数学建模零件参数的优化设计
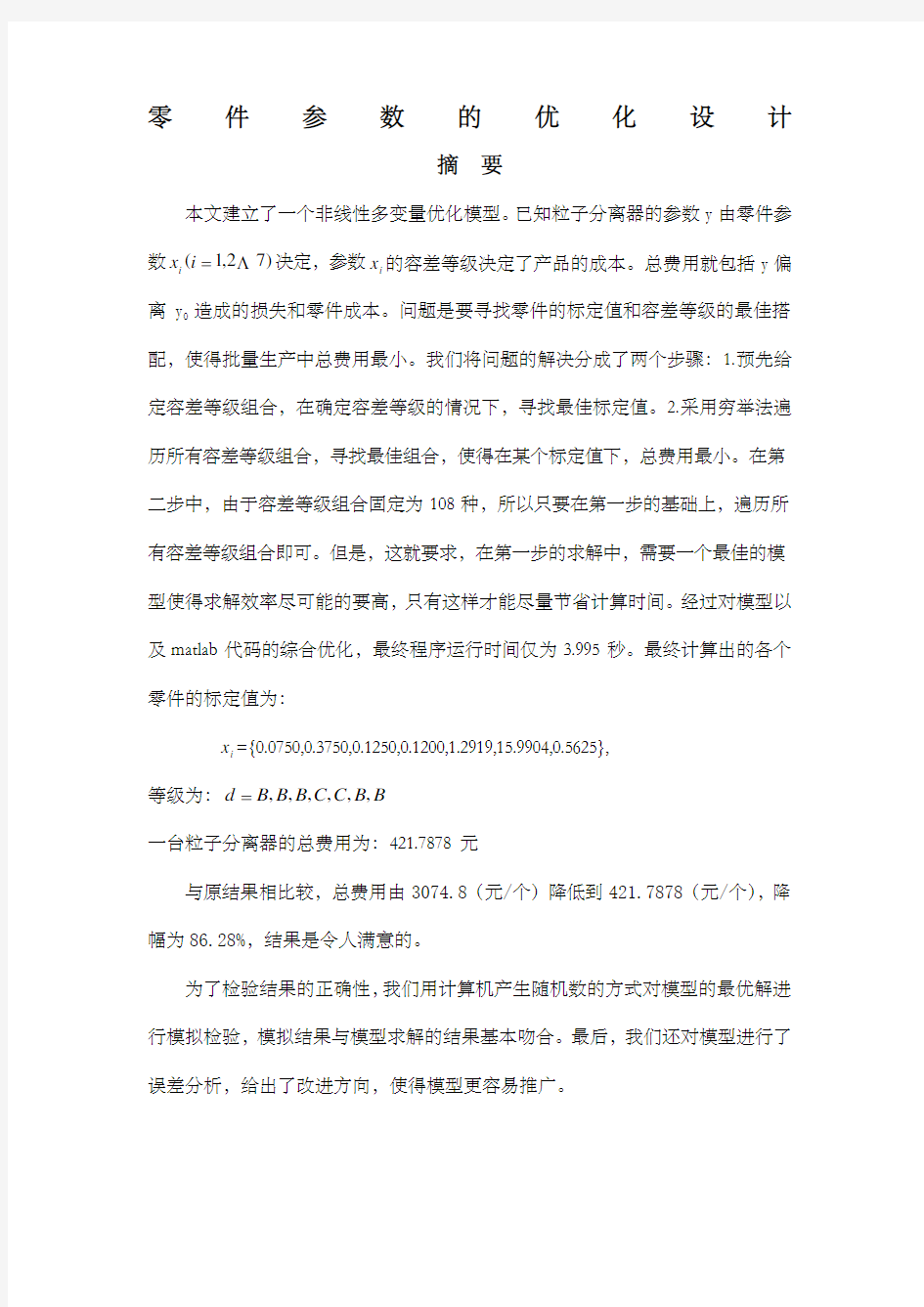

零件参数的优化设计
摘要
本文建立了一个非线性多变量优化模型。已知粒子分离器的参数y由零件参
数)7
2,1
(
i
x
i 决定,参数
i
x的容差等级决定了产品的成本。总费用就包括y偏
离y0造成的损失和零件成本。问题是要寻找零件的标定值和容差等级的最佳搭配,使得批量生产中总费用最小。我们将问题的解决分成了两个步骤:1.预先给定容差等级组合,在确定容差等级的情况下,寻找最佳标定值。2.采用穷举法遍历所有容差等级组合,寻找最佳组合,使得在某个标定值下,总费用最小。在第二步中,由于容差等级组合固定为108种,所以只要在第一步的基础上,遍历所有容差等级组合即可。但是,这就要求,在第一步的求解中,需要一个最佳的模型使得求解效率尽可能的要高,只有这样才能尽量节省计算时间。经过对模型以及matlab代码的综合优化,最终程序运行时间仅为3.995秒。最终计算出的各个零件的标定值为:
i
x={0.0750,0.3750,0.1250,0.1200,1.2919,15.9904,0.5625},
等级为:B
B
C
C
B
B
B
d,
,
,
,
,
,
一台粒子分离器的总费用为:421.7878元
与原结果相比较,总费用由3074.8(元/个)降低到421.7878(元/个),降幅为86.28%,结果是令人满意的。
为了检验结果的正确性,我们用计算机产生随机数的方式对模型的最优解进行模拟检验,模拟结果与模型求解的结果基本吻合。最后,我们还对模型进行了误差分析,给出了改进方向,使得模型更容易推广。
关键字:零件参数 非线性规划 期望 方差
一、问题重述
一件产品由若干零件组装而成,标志产品性能的某个参数取决于这些零件的参数。零件参数包括标定值和容差两部分。进行成批生产时,标定值表示一批零件该参数的平均值,容差则给出了参数偏离其标定值的容许范围。若将零件参数视为随机变量,则标定值代表期望值,在生产部门无特殊要求时,容差通常规定为均方差的3倍。
进行零件参数设计,就是要确定其标定值和容差。这时要考虑两方面因素:一是当各零件组装成产品时,如果产品参数偏离预先设定的目标值,就会造成质量损失,偏离越大,损失越大;二是零件容差的大小决定了其制造成本,容差设计得越小,成本越高。
试通过如下的具体问题给出一般的零件参数设计方法。
粒子分离器某参数(记作y )由7个零件的参数(记作x 1,x 2,...,x 7)决定,经验公式为:
7616
.1242
3
56
.02485
.01235136.0162.2142.174x x x x x x x x x x x Y
y 的目标值(记作y 0)为1.50。当y 偏离y 0+0.1时,产品为次品,质量损失为1,000元;当y 偏离y 0+0.3时,产品为废品,损失为9,000元。
零件参数的标定值有一定的容许范围;容差分为A、B、C三个等级,用与标定值的相对值表示,A等为+1%,B等为+5%,C等为+10%。7个零件参数标定值的容许范围,及不同容差等级零件的成本(元)如下表(符号/表示无此等级零件):
现进行成批生产,每批产量1,000个。在原设计中,7个零件参数的标定值为:
x 1=0.1,x
2
=0.3,x
3
=0.1,x
4
=0.1,x
5
=1.5,x
6
=16,x
7
=0.75;容差均取最便宜的等级。
请你综合考虑y偏离y0造成的损失和零件成本,重新设计零件参数(包括
标定值和容差),并与原设计比较,总费用降低了多少?
二、模型假设
1、将各零件参数视为随机变量,且各自服从正态分布;
2、假设组成离子分离器的各零件互不影响,即各零件参数互相独立;
3、假设小概率事件不可能发生,即认为各零件参数只可能出现在容许范围内;
4、在大批量生产过程中,整批零件都处于同一等级,。本题可认为1000各零件都为A等、B等或C等;
5、生产过程中出质量损失外无其他形式的损失;
6、在质量损失计算过程中,认为所有函数都是连续可导的。
三、符号说明
i x :第i 类零件参数的标定值(i=1,2……7);
i x :第i 类零件参数的实际值相对目标值的偏差(i=1,2……7);
i r :第i 类零件参数的容差(i=1,2,……7);
i :第i 类零件参数的方差(i=1,2,……7);
i i b a ,:标定值i x 的上、下限;
y :离子分离器某参数的实际值;
0y :离子分离器该参数的目标值;
y :离子分离器某参数的均值;
y :离子分离器某参数的实际值y 相对平均值y 的偏差;
y :离子分离器某参数的方差;
1P :一批产品中正品的概率;
2P :一批产品中次品的概率;
3P :一批产品中废品的概率;
W:一批产品的总费用(包括损失和成本费);
C:第i类零件对应容差等级为j的成本(j=A,B,C)单位:元/个。
ij
四、问题分析Array
其线性化
该问题是一定约束条件下的最优化问题,经分析题意,拟建立以总费用为目
标函数的非线性规划模型。总费用由损失费和成本费两部分组成,零件成本由简
单的线性代数式决定,而损失费涉及概率分布的非线性函数。要求出损失费,就必须知道一批产品的次品率和废品率,结合各类零件都服从),(2
i i x N ,可假设y 也服从正态分布,联想正态分布的性质——当各变量均服从正态分布时,其线性组合也服从正态分布。题中所给经验公式为一复杂的非线性的公式,无法直接对其分析处理,所以需借助泰勒公式将其展开并作相应处理使其线性化。而对于零件成本,需先确定容差等级才能求得成本费。由容差等级和各类零件的标定值
i x 便可知道给类零件的容差i r 。最后,便将问题转化为i x 、i r 关于总目标函数的
最优解的问题上。
在进行零件参数设计时,如果零件设计不妥,造成产品参数偏离预先设定值,就会造成质量损失,且偏差越大,损失也越大;零件容差的大小决定了其制造成本,容差设计得越小(即精度越高)零件成本越高。 合理的设计方案应既省费用又能满足产品的预先设定值,设计方向应该如下:
(1)设计的零件参数,要保证由零件组装成的产品参数符合该产品的预先设定值,即使有偏离也应是在满足设计最优下的容许范围。
(2)零件参数(包括标定值和容差等级)的设计应使总费用最小为优。 此外分析零件的成本及产品的质量损失不难发现,质量损失对费用的影响远大于零件成本对费用的影响,因而设计零件参数时,主要考虑提高产品质量来达到减少费用的目的。
五、模型建立
为了确定原设计中标定值(
的期望值)及已给的容差对产品性能参数影响而导致的总损失W ,即确定
偏离目标值
所造成的损失和零
件成本,先列出总损失的数学模型表达如下:
)90001000(1000327
1
P P C W i ij
当然,为了确定总损失W ,必须知道1P 、2P 、3P (即正品、次品及废品的概率)。为此,将经验公式用泰勒公式在)72,1( i x X i 处展开并略去二次以上高次项后来研究y 的概率分布,设y x f )(,则
7
1)()(i i i
i x x f
x f y X f 将标定值)72,1( i x i 带入经验公式即得 )(i x f y 所以 i i i
x x f
y y y
7
1 由于在加工零件时,在标定值知道的情况下,加工误差服从正态分布,即 )(2
,0N ~i i x 且i x 相互独立,由正态分布性质可知
),0(~2
y N y ),(~2
y y N y
由误差传递公式得 227
12
7
12
)()()(i i i i i
i i i y
x x x f x f (1)
由于容差为均方差的3倍,容差与标定值的比值为容差等级,则
3
1
.0,305.0,301.0
i
i
x y 的分布密度函数为
2
2
21)(y y y e
y y
y 偏离1.00 y 的概率,即次品的概率为
8
.16
.14
.12
.12)()()()(y d y y d y P (2)
y 偏离3.00 y 的概率,即废品的概率为
8
.12
.13)()()()(y d y y d y P (3)
由于y 偏离0y 越远,损失越大,所以在y 固定时,调整y 使之等于目标值0y 可降低损失。取0y y y 即0y y ,则 )1
.0(
2y
P )3
.0(
3y
P
)(t 为标准正态分布函数。
综合考虑y 偏离y 0造成的损失和零件成本,设计最优零件参数的模型建立如下: 目标函数
min )90001000(1000327
1P P C W i ij
s.t. )72,1( i a x b i
i i )72,1()(0 i x f y i
六、模型求解
初略分析
对于原给定的设计方案,利用matlab 编程计算(见附录),计算结果如下:
由于按原设计方案设计的产品正品率过低,损失费过高,显然设计不够合理。进一步分析发现,参数均值y=1.7256偏离目标值
y=1.5太远,致使损失过大。
尽管原设计方案保证了正本最低,但由于零件参数的精度过低,导致正品率也过低。所以我们应综合考虑成本费和损失费。
模型的实现过程:
本模型通过matlab进行求解,我们通过理论模型求解和随机模拟的求解过程如下:在给定容差等级的情况下,利用matlab中求解非线性规划的函数fmincon,通过多次迭代求解,最终求得一组最优解。最初,我们设定的fmincon 函数的目标函数就是总费用,约束条件为各个标定值的容许范围,以及各零件标定值带入产品参数表达式应为
y,即1.5。然而,在迭代过程中我们发现,求解
过程十分慢,在给定容差等级的确定的情况下,计算最优标定值需要将近400秒,如果在此基础上对108种容错等级进行穷举查找最优组合,将需要大概12小时。显然这是不合理的。因此,我们在仔细对matlab实现代码研究发现,求解过程之所以慢,是因为代码中存在多次调用求偏导和积分的函数,在fmincon的多次迭代中,耗费大量时间。所以,为了提高求解速度,我们首先利用matlab中diff 函数对产品参数中的各个表达式进行求偏导,然后得到多个带参表达式,利用int 函数对y的概率密度函数进行积分,分别得到出现次品和废品概率的表达式,然
后将这些表达式写进程序里,这样在求解过程中就不需要在每一次迭代中都要求偏导和积分了,修改后的程序运行时间大大减少。
程序流程图
算 法 等级未计算 结 束
min W W Y
N
程序见附录,求解结果如下:
运行总时间:3.995s
离子分离器参数均值y=1.5
=0.0689
离子分离器参数方差
y
模型检验
对设计方案进行动态模拟,由于每种零件参数均服从正态分布,用正态分布随机数发生器在每种零件参数允许范围内产生1000个随机数参与真实值
x的计
i
算随机模拟N次后结果如下:
正品率次品率废品率成本费损失费总费用0.8570 0.1430 0.0000 275 143 418
=0.0689画出y的概率分布图,再对x随机取样画根据最优解的y=1.5,
y
出y的概率分布图(见图6.1),由图可知:两组数据所画概率分布图的拟合度相当高,进一步确保了模型的正确性。
图6.1概率分布图对比图
通过以上数据,与原设计方案所得结果相比较,总费用由3074.8(元/个)降低到421.7878(元/个),降幅为86.28%,结果是令人满意的。
七、误差分析
1、在建模过程中,通过泰勒公式将)(X f y 展开并略去二次及以上项使线
性化,不可避免地产生了截断误差,所以展开后的式子只是原经验公式的近似关系式。但在一般情况下,线性化和求总和在实用上具有足够的精度,所以由于函数线性化而略去的高次项可以忽略不计。在函数关系式较复杂的情况下,将其线性化更具有明显的优势。
2、本模型忽略了小概率事件发生的可能,认为零件的参数只可能出现在允 范围内,即 i i i i x x 3,3 。现实中,小概率事件仍有发生的可能性,但在大批量生产中,小概率事件的发生对最终结果没有影响,所以可以忽略。
3、该模型对于质量损失的计算,将所有函数都看作连续函数,而这对于每 个零件参数而言是不可能的,所以其中也会产生误差。
八、模型的评价及推广
1.优点
(1)建模过程中,采用泰勒公式将经验公式简化,并假设各零件参数都服从满足大量数据的正态分布,使得整个模型的建立及求解得到大大简化。
(2)本模型运用概率统计与优化知识对零件参数进行优化设计。通过建立一个反映设计要求的数学模型,利用MATLAB 软件,经过编程来实现对设计方案参
数的调整,将总费用由3074.8(元/个)降低到421.7878(元/个),降幅达到86.28%,结果还是令人十分满意的。
(3)本模型在程序运算的过程中,做了适当处理,将每次循环本该由计算机求偏导和积分的提前人为处理,将求偏导和积分后的算式写入程序中,这样大大节约了运算时间,将运行时间由几个小时缩短为3.0995s。
2.缺点
(1)本模型在模型的求解过程中,对一些可接受范围内的误差直接进行了忽略,因而对于结果的精确性还是会有一定的影响。
(2)本模型是建立在一些假设中的,所有实用性受到了限制,在实际生产中,如果可以把更多的一些因素考虑进去应该会更好。在已假定的条件下,本模型的优化结果是好的。
3推广
此模型有较强的应用价值。工程中往往因为某个零件的选取不当,而影响产品的参数,使可靠性降低,造成了极大的经济损失。所以需综合考虑零件成本和质量,以求获得最大的经济效益。
本模型具有广泛的适用性,很容易加以推广。模型中的设计变量可以推广到个的情形,即设计变量,其中设计空间是一个维空间。本模不仅适用于粒子分离器参数的设计,而且也可用于类似的机构、零部件、工艺设备等的基本参数的设计问题;容差等级同样可推广应用。
参考文献
【1】韩之俊,姚平中,《概率与统计》,国防工业出版社,1985
【2】陈宝林,《最优化理论与算法》,清华大学出版社,1989
【3】裘宗燕,《数学软件系统的应用及程序设计》,北京大学出版社,1994 【4】许波,《Matlab 工程数学应用》,清华大学出版社,2001
附录:matlab代码:
function f=result
%穷举108种容错等级组合求解全局最优解
fval=inf;
tic
%Bmin=[2 3 3 3 3 3 2];
%Xmin
B(1)=2;
B(5)=3;
for i=2:3
B(2)=i;
for j=1:3
B(3)=j;
for t=1:3
B(4)=t;
for g=1:3
B(6)=g;
for m=1:2
B(7)=m;
[fv,x]=getcost(B);
if fv Xmin=x; Bmin=B; fval=fv; end; end; end; end; end; end; f=fval,Xmin,Bmin,p=getP(Xmin,Bmin) toc simulation(Xmin,Bmin);%用随机法和计算的结果进行模拟比较function f=simulation(MU,B) %用随机法和计算的结果进行模拟比较 for i=1:10000 y(i)=Yfun(getparaX(MU,B)); end; [f,xi] = ksdensity(y); plot(xi,f); % 画经验概率密度曲线 hold on; y0=Yfun(MU); fc=getfcY(MU,B); %{ x = normrnd(y0,fc,1,10000); [f1,xj] = ksdensity(x); plot(xj,f1,'r'); %} x0=min(y):0.01:max(y); y=((2*pi)^0.5*fc)^(-1)*exp(-(x0-y0).^2/2/fc^2); plot(x0,y,'r'); %{ x=min(y):0.01:max(y); yg=gaussmf(x,[fc,y0]); plot(x,yg,'r'); %} title('对照图'); gtext('注:蓝线为对x随机取样求得的y分布'); gtext('红线为根据模型计算出的y分布'); xlabel('y'); ylabel('y的概率密度'); hold off; function [f,x]=getcost(B) %在给定容差等级的情况下求最优的标定值,使得Y的均值为y0的情况下,方差最小 MU=[0.1 0.3 0.1 0.1 1.5 16 0.75];%给定初始的标定值 options=optimset('LargeScale','off','Display','off');%,'Tolx',1.0000e-032); [x,fval]=fmincon('getfcY',MU,[],[],[],[],[],[],'mycon',options,B); x,B,f=cost(x,B) function [c,ceq]=mycon(MU,B) %求最优标定值时的约束条件 %c为不等式约束 %ceq为等式约束 c(1)=MU(1)-0.125; c(2)=0.075-MU(1); c(3)=MU(2)-0.375; c(4)=0.225-MU(2); c(5)=MU(3)-0.125; c(6)=0.075-MU(3); c(7)=MU(4)-0.125; c(8)=0.075-MU(4); c(9)=MU(5)-1.875; c(10)=1.125-MU(5); c(11)=MU(6)-20; c(12)=12-MU(6); c(13)=MU(7)-0.935; c(14)=0.5625-MU(7); ceq(1)=Yfun(MU)-1.5; function f=cost(MU,B) %当标定值为MU,容差等级为B时,求费用 f=25; p=getP(MU,B);%求正品、次品、废品的概率 if(B(2)==2) f=f+50; else f=f+20; end; switch (B(3)) case 1 f=f+200; case 2 f=f+50; case 3 f=f+20; end; switch (B(4)) case 1 f=f+500; case 2 f=f+100; case 3 f=f+50; end; f=f+50; switch (B(6)) case 1 f=f+100; case 2 f=f+25; case 3 f=f+10; end; if(B(7)==1) f=f+100; else f=f+25; end; f=f+p(2)*1000+p(3)*9000; function f=getfcY(MU,B) %对于所给的标定值和容差求Y的方差 f=0; B=int32(B); for i=1:7 if B(i)==1 sigma(i)=MU(i)*0.01/3; end; if B(i)==2 sigma(i)=MU(i)*0.05/3; end; if B(i)==3 sigma(i)=MU(i)*0.1/3; end; end; x1=MU(1);x2=MU(2);x3=MU(3);x4=MU(4);x5=MU(5);x6=MU(6);x7=MU(7); %求Y对各变量的偏导的评分与对应的方差乘积之和 f=(pd1(x1,x2,x3,x4,x5,x6,x7)*sigma(1))^2;f=f+(pd2(x1,x2,x3,x4,x5,x6,x7)*sigma(2))^2 ; f=f+(pd3(x1,x2,x3,x4,x5,x6,x7)*sigma(3))^2;f=f+(pd4(x1,x2,x3,x4,x5,x6,x7)*sigma(4)) ^2; f=f+(pd5(x1,x2,x3,x4,x5,x6,x7)*sigma(5))^2;f=f+(pd6(x1,x2,x3,x4,x5,x6,x7)*sigma(6)) ^2; f=f+(pd7(x1,x2,x3,x4,x5,x6,x7)*sigma(7))^2; f=abs(f^0.5); function f=pd1(x1,x2,x3,x4,x5,x6,x7) %Y对x1的偏导 f=8721/50/x5*(x3/(x2-x1))^(17/20)*((1-131/50*(1-9/25/... (x4/x2)^(14/25))^(3/2)*(x4/x2)^(29/25))/x6/x7)^(1/2)+... 148257/1000*x1/x5/(x3/(x2-x1))^(3/20)*((1-131/50*(1-9/25/(x4/x2)... ^(14/25))^(3/2)*(x4/x2)^(29/25))/x6/x7)^(1/2)*x3/(x2-x1)^2; function f=pd2(x1,x2,x3,x4,x5,x6,x7) %Y对x2的偏导 f=-148257/1000*x1/x5/(x3/(x2-x1))^... (3/20)*((1-131/50*(1-9/25/(x4/x2)^(14/25))^(... 3/2)*(x4/x2)^(29/25))/x6/x7)^(1/2)*x3/(x2-x1)^... 2+8721/100*x1/x5*(x3/(x2-x1))^(17/20)/((1-131/50*(1-9/25/... (x4/x2)^(14/25))^(3/2)*(x4/x2)^(29/25))/x6/x7)^(1/2)*(24759/31250*... (1-9/25/(x4/x2)^(14/25))^(1/2)/(x4/x2)^(2/5)*x4/x2^2+3799/1250*(1-9/25/... (x4/x2)^(14/25))^(3/2)*(x4/x2)^(4/25)*x4/x2^2)/x6/x7; function f=pd3(x1,x2,x3,x4,x5,x6,x7) %Y对x3的偏导 f=148257/1000*x1/x5/(x3/(x2-x1))^(3/20)*((1-131/50*... (1-9/25/(x4/x2)^(14/25))^(3/2)*(x4/x2)^(29/25))/x6/x7)^(1/2)/(x2-x1); function f=pd4(x1,x2,x3,x4,x5,x6,x7) %Y对x4的偏导 f=8721/100*x1/x5*(x3/(x2-x1))^(17/20)/((1-131/50*(1-9/25/(x4/x2)^(14/25))^... 实验六 PID 控制系统参数优化设计 一.实验目的: 综合运用MATLAB 中SIMULINK 仿真工具进行复杂控制系统的综合设计与优化设计,综合检查学生的文献查阅、系统建模、程序设计与仿真的能力。 二.实验原理及预习内容: 1.控制系统优化设计: 所谓优化设计就是在所有可能的设计方案中寻找具有最优目标(或结果)的设计方法。控制系统的优化设计包括两方面的内容:一方面是控制系统参数的最优化问题,即在系统构成确定的情况下选择适当的参数,以使系统的某些性能达到最佳;另一方面是系统控制器结构的最优化问题,即在系统控制对象确定的情况下选择适当的控制规律,以使系统的某种性能达到最佳。 在工程上称为“寻优问题”。优化设计原理是“单纯形法”。MATLAB 中语句格式为:min ('')X f s =函数名,初值。 2.微分方程仿真应用:传染病动力学方程求解 三.实验内容: 1.PID 控制系统参数优化设计: 某过程控制系统如下图所示,试设计PID 调节器参数,使该系统动态性能达到最佳。(习题5-6) 1020.1156s s e s s -+++R e PID Y 2.微分方程仿真应用: 已知某一地区在有病菌传染下的描述三种类型人数变化的动态模型为 11212122232 3(0)620(0)10(0)70X X X X X X X X X X X X ααββ?=-=?=-=??==? 式中,X 1表示可能传染的人数;X 2表示已经得病的人数;X 3表示已经治愈的人数;0.0010.072αβ==;。试用仿真方法求未来20年内三种人人数的动态变化情况。 四.实验程序: 建立optm.m 文件: function ss=optm (x) global kp; global ki; global kd; global i; kp=x (1); ki=x (2); kd=x (3); i=i+1 [tt,xx,yy]=sim('optzwz',50,[]); yylong=length(yy); ss=yy(yylong); 建立tryopt.m 文件: global kp; global ki; global kd; global i; i=1; result=fminsearch('optm',[2 1 1]) 建立optzwz.mdl: 零件参数的优化设计 摘 要 本文建立了一个非线性多变量优化模型。已知粒子分离器的参数y 由零件参数)72,1( =i x i 决定,参数i x 的容差等级决定了产品的成本。总费用就包括y 偏离y 0造成的损失和零件成本。问题是要寻找零件的标定值和容差等级的最佳搭配,使得批量生产中总费用最小。我们将问题的解决分成了两个步骤:1.预先给定容差等级组合,在确定容差等级的情况下,寻找最佳标定值。2.采用穷举法遍历所有容差等级组合,寻找最佳组合,使得在某个标定值下,总费用最小。在第二步中,由于容差等级组合固定为108种,所以只要在第一步的基础上,遍历所有容差等级组合即可。但是,这就要求,在第一步的求解中,需要一个最佳的模型使得求解效率尽可能的要高,只有这样才能尽量节省计算时间。经过对模型以及matlab 代码的综合优化,最终程序运行时间仅为3.995秒。最终计算出的各个零件的标定值为: i x ={0.0750,0.3750,0.1250,0.1200,1.2919,15.9904,0.5625}, 等级为:B B C C B B B d ,,,,,,= 一台粒子分离器的总费用为:421.7878元 与原结果相比较,总费用由3074.8(元/个)降低到421.7878(元/个),降幅为86.28%,结果是令人满意的。 为了检验结果的正确性,我们用计算机产生随机数的方式对模型的最优解进行模拟检验,模拟结果与模型求解的结果基本吻合。最后,我们还对模型进行了误差分析,给出了改进方向,使得模型更容易推广。 关键字:零件参数 非线性规划 期望 方差 一、问题重述 一件产品由若干零件组装而成,标志产品性能的某个参数取决于这些零件的参数。零件参数包括标定值和容差两部分。进行成批生产时,标定值表示一批零件该参数的平均值,容差则给出了参数偏离其标定值的容许围。若将零件参数视为随机变量,则标定值代表期望值,在生产部门无特殊要求时,容差通常规定为均方差的3倍。 进行零件参数设计,就是要确定其标定值和容差。这时要考虑两方面因素:一是当各零件组装成产品时,如果产品参数偏离预先设定的目标值,就会造成质量损失,偏离越大,损失越大;二是零件容差的大小决定了其制造成本,容差设计得越小,成本越高。 试通过如下的具体问题给出一般的零件参数设计方法。 粒子分离器某参数(记作y )由7个零件的参数(记作x 1,x 2,...,x 7)决定,经验公式为: 7616 .1242 3 56 .02485 .01235136.0162.2142.174x x x x x x x x x x x Y ??? ? ????? ? ???????? ??--???? ? ??-????? ???=- y 的目标值(记作y 0)为1.50。当y 偏离y 0+0.1时,产品为次品,质量损失为1,000元;当y 偏离y 0+0.3时,产品为废品,损失为9,000元。 零件参数的标定值有一定的容许围;容差分为A、B、C三个等级,用与标定值的相对值表示,A等为+1%,B等为+5%,C等为+10%。7个零件参数标定值的容许围,及不同容差等级零件的成本(元)如下表(符号/表示无此等级零件): Min=90000; global H A C %全局变量 H=[10000,25,10000;20,50,10000;20,50,200;50,100,500;50,10000,10000;10,25,100;10000,25,100 ]; %成本矩阵 A=[0.1 0.05 0.01;0.1 0.05 0.01;0.1 0.05 0.01;0.1 0.05 0.01;0.1 0.05 0.01;0.1 0.05 0.01;0.1 0.05 0.01]; %容差矩阵 C=zeros(7,3); 把容差选择矩阵元素全部赋值为0 for z=1:1:3 for x=1:1:3 for c=1:1:3 for v=1:1:3 for g=1:1:3 for n=1:1:3 for m=1:1:3 D=[z x c v g n m]; C=zeros(7,3); for i=1:1:7 C(i,D(i))=1; end %产生7 3列矩阵,该矩阵特点是每一行只有一个 1 ,其它两个数为0。本矩阵是为了对零件容差等级 进行选择 lb=[0.075 0.225 0.075 0.075 1.125 12 0.5625]; ub=[0.125 0.375 0.125 0.125 1.875 20 0.935]; X0=[0.075 0.225 0.075 0.075 1.125 12 0.5625]; [xopt fopt]=fmincon(@mubiao,X0,[],[],[],[],lb,ub,[]); if fopt ADAMS/VIEW 参数化和优化设计实例详解本例通过小球滑落斜板模型,着重详细说明参数化和优化设计的过程。 第一步,启动adams/view(2014版),设置工作路径,设置名称为incline。 名称 存储路径第二部,为满足模型空间,设置工作网格如图参数。 修改尺寸 第三部创建斜板。点击Bodies选项卡,选择BOX,然后建模区点击鼠标右键,分别设置两个点,坐标为(0,0,0)和(-500,-50,0),创建完模型,然后右键Rename,修改名称为xieban。 右键输入坐标,创建点BOX rename 输入xieban 第四部创建小球。点击Bodies选项卡,选择Sphere,然后建模区点击鼠标右键,分别设置两个点,球心坐标为(-500,50,0)和半径坐标(-450,50,0),创建完模型,然后右键Rename,修改名称为xiaoqiu。 输入两点 Rename,及创建效果 第五部创建圆环。点击Bodies选项卡,选择Torus,然后建模区点击鼠标右键,分别设置两个点,圆环中心坐标为(450,-1000,0)和大径坐标(500,-1000,0),创建完模型,然后右键Rename,修改名称为yuanhuan。完成后效果如下图: 第六部修改小球尺寸及位置。首先修改小球半径为25mm,在小球上右键,选择球体,点击Modify,然后设置如下图;然后修改小球位置,将Y坐标移到25mm处,选择Marker_2点, 右键点击Modify,然后设置坐标位置如下图。 右键编辑球半径 修改半径为25 改后效果 修改球的位置 设置球坐标 完成修改后效果 第七部修改圆环尺寸及位置。将圆环绕X轴旋转90度,选择Marker_3点,右键点击Modify,然后设置坐标位置如下图。修改圆环尺寸,大径为40mm,截面圆环半径为12mm,右键,选择圆环体,点击Modify ,然后设置如下图。至此,模型建立完毕。 修改圆环位置 一、问题重述 1、利用优化设计相关理论计算法,对某设计问题做优化设计。要求如下: ①列出优化数学模型; ②选择所用优化算法; ③画出程序框图; ④程序编写; ⑤程序调试运算结果。 现根据以上条件,结合生活实际,准备以铁板为材料设计一鱼缸,为了能使鱼儿有更大的生存空间,要求鱼缸容积最大。 现有边长为5米长的方形铁板,预备在四个角减去四个相等的方形面积,用以制成方形鱼缸,如何减能使鱼缸的容积最大。 二、问题分析 2.1、对于此问题,我采用的数学模型包括三部分,即设计变量、目标函数和约束条件。 模型如下: 其中,设裁去铁块的边长为:x(0 四、程序编写及函数图像 4.1求极值所用程序如下: function q=line_s(a,b) N=10000;r=0.01; a=0;b=1.5; for k=1:N; v=a+0.382*(b-a); u=a+0.618*(b-a); fv=-25*v+20*v^2-4*v^3; fu=-25*u+20*u^2-4*u^3; if fv>fu if b-v<=r u fu break; else a=v;v=u; u=a+0.618*(b-a); end else if u-a<=r v -fv break; else b=u;u=v; v=a+0.382*(b-a); end k=k+1 end end 4.2 函数曲线图程序如下: 如下曲线所得y值为负,前面(1*)已作解释。 x=0:0.1:2.5; y=-25*x+20*x.^2-4*x.^3; plot(x,y); 五、程序调试运行结果 5.1 如图所示: 当k执行5或7或10或12次时,均有x=0.8329时,有最大y=9.2593(函数中已做处理,变负为正,可以对照曲线图)。 极化磁系统参数优化设计 方法的研究 The document was prepared on January 2, 2021 极化磁系统参数优化设计方法的研究 摘要:永磁继电器是一种在国防军事、现代通信、工业自动化、电力系统继电保护等领域中应用面很广的电子元器件,其极化磁系统的参数优化设计是实现永磁继电器产品可靠性设计的前提工作之一。该文采用六因素三水平多目标的正交试验设计方法,分析并研究了极化磁系统的参数优化设计方法。在永磁继电器产品设计满足输出特性指标要求的前提下,给出了输出特性值受加工工艺分散性影响而波动最小的最佳参数水平组合。 1 引言 具有极化磁系统的永磁继电器具有体积小、重量轻、功耗低、灵敏度高、动作速度快等一系列优点,是被广泛应用于航空航天、军舰船舶、现代通信、工业自动化、电力系统继电保护等领域中的主要电子元器件。吸力特性与反力特性的配合技术是电磁继电器产品可靠性设计的关键技术。在机械反力特性及电磁结构已知的情况下,如何对电磁系统进行参数优化设计,使得在保证输出特性值满足稳定性要求的前提下,电磁系统的成本最低,这是继电器可靠性设计必不可少的前提工作之一。 由于极化磁路的非线性及漏磁的影响,使极化磁系统的输出特性值(吸力值)与磁系统各参数水平组合之间存在着非线性函数关系。在各种干扰影响下,各参数存在一定的波动范围。当各参数取不同的水平组合时,参数本身波动所引起的输出特性值的波动亦不相同。由于非线性效应,必定存在一组最优水平组合,使得各参数波动所造成的输出特性值的波动最小,即输出特性的一致性最好。极化磁系统参数优化设计的目的就是要找到各参数的最优水平组合(即方案择优),使得质量输出特性尽可能不受各种干扰的影响,稳定性最好。 影响永磁继电器产品质量使其特性发生波动的主要干扰因素有:①内干扰(内噪声),是不可控因素,如触点磨损、老化等;②外干扰(外噪声),亦是不可控因素,如环境温度、湿度、振动、冲击、加速度等;③可控因素(设计变量)加工工艺的分散性等。其中前两种因素均与产品实际使用环境有关,这里暂不予考虑,本研究只考虑后者对产品质量特性波动的影响。 正交试验设计法是实现参数优化设计的重要手段之一,以往人们在集成电路制造工艺、电火花成型加工工艺、轴承故障诊断等方面得到了很好应用[1-4],但大多是采用单一目标函数的正交试验设计。文献[2]应用正交试验设计法对永磁继电器磁钢尺寸进行了参数优化设计,但没有采用正交试验设计法对永磁继电 题目:机械零件的可靠性优化设计 课程名称:现代设计理论与方法 机械零件 自从出现机械,就有了相应的机械零件。随着机械工业的发展,新的设计理论和方法、新材料、新工艺的出现,机械零件进入了新的发展阶段。有限元法、断裂力学、弹性流体动压润滑、优化设计、可靠性设计、计算机辅助设计(CAD)、系统分析和设计方法学等理论,已逐渐用于机械零件的研究和设计。更好地实现多种学科的综合,实现宏观与微观相结合,探求新的原理和结构,更多地采用动态设计和精确设计,更有效地利用电子计算机,进一步发展设计理论和方法,是这一学科发展的重要趋向。 机械零件是指直接加工而不经过装配的机器组成单元。机械零件是机械产品或系统的基础,机械产品由若干零件和部件组成。按照零件的应用范围,可将零件分为通用零件和专用零件二类。通用的机械零件包括齿轮、弹簧、轴、滚动轴承、滑动轴承、联轴器、离合器等。 机械零件设计就是确定零件的材料、结构和尺寸参数,使零件满足有关设计和性能方面的要求。机械零件除一般要满足强度、刚度、寿命、稳定性、公差等级等方面的设计性能要求,还要满足材料成本、加工费用等方面的经济性要求。 机械零件优化设计概述 进行机械零件的设计,一般需要确定零件的计算载荷、计算准则及零件尺寸参数。零件计算载荷和计算准则的确定,应当依据机械产品的总体设计方案对零件的工作要求进行载荷等方面的详细分析,在此基础上建立零件的力学模型,考虑影响载荷的各项因素和必要的安全系数,确定零件的计算载荷;对零件工作过程可能出现的失效形式进行分析,确定零件设计或校核计算准则。零件材料和参数的确定,应当依据零件的工作性质和要求,选准适合于零件工作状况的材料;分析零件的应力或变形,根据有关计算准则,计算确定零件的主要尺寸参数,并进行参数的标准化。 所谓机械零件优化设计是将零件设计问题描述为数学优化模型,采用优化方法求解一组零件设计参数。机械零件设计中包含了许多优化问题,例如零件设计方案的优选问题、零件尺寸参数优化问题、零件设计性能优化问题等。国内机械设计领域技术人员针对齿轮、弹簧、滚动轴承、滑动轴承、联轴器、离合器等零件优化设计问题开展了大量的工作,解决了齿轮传动比优化分配、各种齿轮参数优化、各种齿轮减速器优化设计、各种齿轮传动的可靠性优化、齿轮传动和减速 零件的参数设计 摘要: 本题目对零件的参数这一问题,综合考虑重新设计零件的参数(包括标定值和容差),并与原设计进行比较,得出最优化的数学模型,并对模型进行求解,最后用计算机模拟对模型的最优解进行检验。由题意知粒子分离器的参数y 由零件参数1234567,,,,,,x x x x x x x 的参数决定,参数i x 的容差等级决定了产品的成本,y 偏离0y 的值决定了产品的损失,问题就是寻找零件的最优标定值和最优等级搭配,使得批量生产时的总费用最少。 一、 问题的重述: 一件产品由若干零件组装而成,标志产品性能的某个参数取决于这些零件的参数。零件参数包括 标定值和容差两部分。进行成批生产时,标定值表示一批零件该参数的平均值,容差则给出了参数偏离其标定值的容许范围。若将零件参数视为随机变量,则标定值代表期望值,在生产部门无特殊要求时,容差通常规定为均方差的3倍。 进行零件参数设计,就是要确定其标定值和容差。这时要考虑两方面因素:一是当各零件组装成产品时,如果产品参数偏离预先设定的目标值,就会造成质量损失,偏离越大,损失越大;二是零件容差的大小决定了其制造成本,容差设计得越小,成本越高。 试通过如下的具体问题给出一般的零件参数设计方法。 粒子分离器某参数(记作y )由7个零件的参数(记作x 1,x 2,...,x 7)决定,经验公式为: 7616 .1242 3 56 .02485.01235136.0162.2142.174x x x x x x x x x x x Y ??? ? ????? ? ????? ??? ??--???? ? ??-????? ???=- y 的目标值(记作0y )为1.50。当y 偏离0y ±0.1时,产品为次品,质量损失为1,000元;当y 偏离0y ±0.3时,产品为废品,损失为9,000元。 零件参数的标定值有一定的容许范围;容差分为A、B、C三个等级,用与标定值的相对值表示,A等为±1%,B等为±5%,C等为±10%。7个零件参数标定值的容许范围,及不同容差等级零件的成本(元)如下表(符号/表示无此等级零件): 汽车理论Project 第一章汽车动力性与燃油经济性数学模型立 1.汽车动力性与燃油经济性的评价指标 1.1 汽车动力性评价 汽车的动力性是指汽车在良好路面上直线行驶时由汽车受到的纵向外力决定的、所能达到的平均行驶速度。汽车的动力性主要可由以下三方面的指标来评定: (1)最高车速:最高车速是指在水平良好的路面(混凝土或沥青)上汽车能达到的最高行驶速度。它仅仅反映汽车本身具有的极限能力,并不反映汽车实际行驶中的平均车速。 (2)加速能力:汽车的加速能力通过加速时间表示,它对平均行驶车速有着很大影响,特别是轿车,对加速时间更为重视。当今汽车界通常用原地起步加速时间与超车加速时间来表明汽车的加速能力。原地起步加速时间是指汽车由第I挡或第II挡起步,并以最大的加速强度(包括选择适当的换挡时机)逐步换至最高挡后达到某一预定的距离或车速所需要的时间。超车加速时间是指用最高挡或次高挡内某一较低车速全力加速至某一高速所需要的时间。 (3)爬坡能力:汽车的爬坡能力是指汽车满载时用变速器最低挡 在良好路面上能爬上的最大道路爬坡度。 1.2 汽车燃油经济性评价 汽车的燃油经济性是指在保证汽车动力性能的前提下,以尽量少的燃油消耗量行驶的能力。汽车的燃油经济性主要评价指标有以下两方面: (1)等速行驶百公里燃油消耗量:它指汽车在一定载荷(我国标准规定轿车为半载、货车为满载)下,以最高挡在良好水平路面上等速行驶100km的燃油消耗量。行驶的燃油消耗量。 (2)多工况循环行驶百公里燃油消耗量:由于等速行驶工况并不能全面反映汽车的实际运行情况。汽车在行驶时,除了用不同的速度作等速行驶外,还会在不同情况下出现加速、减速和怠速停车等工况,特别是在市区行驶时,上述行驶工况会出现得更加频繁。因此各国都制定了一些符合国情的循环行驶工况试验标准来模拟实际汽车运行 状况,并以百公里燃油消耗量来评价相应行驶工况的燃油经济性。1.3 汽车动力性与燃油经济性的综合评价 由内燃机理论和汽车理论可知,现有的汽车动力性和燃油经济性指标是相互矛盾的,因为动力性好,特别是汽车加速度和爬坡性能好,一般要求汽车稳定行驶的后备功率大;但是对于燃油经济性来说,后备功率增大,必然降低发动机的负荷率,从而使燃油经济性变差。从汽车使用要求来看,既不可脱离汽车燃油经济性来孤立地追求动力性,也不能脱离动力性来孤立地追求燃油经济性,最佳地设计方案是在汽车的动力性与燃料经济性之间取得最佳折中。目前,在进行动力 零件参数设计 例8.5 (零件参数设计) 一件产品由若干零件组装而成,标志产品性能的某个参数取决于这些零件的参数。零件参数包括标定值和容差两部分。进行成批生产时,标定值表示一批零件该参数的平均值,容差则给出了参数偏离其标定值的容许范围。若将零件参数视为随机变量,则标定值代表期望值,在生产部门无特殊要求时,容差通常规定为均方差的3 倍。 粒子分离器某参数(记作y )由7个零件的参数(记作7 2 1 ,,,x x x ?)决定, 经验公式为 7 616 .1242 356 .024 85.012 35136.0162.2142.174x x x x x x x x x x x y ??? ? ????? ???????? ? ??--????? ??-???? ??=- 当各零件组装成产品时,如果产品参数偏离预先设定的目标值,就会造成质量损失,偏离越大,损失越大。y 的目标值(记作0 y )为1.50.当 y 偏离1.00 ±y 时, 产品为次品, 质量损失为1000(元); 当y 偏离3 .00 ±y 时,产品为废品,损失为9000(元). 问题是要求对于给定的零件参数标定值和容差,计算产品的损失,从而在此基础上进行零件参数最优化设计。 表8.2给定引例中某设计方案7个零件参数标定值及容差。 容差分为A ﹑B ﹑C 三个等级, 用与标定值的相对值表示, A 等为%1±, B 等为%5±, C 等为%15±。求每件产品的平均损失。 表8.2 零件参数标定值及容差 解:在这个问题中,主要的困难是产品的参数值y是一个随机变 量,而由于y与各零件参数间是一个复杂的函数关系,无法解析的得到y的概率分布。我们采用随机模拟的方法计算。这一方法的思路其实很简单:用计算机模拟工厂生产大量"产品"(如10000件),计算产品的总损失,从而得到每件产品的平均损失。可以假设7个零件参数服从正态分布。根据表8.2及标定值和容差的定义,x1~N(0.1, (0.005/3)2), x 2~N(0.3,0.0052), x 3~N(0.1, (0.005/3)2), x4~N(0.1,0.0052), x5~N(1.5,(0.225/3)2), x6~N(16,(0.8/3)2), x ~N(0.75,(0.0375/3)2), 下面的M脚本eg8_5.m产生1000对零件参数7 随机数,通过随机模拟法求得近似解约f=2900元。 %M文件eg8_5.m clear;mu=[.1 .3 .1 .1 1.5 16 .75]; sigma=[.005/3,.005,.005/3,.005,.225/3,.8/3,.0375/3]; for i=1:7 x(:,i)=normrnd(mu(i),sigma(i),1000,1); 数学建模零件参数的优 化设计 Company number【1089WT-1898YT-1W8CB-9UUT-92108】 零件参数的优化设计 摘要 本文建立了一个非线性多变量优化模型。已知粒子分离器的参数y由零件 参数)7 2,1 ( = i x i 决定,参数 i x的容差等级决定了产品的成本。总费用就包括y 偏离y 造成的损失和零件成本。问题是要寻找零件的标定值和容差等级的最佳搭配,使得批量生产中总费用最小。我们将问题的解决分成了两个步骤:1.预先给定容差等级组合,在确定容差等级的情况下,寻找最佳标定值。2.采用穷举法遍历所有容差等级组合,寻找最佳组合,使得在某个标定值下,总费用最小。在第二步中,由于容差等级组合固定为108种,所以只要在第一步的基础上,遍历所有容差等级组合即可。但是,这就要求,在第一步的求解中,需要一个最佳的模型使得求解效率尽可能的要高,只有这样才能尽量节省计算时间。经过对模型以及matlab代码的综合优化,最终程序运行时间仅为秒。最终计算出的各个零件的标定值为: i x={,,,,,,}, 等级为:B B C C B B B d, , , , , , = 一台粒子分离器的总费用为:元 与原结果相比较,总费用由(元/个)降低到(元/个),降幅为%,结果是令人满意的。 为了检验结果的正确性,我们用计算机产生随机数的方式对模型的最优解进行模拟检验,模拟结果与模型求解的结果基本吻合。最后,我们还对模型进行了误差分析,给出了改进方向,使得模型更容易推广。 关键字:零件参数 非线性规划 期望 方差 一、问题重述 一件产品由若干零件组装而成,标志产品性能的某个参数取决于这些零件的参数。零件参数包括标定值和容差两部分。进行成批生产时,标定值表示一批零件该参数的平均值,容差则给出了参数偏离其标定值的容许范围。若将零件参数视为随机变量,则标定值代表期望值,在生产部门无特殊要求时,容差通常规定为均方差的3倍。 进行零件参数设计,就是要确定其标定值和容差。这时要考虑两方面因素:一是当各零件组装成产品时,如果产品参数偏离预先设定的目标值,就会造成质量损失,偏离越大,损失越大;二是零件容差的大小决定了其制造成本,容差设计得越小,成本越高。 试通过如下的具体问题给出一般的零件参数设计方法。 粒子分离器某参数(记作y )由7个零件的参数(记作x 1,x 2,...,x 7)决定,经验公式为: y 的目标值(记作y 0)为。当y 偏离y 0+时,产品为次品,质量损失为1,000元;当y 偏离y 0+时,产品为废品,损失为9,000元。 零件参数的标定值有一定的容许范围;容差分为A、B、C三个等级,用与标定值的相对值表示,A等为+1%,B等为+5%,C等为+10%。7个零件参数标定值的容许范围,及不同容差等级零件的成本(元)如下表(符号/表示无此等级零件): 工业中截断切割的优化设计 一摘要 本文讨论了加工业中截断切割的优化排序策略我们对于不同的切割 方式总数用穷举法得到720 种所可行解及其费用并对于原问题建立了决策 并对所给出的算法进行了分析和检验 1.当e=0时我归纳出解决问题的最优法则, 从而提出了将面间距统一成判断权重来作为排 序准则的算法,同时证明 了e = 0 的情况下根据这种最优准则能够实现题目所要求的优化目标 2.对于e 1 0 时我们提出了实用准则 最后我结合实际问题将本问题进行了拓展讨论了当最终产品(成品) 在毛坯(待加工长方体)中位置不预定时应如何实施加工方案以达到节省费用 和节约资源的目的,使我们的方案适用于更为广阔的领域 二问题的重述、 在工业生产中,常需要采取将物理一分为二的截断切割方式从一块长方体材料中切出一个小长方体,其加工费用取决于水平切割和垂直切割的截面面积,以及调整刀具时的额外费用。对本题所给出的问题我们首先面临的对加工次序的排序策略然后我们考虑当毛坯和产品位置不预定的时候如何采取策略以达到我们的优化目的 问题: 1> 需考虑的不同切割方式的总数。 2> 给出上述问题的数学模型和求解方法。 3> 试对某部门用的如下准则做出评价,每次选择一个加工费用最少的切割面进行切割。 4> 对于e=0 的情况有无简明的优化准则。 5> 用以下实例验证你的方法: 待加工长方体和成品长方体的长,宽,高分别为10,14.5,19 和3,2,4,两者左侧面,正面,底面之间的距离分别为6,7,5(单位为厘米,垂直切割费用为每平方厘米1 元,r 和e 的数据有 4 组: 1) r=1,e=0; 2) r=1.5,e=0; 3) r=8,e=0; 4) r=1.5, 2 £ e £15 ; 三模型的假设和符号说明 1 切割刀具为两个一个水平放置一个为垂直放置 2 目标长方体所在位置不与毛坯任一表面重合 3 水平方向只需平行移动水平刀具垂直方向只平行移动或调整后再平行 移动刀具因此调整费用e 是否付出仅取决于先后两次垂直切割是否平行而 不记是否穿插着水平切割 4毛坯与工作台接触的底面是事先指定的 案例16 停车场的优化设计 随着城市车辆的增加,停车位的需求量也越来越大,停车困难已逐渐成为市民们头疼的问题。要解决停车难问题,除了尽可能的增加停车场以外,对停车场进行优化设计也能在一定程度上缓解这一供需矛盾。停车场的优化设计就是在停车场大小确定的情况下,对停车区域进行优化设计,以便容纳更多的车辆。本文的目的就是希望分析一下这一情况,找出缓解停车困难的有效办法。 假设某公共场所附近有一块空地,如果不考虑建设地下或多层结构,我们该如何有效的设计停车位置呢?一般来说,想尽可能的把车塞进停车场,最好的办法就是以垂直停靠的方式将车一辆挤一辆地排成行,但是这样停放的后果就是车辆不能自由出入,只有后进入的车辆全部先出去了,先进入的车才可以离开停车场,显然不符合实际的需求。因而,为了使汽车能够自由地出入停车场,必须设立一定数量具有足够宽度的通道,并且每个通道都应该有足够大的“转弯半径”, 而通道越宽越多,就会使得容纳的车辆数越少。所以我们的问题就是要确定在满足车辆能够自由进出的实际需求下,如何进行停车位置和车行通道的设计,才能够停放更多的车辆,从而做到既方便停车又能获得最大的经济效益。 我们先来看看生活中非货运车辆大小的种类。根据实际调查和经验数据,这类车辆一般可分为小轿车,中型客车和大型客车三类。其中小轿车约占九成,大型客车约占一成,而中型客车一般不多于1%。根据这样的情况,我们可以免去对中型客车的车位设计,即便有中型客车停车的需要,可以使用大型车的车位,这也符合现实生活中绝大多数停车场的车位设计情况。我们设小轿车所占的比例为0.9α=,大型客车所占的比例为10.1α-=,当然现实中也有不少全为小轿车设计的停车场,例如小区的地下车库。 再来看看车位的大小。根据实际的调查,城市内比较普通的小轿车长度一般不超过4.7米,宽度一般不超过1.7米,而一般大型客车长度不超过12米,宽度不超过2.2米。另外,经实际考察可知,停车场中标志线的宽度大约为0.1米,所以我们可以假设停车场中停放轿车需要的车位长5L C =米,宽 2.5W C =米,这其中包括了0.1米的标志线宽度和至少0.3米的汽车间的横向间距。设停放大客车需要长12.5L B =米,宽3W B =米,其中包括0.1米的标志线宽度和必要的汽 A题零件的参数设计 摘要 零件的参数设计是工业生产中经常遇到的一个问题。本文通过题中具体例子给出一般零件参数设计的原则与方法。 模型一:蒙特卡罗模型。在确定各个参数标定值与容差的情况下,利用蒙特卡罗方法,尽可能模拟真实零件的生产状况。根据各个参数的分布,每个零件随机产生1000个实际值,代入公式算出每一个产品的Y值,根据其与目标值的关 系判断损失费用。运用MATLAB算出总费用= Q314.57万元 模型二:概率模型。此问题是一个关于概率的非线性规划模型。首先,将产 x的复杂的函数关系式运用泰勒级数展开成线性函数。一品参数Y关于零件参数 i x概率密度的情况下,易求出Y的概率密度,进而求出次品及废品方面,在已知 i 的概率。另一方面,本文引入选择矩阵与等级矩阵,统一零件损失费用,而不需讨论108种分配情况。以工厂损失总费用最小为目标,建立关于积分方程的非线性规划模型。并用lingo编程得到表1-1的结果: 表1-1 算出总费用为:128 = Q万元。节省的总费用为274.442万元。 40 . 由上述例题概括出参数设计的一般方法: S1:在误差范围内,线性化产品参数关于零件参数的函数(可运用泰勒公式); S2:确定产品参数的密度函数; S3:计算不同等级产品出现的概率; S4:确定产品的质量损失费用函数(可利用期望求解); S5:设计零件成本矩阵,计算总成本函数; S6:确保总费用最小,求解零件参数的组合(可运用非线性规划求解)。 关键词:蒙特卡罗、泰勒公式、非线性规划、正态分布、0-1变量 一、 问题重述 1、背景知识 机械零件作为组成机械和机器的不可拆分的基本单元,在制造业中至关重要。机械零件是从机械构造学和力学分离出来的。随着机械工业的发展,新的设计理论和方法、新材料、新工艺的出现,机械零件进入了新的发展阶段。对零件也有了更加严格的要求。有限元法、断裂力学、弹性流体动压润滑、优化设计、可靠性设计、计算机辅助设计(CAD )、实体建模(Pro 、Ug 、Solidworks 等)、系统分析和设计方法学等理论,已逐渐用于机械零件的研究和设计。更好地实现多种学科的综合,实现宏观与微观相结合,探求新的原理和结构,更多地采用动态设计和精确设计,更有效地利用电子计算机,才能进一步发展设计理论和方法。 2、问题重述 一件产品由若干零件组装而成,标志产品性能的某个参数取决于这些零件的参数。零件参数包括标定值和容差两部分。进行成批生产时,标定值表示一批零件该参数的平均值,容差则给出了参数偏离其标定值的容许范围。若将零件参数视为随机变量,则标定值代表期望值,在生产部门无特殊要求时,容差通常规定为均方差的3倍。 零件参数的设计,就是要确定其标定值和容差。这时要考虑两方面因素: 一是当各零件组装成产品时,如果产品参数偏离预先设定的目标值,就会造成质量损失,偏离越大,损失越大; 二是零件容差的大小决定了其制造成本,容差设计得越小,成本越高。 粒子分离器某参数(记作y )由7个零件的参数(记作x 1,x 2,...,x 7)决定,经验公式为: 7616 .124 2 3 56 .02485 .012 35136.0162.2142.174x x x x x x x x x x x Y ??? ? ????? ? ???????? ??--????? ??-????? ???=- y 的目标值(记作y 0)为1.50。当y 偏离y 0±0.1时,产品为次品,质量损失为1,000元;当y 偏离y 0±0.3时,产品为废品,损失为9,000元。 零件参数的标定值有一定的容许范围;容差分为A、B、C三个等级,用与标定值的相对值表示,A等为+1%,B等为+5%,C等为+10%。7个零件参数标定值的容许范围,及不同容差等级零件的成本(元)如下表(符号/表示无此等级零件) 景德镇陶瓷学院 第四组 钟哲卢彧文吴俊杰 粒子分离器零件参数设计的计算机仿真模型 摘要 本文建立起模型对离子分离器参数优化问题进行讨论。参照与原始的标定值选择区间,用lingo进行求解计算的到最佳标定值为[0.075 0.2993 0.075 0.125 1.125 12 0.5812]。然后需要对7个零件的加工等级进行讨论,综合考虑零件加工成本和由零件误差导致的离子分离器的质量损失与废品损失。 利用计算机仿真的优势,对粒子分离器参数设计进行计算机仿真模拟,并用计算机统计出20次(每次1000个零件)的仿真结果,从结果中找出统计规律来确定粒子分离器的参数选择,得到了【B B B C C B B】的零件容差等级选择方案。 使用该方案得到的平均总费用为495182元,而平均最小损失费用为220182 。并通过计算求得原始方案费用,总费用共减少了4391818元,可以得出结论:使用所得方案可获得较大的效益。 最后分析了模型的优缺点,并对模型进行了一定范围的推广,为其他同类问题提供相似的解决方案。 关键词:计算机仿真计算机统计统计规律 一、问题的重述 一件产品通常由若干零件组装而成,这些零件的参数决定着标志产品性能的某个 参数,进而影响到产品的合格率,产品的合格率低将会给企业造成一定的经济损失。零件参数包括标定值(即设计值)和容差(即最大允许误差)两部分,标定值有一定的容许变化范围:容差一般以相对于标定值的误差表示,分为若干个等级,零件参数的容差越小,则组装的产品的质量越高,即质量损失越小,但相应的零件加工成本越高,反之亦然。因此,合理地设计零件参数的标定值和容差等级,是降低生产成本及质量损失,提高企业经济效益的关键。 例如,粒子分离器的性能参数(记作y )由7个零件的参数(记作x 1,x 2……,x 7)决定,经验公式为: y=174.427 616 .1242 /356.024*******.0162.21x x x x x x x x x x x ??? ? ?????? ???? ?? ?? ??--? ? ? ??-???? ???-0.85 y 的目标值(记作y 0)为1.50。当y 偏离y 0±0.1时,产品为次品,质量损失为1,000元;当y 偏离y 0 3.0±时,产品为废品,质量损失为9,000元。各零件参数的标定值范围、容差等级及其相应的加工成本如表1所示: 表1 各零件参数的标定值范围、容差等级及其相应的加工成本 标定值容许范 围 C 等 B 等 A 等 X 1 [0.075,0.125 ] / 25 / X 2 [0.225,0.375 ] 20 50 / X 3 [0.075,0.125 ] 20 50 200 X 4 [0.075,0.125 ] 50 100 500 X 5 [1.125,1.875 ] 50 / / X 6 [12,20] 10 25 100 X 7 [0.5625,0.93 5] / 25 100 现批量生产粒子分离器,每批1000个,在原设计中,7个零件参数的标定值为:x 1=0.1,x 2=0.3,x 3=0.1,x 4=0.1,x 5=1.5,x 6=16,..x 7=0.75;容差均取最便宜的等级。 现在问题是: 1、综合考虑y 偏离的y 0造成的损失和零件成本,为该粒子分离器设计出合理的零件参数,与原设计比较总费用降低了多少。 2、给出了一般产品的零件参数设计方法。 第2章 优化设计的数学模型及基本要素 Chapter 2 Mathematical Modeling for Optimization 2-1 数学模型的建立 (mathematical modeling) 建立数学模型,就是把实际问题按照一定的格式转换成数学表达式的过程。数学模型建立的合适、正确与否,直接影响到优化设计的最终结果。 建立数学模型,通常是根据设计要求,应用相关基础和专业知识,建立若干个相应的数学表达式。如机械结构的优化设计,主要是根据力学、机械设计基础等专业基础知识及机械设备等专业知识来建立数学模型的。 当然,要建立能够反映客观实际的、比较准确的数学模型并非容易之事。数学模型建的过于复杂,涉及的因素太多,数学求解时可能会遇到困难;而建的太简单,又不接近实际情况,解出来也无多大意义。因此,建立数学模型的原则:抓主要矛盾,尽量使问题合理简化。Principle :The problem is simplified as much as possible. 由于设计对象千变万化,即使对同一个问题,由于看问题的角度不同,数学模型建的可能也不一样。建立数学模型不可能遵循一个不变的规则,本课也不准备把大量的时间花在数学模型的建立上。仅想以几个例子来演示一下数学模型的建立过程,使学生从中得到一些启发。 Exp. 2-1 例2-1 用宽度为cm 24,长度cm 100的薄 铁皮做成cm 100长的梯形槽,确定折边的尺寸 x 和折角θ(如图 2-1所示) ,使槽的容积最大。 解: 由于槽的长度就是板的长度,槽的梯形 截面积最大就意味着其容积最大。因此,该问题 就由,求体积最大变成求截面积最大。槽的梯形 截面积为: 图 2-1 ?= 2 1S 高 ?(上底边+下底边) 其中,上底边=x 224-;下底边=θcos 2224x x +-;高=θsin x 定义:该优化设计问题的目标函数是槽的梯形截面积S ,设计变量为θ,x 。问题可以简单地归结为:选择适当的设计变量θ,x ,在一定的限制条件下,使目标函数S 达到最大,限制条件为: 120,20<<< 零件参数的优化设计 摘要 本文建立了一个非线性多变量优化模型。已知粒子分离器的参数y由零件参数 )7 2,1 ( i x i 决定,参数 i x的容差等级决定了产品的成本。总费用就包括y偏离y0造 成的损失和零件成本。问题是要寻找零件的标定值和容差等级的最佳搭配,使得批量生产中总费用最小。我们将问题的解决分成了两个步骤:1.预先给定容差等级组合,在确定容差等级的情况下,寻找最佳标定值。2.采用穷举法遍历所有容差等级组合,寻找最佳组合,使得在某个标定值下,总费用最小。在第二步中,由于容差等级组合固定为108种,所以只要在第一步的基础上,遍历所有容差等级组合即可。但是,这就要求,在第一步的求解中,需要一个最佳的模型使得求解效率尽可能的要高,只有这样才能尽量节省计算时间。经过对模型以及matlab代码的综合优化,最终程序运行时间仅为秒。最终计算出的各个零件的标定值为: i x={,,,,,,}, 等级为:B B C C B B B d, , , , , , 一台粒子分离器的总费用为:元 与原结果相比较,总费用由(元/个)降低到(元/个),降幅为%,结果是令人满意的。 为了检验结果的正确性,我们用计算机产生随机数的方式对模型的最优解进行模拟检验,模拟结果与模型求解的结果基本吻合。最后,我们还对模型进行了误差分析,给出了改进方向,使得模型更容易推广。 关键字:零件参数非线性规划期望方差 一、问题重述 一件产品由若干零件组装而成,标志产品性能的某个参数取决于这些零件的参数。 零件参数包括标定值和容差两部分。进行成批生产时,标定值表示一批零件该参数的 平均值,容差则给出了参数偏离其标定值的容许范围。若将零件参数视为随机变量, 则标定值代表期望值,在生产部门无特殊要求时,容差通常规定为均方差的3倍。 进行零件参数设计,就是要确定其标定值和容差。这时要考虑两方面因素:一是 当各零件组装成产品时,如果产品参数偏离预先设定的目标值,就会造成质量损失,实验六PID控制系统参数优化设计
数学建模_零件参数的优化设计说明
零件参数设计matlab程序(数学建模)
ADAMS VIEW 参数化和优化设计实例详解
优化设计数学建模
极化磁系统参数优化设计方法的研究
机械零件的可靠性优化设计
数模-零件的参数设计
汽车动力传动系参数优化设计
数学建模竞赛-零件参数设计
数学建模零件参数的优化设计
数学建模截断切割的优化设计
数学建模案例_停车场的优化设计(1)
零件的参数设计-论文
零件的优化设计
优化设计的数学模型及基本要素
数学建模零件参数的优化设计