自动调整臂原理图及安装调整方法

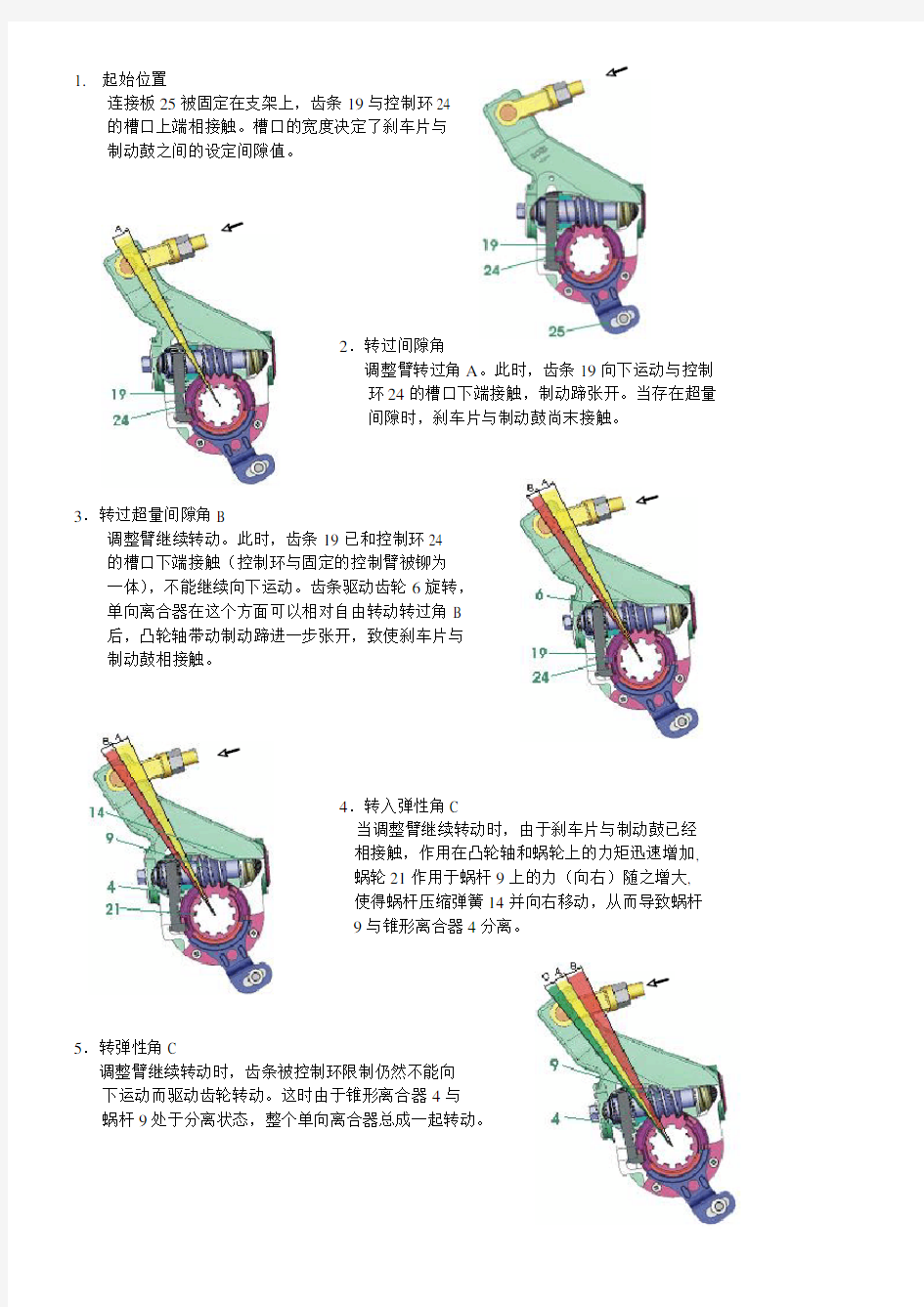
零件清单:
1.起始位置
连接板25被固定在支架上,齿条19与控制环24
的槽口上端相接触。槽口的宽度决定了刹车片与
制动鼓之间的设定间隙值。
2.转过间隙角
调整臂转过角A。此时,齿条19向下运动与控制
环24的槽口下端接触,制动蹄张开。当存在超量
间隙时,刹车片与制动鼓尚末接触。
3.转过超量间隙角B
调整臂继续转动。此时,齿条19已和控制环24
的槽口下端接触(控制环与固定的控制臂被铆为
一体),不能继续向下运动。齿条驱动齿轮6旋转,
单向离合器在这个方面可以相对自由转动转过角B
后,凸轮轴带动制动蹄进一步张开,致使刹车片与
制动鼓相接触。
4.转入弹性角C
当调整臂继续转动时,由于刹车片与制动鼓已经
相接触,作用在凸轮轴和蜗轮上的力矩迅速增加,
蜗轮21作用于蜗杆9上的力(向右)随之增大,
使得蜗杆压缩弹簧14并向右移动,从而导致蜗杆
9与锥形离合器4分离。
5.转弹性角C
调整臂继续转动时,齿条被控制环限制仍然不能向
下运动而驱动齿轮转动。这时由于锥形离合器4与
蜗杆9处于分离状态,整个单向离合器总成一起转动。
6.向回转过弹性角C
制动开始释放,调整臂向回转过角C。在回位弹簧17
和18的作用下,使得齿条向下紧帖控制环24的槽口
下端。此时,锥形离合器4与蜗杆9仍处于分离状态,
齿条可以驱使单向离合器总成自由转动。
7.向回转入间隙角A
随着刹车片作用于制动鼓上压力的释放,作用于
凸轮轴和蜗轮的力矩消失,蜗轮21向右施加给蜗
杆9的力也消失,弹簧14复原,推动蜗杆向左移
动,使得蜗杆与锥形离合器4从新啮合。
8.向回转过间隙角A
调整臂向回转过A。齿条19向上运动,与控制环24
的槽口的接触从下端变为上端。
9.向回转过超量间隙角B
调整臂继续转动回到起始位置。此时,齿条19
已与固定的控制环24的槽口上端相接触,受
其限制不能继续向上移动。当调整臂回转时,
齿条驱动齿轮6转动,这时单向离合器和锥齿
离合器均处于啮合状态,使得蜗杆9随齿轮一
起转动,蜗杆驱动蜗轮21,蜗轮驱动凸轮轴,
面对面凸轮辆的转动使得超量间隙减小。
自动调整臂安装说明书
在安装调整臂之前请务必阅读此说明书,以免不正确的安装带来严重的后果!
第一步:解除制动(制动室推杆回位到底),卸下失效的调整臂。清除凸轮轴花键上的杂物,装上自动调整臂(注意臂体上的剪头方向要向前!)。
第一步第二步
第二步:调整臂上的孔和推杆叉上的孔对不上,要用扳手调整六角头使其对齐。
第三步:用垫片或其它尽量使调整臂处于图示位置。
第三步第四步
第四步:按臂体上箭头的方向用手推控制板,直到手推不动为止,固定好控制板。第五步:用扳手调整六角头使摩擦片压紧制动鼓为止,在这个调整过程中手感是:先很轻松转动,到最后不管用多少力都调不动。如果用力调听到咔咔响,说明方向调反了。
第五步第六步
第六步:在第五步基础上反向调节1/2~3/4圈,安装完毕。
使用过程中的注意事项!
1.如果在使用过程中控制板断了,必须尽快换控制板或总成。
2.用手用力推控制板,铆合处不能转动。
3.把扭力扳手放入六角头测蜗杆的力矩(第六步中用扭力扳手),如果力矩小于18N.m,调整臂已失效,应更换。如果不能及时更换,必须手动调到合理制动间隙。
刹车自动调整臂
刹车自动调整臂 制动鼓与蹄自动调整臂及其失效 制动间隙自动调整臂在国外是一个比较成熟的重型车制动配件,在欧美一些汽车工业发达国家,早己将间隙自动调整臂作为一种标准件使用。在国内,中型货车、挂车及重型车基本采用的是S型凸轮鼓式制动器,且基本采用手动间隙调整臂。近几年,随着我国汽车工业的发展、公路状况的改善,汽车的载重量及车速都有了较大的提高,用户对汽车的制动性能越来越重视,要求也越来越高,自动间隙调整臂正逐步得到推广和应 用。 图1描述的是手动调整臂和自动调整臂的区别。折线表示采用手动调整臂时刹车间隙的变化,该线向上倾斜段表示刹车间隙随着摩擦衬片磨损而不断增加直至该间隙达到需要手动调整时的危险间隙;垂线段表示刹车间隙经手动调整从危险间隙恢复到正常间隙;水平带表示采用刹车间隙自动调整臂时,刹车间隙始终 保证在正常的间隙范围内。 图1 手动调整臂和自动调整臂的区别 1. 1制动时调整臂的角行程制动时调整臂的角行程可划分为3部分(如图2所示) 。 ①正常间隙角度(C)对应于设定的制动鼓和摩擦衬片间的正常间隙; ②超量间隙角度(Ce)对应于因摩擦衬片磨损而增加的间隙; ③弹性角度( E)对应于制动鼓、摩擦衬片以及传动元件弹性变形引起的角度变化。 1. 2自动调整臂工作过程 制动间隙自动调整臂结构简图如图3所示。安装时,将主臂孔连接到制动分泵连接叉,内花键与制动器凸轮轴外花键配合连接,控制臂固定在车桥的安装支架上。其工作原理如下: ①制动间隙处于设计理想状态时。制动时,制动分泵连接叉推动主臂逆时针旋转,大弹簧承受制动力被压缩,蜗杆右端面7与壳体孔端面接触,蜗杆左端凸面斜齿和离合器内凹斜齿处于松动状态,此时蜗杆推动蜗轮,蜗轮通过内花键带动凸轮轴转动实现制动;若制动间隙处于理想状态,此时只有正常间隙(C) ,齿条右侧凸块将在控制臂组件下端缺口中运动,齿条与臂体无相对运动。解除制动时,制动分泵连接叉推动主臂顺时针旋转,大弹簧被释放,蜗杆左端凸面斜齿和离合器内凹斜齿处于啮合状态,此时蜗杆推动蜗轮,蜗轮通过内花键带动 凸轮轴转动解除制动,对制动间隙没有调整作用。
东风商用车制动间隙自动调整臂结构原理
制动间隙自动调整臂结构、工作原理: 制动间隙自动调整臂(以下简称自调臂)适用于鼓式制动器。 因为频繁的刹车,制动蹄片与制动鼓的间隙由于摩擦片的磨损而增大,使整车的制动性能大大降低。手动调整臂通过人工调整制动器的间隙来保证行车的安全;在正常工作情况下的自调臂,则不再需要人工调节间隙,它利用制动和回位过程的推力和拉力使摩擦片与制动鼓之间的间隙保持到预留值,进一步提高车辆安全性。同时,节约大量维护和保养时间,提高运营经济效益。1、自调臂的工作原理: 自动调整臂比手动调整臂增加了制动间隙的测量和制动间隙的补偿功能。自调臂利用刹车制动和回位过程的推力与拉力,使螺纹叉c带动齿条a在自调臂转动过程中上下运动,以驱动控制元件使蜗杆b、蜗轮e相对于自调臂转动,来带动制动器凸轮轴转动,使制动间隙变小。 自调臂是通过转角来测量制动间隙,并根据其大小来实现间隙的自动调整,最终稳定在制动间隙的设定值(设定值为0.6~1.0mm)。 行车制动时,自调臂的工作可分解为三部分(见图21):正常间隙角度C (clearance), 。Ce(excessive clearance)和弹性变形角度E(elasticity)过度间隙角度 图21 :对应于设定的正常蹄、鼓之间的制动间隙,自调臂在该角度范围内C正常间隙角度不调整制动器的间隙。:对应于因摩擦片的磨损和其它原因产生的大于正常设定值的间隙,Ce过度间隙角度直到制动间隙为正常设定自调臂根据该角度的大小在制动过程中进行制动间隙的自动调整,值、无超量间隙为止。 弹性变形角度E:对应于因摩擦片与制动鼓及传动元件弹性变形引起的角度变化,自调臂在该角度范围内不进行制动间隙的调整。 所以,在正常间隙角度C范围内,自调臂不参与间隙调整,只有当C+Ce>C时,自调臂才进行间隙调整,直至C+Ce=C。并且任何一次制动过程中的弹性变形E都不参与自动调整。 2、自调臂的结构型式: 目前,应用于东风公司中重型商用车的自动调整臂从结构上可以分为两种:一种为带控制臂结构(Bendix结构)的产品,另一种为不带控制臂结构(Haldex结构)的产品。前者的控制臂必须固定在特定的位置,需在外部加装连接件,后者的整套调整机构都在自调臂总成上,安装相对简单,可以与手调臂直接互换。两种类型的结构见图1和图2,在桥上的位置见图3和图4。
自动调整臂原理图及安装调整方法
零件清单:
1.起始位置 连接板25被固定在支架上,齿条19与控制环24 的槽口上端相接触。槽口的宽度决定了刹车片与 制动鼓之间的设定间隙值。 2.转过间隙角 调整臂转过角A。此时,齿条19向下运动与控制 环24的槽口下端接触,制动蹄张开。当存在超量 间隙时,刹车片与制动鼓尚末接触。 3.转过超量间隙角B 调整臂继续转动。此时,齿条19已和控制环24 的槽口下端接触(控制环与固定的控制臂被铆为 一体),不能继续向下运动。齿条驱动齿轮6旋转, 单向离合器在这个方面可以相对自由转动转过角B 后,凸轮轴带动制动蹄进一步张开,致使刹车片与 制动鼓相接触。 4.转入弹性角C 当调整臂继续转动时,由于刹车片与制动鼓已经 相接触,作用在凸轮轴和蜗轮上的力矩迅速增加, 蜗轮21作用于蜗杆9上的力(向右)随之增大, 使得蜗杆压缩弹簧14并向右移动,从而导致蜗杆 9与锥形离合器4分离。 5.转弹性角C 调整臂继续转动时,齿条被控制环限制仍然不能向 下运动而驱动齿轮转动。这时由于锥形离合器4与 蜗杆9处于分离状态,整个单向离合器总成一起转动。
6.向回转过弹性角C 制动开始释放,调整臂向回转过角C。在回位弹簧17 和18的作用下,使得齿条向下紧帖控制环24的槽口 下端。此时,锥形离合器4与蜗杆9仍处于分离状态, 齿条可以驱使单向离合器总成自由转动。 7.向回转入间隙角A 随着刹车片作用于制动鼓上压力的释放,作用于 凸轮轴和蜗轮的力矩消失,蜗轮21向右施加给蜗 杆9的力也消失,弹簧14复原,推动蜗杆向左移 动,使得蜗杆与锥形离合器4从新啮合。 8.向回转过间隙角A 调整臂向回转过A。齿条19向上运动,与控制环24 的槽口的接触从下端变为上端。 9.向回转过超量间隙角B 调整臂继续转动回到起始位置。此时,齿条19 已与固定的控制环24的槽口上端相接触,受 其限制不能继续向上移动。当调整臂回转时, 齿条驱动齿轮6转动,这时单向离合器和锥齿 离合器均处于啮合状态,使得蜗杆9随齿轮一 起转动,蜗杆驱动蜗轮21,蜗轮驱动凸轮轴, 面对面凸轮辆的转动使得超量间隙减小。
刹车间隙自动调整臂的技术现状及其发展趋势
制动间隙自动调整臂 的技术现状及其发展趋势 [摘要]作为汽车制动系统可靠性的一个关键零部件-制动间隙调整臂,自动调整臂正在取代手动调整臂,罗克威尔式自动调整臂将取代瀚德式自动调整臂。 [关键词]制动间隙;自动调整臂;罗克威尔式;翰德式 Present Technical Status and Developmental Trends of the Automatic Adjusting Arm of the Braking Clearance Yin xian-jun (Hunan sany Ltd., Changsha 410100,Hunan, China) Abstract: The adjusting arm of braking clearance, it is the key device to ensure the reliability of the vehicle braking system. The automatic adjusting arm is increasingly replacing the manual arm. The automatic adjusting arm of Rockwell will take the place of the Haldex. Key words: the braking clearance; the automatic adjusting arm; the automatic adjusting arm of Rockwell; the automatic adjusting arm of Haldex 汽车制动系统的可靠性是汽车安全行驶的关键要素,保证合理的制动间隙是制动系统正常工作的必要条件。我国目前的商用车,尤其是货车,利用凸轮块制动的鼓式制动器,大多数使用制动间隙手动调整臂。在欧美发达国家,对于这类制动器,不论客车还是货车,都已采用制动间隙自动调整臂。因此,制动间隙自动调整臂取代制动间隙手动调整臂是必然趋势。而安装简便、性能可靠的罗克威尔式制动间隙自动调整臂,不但满足了这种发展趋势,还将逐渐取代安装不便的瀚德式制动间隙自动调整臂。 一.制动间隙自动调整臂的优点及在我国的应用现状 制动间隙自动调整臂因为有如下优点,在汽车行业的应用将日益普及: ①自动保持摩擦片和制动鼓之间间隙恒定,所有车轮的制动效果一致、稳定,因而制动迅速、安全可靠。 ②压缩空气损耗小,延长了空气压缩机、制动气室和相应部件的使用寿命。 ③安装过程结束后,不再需要人工调节制动间隙,减少了维修次数,提高了经济效益。 2004年度,我国商用车年产量达到275万4千2百辆,其中重型、中型载货车54万1千8
自动调整臂用户手册
东风自动调整臂用户手册 东风车桥有限公司 DongFeng Axle Co.,Ltd
东风自动调整臂简介 东风自动调整臂是东风车桥有限公司吸收、引进国际先进技术,自主研制、开发的具有国际先进水平、科技含量高的重要车桥零部件。该产品采用整体式结构,调整机构密封在壳体内受到很好的保护,避免了受潮锈蚀、脏物及磕碰等对调整机构的损坏。 东风自动调整臂已通过了襄樊国家汽车质量检测中心按照美国SAE J1462、SAE J1513标准进行的台架试验和东风汽车有限公司商用车研发中心整车道路试验。经过严格的台架试验和道路试验考核表明,东风自动调整臂完全满足客户使用要求,产品性能稳定,可靠性高,质量水平领先于国内同行业制造厂家。 目前,东风车桥有限公司已开发了4大系列47个品种的自动调整臂总成,年产能80万只,可广泛应用于国内外各种类型、安装“S”型凸轮制动器的气制动车辆及挂车,满足不同客户的配置需求。 选用东风自动调整臂的车辆,在使用过程中具有以下优点: 1、确保车轮具有恒定的刹车间隙,刹车安全可靠; 2、制动分泵推杆行程短,制动迅速可靠; 3、制动前制动分泵推杆始终处于初始位置,确保了最佳的刹车力矩; 4、保证所有车轮的制动效果一致、稳定; 5、减少了压缩空气的消耗量,延长了空压机、制动分泵和压缩空气系 统中其它部件的寿命;
6、减少了材料消耗,延长了刹车部件的使用寿命; 7、安装使用方便,减少了人工维修次数,提高了经济效益,降低劳动 强度。 东风自动调整臂使用说明 本说明详细介绍了东风自动调整臂使用、调节方法,选用东风自动调整臂的客户请详细阅读本说明后,再使用本产品。 东风自动调整臂的安装: 1、安装前,确保制动气室推杆处于初始位置; 2、将隔离衬套装到凸轮轴上,贴近气室支架凸轮轴孔端面,以保证刹车间隙自动调整臂(以下简称调整臂)与支架之间合适的间隙。 3、将调整臂安装到凸轮轴花键部分上,应确保调整臂壳体上箭头所指方向与气室推杆推出方向一致,尽可能使调整臂接近气室推杆联接叉。顺时针旋转调整臂蜗杆的六方头,使调整臂逐渐转入联接叉内,直至联接叉销孔与调整臂上的销孔自然对正,然后将圆柱销轻松插入并通过联接叉和调整臂销孔,装上开口销(注意:安装过程中不能改变气室推杆初始位置;联接叉销孔与调整臂上的销孔一定要自然对正)。 4、将调整臂的控制臂沿其上箭头所示方向推动,直至推不动为止,目的是为了确保刹车衬片与制动鼓之间的设定间隙。 5、将限位支架预安装在指定位置,再将控制臂与限位支架角向可靠联
调整制动间隙
调整制动间隙 车轮制动器制动间隙的调整分局部调整和全面调整两种。局部调整只需调整制动蹄的张开端,通常用于车辆在运行过程中因蹄鼓的间隙变大而进行的调整。全调整需同时调整制动蹄片两端的位置,通常用于更换制动蹄衬片或镗削制动鼓后为保证制动蹄与制动鼓的正确接触而进行的调整。对于不设置固定端的自动增力式车轮制动器而言,没有全面调整和局部调整之分。 (1)液压制动系鼓式车轮制动器 其局部调整的步骤如下: 1)顶起车轮,一边转动车轮,一边向外转动调整凸轮螺栓,直至制动蹄压紧制动鼓为止。转动车轮时,应有一定的方向,即调整前轮两蹄和后轮的前制动蹄时向前转动车轮;调整后轮后制动蹄时向后转动车轮。 2)向内转动调整凸轮螺栓,直至车轮能自由转动而制动蹄与制动鼓不碰擦。 3)用同样的方法调整其他调整凸轮螺栓。 4)用塞尺检查蹄鼓间隙应符合规定。 全面调整的方法如下: 1)按局部调整的方法转动调整凸轮螺栓至制动鼓不能转动为止 2)向能够转动支承销的方向转动支承销。 3)重复上述的1)、2)两步,直至调整凸轮螺栓与支承销均不能转动为止。 4)锁紧支销后,向内转动偏心轮螺栓,直至车轮能自由转动且制动筛与制动鼓不碰擦。 5)在检视孔用塞尺测量蹄鼓间隙。支承轴端为0.15m.张开端为0.3mm。 (2)气压制动系鼓式车轮制动器 局部调整的步骤如下: 1)支起车桥,使车轮能够自由转动。 2)推进调整臂的锁止套. 用扳手转动蜗杆轴使制动路压紧制动鼓(搬动蜗杆轴时应注意观察凸轮轴的转动方向应为其工作方向),至蜗杆轴不能再转动为止。 3)以反方向退回蜗杆轴至车轮自由转动且石碰擦制动鼓。 4)用塞尺检查制动器蹄鼓间隙,靠近凸轮端为0.4~0.7mm,靠近支承销端为0.22~0.5mm。5)用锁止套锁紧蜗杆轴。局部调整时应注意不允许用改变制动气室推杆总长度的方法来 调整制动间隙,因为这样会减小使蹄片张开的推动力。 全面调整的步骤如下: 1)松开凸轮轴支架的固定螺栓,使凸轮获得一定的自由度,以便其自动找正中心。 2)转动调整臂的蜗杆轴使制动蹄压向制动鼓,至蜗杆轴不能再转动为止。晃动凸轮轴支架,使凸轮位置居中。 3)向可以转动的方向转动两支承销,直至制动蹄片固定端抵住制动鼓,支承销不能再转动力止: 4)重复②、③两步,直至制动蹄片的两端均抵住制动鼓,蜗杆轴和支承销不能再转动为止。在此位置上,先将凸轮轴支架固定和支承销固定,然后转动调整臂的螺杆袖,使制动肺片退回,两端出现间隙。 5)用厚薄规检查制动蹄鼓的间隙应符合要求。
“铁哥们”制动间隙自动调整臂结构、工作原理、特点、安装及调整方法
“铁哥们”制动间隙自动调整臂 结构、工作原理、特点、安装及调整方法 1.结构组成: 制动间隙自动调整臂为阶跃式间隙自动调整装置。 该调整臂主要由壳体、蜗杆、蜗轮、棘轮、棘爪、压缩弹簧及与之相连的滑块、连杆等构件为调整补偿构件。 2.工作原理: 2.1无需自动补偿时 制动时,气室充气,气室推杆推动调整臂转动,并带动与调整臂中蜗轮相啮合的S-凸轮轴转动,从而打开制动蹄片压住制动鼓产生摩擦力矩,直至制动。在这期间调整臂转动后消除了制动蹄片与制动鼓间的间隙以及制动蹄片、S-凸轮轴、制动鼓所引起的弹性变形,刹车中由于连接套与气室的推杆相连接从而随着调整臂的转动,使与连接套相连的连杆带动滑块向上窜动,其窜动量设定值等于正常制动时调整臂转动所引起的最大窜动值。由于棘轮、棘爪的外表面带一定螺旋角的锯齿形斜齿,当棘轮向上运动时由于此时受力面为非工作面,棘爪在棘轮上滑动,当制动间隙没有超过设定值时棘轮上窜动的行程小于棘轮外表面相邻两齿的轴向齿距此时棘轮、棘爪不发生跳齿,制动器放松后,调整臂复位,棘轮和棘爪又返回原位,不进行间隙补偿。 2.2自动补偿时 当制动间隙由于摩损而引起增大、增大量超过设定值后棘轮的行程大于相邻两齿的轴向齿距时,在压缩弹簧的作用下棘爪跳过一齿重新啮合。当制动器放松后调整臂复位时,棘轮返回。此时棘轮、棘爪齿形工作面为直面,棘轮轴向返回,在棘爪的作用下棘轮会转动一定角度,棘轮和蜗杆是由花键相连接,因此棘轮会带动蜗杆旋转相同角度;蜗杆又带蜗轮转动,同样,蜗杆带动S-凸轮轴也转过同样的角度,既实现了间隙补偿。 3.产品特点: 3.1该装置具有检测机构和调整补偿机构,结构紧凑、动作灵活、性能安全可靠,它的安装方法基本与手动调整臂一样,安装十分方便。 3.2由于调整结构被封闭于壳体之内而受到很好的保护,从而避免了受潮、脏物及磕碰等。 3.3 不再需要人工调节制动间隙,使车辆制动鼓和蹄片之间的间隙始终保持在一个正常
调整臂的作用
调整臂的作用: 调整臂的作用是对制动器制动间隙进行调整,是指对制动器摩擦副元件——制动鼓和制动衬片之间的间隙进行的调整。汽车在使用过程中,频繁的制动会导致制动元件的不断磨损,致使制动鼓与蹄片之间的间隙不同程度的增大,导致踏板行程加长、制动气室推力下降、制动滞后和制动力降低等。为保证车辆行驶安全,维持踏板行程的相对稳定和各制动器之间工作均衡,需对制动间隙进行调整(此处所说的调整是只使用过程中的调整),起到调节和控制制动功能和灵敏度的功能。按调整的方式分为手动调整臂和自动调整臂。手动调整臂和自动调整臂的区别 手动调整臂,即当车辆行驶一定路程后,会有制动磨损和制动间隙的增大,需手动调整确保制动间隙。由于是手动调整,存在调整不及时和随机性,可能导致各制动器间间隙不一致、制动响应时间延长、车轮跑偏、车辆甩尾甚至制动失效。为解决以上问题,需要定期检查并对制动器制动间隙进行手动调节,并使之保持恒定一致。手动调整臂由于价格较低,在重卡市场上占的份额较大。但由于手动调整臂不能满足大吨位重型车所应有的持续、高效、始终一致的制动效果,易导致制动滞后、偏刹,甚至造成摩擦片松动、脱落,给运行车辆带来重大的安全隐患。所以自动调整臂将成为新的趋势。 间隙自动调整臂具有如下特点: ⑴保证各车轮制动器具有恒定一致的制动间隙,使整车的制动更灵敏、均衡、有效,缩短制动距离,即使各车轮制动器蹄片厚度不一致、磨损程度不同,亦能保证制动的最佳效能,这一点在车桥来自不同厂家、制动器和摩擦副材料不同时尤其重要,手动定期调节则会由于不同的制动器之间的不同磨损造成制动器间间隙的不同,致使制动力分布不均。 ⑵缩短制动反应时间,减少压缩空气的消耗量。由于消除了多余间隙,所以制动气室能在最短的行程、最佳的工作区域实施制动,从而获得最佳的制动效能、最短的制动反应时间和最少的耗气量。 (3)由于调整机构被封于壳体之内而受到很好的保护,从而避免了受潮、腐蚀及碰撞等。 (4)安装方便。 (5)不再需要人工调节刹车调整臂,减少了维修次数,使车辆保养的时间间隔得以延长,从而增加经济效益。 (6)刹车间隙自动调整带来的刹车均衡效果,随着车桥数增加而增加。 调整臂更换 调整臂更换原因是 1. 蜗轮齿轮磨损,致使不能很好带到凸轮转动以消除摩擦副间的多余间隙。 2. 涡轮与蜗杆卡死。 3. 壳体破裂。 调整臂的工作原理 在调整臂的内部有一蜗轮和蜗杆,通过调整蜗杆转动蜗轮从而带动带动凸轮转动,消除摩擦衬片与制动鼓的多余间隙。 自动调整臂使用和保养 (一)使用: 1、车辆在正常运行过程中,不要用扳手随意拧蜗杆六角头; 2、力矩检测时,1)拆卸后检测;2)转动幅度不要太大; 3、更换摩擦片或制动鼓后,重新安装制动自动调整臂; 4、同一根桥上摩擦片要求同时更换。 (二)保养: 1、每20000公里应对自动调整臂加注2号锂基润滑脂一次; 2、感觉制动疲软时,建议检测自动调整臂蜗杆六角头的逆时针力矩。旋转一周,若所测最小力矩小于18N/m,则表明自动调整臂已损坏,必须及时更换自动调整臂总成。 自动调整臂的组成
制动间隙自动调整臂
制动间隙自动调整臂 汽车制动间隙自动调整臂,最早出现在我国是在九十年代中期,当时只有几个专利技术,尚不成熟,后来瀚德技术公开,国内有少数几个厂家研制,但应用效果均不理想,从此,许多有识之士,开始对自动调整臂的研究,直到近期已有几十项专利,研究人员也由过去的廖廖数人发展到几十人。代表的臂型共有以下几种: (1)以瀚德一代为基础的瀚德臂型。 (2)以瀚德二代为基础的瀚德臂型。 (3)以美国臂型为基础的具有调整拐的臂型。 (4)以45°斜齿轮传动为特点的臂型。 以上各种臂型的产品均已投放市场,但投放量远远低于主机厂需求,究其原因有以下三个方面: (1)技术尚不成熟,可靠性差故障率高; (2)结构复杂,使用者不易掌握,体积大,安装不便适应性差; (3)出厂成本高,导致售价高,无法普及。 由于以上原因阻碍了自动调整臂的普及推广,早在两年前,国家建设部就颁文要求强制采用自动调整臂,但由于存在上述原因未得实施,去年国家再次颁文强制执行,情况仍未好转。 针对上述情况,本文作者及相关人等开发研制了外联直传型自动调整臂,本着结构简单体积小,使用方便维护少;制造容易造价低,适应广泛易普及;低故障率,高可靠性的设计原则进行了方案设计及施工图设计,按国家建设部
新颁布的标准进行实验室试验结果理想。主要技术指标已达到(1)调整负载为40Nm时,稳定运行达5000次以上。(2)正常调整负载时有效运行10万次以上。(3)粉尘试验,盐浴试验均完成标准要求。除此之外,一个普通装配工人,用一支螺丝刀,一把手锤,一把搬手,在两分钟内便可完成一只臂的装配,车辆每更换一次刹车衬片时,对调整臂进行一次拆洗和注润滑脂便是其维护的全部内容,与此前所有臂型相比,此调整臂的安装空间最小,安装时最方便,没有任何特殊要求。现以图示为例,说明各型调整臂结构特点,并做对比。 1、瀚德一代臂型 主要有1小压簧、2中压簧、3外部连接件、4控制板、5联结套、6齿条、7盖板、8主动盘、9轴承套、10壳体、11前堵盖、12止推轴承、13从动套、14扭簧、15齿轮、16整体蜗杆、17蜗轮、18挡片、19大压簧、20后堵盖等件,共由二十个主要件构成。其结构特征为:控制板与主动盘通过联结套铆合固联,主动盘上豁口与齿条凸台啮合,齿条与齿轮啮合,齿轮、从动套、扭簧均套在
拉杆式自动调整臂结构、工作原理
拉杆式制动间隙自动调整臂 结构、工作原理、特点 随着社会的发展,行车安全问题越来越受到主机厂及司机朋友的重视,而作为汽车制动系重要构成的调整臂的性能如何直接决定了行车的安全性,自调臂因其能及时的自动调整制动间隙,为制动间隙的有效性提供了有力保障,而且,由于国家政策的提倡,自调臂代替手调臂是未来行业发展的必然趋势,为抢先占领市场,尽早开发出我们自己的优质自调臂产品投放市场是我们近期的主要工作。而拉杆式自调臂以其结构结构紧凑、动作灵活、性能安全可靠,相对其他类型自调臂成本较低的有点,我们将其列为首选开发类型,1.结构组成: 制动间隙自动调整臂为阶跃式间隙自动调整装置。 该调整臂主要由壳体、蜗杆、蜗轮、棘轮、棘爪、压缩弹簧及与之相连的滑块、连杆等构件为调整补偿构件。 2.工作原理: 2.1无需自动补偿时 制动时,气室充气,气室推杆推动调整臂转动,并带动与调整臂中蜗轮相啮合的S-凸轮轴转动,从而打开制动蹄片压住制动鼓产生摩擦力矩,直至制动。在这期间调整臂转动后消除了制动蹄片与制动鼓间的间隙以及制动蹄片、S-凸轮轴、制动鼓所引起的弹性变形,刹车中由于连接套与气室的推杆相连接从而随着调整臂的转动,使与连接套相连的连杆带动滑块向上窜动,其窜动量设定值等于正常制动时调整臂转动所引起的最大窜动值。由于棘轮、棘爪的外表面带一定螺旋角的锯齿形斜齿,当棘轮向上运动时由于此时受力面为非工作面,棘爪在棘轮上滑动,当制动间隙没有超过设定值时棘轮上窜动的行程小于棘轮外表面相邻两齿的轴向齿距此时棘轮、棘爪不发生跳齿,制动器放松后,调整臂复位,棘轮和棘爪又返回原位,不进行间隙补偿。 2.2自动补偿时 当制动间隙由于摩损而引起增大、增大量超过设定值后棘轮的行程大于相邻两齿的轴向齿距时,在压缩弹簧的作用下棘爪跳过一齿重新啮合。当制动器放松后调整臂复位时,棘轮返回。此时棘轮、棘爪齿形工作面为直面,棘轮轴向返回,在棘爪的作用下棘轮会转动一定角度,棘轮和蜗杆是由花键相连接,因此棘轮会带动蜗杆旋转相同角度;蜗杆又带蜗轮转动,同样,蜗杆带动S-凸轮轴也转过同样的角度,既实现了间隙补偿。
刹车间隙自动调整臂使用维修说明书
刹车间隙自动调整臂使用维修说明书 欧曼营销公司服务管理部 2008年3月
目 录 第一章 刹车间隙自动调整臂安装步一 (1) 第二章 刹车间隙自动调整臂拆卸步骤 (4) 第三章 刹车间隙自动调整臂的保养 (4) 第四章 安装刹车间隙自动调整臂过程的注意事项 (4) 第五章 常见故障及处理指南 (5)
第一章 刹车间隙自动调整臂的安装 1.安装前,确保制动分泵推杆处于初始位置。备有弹簧制动分泵时,制动系统气压应保持在6b a r以上,以使分泵推杆处于初始位置(见图一)。把调整臂安装在凸轮轴上。注意壳体上的箭头方向应与制动方向一致,也就是制动分泵推杆向外推动调整臂方向(见图二)。 (图一) (图二) 2.用S W l2扳手顺时针旋转调整臂端部的蜗杆六方头(注意:不能使用电动扳手,风动钻),使调整臂的孔与分泵推U形叉的定位孔自然正对,然后,将园柱销上轻松插入U形叉孔,锁上开口销(见图三)。 (图三) 3用隔圈、螺栓或垫片、卡簧将调整臂固定在凸轮轴上,此时应确保调整臂轴向间隙A=0.50-2.00m m(见图四或图五),然后将控制臂向制动方向推动(图 六)(控制臂上有箭头示意推动方向)直到推不动为止。此时,控制臂上指针应 指向开口或控制臂上的刻线与控制臂盖上的对齐(见图七或图八)。其操作目的是保证摩擦片与制动鼓之间的设定间隙。
(图四)(图五) (图六) (图七)
(图八) 4.安装调整臂支架,随后将控制臂紧固在定位支架上(见图九)。 (图九) 5.用扳手顺时针转动调整臂蜗杆六角头直至摩擦片与制动鼓接触,然后再逆时针方向转动蜗杆六角头3/4圈(反向转动时会听到咔咔声)(见图十)。注意:不能使用电动扳手、风动钻! (图十) 6. 施加若干次(约5次)制动,刹车间隙自动调整至正常范围,调整功能可通过蜗杆六角头在刹车即将结束时顺时针力向自动旋转观察到,至此安装过程结束。(见图十一)
自动调整臂工作原理
自动调整臂工作原理-标准化文件发布号:(9556-EUATWK-MWUB-WUNN-INNUL-DDQTY-KII
学习内容: 1、掌握汽车制动器自动调整臂装配图结构与零件装配关系 2、主要零件壳体结构与技术要求 3、结合所给参考资料写出所给汽车制动器自动调整臂工作原理与自动调整的装配关系 自动调整臂实际上就是一个开环的机械自动控制系统,其工作原理如图2-2所示。 控制盘固定在车轴上作为定位元件,其上的开口对应于标准的制动间隙值, 齿条可在开口内 上下移动(在壳体的带动下),在制动开始时,齿条与开口的上端接触,在制动过程中,齿条移到开口的下端。超量间隙的调整是在制动回位的过程中完成的。回位时,壳体如ω方向转动,壳体带动齿条移到开口的上端,如存在超量间隙△,壳体继续回位,齿条已不能移动,齿条驱动调整器转动调整器带动蜗杆。z方向转动驱动蜗轮转动一永久的角度(当然凸轮轴亦转过同样的角度△)而达到消除超量间隙△,调节制动间隙到标准值△Xo。 其工作原理如下图。
(1)制动间隙处于设计理想状态时。制动时,制动分泵连接叉推动主臂1逆时针旋转,大蜗杆7推动大蜗轮9,大蜗轮9通过内花键3带动凸轮轴转动实现制动。在臂体1逆时针转动时,因控制臂5为固定的,与其固定连接的大齿轮4不动,小齿轮6将沿大齿轮4的节圆滚动,即小齿轮6也逆时针转动;经内爪键17的传动,上端锯齿轮11相应逆时针转动。当制动间隙在理想状态内时,在上端锯齿轮11逆时针转动过程中,它将压缩顶簧13顺着下端锯齿轮12的锯齿斜而轴向移动,但不会跳齿。因小蜗杆右端为一单向超越离合器,下端锯齿轮12与小蜗杆不会转动。解除制动时,制动分泵连接叉推动主臂1顺时针旋转,大蜗杆7推动大蜗轮9,大蜗轮9通过内花键3带动凸轮轴转动解除制动,在臂体1顺时针转动时,小齿轮6将沿大齿轮4的节圆滚动,即小齿轮6也顺时针转动;经内爪键7的传动,上端锯齿轮11相应顺时针转动,同时在顶簧13作用,顺着下端锯齿轮12的锯齿斜而做反向的轴向移动,其运动的角度和位移均与制动时相同,因血不做间隙调整。
汽车制动器第二代自动调整臂技术分析
汽车制动器第二代自动调整臂技术分析 一,第二代自动调整臂的前世今生 瑞典Haldex是第一家推出第二代自动调整臂的企业。Haldex把其第二代自动调整臂命名为S-ABA,即Self-Automatic Brake Ad juster。第二代自动调整臂利用单向离合器,增加了棘轮机构,调整速度更慢,减少并避免了过调的可能。同时,控制臂的安装在规定的范围内任意位置固定,方便安装且不易发生安装错误。 尽管S-ABA早在90年代就已经推向市场,但它并没有象Haldex所期望的那样迅速取代第一代调整臂,而是在市场中艰难地成长。直到2005年之后,S-ABA才逐渐开始在欧洲各大主机厂使用。笔者经过对国外几家主机厂采购部门的调查,发现有三个原因阻止了第二代调整臂的快速扩张: 1. S-ABA只能替代部分第一代产品。到目前为止S-ABA仅能够替代间隙角度为7.4°、8.4°、9.4°。 2. 某些S-ABA产品在使用时,会发生制动过热现象。例如,韩国大宇客车在测试S-ABA时,发现有过热现象,因此大宇没有使用第二代调整臂。 3. S-ABA的价格比第一代产品高。由于S-ABA的生产成本高于第一代产品,导致其价格高于第一代调整臂。 以上的三个原因也是造成第二代自动调整臂一直在中国无法大批应用的主要原因。 尽管如此,由于第二代调整臂能够简化物流控制、方便安装、降低因安装错误导致的质量事故,很多主机厂都希望自动调整臂厂家能够改进设计,开发出调整功能稳定、覆盖面广、价格适中的第二代调整臂。因此,一些有实力的调整臂厂家,如,印度的ME
⑷使用寿命长,超过250万次。由于其调整过程是在制动即将结束、力矩最小时进行,从而保证整车的安全可靠,蜗轮副、单向离合器磨损极小。 ⑸结构先进。采用最终间隙感知工作原理,只对摩擦衬片和制动鼓之间由于磨损产生的超量间隙起调整作用,对应于制动鼓、摩擦衬片和S凸轮轴等的弹性变形不影响自动调整过程,保证间隙调整的连续、高效和稳定。 隆中第二代S-ASA自动调整臂爆炸图 四,二代自动调整臂优于一代自动调整臂的特点 1.产品通用性强:二代调整臂不像一代调整臂那样有控制臂角度的限制,因此产品的型号与一代产品相比大大减少。只要产品其它联接尺寸相同,一个二代产品可同时替代多种AA1产品。 2.对装配和维护人员的技术素质相对要低。降低了使用单位的培训费用。控制臂、螺栓断裂、控制臂打滑的问题也就减少了。
自动调整臂的安装说明
自动调整臂简介 一、工作原理: 汽车刹车间隙自动调整臂是在手动调整臂的基础上增加了齿轮、齿条、离合器、控制环等零件而构成,当松开制动调整臂回程时,由控制环控制齿条带动齿轮、蜗杆、蜗轮、凸轮轴,使因摩擦片磨损而增大的间隙得到自动调节,致使刹车间隙保持恒定。 二、自动调整臂具有其独特的产品优势,与手动调整臂相比,具有以下优点: 1、自动保持摩擦片和制动鼓之间间隙恒定,使刹车安全可靠, 不会出现跑偏、甩尾甚至制动失灵的现象。 2、使所有车轮的制动效果一致、稳定。 3、制动分泵推杆行程短,制动更加迅速可靠。 4、主要零部件选用进口原材料,延长了自动调整臂的寿命。 5、减少压缩空气的损耗,延长了空压机、制动分泵和压缩空气 系统中其它部件的寿命。 6、不需要人工经常调整,减少了维修次数,使车辆保养的时间 间隔得以延长,从而提高了经济效益。 三、自动调整臂的安装方法: 1、安装前需解除制动,确保弹簧气缸推杆处于初始位置。 2、把调整臂推装于花键轴头上,保证调整臂壳体上的箭头方向 与制动方向一致。(附图)
3、用手动扳手顺时针微调调整臂蜗杆六角头(附图), 使弹簧气缸推杆叉销子孔和调整臂销子孔自然对正,然后插入销子并销上开口销。 4、用挡圈、调整垫片和卡簧(或锁紧螺母)将调整臂固定在花键轴头上,并检查回位是否灵活。 5、顺着固定板上的箭头方向(附图), 推动固定板,直至推不动为止,然后拧紧固定螺栓,为了确认是否推到位,看固定板上的A线与盖板上的B线是否对齐,对齐说明推到位了(图1),否则没推到位(图2)。
图1 图2 如果固定板没有推到位,就把固定螺栓拧紧,这样会出现偏刹车、拖磨、抱死的现象发生,进而使轮鼓发热,导致客户或服务站误认为自调臂失效,造成刹车不好用。 6、用手动扳手顺时针转动调整臂蜗杆六角头(此时转动力矩小), 直至扳不动为止,此时刹车衬片与制动鼓接触,刹车间隙为0. 7、用手动扳手逆时针转动调整臂蜗杆六角头(此时转动力矩大, 会听到咔咔声)180°~270°即可。 8、试刹车五次以上,观察自动调整臂的工作情况;刹车若干次 后,刹车间隙将自动调整至设定间隙值。 四、自动调整臂的保养: 需定期注入2号锂基润滑脂保养,一般行使三个月或一万公里注油保养一次。、 五、使用注意事项: 1、自动调整臂能自动及时地补偿刹车磨损带来的增量间隙,不需人工调整。 2、定期检查调整臂固定板及固定支架紧固螺钉是否松动,若松动必须及时紧固。(若紧固螺钉松动则自调臂不起作用)
制动间隙调整臂寿命试验方法
江苏联升汽车部件有限公司JIANGSU LIANSHENG AUTOMOBILE PARTS CO.,LTD 制动间隙自动调整臂 台架试验方法 编号:LSJSB20131220001 生效日期:2014.01.01
1.范围 本标准规定了制动间隙自动调整臂寿命试验方法和相应的评价指标。 本标准适用于气压制动凸轮式制动器的制动间隙自动调整臂。 2.引用标准 SAE J1461 自动调整臂标准(美国) SAE J1462 外置式自动间隙调整臂试验方法 SAE J1513 外置式自动间隙调整臂性能要求 CJ/T 242-2007 城市客车外置式制动间隙自动调整臂 3.术语和定义 3.1制动间隙自动调整臂 在行车过程中,能根据制动器摩擦衬片的磨损情况自动调整摩擦衬片和制动鼓之间的间隙,并使之保持在一定范围内的调整臂称为制动间隙自动调整臂,以下简称自调臂 3.2额定载荷 在相匹配的最大规格制动气室的额定工作气压下,自调臂所承受的载荷称为自调臂的额定载荷。 4 试验项目 4.1性能试验 a)自调功能稳定性试验 b)自调功能寿命实验 c)低压性能试验 d)壳体、蜗轮、蜗杆耐久性试验
5 实验条件 5.1被试验样品应为在正常生产流程及工艺条件下生产出的符合图纸及技术文件规定的合格产品。 5.2被试样件应在实验装置上正确安装和调整。 5.3调节试验装置的试验频率为12-15次/min,每次制动加载时间不超过2秒,其余时间应能保证试验样品能完全回位。 6.试验方法 6.1 自调功能稳定性试验 6.1.1取被测样件在试验装置上正确安装(可参照自调臂安装说明书) 6.1.2在制动鼓与制动蹄左、中、右三个位置分别作一标记,实验过程中测试点 均取此三个位置点测量,并保证每次试验起始状态时同一测量点制动蹄与制动鼓的间隙始终一致。 6.1.3在自调臂蜗杆轴头部和通盖上作一位置标记,便于观察蜗杆轴的转动情况 (即自调情况) 6.1.4调整气室制动气压分别在0.2Mpa、0.4Mpa、0.6Mpa和0.8Mpa,启动试验 台,观察自调臂蜗杆轴头部处的标记,直至肉眼观察不到蜗杆轴转动时,记录此时的制动次数,然后再次往复实验10次后停止试验台,测量6.1.2所作三处标记处的制动蹄与制动鼓的间隙值,并记录。 6.1.5 调整通孔堵盖,使调整扭矩分别在40N·m、30N·m、20N·m、15N·m 和10N·m时重复6.1.4实验并记录。 6.2自调功能寿命实验 6.2.1重复6.1.1、6.1.2、6.1.3动作,完成实验准备工作 6.2.2调整通孔堵盖,保持调整力矩在25-30N·m,调整气室制动气压在0.4Mpa,
自动调整臂可研
汽车制动间隙自动调整臂产品开发可行性研究报告 承担单位:国营第五二四厂 承担单位负责人:姜泽栋 承担单位联系人:石如松 张浩 电话:(0432)3044869 传真:(0432)3039340 编制日期:二零零三年二月
目录 1. 项目概况 1.1 项目名称 1.2 项目承担单位 1.3 项目负责人 1.3.1法定代表人 1.3.2 技术负责人 1.3.3 经济负责人 1.3.4 项目负责人 2. 承担单位概况 3. 项目环境与发展前景分析 3.1 项目产品(或技术)主要应用领域、国内外现状与发展趋势3.2 产业化关联分析(含对行业技术进步的作用) 3.3 市场需求预测与市场定位 4.项目研究开发主要内容 4.1 技术成果来源 4.2 研究开发的现有基础 4.3 研究开发的主要内容(含关键技术) 4.3.1 技术(含性能)指标 4.3.2 技术与工艺特点(与现有的比较) 5.项目研究开发方案
5.1 研究开发目标 5.1.1 研究开发项目的具体目标 5.1.2 开发目标的检测 5.2 研究开发的方案(含工艺路线)5.3 设备选择(含现有设备利用)5.4 原材料供应与外协配套 5.5 动力供应与辅助设施 5.6 厂房建设与土建工程 5.7 环境保护与职业安全卫生 5.8 组织管理与劳动定员 6. 投资估算与资金来源 6.1 研究开发投资估算 6.1.1 研究开发投资估算依据和结果 6.1.2 研究开发投资构成及资金来源 7. 项目实施计划与措施 8. 风险收益评价与产业化衔接计划8.1 投资风险分析 8.2 投资回报 8.3 产业化衔接计划 9. 结论与建议
刹车调整臂安装
东风153客车桥HALDEX刹车间隙 自动调整臂安装步骤 一、前桥HALEDX刹车间隙自动调整臂的拆卸 1、移去制动分泵连接叉的开口销、圆柱插销,使之与刹车间隙自动调整臂分离。 2、拆去控制臂与定位支架相连的支柱螺栓,螺母垫片。 3、拆去轮轴上的轴向定位螺检及垫片。 4。SW12的扳手逆时针方向转动刹车间隙自动调整臂上的六角调整螺母,移出调整臂(所需力矩较大,会听到咔咔声),随后将其拆除。 二、前桥HALDEX刹车间隙自动调整臂的安装 1.解除制动,确保制动分泵推杆处于初始位置。 2. 在S凸轮轴上涂上 黄油。将调整臂安装在 S 凸轮轴上,调整臂壳 体上箭头方向应与制动 方向一致,顺时针转动 调整臂端部的六角螺 母,使调整臂转入分泵 推杆U型叉内,直至调 整臂上的孔与U 形叉 孔对正。在圆柱销上涂 上黄油,将其轻松插入 叉孔,锁上开口销。(注 意:调整臂上孔与U形 叉孔一定要对正。) 3 .将控制臂沿控制臂 上箭头示意方向推动, 直至推不动为止。目的 是保证磨擦衬片和制动 鼓之间的设定间隙。随 后先将HALDEX卡箍式 定位支架安装在凸轮轴 轴端外壳上,在定位支 架上的螺母、垫片最终紧固前,将控制臂通过定位支架的螺栓支柱,螺母,垫片定位于定位支架上(详请参见图示),最后紧固定位支架于车桥上(通过其上的两只螺母,紧固力矩至少为20nm)。控制臂与定位支架的联接方式见图示。 4.用两只螺栓、垫片将调整臂固定在S凸轮轴上。 5.用SW12的扳手顺时针方向(转动力矩小,无咔咔声)转动调整臂的六角螺母,直至磨擦衬片与制动鼓按触,然后再逆时针方向转动六角螺母3/4圈(转动力矩较大,会听到咔咔声),注意不能用电动扳手或风动钻。 6.施加若干次制动,刹车间隙将自动调整至正常范围。调整功能可通过六角螺母在刹车即将结束时顺时针方向的自动旋转观察到。至此安装过程完毕。