理机械性能稍有 下降,但用量的增加对该性能的影响并不大。 关键词:N,N′-间甲基苯基双(3-甲基马来酰亚胺);过氧化二异丙苯;助交联剂;丁腈橡胶;交联密度;耐热性;耐溶剂性;物理机械性能 中图分类号:T Q314124 文献标识码:B 文章编号:1000-1255(2008)06-0472-03 以过氧化二异丙苯(DCP)硫化的丁腈橡胶(NBR)虽已具有很好的耐热性、耐溶剂性和弹性,但为了进一步提高这些性能,常用硫黄、三聚氰酸三烯丙酯及N,N-间苯撑双马来酰亚胺(HVA-2)等作为DCP的助交联剂[1-3]。N,N′-间甲基苯基双(3-甲基马来酰亚胺)(简称PK900)是一种效果很好的抗硫化返原剂,当以其作为天然橡胶(NR)的助交联剂时,它能够参与交联反应,形成长的、柔顺的碳碳交联键,抑制硫化返原的发生,使NR硫化胶具有低生热、高模量保持率和优良的耐疲劳性能[4]。PK900与H VA-2有类似的分子结构[4-6],由于PK900分子中的2个双键间距离更远,所以其参与交联所形成的碳链也更长更柔顺。本工作以PK900作为DCP的助交联剂,研究了其对NBR硫化胶耐热性、耐溶剂性和物理机械性能的影响。 1 实验部分 111 原材料 DCP,上海高桥石油化工公司产品。PK900,其分子式见图1,美国Flexsys公司提供。NBR,牌号为N,中国石油兰州石化公司产品。炭黑,牌号为N55,河北沙河炭黑厂产品。其他原材料均为市售品 。 Fig1 Structure for m ula of PK900 112 实验方法 NBR硫化胶的基本配方(质量份):NBR 100,硬脂酸110,炭黑50,DCP变量(110,114, 116),PK900变量(110,210,310)。 在广东湛江橡塑机械制造厂生产的S(X) K-160A型冷辊开炼机上混炼,辊温为50℃左 右,NBR先薄通5次,依次加入硬脂酸、炭黑,混 炼均匀后加入DCP及PK900。停放2d,适当返 炼后在上海橡胶机械制造厂生产的25t平板硫化 机上硫化,硫化温度为170℃,时间为12m in。 113 分析与测试 硫化特性 用上海埃尔法仪器科技有限公司生产的MDR2000型无转子硫化仪测试混炼胶的 硫化曲线,测试温度170℃。 ①收稿日期;修订日期63。 作者简介贺春江(6—),男,硕士,助理研究员。已发表论 文余篇。 41 :2007-07-27:2008-0-1 :197 10
橡胶用秋兰姆类硫化促进剂简介
橡胶用秋兰姆类硫化促进剂简介 秋兰姆类促进剂是在橡胶制品中广泛应用的硫化促进剂。它包括一硫化秋兰姆、二硫化秋兰姆和多硫化秋兰姆。其中二硫化秋兰姆和多硫化秋兰姆在常规硫化温度下易释放出活性硫,使胶料不加硫黄即可进行硫化即称为“无硫硫化”。用二硫化秋兰姆作硫化促进剂时多采用二硫化四甲基秋兰姆(促进剂TMT D)、二硫化四乙基秋兰姆(促进剂T ETD)以及二硫化甲基苯基秋兰姆(M PhT D)等。 一硫化四甲基秋兰姆(TMTM)和二硫化四甲基秋兰姆(TMT D)都是性能较好的秋兰姆类橡胶硫化促进剂,但近年来发现它们在硫化时会产生亚硝酸胺,因此,人们积极开发出性能更加优异且不会产生致癌物质的新型秋兰姆类硫化促进剂。Cromp t on公司开发成功烷基化三亚乙基四胺二硫化秋兰姆(TATD),其结构类似于其它秋兰姆二硫化物,只是它含有高分子量的长键烷基不同于其它二硫化秋兰姆。其分子量高于其它二硫化秋兰姆2到4倍。由于它的分子量高,挥发性很低,在实际应用中不会产生亚硝酸胺,是一种亚硝酸胺安全的创新型橡胶超硫化促进剂。它适合于天然橡胶、丁苯橡胶、顺丁橡胶、丁腈橡胶、乙丙橡胶以及各类橡胶的共混物。 二硫化四苄基秋兰姆(T BzT D)是橡胶促进剂秋兰姆类产品之一,是一种高效、绿色硫化促进剂,适用于天然橡胶、顺丁橡胶、异戊橡胶、丁苯橡胶、丁腈橡胶、丁基橡胶、三元乙丙橡胶和乳胶,其硫化促进效果与TMT D相似,硫化速度稍逊于TMT D,但稳定性胜于TMT D,广泛适用于制造电线电缆、轮胎、胶带、着色透明制品、鞋类、耐热制品等,并且不产生可致癌亚硝胺,是一种绿色、安全、环保、高效的橡胶硫化促进剂,可替代TMT D,T ETD、MPhTD,加工安全性更好,拥有更长的焦烧时间,可作为天然橡胶、丁基橡胶和丁苯橡胶的快速硫化主促进剂或助促进剂,有时也可用于PVC橡胶硫化抑制剂。T BzT D 分子量大,熔点高,不易分解,故不产生可致癌亚硝胺,目前已成为极具发展潜力的秋兰姆类硫化促进剂新品种。 一硫化四异丁基秋兰姆(T iBTM)是一种兼具橡胶硫化促进和防焦剂性能的多功能环保新型促进剂,是TMTM(一硫化四甲基秋兰姆)的最佳替代品。在丁苯橡胶/天然橡胶并用体系中,当T iBTM和CT P分别与T BBS和CBS并用时,两种防焦剂对焦烧延迟程度一样,T iBTM同时还可以使硫化速度明显加快,而CT P 有时还能引起硫化速度下降。在天然橡胶中,CT P的防焦效果要好于T iBTM,但是T iBTM能增加胶料的抗硫化返原性,T iBTM主要作为助促进剂使用。对于丁苯橡胶或是天然橡胶而言,无论是提高硫化温度、变化硫磺用量,还是加入白炭黑,都不会影响T iBTM既能增加焦烧安全又可提高硫化速率的性能,使用
促进剂并用原理
促进剂并用原理 促进剂是一种能够提高硫黄及其它硫化剂的硫化速度、交联程度的配合剂。它的主要作用是加快硫化速度,缩短硫化时间、改善胶料物理机械性能、 减少硫黄用量,避免硫黄喷霜。 促进剂的种类繁多有二硫代氨基甲酸盐类、秋姆类、噻唑类、次磺酰胺类、胍类、硫脲类、黄原酸盐类、醛胺类。 最常用的促进剂一般也就是秋兰姆类的TMTD TMTM TETD 这类促进剂;焦烧倾向大,定伸应力及拉伸强度大。一般作副促进剂用。噻唑类的DM M它是一种应用广泛,价格低廉的促剂它具有硫化平坦性好、耐老化、不易龟裂,耐磨性好等优点。加入少量的呱类促进剂可以迅速地提高硫化速度。DM有着良好的防焦烧性能。M易早期硫化操作安全性比DM差,这两种促进剂在配方中一般都用作第一促进剂及第二促进剂用。 https://www.360docs.net/doc/ad2832874.html, 次磺酰类的CZ NOBS TBBS 这类促进剂具有良好的焦烧性能,硫化胶强度高,硫化曲线十分平坦,与碳黑加工时不会发生焦烧。一般都用作第一促进剂用。胍类促进剂的D,DOTG一般作副促进剂用,其特点是硫化胶硬度高、定伸大、硫 化平坦性差。 促进剂一般很少单用只是在一些厚制品及测试用的标准胶中单用。为了提高生产效率、抑制喷霜等原因在日常生产中大量采用了促进剂并用。 促进剂并用的方法种类繁多。在这些常用促进组合中最典型并用形式有,DM/D(H) DM/TT、 DM/M/TMTD、 DM/D/TMTD、 DM/TMTD 、CZ/NS、 CZ/TMTM 、 CZ/D 、M/H。 一.DM与D DM与D并用它的焦烧性能中等,有着良好的硫化速度,优异扯断强度、及定伸力。它是一种酸性促进剂与减性促进剂并用。它的配比一般在 1.3—1.5/0.5-0.8但实际上一般都是1.4/0.5-0.8促进D的变量用于撑控硫化 速度。 二.DM/TMTD DM/TMTD并用,它的焦烧性能中等,良好的硫化速度、扯断强度。是一种酸性与酸性性促进并用,一般配比是1.3-1.5/0.2-0.4这种配比有着它的酸酸互抑功效,有效合理的配比可以延长焦烧时间。当DM用量较多时显示DM的硫变曲线走向,为了调控硫速加入少量TMTD反而焦烧延长,T90向后推迟。继
抗氧化作用的机制
一:碳氢化合物氧化和抗氧化作用的机制1.1润滑油的自身氧化 总所周知,碳氢化合物通过自动氧化过程氧化,这个过程形成酸和油的稠化。更严重的情况下,油泥和油漆类可能形成。润滑效果下降,降低燃油经济性,和增加摩擦,抗氧剂是很重要的添加剂来最小化氧化的影响,机理分析如下: 1.1.1 油的自身氧化 自由基机理[179-181],包括链引发,增长,分支,终止。 1)链引发 链引发的特征是通过烃类化合的C-H、C-C的断裂产生烷基自由基,这个过程一般是在烃类暴漏在氧气氛围、则加热状态下、紫外光、机械剪应力等条件下【182】,这种均裂的难易程度有以下规律:C-H的键能和自由基的稳定性,183.苯基﹤伯﹤仲﹤叔﹤烯丙基﹤苄基。这样的话烃类化合物如果含有叔氢和氢在碳碳双键的α位时特别容易受到氧的影响。这个过程在室温下一般比较慢,但是通过加热或则金属催化下会大大加快(铜、铁、镍、钒、锰、钴等)。 2)链增长: 增长过程包括一个不可逆的烷基自由基与氧气反应生成烷基过氧自由基。这个反应很快,速率与自由基上的取代基有密切的关系【179】。一旦形成,过氧自由基可以随机与其他烃反应生成氢过氧化物(ROOH)和新的烷基自由基,基于以上机理,一个烷基自由基的形成,大量的烃类化合物会被氧化为氢过氧化物。 3)链分支: A:自由基的形成 B:醛酮的形成: 链分支过程开始于氢过氧化物断裂为烷氧基自己基和羟基自由基。这个反应需要很高的活化能一般是温度大于150℃.金属则催化这个过程。结果就是自由基可能经历以下过程a:烷氧基自由基从烃吸收氢变为醇,而烃生成新的烷基自由基b:羟基自由基通过吸收烃上的氢变成水和新的烷基自由基。c:仲烷氧基自由基可以通过分解变为醛和和新的烷基自由基。d:叔烷氧基自由基则降解为酮和新的烷基自由基。 以上过程对于加快润滑油的氧化过程是非常重要的,不但生成大量的烷基自由基来加速氧化过程,而且生成很多小分子的醛和酮,这个物质无疑会降低润滑油的粘度、增加润滑油的挥发性和极性。在高温条件下醛和酮则会被继续氧化为酸和其他大分子化合物使油变得粘稠,从而形成油泥和varnish deposits。 4)链终止: 在氧化过程中,大分子碳氢化合物的形成会增加油的粘度。当润滑油的粘度增加到影响氧气在有油中的传递的时候,链终止过程就开始了,比如:两个烷基自由基可以反应生成新的烃类化合物。烷基自由基可以与烷基过氧化物自由基反应生成新的过氧化物。当然这种过氧化物不稳定,容易形成更多的烷氧基自由基。在这个过程中生成的羰基化合物和醇类化合物也可能是含有α氢的过氧自由基反应所得: 金属催化主要是通过氧化还原过程作用在链分支阶段催化氢过氧化物降解,【184】。可以显着减低氧化反应的活化能,使氧化反应能够在低温下进行。 初始阶段: 增长阶段:
第三章抗氧化剂
第三章食品抗氧化剂 Antioxidants 第一节概述 一、食品抗氧化剂 1、食品抗氧化剂 (1)定义:防止或延缓食品氧化,提高食品的稳定性和延长贮存期的物质。 (2)作用:阻止或延迟空气中氧气对食品中油脂和脂溶性成分(如维生素、类胡萝卜素等)的氧化作用,从而提高食品的稳定性和延长食品的保质期。 ⑶使用意义: 终止贮藏、加工过程中因自由基的导致的链锁反应,延缓食品被氧化的过程。 自由基(free radical):由氧化反应或活性氧产生的带电粒子。 二、油脂的氧化机理 (一)油脂的氧化过程 RH R? ROO? ROOH+R? (二)激发油脂氧化的因素 1、可变价金属离子(尤其是铜和铁) (1)金属离子直接与油脂作用,生成脂肪自由基 Mn+ + RH M(n-1)+ + R?+ H+ (2)金属离子使氧分子活化成单线态氧或过氧化自由基 Mn+ +O2 M(n+1)+ + O2- O2- –e 1O2 或O2- + H+ HOO?(3)加速氢过氧化物的分解,并成为自由基的主要来源 ROOH + Mn+ RO?+ OH- + M(n+1)+ ROOH + M(n+1)+ ROO?+ H+ + Mn+ 2、温度 3、紫外线 4、碱性条件和碱土金属离子 5、油脂的不饱和度 6、体系中氧含量 周期系ⅡA族元素,包括铍(Be)、镁(Mg)、钙(Ca)、锶(Sr)、钡(Ba)、镭(Ra)六种金属元素。(三)油脂氧化的终结和分解 氢过氧化物作为脂类自动氧化的主要初期产物,经过许多复杂的分裂和相互作用,最终形成有油脂酸败特征的醛、酮、醇、碳氢化合物、环氧化物及酸等低分子物质;也可经聚合作用生成深色的、有毒副作用的聚合物,同时也会使色素、香味物质等被氧化。 二、抗氧化剂的种类及其作用机理 (一)抗氧化剂的种类 按照抗氧化剂的溶解性分为水溶性抗氧化剂和脂溶性抗氧化剂两大类; 按照抗氧化剂的来源分为天然抗氧化剂(生物抗氧化剂)和人工合成抗氧化剂; 按照抗氧化剂的作用方式可以分为自由基吸收剂、金属离子螯合剂、氧消除剂、酶类抗氧化剂、紫外线吸收剂或单线态氧淬灭剂等。 (二)抗氧化剂的作用机理 1、自由基吸收剂
硫化促进剂的作用机理
硫化促进剂的作用机理 橡胶硫化促进剂是能加快硫化速度、降低硫化温度、减少硫化剂用量、并能改善硫化胶的物理机械性能的一类物质的总称,是当今橡胶工业必不可少的基本材料之一,促进剂本身不与橡胶发生直接作用,下面讲述促进剂作为“勤快的有一定献身精神的硫磺搬运工”的发展历史和作用机理: 1839年,固特异发现了橡胶硫磺硫化; 1843年,橡胶硫磺硫化技术正式问世; 20世纪初,硫磺硫化橡胶才被大规模应用于汽车轮胎的生产; 1906年,在实验中偶然发现苯胺具有硫化促进作用; 1908年,申请苯胺作为硫化促进剂的专利; 1910年,为改善苯胺的挥发性和毒性,开发了二苯基硫脲DPTU; 1915年,开始使用烷基黄原酸锌作为促进剂; 1918年,二硫代氨基甲酸盐作为硫化促进剂首次应用于橡胶工业; 1920-1925年,苯并噻唑作为促进剂的专利由意大利人和美国人申请; 1931年,德国拜尔发明了综合性能最好、使用最广泛的促进剂:次磺酰胺; 尽管硫化促进剂的种类繁多,但主要分为无机促进剂和有机促进剂,无机助促进剂主要包括氧化锌、氧化镁等,有机助促进剂主要包括硬脂酸、硬脂酸锌、胺类等;
例如,天然橡胶单独用3质量份硫磺硫化时,硫化时间为5h,并用5质量份ZnO后缩短为4h,在并用1质量份促进剂MBT和1质量份硬脂酸,则只需20-30min即可完成硫化,并且所制得的硫化剂性能大为改善。 各类促进剂都是由不同官能基团组成的,不同基团在橡胶的硫化过程中又发挥不同影响。促进剂分子结构中含促进基团、活性基团、硫化基团,因为每种促进剂含有不同官能基,其促进活化或硫化特性也产生差异。 促进基团:结构为:R1-S-。在硫化过程中,促进剂分解出基团起促进作用,噻唑类、秋兰姆类、二硫代氨基甲酸盐类、次磺酰胺类都有这种促进基团; 活性基团:结构为:R2-N-。促进剂在硫化过程中放出胺基具有活化作用,大部分有机碱(或胺类促进剂)都有硫化促进活性作用,而且许多生物碱具有显著生理活性,如尼古丁(烟碱/1—甲基—2—(3—吡啶基)吡咯烷)、吗啡(吗啡碱)、可待因、海洛因、奎宁(金鸡纳碱)、冰毒(甲基苯丙胺)、摇头丸(亚甲基二氧苯丙胺)、K 粉(氯胺酮)等。 硫化基团:结构为:-S-S-、-S-S n-S-。在硫化时,硫载体被分解而放出活性原子硫,参与交联反应,硫载体中的含硫基团称为硫化基团。 促进剂的作用机理非常复杂,但是常规认识为:1.促进剂先均裂,生成促进剂自由基,此促进剂自由基可引发硫磺S8开环,并可与之
抗氧化作用的机制
抗氧化作用的机制文件排版存档编号:[UYTR-OUPT28-KBNTL98-UYNN208]
一:碳氢化合物氧化和抗氧化作用的机制润滑油的自身氧化 总所周知,碳氢化合物通过自动氧化过程氧化,这个过程形成酸和油的稠化。更严重的情况下,油泥和油漆类可能形成。润滑效果下降,降低燃油经济性,和增加摩擦,抗氧剂是很重要的添加剂来最小化氧化的影响,机理分析如下: 油的自身氧化 自由基机理[179-181],包括链引发,增长,分支,终止。 1)链引发 链引发的特征是通过烃类化合的C-H、C-C的断裂产生烷基自由基,这个过程一般是在烃类暴漏在氧气氛围、则加热状态下、紫外光、机械剪应力等条件下【182】,这种均裂的难易程度有以下规律:C-H的键能和自由基的稳定性,183.苯基﹤伯﹤仲﹤叔﹤烯丙基﹤苄基。这样的话烃类化合物如果含有叔氢和氢在碳碳双键的α位时特别容易受到氧的影响。这个过程在室温下一般比较慢,但是通过加热或则金属催化下会大大加快(铜、铁、镍、钒、锰、钴等)。 2)链增长: 增长过程包括一个不可逆的烷基自由基与氧气反应生成烷基过氧自由基。这个反应很快,速率与自由基上的取代基有密切的关系【179】。一旦形成,过氧自由基可以随机与其他烃反应生成氢过氧化物(ROOH)和新的烷基自由基,基于以上机理,一个烷基自由基的形成,大量的烃类化合物会被氧化为氢过氧化物。 3)链分支: A:自由基的形成 B:醛酮的形成:
链分支过程开始于氢过氧化物断裂为烷氧基自己基和羟基自由基。这个反应需要很高的活化能一般是温度大于150℃.金属则催化这个过程。结果就是自由基可能经历以下过程a:烷氧基自由基从烃吸收氢变为醇,而烃生成新的烷基自由基b:羟基自由基通过吸收烃上的氢变成水和新的烷基自由基。c:仲烷氧基自由基可以通过分解变为醛和和新的烷基自由基。d:叔烷氧基自由基则降解为酮和新的烷基自由基。 以上过程对于加快润滑油的氧化过程是非常重要的,不但生成大量的烷基自由基来加速氧化过程,而且生成很多小分子的醛和酮,这个物质无疑会降低润滑油的粘度、增加润滑油的挥发性和极性。在高温条件下醛和酮则会被继续氧化为酸和其他大分子化合物使油变得粘稠,从而形成油泥和varnish deposits。4)链终止: 在氧化过程中,大分子碳氢化合物的形成会增加油的粘度。当润滑油的粘度增加到影响氧气在有油中的传递的时候,链终止过程就开始了,比如:两个烷基自由基可以反应生成新的烃类化合物。烷基自由基可以与烷基过氧化物自由基反应生成新的过氧化物。当然这种过氧化物不稳定,容易形成更多的烷氧基自由基。在这个过程中生成的羰基化合物和醇类化合物也可能是含有α氢的过氧自由基反应所得: 金属催化主要是通过氧化还原过程作用在链分支阶段催化氢过氧化物降解,【184】。可以显着减低氧化反应的活化能,使氧化反应能够在低温下进行。 初始阶段: 增长阶段: :
催化剂硫化
催化剂硫化 1.催化剂硫化的目的和原理 1.1硫化目的: 在一定的温度和硫化氢分压下,把催化剂的活性组分(氧化镍、氧化钼等)由活性低的氧化态变成活性稳定的硫化态,提高催化剂活性和稳定性,延长催化剂寿命。 虽然加氢催化剂在使用氧化态形式开工后,也会因较弱的加氢活性促使一部分原料中的硫化物发生加氢脱硫反应,生成硫化氢,继而使催化剂金属组分从氧化态转化为硫化态,但这种转化是在催化剂长时间与高温氢气接触、并且有大量结焦的情况下进行,催化剂的活性金属组分在转化为硫化态之前,有一部分可能被氢还原,这种氢还原或已经沉积有炭的金属组分很难再被硫化,从而使催化剂处于低的加氢活性,并带来短的寿命。 因此,加氢催化剂在接触原料油之前,必须先将催化剂活性金属组分的氧化态用硫化剂将其转化为硫化态,即进行催化剂预硫化。本装置催化剂硫化方式采用湿法硫化。 1.2 预硫化原理: 预硫化时,硫化反应极其复杂。在反应器内会发生两个主要反应: (1)硫化剂(DMDS)和氢气反应,产生硫化氢和甲烷,反应会放出热量。预硫化时该反应一般在反应器入口发生,反应速度较快。 反应方程式: CS2+4H2→CH4+2H2S (2)氧化态的催化剂活性组分(氧化镍、氧化钼等)和硫化氢反应变成硫化态的催化剂活性组分,反应会放出热量。预硫化时该反应发生在各个床层。 反应方程式: M O O3+2H2S+H2→M O S2+3H2O 3N i O3+2H2S+H2→NiS2+3H2O (3)副反应: 在有氢气存在、无硫化氢的条件下,氧化态的催化剂活性组分(氧化镍、氧化钼等)被氢气还原,生成金属镍、钼和水,导致催化剂活性损失。温度越高(大于230℃),反应越严重;在循环气中的硫化氢含量过高时,会生成金属的多硫化物,降低了催化剂活性,易造成产品腐蚀不合格。 2. 催化剂硫化应具备的条件 (1)反应系统催化剂干燥、高压气密结束,紧急泄压和急冷氢试验问题整改完。 (2)分馏系统热油运运转正常,具备接收生成油条件。 (3)高压注水等其他系统试运正常。 (4)新氢系统具备正常供氢条件。 (5)注硫系统试运正常,DMDS装罐。 (6)通知化验及其他相关单位,做好催化剂预硫化的配合工作。 (7)仪表、DCS及SIS联锁系统调试合格,工艺联锁已全部投用。 (8)预硫化所需化工原材料和有关物品准备齐全,其中硫化剂:DMDS77t,硫化油:直馏柴油(氮含量<100 g/g、干点<350℃、含水量<0.01%)2000t