铝合金压铸件一般技术要求
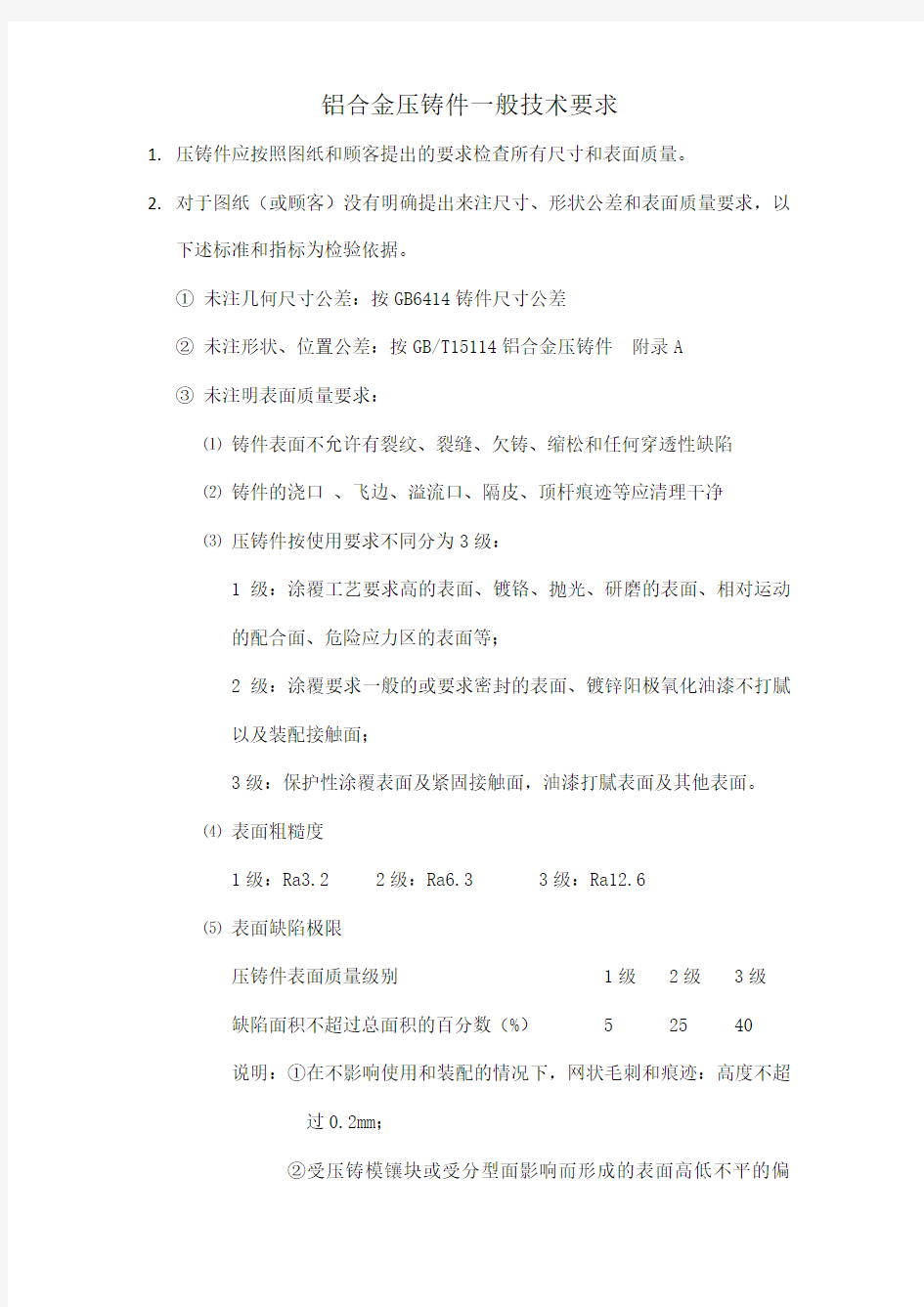
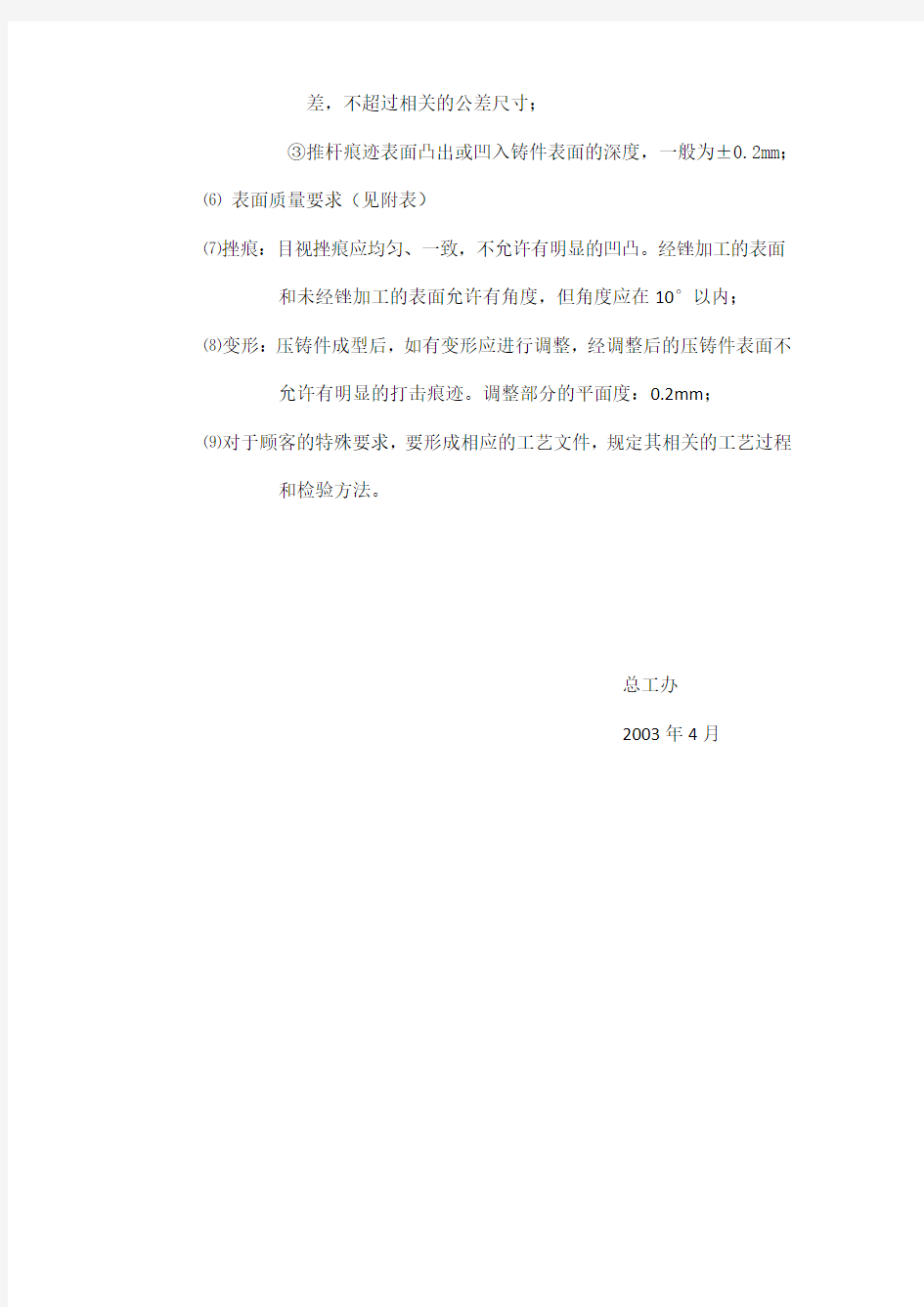
铝合金压铸件一般技术要求
1.压铸件应按照图纸和顾客提出的要求检查所有尺寸和表面质量。
2.对于图纸(或顾客)没有明确提出来注尺寸、形状公差和表面质量要求,以
下述标准和指标为检验依据。
①未注几何尺寸公差:按GB6414铸件尺寸公差
②未注形状、位置公差:按GB/T15114铝合金压铸件 附录A
③未注明表面质量要求:
⑴铸件表面不允许有裂纹、裂缝、欠铸、缩松和任何穿透性缺陷
⑵铸件的浇口 、飞边、溢流口、隔皮、顶杆痕迹等应清理干净
⑶压铸件按使用要求不同分为3级:
1级:涂覆工艺要求高的表面、镀铬、抛光、研磨的表面、相对运动
的配合面、危险应力区的表面等;
2级:涂覆要求一般的或要求密封的表面、镀锌阳极氧化油漆不打腻
以及装配接触面;
3级:保护性涂覆表面及紧固接触面,油漆打腻表面及其他表面。
⑷表面粗糙度
1级:Ra3.2 2级:Ra6.3 3级:Ra12.6
⑸表面缺陷极限
压铸件表面质量级别 1级 2级 3级
缺陷面积不超过总面积的百分数(%) 5 25 40
说明:①在不影响使用和装配的情况下,网状毛刺和痕迹:高度不超过0.2mm;
②受压铸模镶块或受分型面影响而形成的表面高低不平的偏
差,不超过相关的公差尺寸;
③推杆痕迹表面凸出或凹入铸件表面的深度,一般为±0.2mm;
⑹表面质量要求(见附表)
⑺挫痕:目视挫痕应均匀、一致,不允许有明显的凹凸。经锉加工的表面
和未经锉加工的表面允许有角度,但角度应在10°以内;
⑻变形:压铸件成型后,如有变形应进行调整,经调整后的压铸件表面不
允许有明显的打击痕迹。调整部分的平面度:0.2mm;
⑼对于顾客的特殊要求,要形成相应的工艺文件,规定其相关的工艺过程
和检验方法。
总工办
2003年4月
附表: 缺陷名称 缺陷范围
表面质量级别 备注 1级
2级 3级 流痕
深度(mm )≤ 0.05 0.07 0.15 面积不超过总面积的百分数
5
15 30
冷隔
深度(mm )≤ 不允许
1/5壁厚 1/4壁厚 1. 在同一部
分对应出不允许同时存在 2. 长度是指
缺陷流向的展开长度
长度不大于铸件的最大轮廓尺寸的(mm )
1/10
1/5
所在面上的不允许超过的数量 2处 2处 离铸件边缘距离(mm )≥ 4 4 两冷隔间距(mm )≥
10 10 拉伤
深度(mm )≤ 0.05 0.1 0.25 除一级表面外,浇道部位允许增加一倍 面积不超过总面积的百分数
3 5 10 凹陷 凹入深度(mm ) 0.1
0.3 0.5 粘附物痕迹
整个铸件缺陷不允许超过 不允许
1处 2处 占带缺陷的表面面积的百分比
5 10
气泡平均直径≤3mm
1.每100cm 2缺陷个数不超过 不允许 1 2 允许两种气泡同时存在,但大气泡不超过3个,总数不超过10个。
2.整个铸件缺陷个数不超过 3 7
3.离铸件边缘距离(mm )≤ 3 7
4.气泡凸起高度(mm )≤
0.2 0.3 气泡平均直径>3‐6mm
1.每100cm 2缺陷个数不超过 不允许 1 1 其边距不小于10mm
2.整个铸件缺陷个数不超过 1 3
3.离铸件边缘距离(mm )≤ 5 5
4.气泡凸起高度(mm )≤
0.3 0.5 边角残缺深度
铸件边长≤100mm
0.3 0.5 1.0 残缺长度不超过边长度的5%
铸件边长≥100mm
0.5 0.8 1.2 各类缺陷总和
面积不超过总面积的百分数
5 30
50
铝合金压铸技术要求
1、范围 本标准规定了铝合金压铸件的技术要求、试验方法、检验规则、交货条件等。本标准适用于汽车发电机铝合金端盖压铸件。 2、引用标准 GB6414铸件尺寸公差 GB6987.1-GB6987.16铝及铝合金化学分析方法 GB288-87金属拉力试验法 GB/T13822-92 压铸有色合金试样 GB6060.5 表面粗造度比较样块抛(喷)丸、喷吵加工表面 3、技术要求 3.1 压铸铝合金的牌号 压铸铝合金采用UNS-A03800(美国A380.0,日本ADC10) 可选用材料UNS-A03830 (美国383.0,日本ADC12) 化学成份见表1 表1
供应商可选择上述四种牌号的任何一种,如在生产过程中更换其它牌号,需重新进行样件鉴定。 3.1.1回炉料使用规定 3.1.1.1回炉料分类 一级回炉料:浇道、化学成份合格的废铸件,后加工次品等不含水分和油污。 二级回炉料:集渣包、坩埚底部剩料、退货废品、存放时间长(超过10天)的一级回炉料。 三级回炉料:飞边、溅屑、细小的碎料、带有油污的渣料、因化学成份报废的铸件、从铝渣中捡出的铝粒。 3.1.1.2回炉料使用比例 使用单一某级回炉料: 一级回炉料最大使用量50%,二级回炉料最大使用量40%。 一级、二级回炉料混合使用: 回炉料总量不超过40%,其中二级回炉料最大使用量20%。 三级回炉料: 不能直接使用,必须经过重熔、精炼且化学成份分析合格后才能使用,其最大使用量10%,仅与铝锭混合使用。 3.1.1.3加料循序 小颗粒回炉料大块回炉料铝锭,如此循环。 3.2 力学性能 采用单铸拉力试样检验,其力学性能应满足抗拉强度≥240Mpa,伸长率≥1%,
铝合金压铸技术要求
1、围 本标准规定了铝合金压铸件的技术要求、试验方法、检验规则、交货条件等。 本标准适用于汽车发电机铝合金端盖压铸件。 2、引用标准 GB6414铸件尺寸公差 GB6987.1-GB6987.16铝及铝合金化学分析方法 GB288-87金属拉力试验法 GB/T13822-92 压铸有色合金试样 GB6060.5 表面粗造度比较样块抛(喷)丸、喷吵加工表面 3、技术要求 3.1 压铸铝合金的牌号 压铸铝合金采用UNS-A03800(美国A380.0,日本ADC10) 可选用材料UNS-A03830 (美国383.0,日本ADC12) 化学成份见表1 表1
供应商可选择上述四种牌号的任何一种,如在生产过程中更换其它牌号, 文档Word 需重新进行样件鉴定。回炉料使用规定 3.1.1回炉料分类 3.1.1.1 一级回炉料:浇道、化学成份合格的废铸件,后加工次品等不含水分和 油污。10二级回炉料:集渣包、坩埚底部剩料、退货废品、存放时间长(超过 天)的一级回炉料。三级回炉料:飞边、溅屑、细小的碎料、带有油污的渣料、因化学成份 报废的铸件、从铝渣中捡出的铝粒。 3.1.1.2回炉料使用比例 使用单一某级回炉料:,二级回炉料最大使用量40%。一级回炉料最大使用量50% 一级、二级回炉料混合使用:20%。,其中二级回炉料最
大使用量回炉料总量不超过40% 三级回炉料:必须经过重熔、精炼且化学成份分析合格后才能使用,其最不能直接使用,10%,仅与铝锭混合使用。大使用量 3.1.1.3加料循序 大块回炉料铝锭,如此循环。小颗粒回炉料 3.2 力学性能 采用单铸拉力试样检验,其力学性能应满足抗拉强度≥240Mpa,伸长率≥ 1%,HB85(5/250/30)。 试样尺寸及形状应符合GB/T 13822-92《压铸有色合金试样》的规定。 3.3 压铸件尺寸 压铸件的几何形状和尺寸应符合铸件图的规定。 3.4 待加工表面用符号“”标明,尖头指向被加工面。 例:0.5 表示该表面留有加工余量0.5mm 3.5 表面质量 3.5.1 铸件清理后的表面质量 铸件的浇口、飞边、溢流口、隔皮等应清理干净,但允许留有清理痕迹。在不影响使用的情况下,因去除浇口、溢流口时所形成的缺肉或高出均不得超过壁厚的四分之一,并且不得超过1.5 mm。 文档Word 3.5.2 铸件不加工表面的质量 3.5.2.1 不允许有裂纹,欠铸和任何穿透性缺陷。 3.5.2.2 由于模具组合镶拼或受分型面影响而形成铸件表面高低不平的
铝合金压铸件综合技术条件(拉力)资料
1 主题内容与适用范围 本标准根据GB 1173及GB 9438的相关内容,规定了铝合金铸件的分类和铸件的外观质量、内在质量以及铸件修补等内容的技术要求与检验规则等。 本标准适用于铝硅系合金铸件的砂型铸造、特种铸造(不含压力铸造)。 2 一般规定 2.1 合金牌号 2.1.1 铸造铝合金牌号由铝及主要合金元素的化学成分符号组成。主要合金元素后面跟有表示其名义百分含量的数字(名义百分含量为该元素的平均百分含量的修约化整值)。如果合金化元素的名义百分含量不小于1,该数字用整数表示;如果合金化元素的名义百分含量小于1,一般不标数字,必要时可用一位小数表示。 在合金牌号前面冠以字母“Z”(“铸”字汉语拼音第一个字母)表示属于铸造合金。 2.1.2 若合金化元素多于两个,除对表示合金的本质特性是必不可少的外,不必把所有的合金化元素都列在牌号中。 2.1.3 杂质含量较一般合金低、性能高的优质合金,在其牌号后面附加字母“A”。 2.1.4 在牌号中主要合金化元素按名义百分含量的递减次序排列,当名义百分含量相等时,按其化学符号字母顺序排列。 2.2 合金代号 本标准中合金代号由字母“Z”、“L”(它们分别是“铸”、“铝”的汉语拼音第一个字母)及其后面的三个阿拉伯数字组成。“ZL”后面第一个数字表示合金系列,其中“1”表示铝硅系列合金,第二、三两个数字表示顺序号。 优质合金,在其代号后面附加字母“A”。 引用顾客提供的材料标准时,其代号按原用代号不变。 2.3 合金铸造方法、变质处理代号 S——砂型铸造 J——金属型铸造 R——熔模铸造 K——壳型铸造 B——变质处理 2.4 合金状态代号 F——铸态 T1——人工时效 T2——退火 T4——固溶处理+自然时效 T5——固溶处理+不完全人工时效 T6——固溶处理+完全人工时效 T7——固溶处理+稳定化处理 T8——固溶处理+软化处理 2.5 数字修约规则 合金牌号中合金化元素的名义百分含量、合金化学成分、合金性能等数字修约按GB 1.1中附录C规定。 3 铸件分类 根据工作条件、用途以及在使用过程中如果损坏,所能造成的危害程度,来确定铸件的类别。 3.1 铸件分三类,其定义及检验项目见表1: 表1 铸件分类的定义及检验项目
压铸铝合金
铝合金压铸件中气孔缺陷及压铸技术新发展 摘要:压铸铝合金有良好的使用性能和工艺性能,因此铝合金的压铸发展迅速,在各个工业部门中得到广泛的应用,用量远远高于其他有色合金,在压铸生产中占有极其重要的地位。铝合金压铸生产的工件常因气孔存在而导致报废。产生气孔的原因很多,在解决这一产品质量问题时常常无从下手,如何快速、正确地采取措施减少因气孔而造成的度品率,这是各铝合金压铸厂所关注的问题。 关键词:压铸铝合金;性能;气孔缺陷;精炼处理 1、压铸铝合金的性能及分类 长期以来,在我国由于压铸件本身中总是存在气孔的缺陷,所以它们经常地只是局限于一些装饰零件,受载荷不大的零件制造,故压铸铝合金的牌号发展一直停留在几个型号上。但是,随着生产的发展,压铸技术的掌握,人们在扩大压铸件的应用范围方面提出了更多的要求,如在自行车减轻自重的结构改进中,很重要的措施之一就是用铝合金代替钢材制作自行车的零件。 压铸铝合金除了应满足所制零件的工作性能要求外,为了能顺利地进行压力铸造,它还应具有如下的性能: (1)在过热度不高,甚至处于固、液相线温度范围内时,它应有较好的塑性体流变性能,即在压力作用下,貌似粘稠的铝合金液仍具有优良的流动性,便于填充复杂的型腔,保证良好的压铸件表面质量,减少铸件内的收缩孔洞。同时改善压铸型的工作状况,提高其工作寿命; (2)线收缩率小,并且有一定的高温强度,以免铸件产生裂纹和变形,提高铸件尺寸精度; (3)结晶温度范围小,可以减少铸件中收缩孔洞产生的可能性; (4)具有一定的高温固态强度,防止模具开模时推出铸件产生变形或破裂;(5)在常温下应具有一定的强度,以尽可能提高压铸件的机械强度和表面硬度;(6)与压铸型不发生化学反应,亲和力小,防止粘型和铸件、铸型相互合金化;(7)在高温熔融状态下不易吸气、氧化,以便能满足压铸时需长期保温的要求。 压铸铝合金有良好的使用性能和工艺性能,因此铝合金的压铸发展迅速,在各个工业部门中得到广泛的应用,用量远远高于其他有色合金,在压铸生产中占
铝合金压铸件的标准
铝合金压铸件的标准 2010-01-25 10:08 铝合金压铸件 GB/T 15114-94 1.主题内容与适用范围 本标准规定了铝合金压铸件的技术要求,质量保证,试验方法及检验规则和交货条件等. 本标准适用于铝合金压铸件. 2.引用标准 GB1182 形状和位置公差代号及其标准 GB2828 逐批检查计数抽样程序及抽样表(适用于连续的检查) GB2829 周期检查计数抽样程序及抽样表(适用于生产过程稳定性的检查) GB6060.1 表面粗糙度比较样块铸造表面 GB6060.4 表面粗糙度比较样块抛光加工表面 GB6060.5 表面粗糙度比较样块抛(喷)丸,喷砂加工表面 GB6414 铸件尺寸公差 GB/T11350 铸件机械加工余量 GB/T15115 压铸铝合金 3.技术要求 3.1化学成分 合金的化学成分应符合GB/T15115的规定. 3.2力学性能 3.2.1当采用压铸试样检验时,其力学性能应符合GB/T15115的规定 3.2.2当采用压铸件本体试验时,其指定部位切取度样的力学性能不得低于单铸试样的75%,若有特殊要求,可由供需双方商定. 3.3压铸件尺寸
3.3.1压铸件的几何形状和尺寸应符合铸件图样的规定 3.3.2压铸件尺寸公差应按GB6414的规定执行,有特殊规定和要求时,须在图样上注明. 3.3.3压铸件有形位公差要求时,其标注方法按GB1182的规定. 3.3.4压铸件的尺寸公差不包括铸造斜度,其不加工表面:包容面以小端为基准,有特殊规定和要求时,须在图样上注明. 3.4压铸件需要机械加工时,其加工余量按GB/T11350的规定执行.若有特殊规定和要求时,其加工作量须在图样上注明. 3.5表面质量 3.5.1铸件表面粗糙度应符合GB6060.1的规定 3.5.2铸件不允许有裂纹,欠铸,疏松,气泡和任何穿透性缺陷. 3.5.3铸件不允许有擦伤,凹陷,缺肉和网状毛刺等腰三角形缺陷,但其缺陷的程度和数量应该与供需双方同意的标准相一致. 3.5.4铸件的浇口,飞边,溢流口,隔皮,顶杆痕迹等腰三角形应清理干净,但允许留有痕迹. 3.5.5若图样无特别规定,有关压铸工艺部分的设置,如顶杆位置,分型线的位置,浇口和溢流口的位置等由生产厂自行规定;否则图样上应注明或由供需双方商定. 3.5.6压铸件需要特殊加工的表面,如抛光,喷丸,镀铬,涂覆,阳极氧化,化学氧化等须在图样上注明或由供需双方商定. 3.6内部质量 3.6.1压铸件若能满足其使用要求,则压铸件本质缺陷不作为报废的依据. 3.6.2对压铸件的气压密封性,液压密封性,热处理,高温涂覆,内部缺陷(气孔,疏孔,冷隔,夹杂)及本标准未列项目有要求时,可由供需双方商定. 3.6.3在不影响压铸件使用的条件下,当征得需方同意,供方可以对压铸件进行浸渗和修补(如焊补,变形校整等)处理. 4质量保证 4.1当供需双方合同或协议中有规定时,供方对合同中规定的所有试验或检验负责.合同或协议中无规定时,经需方同意,供方可以用自已适宜的手段执
铝合金压铸件资料
铝合金压铸件资料 ADC-12(相当国内的ZL104)是压铸铝合金牌号,为脆性材料,易崩裂。性质类似铸铁,但有质轻和导热性好的优点。主要用于做高档望远镜外壳,相机三脚架云台,发动机外壳等。具体性能指标,可由铝合金压铸厂提供,或等我查资料后再告知。在广东省南海市有大量生产厂家。 数码相机的铝合金外壳的壁厚多少合理?表面是如何处理的?有没有加工此类产品的厂家?壁厚:1.2~1.5mm,表面:铬酸皮膜后喷涂; 铝合金压铸件的内部裂痕怎样检测? 通过无损探伤来检测产品 1.超声波探伤 各类金属管材、板材、铸件、锻件和焊缝的超声波检测和超声波测厚. 当超声波在传播中遇到裂缝、空洞、离析等缺陷时,超声波的声速、振幅、频率等声学参数会因此改变。根据仪器测量这些改变,可以判断缺陷的存在,并能确定其具体位置. 超声波脉冲(通常为1.5MHz)从探头射人被检测物体,如果其内部有缺陷,缺陷与材料之间便存在界面,则一部分人射的超声波在缺陷处被反射或折射,则原来单方向传播的超声能量有一部分被反射,通过此界面的能量就相应减少。这时,在反射方向可以接到此缺陷处的反射波;在传播方向接收到的超声能量会小于正常值,这两种情况的出现都能证明缺陷的存在。在探伤中,利用探头接收脉冲信号的性能也可检查出缺陷的位置及大小。前者称为反射法,后者称为穿透法。 2.磁粉探伤 适宜于铁磁性材料如铸造、锻造和其它机加工部件的无损检测。 3.紫外线灯 价格低廉、可靠高和操作简单,各种管道的泄漏探查、涂镀层是否均匀的检验、杂质或污点的检测、半导体和生物领域、医疗、舞台特除艺术效果 4.射线探伤 射线探伤可以分为X射线、γ射线和高能射线探伤三种 X射线照相法探伤是利用射线在物质中的衰减规律和对某些物质产生的光化及荧光作用为基础进行探伤的。从射线强度的角度看,当照射在工件上射线强度为J0,由于工件材料对射线的衰减,穿过工件的射线被减弱至Jc。若工件存在缺陷时,因该点的射线透过的工件实际厚度减少,则穿过的射线强度Ja、Jb比没有缺陷的点的射线强度大一些。从射线对底片的光化作用角度看,射线强的部分对底片的光化作用强烈,即感光量大。感光量较大的底片经暗室处理后变得较黑。因此,工件中的缺陷通过射线在底片上产生黑色的影迹,这就是射线探伤照相法的探伤原理。 铝合金压铸件的结构设计经验 1。考虑壁厚的问题,厚度的差距过大会对填充带来影响 2。考虑脱模问题,这点在压铸实际中非常重要,现实中往往回出现这样的问题,这比注塑脱模讨厌多了,所以拔模斜度的设置和动定模脱模力的计算要注意些,一般拔模斜度为1到3度,通常考虑到脱模的顺利性,外拔模要比内拔模的斜度要小些,外拔模也就1度,而内拔模要2~3度左右 3。设计时考虑到模具设计的问题,如果有多个位置的抽心位,尽量的放两边,最好不要放在下位抽心,这样时间长了下抽心会容易出问题 4。有些压铸件外观可能会有特殊的要求,如喷油、喷粉等,这时就要时结构避开重要外观位置便于设置浇口溢流槽5。在结构上尽量的避免出现导致模具结构复杂的结构出现,如,不得不使用多个抽心或螺旋抽心等 6。对于需进行表面加工的零件,注意,需要在零件设计时给适合的加工留量,不能太多,否则加工人员会骂你的,而且会把里面的气孔都暴露出来的,不能太少,否则粗精定位一加工,得,黑皮还没干掉,你就等再在模具上打火花了,那给多少呢,留量最好不要大于0。8mm,这样加工出来的面基本看不到气孔的,因为有硬质层的保护。 7。再有就是注意选料了,是用ADC12还是A380等,要看具体的要求了 8。铝合金没有弹性,要做扣位只有和塑料配合。 9。一般不能做深孔!在开模具时只做点孔,然后在后加工! 10。如果是薄壁零件与不能太薄,而且一定要用加强肋,增加抗弯能力!由于铝铸件的温度要在800摄氏度左右!模具寿命一般比较短一般做如电机外壳的话只有80K左右就再见了!
铝合金压铸件的标准
铝合金压铸件 1 范围 本标准规定了铝合金压铸件(以下简称压铸件)的材质、尺寸公差、角度公差、形位公差、工艺性要求和表面质量。 本标准适用于照相机、光学仪器等产品的铝合金压铸件。 2 规范性引用文件 下列文件中的条款通过本标准的引用而成为本标准的条款。凡是注明日期的引用文件,其随后所有的修改单(不包括勘误的内容)或修订版均不适用于本标准,然而,鼓励根据本标准达成协议的各方研究是否可使用这些文件的最新版本。凡是不注日期的引用文件,其最新版本适用于本标准。 GB/T 6414—1999 铸件尺寸公差与机械加工余量 GB/T 11334—1989 圆锥公差 JIS H 5302—1990 压铸铝合金 3 压铸铝合金 3.1 压铸铝合金选用JIS H 5302—1990中的ADC10。 3.2 ADC10的化学成分表1给出。其中铜的含量控制在不大于2.8 %。 a ) 抗拉强度σ b :245 MPa; b ) 伸长率δ5 :2 %; c ) 布氏硬度HBS(5/250/30):80。 4 铸件尺寸公差 4.1 压铸件尺寸公差的代号、等级及数值 压铸件尺寸公差的代号为CT。尺寸公差等级选用GB/T 6414—1999中的CT3 ~CT8。一般(未注)公差尺寸的公差等级基本规定为:照相机零件按CT6,其他产品零件按CT7。尺寸公差数值表2给出。 4.2 壁厚尺寸公差 壁厚尺寸公差一般比该压铸件的一般公差粗一级。例如:一般公差规定为CT7,壁厚公差则为CT8。
当平均壁厚不大于1.2 mm时,壁厚尺寸公差则与一般公差同级,必要时,壁厚尺寸公差比一般公差精一级。 4.3 公差带的位置 尺寸公差带应相对于基本尺寸对称分布,即尺寸公差的一半为正值,另一半取负值。当有特殊要求时,也可采用非对称设置,此时应在图样上注明或在技术文件中规定。 对于有斜度要求的部位,其尺寸公差应沿斜面对称分布。 单位为毫米 4.4 公差增量和错型值 受分型面及型芯的影响而引起的固定增量和错型值,已包含在尺寸公差数值之内。当需进一步限制错型值时,则应在图样上注明其允许的最大错型值。 4.5 尺寸公差标注 4.5.1 标注公差尺寸采用极限偏差标注尺寸公差(见示例1)。 10+。 示例1: 10±0.18 ,26.010.0 10+-, 36.00 4.5.2 未注公差尺寸采用公差代号标注尺寸公差(见示例2)。当按未注公差基本规定的等级时,允许不作说明。 示例2: 一般公差按GB/T 6414 – CT7 。 4.5.3 当需进一步限制错型值时,应注明其允许的最大错型值(见示例3)。
铝合金压铸技术要求(DOC)
页号:1/8 1、范围 本标准规定了铝合金压铸件的技术要求、试验方法、检验规则、交货条件等。 本标准适用于汽车发电机铝合金端盖压铸件。 2、引用标准 GB6414铸件尺寸公差 GB6987.1-GB6987.16铝及铝合金化学分析方法 GB288-87金属拉力试验法 GB/T13822-92 压铸有色合金试样 GB6060.5 表面粗造度比较样块抛(喷)丸、喷吵加工表面 3、技术要求 3.1 压铸铝合金的牌号 压铸铝合金采用UNS-A03800(美国A380.0,日本ADC10) 可选用材料UNS-A03830 (美国383.0,日本ADC12) 化学成份见表1 表1
页号:2/8 供应商可选择上述四种牌号的任何一种,如在生产过程中更换其它牌号,需重新进行样件鉴定。 3.1.1回炉料使用规定 3.1.1.1回炉料分类 一级回炉料:浇道、化学成份合格的废铸件,后加工次品等不含水分和油污。 二级回炉料:集渣包、坩埚底部剩料、退货废品、存放时间长(超过10天)的一级回炉料。 三级回炉料:飞边、溅屑、细小的碎料、带有油污的渣料、因化学成份报废的铸件、从铝渣中捡出的铝粒。 3.1.1.2回炉料使用比例 使用单一某级回炉料: 一级回炉料最大使用量50%,二级回炉料最大使用量40%。 一级、二级回炉料混合使用: 回炉料总量不超过40%,其中二级回炉料最大使用量20%。 三级回炉料: 不能直接使用,必须经过重熔、精炼且化学成份分析合格后才能使用,其最大使用量10%,仅与铝锭混合使用。
页号:3/8 3.1.1.3加料循序 小颗粒回炉料大块回炉料铝锭,如此循环。 3.2 力学性能 采用单铸拉力试样检验,其力学性能应满足抗拉强度≥240Mpa,伸长率≥1%,HB85(5/250/30)。 试样尺寸及形状应符合GB/T 13822-92《压铸有色合金试样》的规定。 3.3 压铸件尺寸 压铸件的几何形状和尺寸应符合铸件图的规定。 3.4 待加工表面用符号“”标明,尖头指向被加工面。 例:0.5 表示该表面留有加工余量0.5mm 3.5 表面质量 3.5.1 铸件清理后的表面质量 铸件的浇口、飞边、溢流口、隔皮等应清理干净,但允许留有清理痕迹。在不影响使用的情况下,因去除浇口、溢流口时所形成的缺肉或高出均不得超过壁厚的四分之一,并且不得超过1.5 mm。 3.5.2 铸件不加工表面的质量 3.5.2.1 不允许有裂纹,欠铸和任何穿透性缺陷。 3.5.2.2 由于模具组合镶拼或受分型面影响而形成铸件表面高低不平的偏差,不得超过有关尺寸公差。 3.5.2.3 推杆痕迹不得凸起,允许凹入铸件表面,深度不得超过该处壁厚的十分之一,并不超过0.4 mm。
铝合金铸件气孔标准修订稿
铝合金铸件气孔标准 WEIHUA system office room 【WEIHUA 16H-WEIHUA WEIHUA8Q8-
铝合金铸件气孔、针孔检验标准 一. 适用范围 本标准规定了铸件气孔、针孔允许存在的范围、大小、数量等技术要求。本标准规定了铸造铝合金低倍针孔度的分级原则和评级方法。本标准适用于铝合金的砂型铸造。适用于评定铸件外表面及需要加工面经加工后的表面气孔、针孔。 二. 引用标准 GB1173-86铸造铝合金技术条件 GB9438-88铝合金铸件技术条件 GB10851-89铸造铝合金针孔 三. 气孔、针孔等孔洞类特征 1. 位于铸件内部而不延伸到铸件外部的气眼。 (1)气孔、针孔内壁光滑,大小不等的圆形孔眼,单个或成组无规则的分布在铸件的各个部位。 (2)气渣孔其特征同气孔、针孔相似,但伴随有渣子。 2. 表面或近表面的孔眼,大部分暴露或与外表面相连。 (1)表面或皮下气孔大小不等的单个或成组的孔眼,位于铸件表面或近表面的部位,其内壁光滑。
(2)表面针孔铸件表面上细小的孔洞,呈现在较大的区域上。 四. 具体条件 1. 砂型、金属型铸件的非加工表面和加工表面,在清整干净后允许存在下列孔洞: (1) 单个孔洞的最大直径不大于3mm,深度不超过壁厚1/3,在安装边上不超过壁厚的1/4,且不大于1.5mm,在上述缺陷的同一截面的反面对称部位不得有类似的缺陷。 (2)成组孔洞最大直径不大于2mm,深度不超过壁厚的1/3,且不大于 1.5mm。 (3) 上述缺陷的数量及边距应符合表一规定 表一 非加工表面或加工表面总面积小于1000cm2 单个孔洞成组孔洞 在 10cm×10cm 单位面积上 孔洞数不多 于4个 孔洞边 距不小 于10mm 一个铸件的非加 工表面或加工面 上孔洞总数不多 于6个,孔洞边 缘距铸件或距内 孔边缘的距离不 小于孔洞最大直 径的2倍 以 3cm×3cm 单位面积 为一组, 其孔洞数 不多于3 个 在一个铸 件上组的 数量不多 于2组 孔洞边缘 距铸件边 缘或距内 孔边缘的 距离不小 于孔洞最 大直径的 2倍 2.液压、气压件的加工表面上,铸件以3级针孔作为验收基础,要求2级针孔占受检面积的25%以上,局部允许4级针孔,但一般不得超过受检面积的
断桥隔热铝合金门窗技术要求(DOC)
具体要求 断桥隔热铝合金门、窗: (一)、主要性能要求 1、外窗隔声性能满足《建筑外窗隔声性能分级及检测方法》(GB/T8485—2002 三级标准35dB>Rw>30dB 2、外窗保温性能满足《建筑外窗保温性能分级及检测方法》(GB/T7108—2002 二级标准)3.0>k≥2.5 3、外窗空气渗漏性能满足《建筑外窗空气渗漏性能及检测方法》(GB7107-2002 >1.5m3/m.h 三级标准)2.5≥q 1 4、外窗雨水渗透性能满足《建筑外窗雨水渗透性能分级及检测方法》 (GB7108-2002三级标准) 250≤△P<350 5、符合其他国家规定性标准规范。 (二)、对门窗材料的规定 窗传热系数必须满足K≤2.30W/(m2·K),并由投标单位提供门窗计算书以及“五性实验”报告。因整窗传热系数不满足要求而导致的全部问题、责任及费用均全部由投标单位(中标单位)负责。规定门窗配置:型材不小于55系列,要求等温线平缓,温差梯度均匀隔热条选用国产品牌,中空玻璃厚度5mm+9mm+5mm。 一、铝合金型材、玻璃及配件 1、铝合金型材 1.1、铝合金型材的选择应符合下表要求:(型材的断面尺寸指窗框材在墙体上的投影的有效尺寸)
上表中型材壁厚为最低要求,主型材壁厚应经计算或试验确定,投标方须提供典型门窗的设计计算书。 1.2、铝合金门窗全部采用内扣条,扣条采用方扣条,连接处为45°拼缝,手感顺滑,不得有明显错台,并作好防水处理,详见下图: 1.3、铝合金型材表面采用静电粉末喷涂,涂层厚度≥40μm,室外喷涂颜色为:室内喷涂颜色为:正式加工前,中标方须提供色卡经招标方确认。投标方负责要求粉末喷涂厂家向招标方提供10年的品质保证证书,即10年内颜色无明显变化,涂层不脱落。 1.4、根据需要采取有效的防渗漏措施。如:所有门窗下框室内侧翼緣有足够的挡水高度(内外高差宜大于30mm),平开门窗下框应带排水槽(孔),并配备与型材颜色一致或相近的排水孔盖。 1.5、窗开启扇配置隐形纱窗(导轨铝合金型材壁厚不小于1.2㎜),采用国产优质品牌。 2、玻璃 2.1、门窗玻璃原片厚度不小于5mm+9mm+5mm。 2.2、厨房、卫生间外窗玻璃外片采用磨砂玻璃。 2.3、中空玻璃密封必须设置分子筛,密封材料选择优质丁基胶及聚硫 胶。
铝合金压铸件质量检验规范
铝合金压铸件质量检验规范 (ISO9001-2015) 1.范围 本标准规定了铝合金压铸件的技术要求、试验方法及检验规则等,主机厂和供应商双方确认的其他发动机及其附件支架可以参照执行此标准。 本标准仅适用于铝合金压铸件以及主机厂和供应商双方确认的其他发动机及其附件支架。2.引用标准 下列标准所包含的条文,通过在本标准中引用而构成本标准的条文。本标准出版时,所示版本均为有效。所有标准都会被修订,使用本标准的各方应探讨使用下列标准最新版本的可能性。 GB/T1182形状和位置公差.通则.定义.符号.和图样表示法 GB2828逐批检查计数抽样程序及抽样表(适用于连续批的检查) GB2829周期检查计数抽样程序及抽样表(适用于生产过程稳定性的检查) GB/T6060.1表面粗糙度比较样块铸造表面 GB/T6060.4表面粗糙度比较样块抛光加工表面 GB/T6060.5表面粗糙度比较样块抛(喷)丸,喷沙加工表面 GB6414铸件尺寸公差 GB/T11350铸件机械加工余量 GB/T15114铝合金压铸件 GB/T15115压铸铝合金 3.技术要求 3.1化学成分 铝合金的化学成分应符合GB/T15115的规定。 3.2力学性能 3.2.1当采用压铸试样检验时,其力学性能应符合GB/T15115的规定。 3.2.2当采用压铸件本体检验时,其指定部位切取试样的力学性能不得低于单铸试样的75%。 3.2.33.3压铸件尺寸 3.3.1压铸件的几何形状和尺寸应符合零件图样的规定。 3.3.2压铸件的尺寸公差应按GB6414的规定执行。 3.3.3压铸件有形位公差要求时,可参照GB/T15114;其标注方法按GB/T1182的规定。 3.3.4压铸件的尺寸公差不包括铸造斜度,其不加工表面:包容面以小端为基准,被包容面以大端为基准;待加工表面:包容面以大端为基准,被包容面以小端为基准。 3.3.5压铸件需要机械加工时,其加工余量按GB/T11350的规定执行。 3.4压铸件质量要求 3.4.1压铸件应符合零件图样的规定。 3.4.2表面质量
1压铸件质量要求
压铸件的分级 1.1铸件表面分级 压铸件表面使用围分为三级,见表1: 表1压铸件表面分级表 华为公司的产品一般为Y2、Y3级要求的表面。 1.2压铸件缺陷特征定义 压铸件常见缺陷特征定义如表2所示: 表2压铸件压铸件常见缺陷特征定义
1.3表面质量 1.压铸件表面粗糙度应符合GB 6060.1-1985的规定。 2.压铸件不允许有裂纹、欠铸等任何穿透性缺陷。 3.压铸件允许有拉伤、凹陷、网状毛刺等缺陷。但其缺陷的程度和数量应符合附录C的要求。 4.铸件的浇口、飞边、溢流口、隔皮、顶杆痕迹等应清理干净、平齐,但允许留有不刮手的痕迹。 5.若图样无特别规定,有关压铸工艺部分的设置,如顶杆位置、分型线的位置、浇口和溢流口的位置等可由生产厂自行规定。 6.压铸件需要特殊加工的表面,如抛光、喷丸、镀铬、涂覆、阳极氧化、化学氧化等以图样上的标注或供需双方商定的容、样件为准。 部质量 对压铸件的气密性、液压密封性、热处理、高温涂覆、部缺陷(气孔、疏松等)及本标准未列项目有要求时,以华为公司图样标注的技术要求为准。 后处理: 由于压铸件的残余应力分布不均匀会使有些零件产生变形,当华为公司有要求时,供应商必须进行相应的后处理(如:校形后时效处理等)以达到华为公司的要求。 1.4压铸件尺寸公差 表3压铸件尺寸公差数值
注:1、对铝合金压铸件选取围: CT5~CT7,一般情况取CT6级; 2、对锌合金压铸件选取围: CT4~CT6,一般情况取CT5级。 1.5平面度公差(形状公差) 压铸件的表面形状公差值(平面度和拔模斜度除外)应在有关尺寸公差值围: 表4平面度公差(mm) 1.6位置公差 表5位置公差平行度、垂直度、端面跳动公差(mm)
铝合金压铸件一般技术要求
铝合金压铸件一般技术要求 1.压铸件应按照图纸和顾客提出的要求检查所有尺寸和表面质量。 2.对于图纸(或顾客)没有明确提出来注尺寸、形状公差和表面质量要求,以 下述标准和指标为检验依据。 ①未注几何尺寸公差:按GB6414铸件尺寸公差 ②未注形状、位置公差:按GB/T15114铝合金压铸件 附录A ③未注明表面质量要求: ⑴铸件表面不允许有裂纹、裂缝、欠铸、缩松和任何穿透性缺陷 ⑵铸件的浇口 、飞边、溢流口、隔皮、顶杆痕迹等应清理干净 ⑶压铸件按使用要求不同分为3级: 1级:涂覆工艺要求高的表面、镀铬、抛光、研磨的表面、相对运动 的配合面、危险应力区的表面等; 2级:涂覆要求一般的或要求密封的表面、镀锌阳极氧化油漆不打腻 以及装配接触面; 3级:保护性涂覆表面及紧固接触面,油漆打腻表面及其他表面。 ⑷表面粗糙度 1级:Ra3.2 2级:Ra6.3 3级:Ra12.6 ⑸表面缺陷极限 压铸件表面质量级别 1级 2级 3级 缺陷面积不超过总面积的百分数(%) 5 25 40 说明:①在不影响使用和装配的情况下,网状毛刺和痕迹:高度不超过0.2mm; ②受压铸模镶块或受分型面影响而形成的表面高低不平的偏
差,不超过相关的公差尺寸; ③推杆痕迹表面凸出或凹入铸件表面的深度,一般为±0.2mm; ⑹表面质量要求(见附表) ⑺挫痕:目视挫痕应均匀、一致,不允许有明显的凹凸。经锉加工的表面 和未经锉加工的表面允许有角度,但角度应在10°以内; ⑻变形:压铸件成型后,如有变形应进行调整,经调整后的压铸件表面不 允许有明显的打击痕迹。调整部分的平面度:0.2mm; ⑼对于顾客的特殊要求,要形成相应的工艺文件,规定其相关的工艺过程 和检验方法。 总工办 2003年4月
铝合金技术要求
铝合金门窗施工技术要求 1、技术要求 1.1 铝合金型材 1.1.1 铝合金门窗型材的选用应符合下表要求: 1.1.2 上表型材壁厚为最低要求,承包人应依据国家有关标准: 1.1. 2.1 玻璃幕墙工程技术规范JGJ102-2003 1.1. 2.2 铝合金门GB/T8478-2003 1.1. 2.3 铝合金窗GB/T8479-2003 1.1. 2.4 铝合金型材,除应满足国家规范要求外,尚应满足《节能计算报告》中的有关传热 系数的要求的规定,按照设计要求确定,并提供门窗主要构件的设计计算书,必要 时可以在铝型材内加衬钢确保刚度要求。 1.1.3 铝型材选用 型材为,发包人指定选用品牌的铝材或相同档次的产品。 1.1.4 主要型材结构式样参见招标图纸,承包人也可依据指定的型材厂家选择最恰当的型材系列,部分型材断面有可能需要新开模具,承包人应对生产厂商进行了解,投标时视为已经考虑开模费用。 1.1.5 铝金金门窗型材的基材应满足 1.1.5.1 铝合金型材牌号为; 1.1.5.2 型材的尺寸偏差精度等级为高精度级; 1.1.5.3 型材的其它性能应符合GB/T -2000的要求 1.1.6 铝合金门窗喷涂型材应满足 1.1.6.1 铝型材表面采用氟碳喷涂,平均膜厚≥30μm; 1.1.6.2 铝型材表面采用粉末喷涂,平均膜厚≥40μm,涂层的光泽为哑光RD34%;
1.1.6.3 颜色在铝型材采购前由发包人确定,除非承包人投标中已作说明,发包人颜色的确 定均不增补费用。 1.1.6.4 其它性能应符合GB/T 的要求。 1.1.6.5 承包人负责要求粉末喷涂厂家向发包人提供10年品质保证证书。 1.2 玻璃 1.2.1 玻璃的选用应符合下表: 有特别注明的玻璃按图纸所示采用,玻璃的选用必须符合国家和地区之法规、规范。所有安全玻璃必须有永久性的3C标志。 1.2.2 应按《建筑玻璃应用技术规程》(JGJ113-2003)进行设计。玻璃具体厚度应根据抗风压计算和保温隔声要求计算确定,并提供抗风压计算书,并满足上表最小厚度要求。 1.2.3 中空玻璃的传热系数应满足土建建筑图纸所注明要求。 1.3 五金
铝合金门窗的技术要求
XX项目铝合金门窗、栏杆、雨棚、百页技术规范 1、总则 1.1、此技术规范及技术要求的所有条款和说明实用于图纸上所显示的工程。 当本技术规范及技术要求与图纸上的设计说明有任何不一致时,应以较 严格要求为准或业主/顾问的澄清说明为准。 1.2、所有承包商在承包项目工作前应有责任,有义务事先了解施工场地、熟 悉图纸,及时发现问题,并向业主/顾问求得解释,满足国家及地方等 相关最新规范要求。不可以提及任何借口,而免其承担质量及返工费用 责任。 1.3标准和要求 1.3.1、工程的物料、工艺质量标准,无论在设计、装配图、结构计算、物料生产、配装、工程计划、技术性能、测试、施工安装、成品保护及验收方面等,应满足中国国家有关规范、重庆市现行的一切有关法定要求。乙方必须满足雇主指定的质量标准或乙方承诺的质量标准,以较严格为准。 1.3.2、工程技术规范 1)、《建筑工程施工质量验收统一标准》GB50300; 2)、《建筑装饰装修工程质量验收规范》GB50210; 3)、重庆市地方标准《民用建筑门窗安装及验收规程》DBJ50-065-2007; 4)、重庆市地方标准《住宅工程质量通病控制技术规程》DBJ/T50-074-2008; 5)、《建筑安全玻璃管理规定》发改运行[2003]2116号; 6)、《建筑玻璃应用技术规程》 JGJ113; 7)、《铝合金门》 GB/T8478-2003; 8)、《铝合金窗》 GB/T8479-2003; 9)、《建筑结构荷载规范》 GB50009-2006;;
10)、《民用建筑热工设计规范》 GB50176; 11)、《民用建筑节能设计标准》 JGJ26-95; 12)、《民用建筑节能65%设计标准》DBJ50-071-2007; 13)、《居住建筑节能工程施工质量验收规程》DBJ50-069-2007; 14)、《民用建筑节能65%设计标准》DBJ50-071-2007; 15)、《住宅装饰装修工程施工规范》GB50327-2001; 16)、《建筑物防雷设计规程》GB50057-94; 17)、《民用建筑门窗安装及验收规程》DBJ50-065-2007; 18)、《工程建设标准强制性条文》(房屋建设部分)(2009版); 19)、《建筑外窗抗风压性能分级及其检测方法》GB/T 7106; 20)、《建筑外窗空气渗透性能分级及其检测方法》GB/T 7107; 21)、《建筑外窗雨水渗透性能分级及其检测方法》GB/T 7108; 22)、《建筑外窗保温性能分级及其检测方法》GB8484-2002; 23)、《建筑外窗空气声隔声性能分级及其检测方法》GB 8485-2002; 24)、《建筑用安全玻璃》GB15763-2009。 如上述标准及规范要求有出入,以及与最新规范有不同处,以较严格者为准。 1.3.3、专业技术要求 1)、专业技术要求统一说明 2)、专业技术要求高于规范要求,应按专业技术要求施工; 3)、专业技术要求与设计图纸有矛盾时,应按专业技术要求施工; 4)、专业技术要求未涉及部分仍按设计图纸要求执行; 5)、设计图纸中无明确要求时,按有关规范的要求执行。 2、工作内容(请参照相关合同详细描述) 照母山约克郡G24-B地块62-73栋所有铝合金门窗、栏杆、雨棚、百叶隔栅制作安装工程。 3、材料要求
铝合金压铸件外观质量标准(2012.5)
编号: 克拉克过滤器(中 国)有限公司 铝合金铸件 外观质量标准(暂行) 共2 页 第1 页 1.适用范围: 本标准适用于为克拉克过滤器(中国)有限公司配套的铝合金铸件(以下简称铸件)的外观检验,包括低压、高压铸造毛坯、成品滤座(完成铸造后机械加工的滤座)。 2.质量要求: 2.1总体要求 2.1.1整体外观:铸件外表面必须经过抛丸处理;颜色为白亮的银灰色,色泽均匀无色斑;各部位表面粗糙度的观感均衡。 2.1.2欠铸、气孔的封堵:铸件允许采用浸渗工艺封堵微孔,但不允许使用堵漏剂对大的孔穴进行人工封堵;特殊品种确需人工封堵时需要对堵漏剂的颜色、可靠性进行充分评价,并经我公司技术部、质量部书面批准。 2.1.3镶嵌件的锈蚀:铸件带有的任何嵌件不允许存在色斑、锈点等缺陷。 2.1.4隔皮、夹渣:铸件不允许存在隔皮、夹渣; 2.2非加工外表面 2.2.1表面修磨:对铸件外表面的任何修磨必须在抛丸前进行,修磨面与相邻表面应良好过渡; 2.2.2浇冒口:浇冒口应予以修磨,修磨后表面高出、凹陷不能超过0.5mm; 2.2.3顶杆痕迹:铸件顶杆痕迹高出、凹陷不能超过0.5mm,其表面形态(弧面或平面)应与所处位置一致; 2.2.4气孔或缩孔:气孔或缩孔的深度不能超过1mm,直径不能超过2mm,每50cm 2范围内存在的缺陷不能超过一处; 2.2.5飞边:铸件分型面飞边高度不能超过0.5mm; 2.2.6边角残缺:铸件因磕碰导致的边角残缺深度不超过0.5mm,宽度不超过2mm,任意100mm 长度范围内缺陷不得超过1处; 2.2.7线状凸起、凸瘤:铸件外表面因任何原因导致的线状凸起高度不允许超过0.3mm、长度不超过5mm;凸瘤高度、直径不能超过0.5mm,每个表面存在的缺陷数不得超过2处;
铝合金门窗技术要求
铝合金门窗技术要求 1. 技术要求:i%B.c o O p3P)@$V k)uGuest 1.1铝合金门窗的设计方案由中标单位负责,经招标单位审核(或委托设计院)批准后,方可据此进行施工图设计。博客频道@中国幕墙网o z4Q} UC?0GyU o 1.2投标时必须提供门窗方案设计图和样窗样板,方案设计图包括设计说明、节点图大样、拟采用的各种铝型材的型号及其断面大样等。d.H g-f/A a;D*jGuest 1.3铝合金门窗应按《住宅建筑门窗应用技术规范》(DBJ01-79-2004)进行设计。在提供设计图的同时应附上主要受力铝材设计的计算书供甲方审核。}1n N `v e a hGuest 1.4如建筑设计图纸中所选的玻璃厚度不能满足强度要求,玻璃厚度以投标单位设计计算并经招标单位确认为准。玻璃应按《建筑玻璃应用技术规程》(JGJ113-97)进行设计。玻璃的外观和性能应符合现行国家标准和行业标准规定。H n L7I:DGuest 1.5窗框扇均需隔热断桥铝合金型材。隔热条材料采用聚酰胺66(PA66)。r4K G2n+jGuest 1.6铝合金门窗开启形式:/c'r X+vM#[(q/A mGuest (以下业主选定1种或几种)m(r.x3?6E8z3IGuest 内平开窗;内倾内平开窗;外上旋窗;博客频道@中国幕墙网-~0l h0A a)c n j7E外平开门;内平开门;推拉门;提升推拉门;折叠门;侧滑平开门;+E6Z pAn ]Guest 1.7铝合金窗固定或开启框料处均设置排水孔。4R K-q1i(re yGuest 1.8铝合金外窗铝型材接缝处均应打上密封树脂胶J01-79-2004)、《铝合金门》(GB/T 84782003)、《铝合金窗》(GB/T
铝合金壳体铸件检验标准
QJ B3100JQAQ(2010)005 QJ530410 上海汽车变速器有限公司 企业标准 QJ530410-2010 铝合金压铸件检验要求 2010-10-20 发布 2010-10-22 实施 上海汽车变速器有限公司 发 布
QJ530410—2010 前言 本标准是根据GB/T 1.1-2009《标准化工作导则第1部分:标准的结构和编写》的基本规定和格式要求进行编制的。 本标准编制时参考了ZF“铝合金铸件气孔等级检验规范”及F15压铸件质量原则等有关规定。 本标准由上海汽车变速器有限公司提出。 本标准由上海汽车变速器有限公司标准化室归口。 本标准起草单位:上海汽车变速器有限公司产品工程部。 本标准主要起草人:娄勇才、王建新。
铝合金压铸件检验要求 1.范围 本标准规定了铸件机加工后表面气缩孔及局部功能部位内部气缩孔的探测及评价的要求。 本标准适用于上海汽车变速器有限公司(简称本公司)及所有外协配套制造厂(供应商)生产的铝合金铸件。 2.铝合金压铸件气缩孔检验要求 下表中规定了铸件机加工后表面气缩孔及局部功能部位内部气缩孔的探测及评价的要求: 表气缩孔的探测及评价要求 3.铝合金铸件的外观及其他检验要求 3.1 铸件未注角度偏差为±1°; 3.2 铸件的最大错型值为0.5mm; 3.3 铸件未注起模斜度≤2°; 3.4 铸件须经时效处理; 3.5 铸件材料的化学成分及机械性能须符合技术要求; 3.6 铸件的表面硬度(或密度)须符合技术要求; 3.7 铸件表面粗糙度≤Ra12.5; 3.8 铸件非加工表面不允许存有欠铸、冷隔、裂纹等铸造缺陷,机械加工后的表面不允许存有影响使 用的铸造缺陷; 3.9 铸件的浇口、溢流口、飞边等必须清理干净,允许的残痕高度≤1mm; 3.10 铸件非加工表面上允许存在有轻度的网状毛刺,高度为≤0.2mm,由推杆造成的痕迹,其凸出高 度或凹入深度允许为≤0.5mm,毛孔毛刺及隔皮经清理后允许的痕迹≤0.4mm; 3.11 铸件的工艺基准,表面必须光滑平整,满足工装要求;
铝合金门窗工程技术规范
1 总则 1.0.1 为使铝合金门窗工程做到安全适用、技术先进、经济合理、确保质量,制定本规范。 1.0.2 本规范适用于一般工业与民用建筑的铝合金门窗工程设计、制作、安装、验收和维护。 1.0.3 铝合金门窗工程的设计、制作、安装、验收和维护、除应符合本规范的的规定外,尚应符合国家现行有关标准的规定。 2 术语和符号 2.1.1 主型材 main profiles 用于制作铝合金门窗框、扇和组合门窗的拼接型材。 2.1.2 辅型材 accessorial profiles 铝合金门窗构建体系中,镶嵌或固定在主型材上的辅助构建,起到传力或某种功能作用的附加型材。 2.1.3主要受力杆件 铝合金门窗立面内承受并传递门窗自重力和水平风荷载等作用力的框、扇和组合门窗拼樘框型材。 2.1.4 型材截面主要受力部位 铝合金主型材横截面中承受垂直和水平方向荷载作用力的腹板、翼缘或其他构件的连接受力部位。 2.1.5遮阳性能 建筑门窗在夏天阻隔太阳辐射热的能力,遮阳性能用遮阳系数SC表示。 2.1.6干法安装 墙体门窗洞口预先安置附加金属外框并对墙体缝隙进行填充、防水密封处理,在墙体洞口表面装饰湿作业完成后,将门窗固定在金属附框上的安装方法。 2.1.7 湿法安装 将铝合金门窗直接安装在未经表面装饰的墙体门窗洞口上,在墙体表面湿作业装饰时对门窗洞口间隙进行填充和防水密封处理。 2.2 符号 2.2.1 结构设计 M x————绕x轴弯曲设计值
M y————绕y轴弯曲设计值 P3 ————抗风压性能指标值 R ————承载力设计值 S ————荷载设计值 W o————基本风压 W k————风荷载标准值 W x ————绕x轴的弹性截面模量W y ————绕y轴的弹性截面模量μz ————风压高度变化系数 γG————重力载荷分项系数 γW————风载荷作用分项系数 2.2.2 物理性能 C ————水密性能设计计算系数△P ————水密性能压力差值 T r ————透光折减系数 V o ————水密性能设计风速ρ————空气密度 2.2.3 材料 E ————材料弹性模量 l ————杆件长度 μ——杆件弯曲挠度值α——材料线膨胀系数 f a——铝合金型材强度设计值 f b——钢材强度设计值 δ——应力设计值 γ——塑性发展系数