MDF板件翘曲变形原因分析
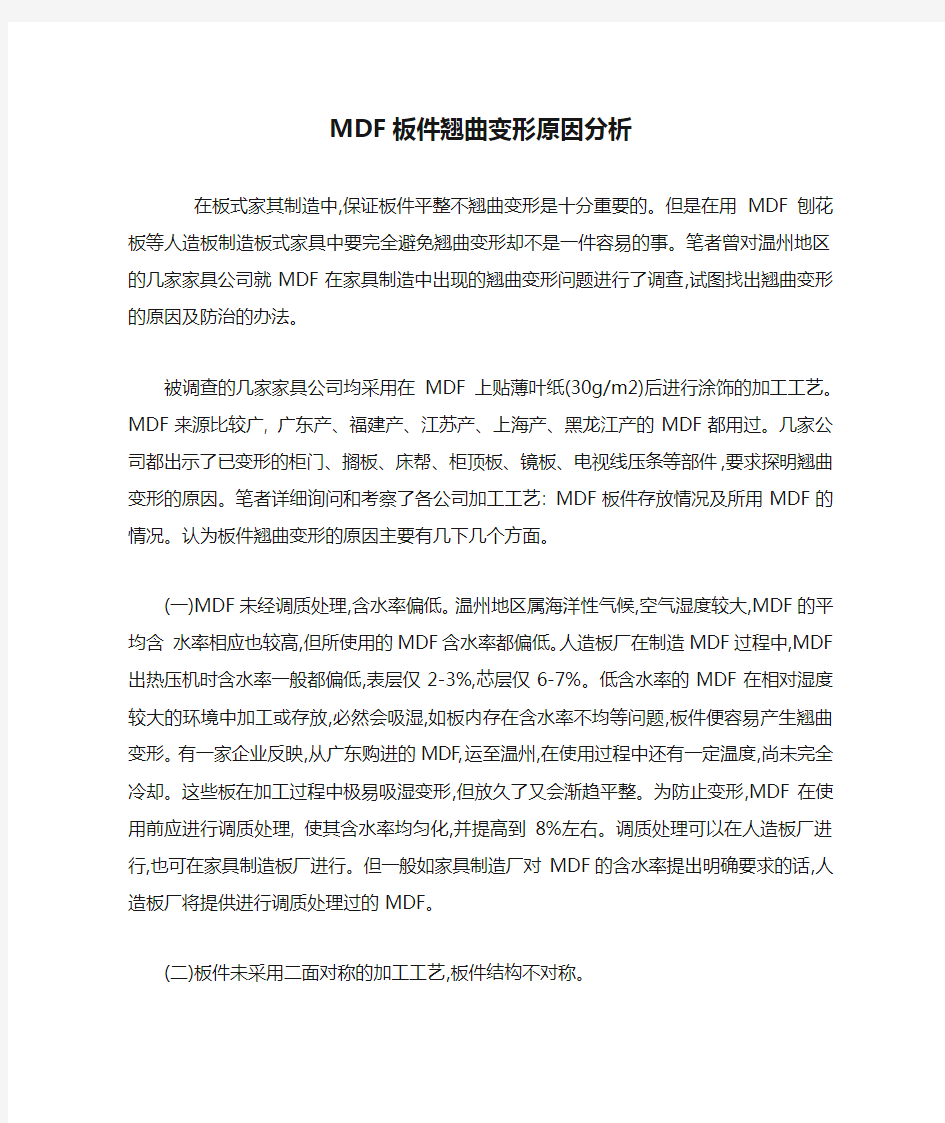

MDF板件翘曲变形原因分析
在板式家其制造中,保证板件平整不翘曲变形是十分重要的。但是在用MDF刨花板等人造板制造板式家具中要完全避免翘曲变形却不是一件容易的事。笔者曾对温州地区的几家家具公司就MDF在家具制造中出现的翘曲变形问题进行了调查,试图找出翘曲变形的原因及防治的办法。
被调查的几家家具公司均采用在MDF上贴薄叶纸(30g/m2)后进行涂饰的加工工艺。MDF来源比较广, 广东产、福建产、江苏产、上海产、黑龙江产的MDF都用过。几家公司都出示了已变形的柜门、搁板、床帮、柜顶板、镜板、电视线压条等部件,要求探明翘曲变形的原因。笔者详细询问和考察了各公司加工工艺: MDF板件存放情况及所用MDF的情况。认为板件翘曲变形的原因主要有几下几个方面。
(一)MDF未经调质处理,含水率偏低。温州地区属海洋性气候,空气湿度较大,MDF的平均含水率相应也较高,但所使用的MDF含水率都偏低。人造板厂在制造MDF过程中,MDF出热压机时含水率一般都偏低,表层仅2-3%,芯层仅6-7%。低含水率的MDF在相对湿度较大的环境中加工或存放,必然会吸湿,如板内存在含水率不均等问题,板件便容易产生翘曲变形。有一家企业反映,从广东购进的MDF,运至温州,在使用过程中还有一定温度,尚未完全冷却。这些板在加工过程中极易吸湿变形,但放久了又会渐趋平整。为防止变形,MDF在使用前应进行调质处理, 使其含水率均匀化,并提高到8%左右。调质处理可以在人造板厂进行,也可在家具制造板厂进行。但一般如家具制造厂对MDF的含水率提出明确要求的话,人造板厂将提供进行调质处理过的MDF。
(二)板件未采用二面对称的加工工艺,板件结构不对称。
据了解,几家家私公司对家具的主要部件如柜门、台面、床帮等的正面都采用了比较精细的加工工艺,MDF基材先进行处理(精砂、封纸、涂底漆、砂光)然后再购薄叶纸,贴纸后再进行涂饰处理(二道底漆、干砂、水砂、一道面漆),涂饰后表面平滑,光亮如镜,但背面一般只进行简单的封底处理,或即使贴薄叶纸,涂饰的道数也相应减少,背面能观察到明显的纤维吸湿膨胀的痕迹。有的公司把镜子与MDF直接粘合在一起,造成镜子破碎或镜板严重变曲变形。以上这样处理的板件由于其正反二面对空气中湿气的吸湿能力不同,吸湿速度不同,而极易造成板件的变形。因此板件在贴面和涂饰加工中要注意二面对称,使其结构对称、平衡, 这很重要的。二种性能完全不同的材料,如镜子和MDF不能采用胶合的方式复合,应采用螺钉结合,并留有伸缩余地。
(三)MDF密度偏低
MDF的密度偏低造成加工面不光滑,且易吸湿变形,一般用于家具制造的MDF密度在厚度方向的分布应均匀,表芯层密度差异过大的MDF不适宜做家具,平均密度在0.75g/m3左右比较合适。
(四)MDF防水性较差
用于家具制造的MDF应具有一定的防火性能,否则易吸湿变形。通常MDF的防水性能以吸水厚度膨胀率来表示,用于家具制造的MDF的吸水厚度膨胀率应小于6%较为合适。(五)贮存条件较差
MDF基板或板件应平整堆放,不能竖放,而且应存放在干燥通风的环境中,如存放在潮湿的环境中则易吸湿变形,甚至发霉。
综上所述,造成MDF板件变形的原因是多种多样的,要防止MDF板件变形,首先应选用合适的MDF,其含水率应为8%左右,密度为0.75g/m3左右,吸水厚度膨胀率应小于6%。其次加工中应注意结构对称,并注意贮存保管的条件。对已产生变形的板件,在湿度较高的环境中上压重物堆放,可得到缓解。
翘曲分析
注塑制品的翘曲变形分析 一、引言 翘曲变形是指注塑制品的形状偏离了模具型腔的形状,它是塑料制品常见的缺陷之一。随着塑料工业的发展,人们对塑料制品的外观和使用性能要求越来越高,翘曲变形程度作为评定产品质量的重要指标之一也越来越多地受到模具设计者的关注与重视。模具设计者希望在设计阶段预测出塑料件可能产生翘曲的原因,以便加以优化设计,从而提高注塑生产的效率和质量,缩短模具设计周期,降低成本。 本文主要对在注塑模具设计过程中影响注塑制品翘曲变形的因素加以分析。 二、模具的结构对注塑制品翘曲变形的影响 在模具设计方面,影响塑件变形的因素主要有浇注系统、冷却系统与顶出系统等。 1.浇注系统的设计 注塑模具浇口的位置、形式和浇口的数量将影响塑料在模具型腔内的填充状态,从而导致塑件产生变形。 流动距离越长,由冻结层与中心流动层之间流动和补缩引起的内应力越大;反之,流动距离越短,从浇口到制件流动末端的流动时间越短,充模时冻结层厚度减薄,内应力降低,翘曲变形也会因此大为减少。图1为大型平板形塑件,如果只使用一个中心浇口(如图1a所示)或一个侧浇口(如图1b所示),因直径方向上的收缩率大于圆周方向上的收缩率,成型后的塑件会产生扭曲变形;若改用多个点浇口(如图1c所示)或薄膜型浇口(如图1d所示),则可有效地防止翘曲变形。 a) 中心浇口b) 侧浇口c)多点浇口d) 薄膜型浇口 当采用点浇进行成型时,同样由于塑料收缩的异向性,浇口的位置、数量都对塑件的变形程度有很大的影响。图2为一箱形制件在不同浇口数目与分布下的试验图。 a)直浇口b)10个点浇口c)8个点浇口 d)4个点浇口e) 6个点浇口f) 4个点浇口 由于采用的是30%玻璃纤维增强PA6,而得到的是重量为4.95kg的大型注塑件,因此沿四周壁流动方向上设有许多加强肋,这样,对各个浇口都能获得充分的平衡。实验结果表明,按图f设置浇口具有较好的效果。但并非浇口数目越多越好。实验证明,按图c设计的浇口比图a的直浇口还差。 另外,多浇口的使用还能使塑料的流动比(L/t)缩短,从而使模腔内物料密度更趋均匀,收缩更均匀。同时,整个塑件能在较小的注塑压力下充满。而较小的注射压力可减少塑料的分子取向倾向,降低其内应力,因而可减少塑件的变形。 2.冷却系统的设计 在注射过程中,塑件冷却速度的不均匀也将形成塑件收缩的不均匀,这种收缩差别导致弯曲力矩的产生而使塑件发生翘曲。 如果在注射成型平板形塑件时所用的模具型腔、型芯的温度相差过大,如图3所示,由于贴近冷模腔面的熔体很快冷却下来,而贴近热模腔面的料层则会继续收缩,收缩的不均匀将使塑件翘曲。因此,注塑模的冷却应当注意型腔、型芯的温度趋于平衡,两者的温差不能太大。 除了考虑塑件内外表面的温度趋于平衡外,还应考虑塑件各侧的温度一致,即模具冷却时要尽量保持型腔、型芯各处温度均匀一致,使塑件各处的冷却速度均衡,从而使各处的收缩更趋均匀,有效地防止变形的产生。因此,模具上冷却水孔的布置至关重要。在管壁至型腔表面距离确定后,应尽可能使冷却水孔之间的距离小,才能保证型腔壁的温度均匀一致。同时,由于冷却介质的温度随冷却水道长度的增加而上升,使模具的型腔、型芯沿水道产生温差。因此,要求每个冷却回路的水道长度小于2m。在大型模具中应设置数条冷却回路,一
塑胶产品变形的一些原因
塑胶产品变形的一些原因 翘曲变形是指注塑制品的形状发生畸变而翘曲不平,偏离了制件的形状精度要求,它是注射模设计和注射生产中常见的较难解决的制品缺陷之一。 随着塑料工业的发展,特别是电子信息产业的发展,对塑料制品的外观和使用性能要求越来越高。如笔记本及掌上电脑,扁薄手机等塑壳制件,翘曲变形程度已作为评定产品质量的重要指标之一,越来越受到模具设计者的关注与重视。希望在设计阶段预测出塑料件可能产生的翘曲原因,以便优化设计,减小产品的翘曲变形,达到产品设计的精度要求。 1、翘曲变形产生的原因 翘曲变形是制品在注射工艺过程中,应力和收缩不均匀而产生的。脱模不良,冷却不足,制件形状和强度不宜,模具设计和工艺参数不佳等也使塑件发生曲变。 模温不匀,塑件内部温度不均匀。 塑件壁厚差异和冷却不均匀,导致收缩的差异。 塑件厚向冷凝压差和冷却速差。 塑件顶出时温度偏高或顶出受力不匀。
塑件形状不当,具有弯曲或不对称的形状。 模具精度不良,定位不可靠,致使塑件易翘曲变形。 进料口位置不当,注射工艺参数不佳,使收缩方向性明显,收缩不均匀。 流动方向和垂直于流动方向的分子链取向性差异,致使收缩率不同。 凸凹模壁厚向不对称冷却,冷却时间不足,脱模后冷却不当。 2、模具结构对注塑件翘曲变形的影响 在模具设计方面,影响塑件翘曲变形的因素主要有三大系统,分别是浇注系统、冷却系统与顶出系统等。 浇口的设计 注塑模浇口是整个浇注系统的关键部分,它的位置、形式和浇口的数量直接影响熔料在模具型腔内的填流状态,导致塑料固化、收缩和内应力的异变。常用的浇口类型有侧浇口、点浇口、潜伏式浇口、直浇口、扇形浇口以及薄膜型浇口等。 浇口位置的选择应使塑料的流动距离最短。流动距离越长,内部流动层与外部冻结层之间的流动差增加,这样冻结层与中心流动层之间流动和补缩引起的内应力愈大,塑件变形也随之增大;反之,流动距离越短,从浇口到制件流动末端的流动时间越短,充模时冻结层厚度减薄,内应力降低,翘曲变形也会因此减小。 如精密薄壁较大塑件,使用一个中心浇口或一个侧浇口,因径向收缩率大于周向收缩率,成型后的塑件会产生较大的扭曲变形;若改用多个点浇口或薄膜型浇口,则可有效地防止翘曲变形,因此设计时须进行流动比计算校核。 当采用点浇口成型时,同样由于塑料收缩的异向性,浇口的位置、数量都对塑件的变形程度有很大的影响。
中厚板轧制试卷
第二章习题 一、填空 1.中厚板轧机有、、和万能式等四种型式。 二辊可逆式三辊劳特式四辊可逆式 2.中厚板轧机一般采用来命名。 工作辊的辊身长度 3.四辊可逆式轧机由一对小直径和一对大直径组成。 工作辊支承辊 4.万能式轧机是在在四辊(或二辊)可逆轧机的一侧或两侧带有的轧机。 立辊 5.中厚板轧机的布置型式有、、三种形式。 单机座、双机座、半连续式或连续式、 6.中厚板轧机常采用的布置形式是。 双机座 7.双机座布置是把粗轧和两个阶段的任务分到两个机座上完成。 精轧 8.中厚板加热炉的型式主要有、、三种。连续式加热炉室状式加热炉均热炉 9.用于板坯加热的连续式加热炉主要是和两种型式。 推钢式步进式 10.三段式加热炉,三段指的是预热段、加热段和__________。 均热段 11.中厚板的轧制分为、、三个阶段。 除鳞粗轧精轧 12.中厚板精轧阶段的主要任务是控制。 质量 13.中厚板的展宽方法有、、和角轧-纵轧法四种。 全纵轧法、全横轧法、横轧-纵轧法、 14.平面形状控制是指钢板的控制。
矩形化 15.厚板的轧制分为、和三个阶段。 整形轧制展宽轧制精轧 16.展宽比是指展宽轧制后的与之比。 板宽轧前板宽 17.轧制比是指伸长轧制后的与之比。 钢板长度轧前板坯长度 18.中厚板的冷却方式有和两种。 自然冷却、控制冷却(工艺冷却) 19.中厚板矫直机一般为式矫直机。 辊 20.中厚板划线的目的是。 将毛边钢板剪切或切割成合格的最大矩形。 21.划线的方法有、和等多种方法。 人工划线小车划线光标投射 22.中厚板剪切机的任务是、切尾、、剖分、及取样。 切头切边定尺剪切 23.中厚板生产中常用的热处理作业有常化、淬火、、四种。 回火退火 24.中厚板生产中常用的热处理作业有、、回火、退火四种。 常化淬火 25.速度制度是指变化的曲线图。 轧辊转速随时间 26.可逆式轧机有和两种速度制度。 梯形、三角形 27.当轧件较长时一般采用速度制度。 梯形 28.当轧件较短时一般采用速度制度。 三角形 29.轧件在每道中的轧制时间由、、匀速轧制时间、组成。
塑料件翘曲变形分析
塑料件翘曲变形分析 塑料件的翘曲变形是塑料件常见的成型质量缺陷。 塑料件的翘曲变形主要是因为塑料件受到了较大的应力作用,主要分为外部应力和内部应力,当大分子间的作用力和相互缠结力承受不住这种应力作用时,塑料件就会发生翘曲变形。 1、外部应力导致的翘曲变形 此类翘曲变形主要为制件顶出变形,产生的原因为模具顶出机构设计不合理或成型工艺条件不合理。 、模具顶出机构设计不合理 顶出机构设计不合理,顶出设计不平衡,或顶杆截面积过小,都有可能使塑料件局部受力过大,承受不住应力作用发生塑性形变而导致翘曲变形。 防止顶出变形需改善脱模条件:如平衡顶出力;仔细磨光新型侧面;增大脱模角度;顶杆布置在脱模阻力较大的地方,如加强筋,Boss柱等处。 、成型工艺参数设置不合理 冷却时间不足,凝固层厚度不够,塑料件强度不足,脱模时容易导致产品翘曲变形。 可以延长冷却时间,增加凝固层厚度来解决。 2、内部应力导致的翘曲变形 、塑料内应力产生的机理 塑料内应力是指在塑料熔融加工过程中由于受到大分子链的取向和冷却收缩等因素而产生的一种内在应力。内应力的本质为大分子链在熔融加工过程中形成的不平衡构象,这种不平衡构象在冷却固化时不能立刻恢复到与环境条件相适应的平衡构象,这种不平衡构象实质为一种可逆的高弹形变,而冻结的高弹形变以位能情势储存在塑料制品中,在合适的条件下,这种被迫的不稳定的构象将向自在的稳定的构象转化,位能改变为动能而开释。当大分子间的作用力和相互缠结力承受不住这种动能时,内应力平衡即受到破坏,塑料制品就会产生翘曲变形,严重时会发生应力开裂。 、塑料内应力的种类 取向内应力 取向内应力是塑料熔体在充模流动和保压补料过程中,大分子链沿流动方向定向排列,构象被冻结而产生的一种内应力。 取向应力受塑胶流动速率和粘度的影响。如图一所示,A 层是固化层,B层是流动高剪切层,C层是熔胶流动层。A层为充填时紧贴两侧模壁,瞬间冷却固化层。B层是充填时紧靠A层的高剪切区域所形成的,由于与A层具有最大速度差,所以形成最大剪切流动应力效果(如图二所示),塑胶充填结束时本区尚未完全凝固,因外层A固化层有绝热效果,使B层散热较慢,而C层所受剪切作用较小,若产品厚度有变化,则主要影响C层厚度,若是薄件成品则C层的厚度将会变小。
翘曲变形
变形的调试心得 1、首先是温度问题,按照我们常规理解的,变形会往温度高的方向变,但是事实却不一定如此,这与产品的近胶口有很大的关系,如果是胶口在产品中间的话,平板产品一般会完前模变形,这时通过增加后模模具的温度,产品的变形量会减小很多!如果胶口是在边上的话,变形那就不同了! 2、二次压使用高大会导致变形量加大,所以建议尽量使用一次压,将转换位置减小,保压速度加快!二次压就能减到最小,但是这样如果锁模力不够的话,批锋会比较严重的哦! 所以说,在新模调试的时候要尽量想办法去控制变形量,最好是从模具温度以及参数上去想办法!(这当然是建立在模具结构不能改变的基础上来说的) 塑料射出成形先天上就会发生收缩,因为从制程温度降到室温,会造成聚合物的密度变化,造成收缩。整个塑件和剖面的收缩差异会造成内部残留应力,其效应与外力完全相同。在射出成形时假如残留应力高于塑件结构的强度,塑件就会于脱模后翘曲,或是受外力而产生破裂。 7-1 残留应力 残留应力(residual stress)是塑件成形时,熔胶流动所引发(flow-induced)或者热效应所引发(thermal-induced),而且冻结在塑件内的应力。假如残留应力高过于塑件的结构强度,塑件可能在射出时翘曲,或者稍后承受负荷而破裂。残留应力是塑件收缩和翘曲的主因,可以减低充填模穴造成之剪应力的良好成形条件与设计,可以降低熔胶流动所引发的残留应力。同样地,充足的保压和均匀的冷却可以降低热效应引发的残留应力。对于添加纤维的材料而言,提升均匀机械性质的成形条件可以降低热效应所引发的残留应力。 7-1-1 熔胶流动引发的残留应力 在无应力下,长链高分子聚合物处在高于熔点温度呈现任意卷曲的平衡状态。于成形程中,高分子被剪切与拉伸,分子链沿着流动方向配向。假如分子链在完全松弛平衡之前就凝固,分子链配向性就冻结在塑件内,这种应力冻结状态称为流动引发的残留应力,其于流动方向和垂直于流动方向会造成不均匀的机械性质和收缩。一般而言,流动引发的残留应力比热效应引发的残留应力小一个次方。 塑件在接近模壁部份因为承受高剪应力和高冷却速率的交互作用,其表面的高配向性会立即冻结,如图7-1所示。假如将此塑件存放于高温环境下,塑件将会释放部份应力,导致.的收缩与翘曲。凝固层的隔热效应使聚合物中心层维持较高温度,能够释放较多应力,所以中心层分子链具有较低的配向性。
冲裁件常见缺陷及其原因分析
冲裁件常见的缺陷有: 毛刺、制件表面翘曲不平,尺寸精度超差等。 ㈠毛刺 在冲裁加工中,产生不同程度的毛刺,一般来讲是很难避免的。其影响因素有以下几方面。 1?间隙 冲裁间隙过大、过小或不均匀,均可产生毛刺。造成间隙过大、过小和不均匀的因素有: ⑴模具工作部分的尺寸精度不符合冲模图纸的规定。 ⑵凸模或凹模有反梢(反锥),使冲裁过程中的间隙发生了变化。 ⑶导向部分间隙大。如导柱与衬套的配合间隙或斜楔冲裁的导向板间间隙过大均能引起冲裁过程中间隙的变化。 ⑷装配误差。如凸模与凸模固定板装配垂直,或者凸模与固定板孔配合部分已磨损,或者是固定凸模或凹模位置的定位销位置不准,都会造成凸模与凹模相对位置发生偏差而使间隙不均。 ⑸安装误差。如冲模上下底板表面在安装时未擦干净,或上模螺钉紧固不当而引起工作部分倾斜。 ⑹冲模结构不合理。如冲模或冲模工作部分刚度不够,在冲裁过程中发生变形而影响间隙的变化。或者缺乏用以抵消在冲裁过程中产生侧向力的反侧压块,使工作部分产生了相对移位。 ⑺压力机导轨间隙过大,滑块底面与工作台的平行度不好,或者滑块的运动方向与压床台面的垂直度不好。 ⑻板料的瓢曲度大,在冲裁过程中,使直径较小的凸模发生倾斜。 2.刃口钝
磨损或啃伤冲件。 3.定位高度不当 修边冲孔时,如果制件深度低于定位高度时,在冲裁过程中,制件形状与刃口就会不服贴而产生毛刺。 4.模具结构不当 由于缺乏必要的压料装置,在单面冲裁时,尤其是厚板在冲裁过程中会产生较大的拉应力,使金属纤维伸长并拉断,导致冲裁裂面粗糙,出现较大的毛刺。 毛刺的产生,不仅在以后的变形工序容易引起开裂,而且给板料分层和送料造成困维,并加剧刃口磨损,降低模具的使用寿命以及产生铆接间隙或焊穿、焊不牢等缺陷。毛刺还会在生产和使用过程中划伤操作者,威胁人身安全。如果在制件上已经出现了允许范围外的毛刺,就应当予以消除。消除毛刺的方法最常用的是滚光。产生的原因: 1?冲裁间隙大。间隙过大,很容易产生翘曲。 2.凹模洞口有反梢。制件在通过尺寸小的部位时,外同向中心压缩,从而产生弯曲。 3制件本身产生的翘曲。当制件形状复杂时,制件周围的剪切力就不均匀,而使制件出现翘曲。解决的办法是增大压料力,冲裁前压紧,然后象精冲那样冲裁,能取得良好的效果。 4材料内部应力产生的翘曲。板料在轧制、卷绕时产生的内部应力在冲裁后转移到表面时,制件将出现翘曲,所以这种应力在加工前就将其消除。可以通过矫平机矫平或退火来消除,也可在加工后矫平。 5.由于油、空气、杂物产生翘曲。在冲模和制件之间有油、空气、杂物等压迫制件时,制件将产生翘曲,特别是对薄料,软材料影响较大。 ㈢尺寸精度超差 1.模具刃口尺寸制造超差
塑胶加工中翘曲变形的原因及解决办法
一. 翘曲变形是指注塑制品的形状偏离了模具型腔的形状,它是塑料制品常见的缺陷之一。出现翘曲变形的原因很多,单靠工艺参数解决往往力不从心。结合相关资料和实际工作经验,下面对影响注塑制品翘曲变形的因素作简要分析。 二、模具的结构对注塑制品翘曲变形的影响。 在模具方面,影响塑件变形的因素主要有浇注系统、冷却系统与顶出系统等。 1.浇注系统 注塑模具浇口的位置、形式和浇口的数量将影响塑料在模具型腔内的填充状态,从而导致塑件产生变形。流动距离越长,由冻结层与中心流动层之间流动和补缩引起的内应力越大;反之,流动距离越短,从浇口到制件流动末端的流动时间越短,充模时冻结层厚度减薄,内应力降低,翘曲变形也会因此大为减少。一些平板形塑件,如果只使用一个中心浇口,因直径方向上的收缩率大于圆周方向上的收缩率,成型后的塑件会产生扭曲变形;若改用多个点浇口或薄膜型浇口,则可有效地防止翘曲变形。当采用点浇口进行成型时,同样由于塑料收缩的异向性,浇口的位置、数量都对塑件的变形程度有很大的影响。另外,多浇口的使用还能使塑料的流动比(L/t)缩短,从而使模腔内熔体密度更趋均匀,收缩更均匀。同时,整个塑件能在较小的注塑压力下充满。而较小的注射压力可减少塑料的分子取向倾向,降低其2.冷却系统 在注射过程中,塑件冷却速度的不均匀也将形成塑件收缩的不均匀,这种收缩差别导致弯曲力矩的产生而使塑件发生翘曲。如果在注射成型平板形塑件(如手机电池壳)时所用的模具型腔、型芯的温度相差过大,由于贴近冷模腔面的熔体很快冷却下来,而贴近热模腔面的料层则会继续收缩,收缩的不均匀将使塑件翘曲。因此,注塑模的冷却应当注意型腔、型芯的温度趋于平衡,两者的温差不能太大(此时可考虑使用两个模温机). 除了考虑塑件内外表的温度趋于平衡外,还应考虑塑件各侧的温度一致,即模具冷却时要尽量保持型腔、型芯各处温度均匀一致,使塑件各处的冷却速度均衡,从而使各处的收缩更趋均匀,有效地防止变形的产生。因此,模具上冷却水孔的布置至关重要。在管壁至型腔表面距离确定后,应尽可能使冷却水孔之间的距离小,才能保证型腔壁的温度均匀一致。同时,由于冷却介质的温度随冷却水道长度的增加而上升,使模具的型腔、型芯沿水道产生温差。因此,要求每个冷却回路的水道长度小于2米。在大型模具中应设置数条冷却回路,一条回路的进口位于另一条回路的出口附近。对于长条形塑件,应采用直通型水道。(而我们的模具大多是采用S型回路----既不利于循环,又延长周期。顶出系统的设计也直接影响塑件的变形。如果顶出系统布置不平衡,将造成顶出力的不平衡而使塑件变形。因此,在设计顶出系统时应力求与脱模阻力相平衡。另外,顶出杆的截面积不能太小,以防塑件单位面积受力过大(尤其在脱模温度太高时)而使塑件产生变形。顶杆的布置应尽量靠近脱模阻力大的部位。在不影响塑件质量(包括使用要求、尺寸精度与外观等)的前提下,应尽可能多设顶杆以减少塑件的总体变形(换顶杆为顶块就是这个道理)。用质塑料(如TPU)来生产深腔薄壁的塑件时,由于脱模阻力较大,而材料又较软,如果完全采用单一的机械顶出方式,将使塑件产生变形,甚至顶穿或产生折叠而造成塑件报废,如改用多元件联合或气(液)压与机械式顶出相结合的方式效果会更好(以后会用到)。 三、塑化阶段对制品翘曲变形的影响 塑化阶段即由玻璃态料粒转化为粘流态熔体的过程(培训时讲过原料塑化的三态变化)。在这个过程中,聚合物的温度在轴向、径向(相对螺杆而言)温差会使塑料产生应力;另外,注射机的注射压力、速率等参数会极大地影响充填时分子的取向程度,进而引起翘曲变形。 四、充填及冷却阶段对制品翘曲变形的影响 熔融态的塑料在注射压力的作用下,充入模具型腔并在型腔内冷却、凝固。此过程是注射成型的关键环节。在这个过程中,温度、压力、速度三者相互耦合作用,对塑件的质量和生
汽车塑料件的翘曲变形问题
汽车塑料件的翘曲变形问题 汽车塑料件的翘曲变形问题 随着紧凑型,微型汽车的增多,其所使用的塑料制品也相应朝着体积轻量化,结构复杂化发展。在此情况下,一些薄壁注塑产品越来越出现在一些车型上。 翘曲变形是汽车薄壳塑料成型中的常见缺陷之一,因为涉及到对翘曲变形量的准确预测,而不同材料、不同形状的注塑件的翘曲变形规律差别很大。翘曲变形问题的存在会影响注塑件的形状精度和表面质量,当翘曲变形量超过允许误差后,就成为成形缺陷,进而影响产品装配。 翘曲变形是指注塑件的形状偏离了模具型腔的形状。由于翘曲变形不仅影响产品装配和使用性能,而且影响产品外观质量。翘曲变形程度已成为评定产品质量的重要指标之一。 引起塑件翘曲变形的机理和要素翘曲主要与塑件结构、模具设计以及成型工艺三方面有关。由于塑料成型时流动方向的收缩率比垂直方向的大,使得制件各向收缩率不同而翘曲。 一模具设计方面 (1)浇口位置不当或数量不足。 浇口的位置和数量不仅影响流动的平衡,还将影响填充结束时的体积收缩。浇口位置分析的目的`是要根据零件结构,找到为使流动达到平衡的最佳浇口位置,以尽可能减少制品缺陷,从而获得质量好的产品。 (2)顶出位置不当或制品受力不均匀。 二成型工艺方面
(1)模具、机筒温度太高。 只提高温度会使翘曲变形增大,而同时提高注射速度,则可减小翘曲变形量。 (2)保压压力太高或注射速度太快。 提高注射速度可以使注射时间大大地缩短,但锁模力要有所增加;提高注射速度可以起到减小翘曲变形的作用。但增加注射速度会增 加制品成型过程中表面剪切应力。 (3)注射时间太长或冷却时间太短。 三塑件结构方面,塑件的结构是决定其本身翘曲变形程度的关键。 塑件壁厚不均,变化突然或壁厚过小。 厚壁不均的塑件,不同区域温度、压力和流速的不同,会引起收缩率的差异,进而引起塑件的翘曲变形和参与内应力。
宽厚板轧制过程中扣翘头原因分析与控制措施
宽厚板轧制过程中扣翘头原因分析与控制措施 摘要本文主要针对莱钢4300宽厚板生产线在生产过程中,轧件头尾经常发生扣翘头的原因进行了分析,并结合生产实际给出了调整措施,对现场实际生产具有一定的指导意义。 关键词扣头;翘头;辊速差;压下率 莱钢宽厚板厂自2010年投产以来,已成功生产出工程机械用钢、船板钢、耐磨钢、高附加值管线钢等产品。我厂从调试到生产的过程中,多次遇到轧件扣翘头的现象,这种现象较多的出现在精轧机区域,在轧制过程中,一旦轧件产生翘头或扣头,很容易碰撞到设备,不但严重损坏设备,还影响到轧机的作业率、产量和成材率。 1 轧件扣翘头产生的原因 在宽厚板轧制过程中轧件翘头的产生是一个典型的热力学耦合问题,其影响因素很多,如轧件在厚度方向上、下表面温度分布不均、压下率不同、轧件的摩擦条件不一致、上下辊辊径不同导致的辊面线速度不同等都将引起轧件在轧制时出现扣翘头,结合宽厚板厂的实际生产情况,对扣翘头的主要影响因素进行了分析。 1.1 温度的影响 从理论上分析,正常情况下板坯在理论轧制高度有两个相同直径的轧辊,相同轧制速度下应该产生平直的头部。但是生产过程中,板坯上下表面温度存在差别是影响板坯头部扣翘原因之一,如果下表面温度高于上表面,此时忽略其他影响因素,板坯下表面金属容易变形,金属流动速度快,板坯经过轧制后,应该为翘头;反之应该为扣头。板坯上下表面温度羞产生原因,板坯加热过程中产生的温度差、板坯暴露在空气中产生温度差、板坯经过除鳞机时对板坯上下表面冷却不均产生温度差、板坯在辊道上运输过程中产生温度差。 1.2 轧制线的影响 根据经验和轧制原理分析,当实际轧制线高于理论轧制线时,板坯经过轧机容易产生扣头,因为上辊压下量大于下辊压下量,板坯上表面延伸大于下表面延伸,因此产生扣头,反之翘头。 1.3 轧件道次压下率的影响 在板坯上、下表面存在温差的情况下,必须考虑压下率对板坯上翘的影响。压下率是不对称轧制中用于调整板坯出轧机形状最主要的几个轧制参数之一。实践证明,在生产过程中调整道次压下率,抑制轧件翘头是非常直接和有效的。在
应用CAE模流分析技术改善手机产品开发之收缩翘曲变形问题
應用CAE模流分析技術改善手機產品開發之收縮翹曲變形問題 郭瑞坤、吳燕玲 J. K. KUO, Ann-Wu 大霸電子股份有限公司研發/機構 摘要 近年來隨著全球網路通訊產業的發達,手機市場成長快速,由於產業的逐漸成熟、換機市場的熱絡,各廠商紛紛推出適合不同消費族群的產品,在功能與外型上也做不斷的創新與研發,除了卓越的技術與嚴格的品質控管外,掌握時間與速度才能擁有競爭優勢,面對輕便小巧外觀時尚的多功能手機的趨勢,機構設計空間也變的相當有限,在開發時間緊縮而良率需兼顧的考驗下,產品本身的設計顯得相當重要。為確保產品設計的正確性,本公司利用MOLDEX 3D軟體在產品設計階段同時進行電腦模擬分析,預測產品在成型過程可能發生的問題,避免因設計不當影響產品的開發時間。 一、案例簡介 A. 產品說明 產品為Base手機下蓋,幾何尺寸(mm):長*84寬*43.6高*9.3,平均厚度=1.4最厚2.2最薄0.55;模具設計:三板模採一模一穴三點直接進澆。 B. 問題焦點 此分析針對模具廠澆口選用在薄肉區與產品設計有部份肉厚差異較大,造成射出成型時保壓階段塑料提早固化壓力傳遞不良,產品開模後有縮水情況,進行電腦模擬分析。 C.使用材料 此產品分析所採用的材料為PC。 D. 加工條件 本文所採用之加工條件如表一所示。 二、模流分析-原始設計 圖1為產品厚度分佈由2.2~0.55mm。 1)流動不平衡、結合線、包封產生 圖2流動波前85%,澆口徑向充填並非均勻流動,在靠近薄肉區呈現遲滯,有流動不平衡的情況。 圖3流動波前等位線圖,圖中有部份等位線過密情形,代表此區流動阻力較大,塑料流動通常往流動阻力小的區域流,最後才回填流動阻力較大的區域,造成流動末端有結合線與包封產生,有時甚至有短射之慮。
最新塑料制品的翘曲变形的原因分析和解决方法
塑料制品的翘曲变形的原因分析和解决方法 一、前言 翘曲变形是指注塑制品的形状偏离了模具型腔的形状,它是塑料制品常见的缺陷之一。出现翘曲变形的原因很多,单靠工艺参数解决往往力不从心。结合相关资料和实际工作经验,下面对影响注塑制品翘曲变形的因素作简要分析。 二、模具的结构对注塑制品翘曲变形的影响。 在模具方面,影响塑件变形的因素主要有浇注系统、冷却系统与顶出系统等。 1.浇注系统 注塑模具浇口的位置、形式和浇口的数量将影响塑料在模具型腔内的填充状态,从而导致塑件产生变形。 流动距离越长,由冻结层与中心流动层之间流动和补缩引起的内应力越大;反之,流动距离越短,从浇口到制件流动末端的流动时间越短,充模时冻结层厚度减薄,内应力降低,翘曲变形也会因此大为减少。一些平板形塑件,如果只使用一个中心浇口,因直径方向上的收缩率大于圆周方向上的收缩率,成型后的塑件会产生扭曲变形;若改用多个点浇口或薄膜型浇口,则可有效地防止翘曲变形。 当采用点浇口进行成型时,同样由于塑料收缩的异向性,浇口的位置、数量都对塑件的变形程度有很大的影响。 另外,多浇口的使用还能使塑料的流动比(L/t)缩短,从而使模腔内熔体密度更趋均匀,收缩更均匀。同时,整个塑件能在较小的注塑压力下充满。而较小的注射压力可减少塑料的分子取向倾向,降低其内应力,因而可减少塑件的变形。 2。冷却系统 在注射过程中,塑件冷却速度的不均匀也将形成塑件收缩的不均匀,这种收缩差别导致弯曲力矩的产生而使塑件发生翘曲。 如果在注射成型平板形塑件(如手机电池壳)时所用的模具型腔、型芯的温度相差过大,由于贴近冷模腔面的熔体很快冷却下来,而贴近热模腔面的料层则会继续收缩,收缩的不均匀将使塑件翘曲。因此,注塑模的冷却应当注意型腔、
塑胶加工中翘曲变形的原因及解决办法
注塑质量经验总结 本文来自:6sigma品质网https://www.360docs.net/doc/735956582.html, 作者:peakdongfeng 点击1054次原文:https://www.360docs.net/doc/735956582.html,/viewthread.php?tid=199130 1. 刚开机时产品跑披锋,生产一段时间后产品缺胶的原因及解决方案。 刚开机时注塑机料管内的熔胶由于加热时间长,熔胶粘度低,流动性好,产品易跑披锋,生产一段时间后由于熔胶不断把热量带走,造成熔胶不足,粘度大,流动性差,使产品缺胶。 在生产一段时间后,逐渐提高料管温度来解决。 2. 在生产过程中,产品缺胶,有时增大射胶压力和速度都无效,为什么?解决方法? 是因为生产中熔胶不断把热量带走,造成熔胶不足,胶粘度大,流动性差,使产品缺胶。 提高料管温度来解决。 3. 产品椭圆的原因及解决方法。 产品椭圆是由于入胶不均匀,造成产品四周压力不匀,使产品椭圆,采用三点入胶,使产品入胶均匀。4. 精密产品对模具的要求。 要求模具材料刚性好,弹变形小,热涨性系数小。 5. 产品耐酸试验的目的 产品耐酸试验是为了检测产品内应力,和内应力着力点位置,以便消除产品内应力。 6. 产品中金属镶件受力易开裂的原因及解决方法。 产品中放镶件,在啤塑时由于热熔胶遇到冷镶件,会形成内应力,使产品强度下降,易开裂。 在生产时,对镶件进行预热处理。 7. 模具排气点的合理性与选择方法。 模具排气点不合理,非但起不到排气效果,反而会造成产品变形或尺寸变化,所以模具排气点要合理。 选择模具排气点,应在产品最后走满胶的地方和产品困气烧的地方开排气。 8. 产品易脆裂的原因及解决方法。 产品易脆裂是产品使用水口料和次料太多造成产品易脆裂,或是料在料管内停留时间过长,造成胶料老化,使产品易脆裂。 增加新料的比例,减少水口料回收使用次数,一般不能超过三次,避免胶料在料管内长时间停留。 9. 加玻纤产品易出现泛纤的原因及解决方法 是由于熔胶温度低或模具温度低,射胶压力不足,造成玻纤在胶内不能与塑胶很好的结合,使纤泛出。 加高熔胶温度,模具温度,增大射胶压力。 10. 进料口温度对产品的影响。 进料口温度的过高或过低,都会造成机器回料不稳定,使加料量不稳定,而影响产品的尺寸和外观。 11. 透明产品有白点的原因及解决方法。 透明产品有白点是因为产品内进入冷胶造成,或料内有灰尘造成的。 提高射嘴温度,加冷料井,原料注意保存,防止灰尘进入。 12. 什么是注塑机的射出能力? 射出能力※※=射出压力(kg/cm2)×射出容积(cm3)/1000 13. 什么是注塑机的射出马力? 射出马力PW(KW)=射出压力(kg/cm2)×射出率(cm3/sec)×9.8×100% 14. 什么是注塑机的射出率? 射出率V(cc/sec)=p/4×d2×g
冲裁件常见缺陷及其原因分析
冲裁件常见缺陷及其原因分析 冲裁件常见的缺陷有:毛刺、制件表面翘曲不平,尺寸精度超差等。 ㈠毛刺 在冲裁加工中,产生不同程度的毛刺,一般来讲是很难避免的。其影响因素有以下几方面。 ⒈间隙 冲裁间隙过大、过小或不均匀,均可产生毛刺。造成间隙过大、过小和不均匀的因素有: ⑴模具工作部分的尺寸精度不符合冲模图纸的规定。 ⑵凸模或凹模有反梢(反锥),使冲裁过程中的间隙发生了变化。 ⑶导向部分间隙大。如导柱与衬套的配合间隙或斜楔冲裁的导向板间间隙过大均能引起冲裁过程中间隙的变化。 ⑷装配误差。如凸模与凸模固定板装配垂直,或者凸模与固定板孔配合部分已磨损,或者是固定凸模或凹模位置的定位销位置不准,都会造成凸模与凹模相对位置发生偏差而使间隙不均。 ⑸安装误差。如冲模上下底板表面在安装时未擦干净,或上模螺钉紧固不当而引起工作部分倾斜。 ⑹冲模结构不合理。如冲模或冲模工作部分刚度不够,在冲裁过程中发生变形而影响间隙的变化。或者缺乏用以抵消在冲裁过程中产生侧向力的反侧压块,使工作部分产生了相对移位。 ⑺压力机导轨间隙过大,滑块底面与工作台的平行度不好,或者滑块的运动方向与压床台面的垂直度不好。 ⑻板料的瓢曲度大,在冲裁过程中,使直径较小的凸模发生倾斜。 ⒉刃口钝 磨损或啃伤冲件。 ⒊定位高度不当 修边冲孔时,如果制件深度低于定位高度时,在冲裁过程中,制件形状与刃口就会不服贴而产生毛刺。 ⒋模具结构不当 由于缺乏必要的压料装置,在单面冲裁时,尤其是厚板在冲裁过程中会产生较大的拉应力,使金属纤维伸长并拉断,导致冲裁裂面粗糙,出现较大的毛刺。 毛刺的产生,不仅在以后的变形工序容易引起开裂,而且给板料分层和送料造成困维,并加剧刃口磨损,降低模具的使用寿命以及产生铆接间隙或焊穿、焊不牢等缺陷。毛刺还会在生产和使用过程中划伤操作者,威胁人身安全。如果在制件上已经出现了允许范围外的毛刺,就应当予以消除。消除毛刺的方法最常用的是滚光。
MoldFlow软件翘曲分析及应用
MoldFlow软件翘曲分析及应用Analysis and Application of W arpage with MoldFlow Software 文劲松麻向军 (华南理工大学聚合物新型成型装备国家工程中心SCUT—MoldFlow高级技术应用培训中心)一翘曲产生的原因 1 翘曲分类 Moldflow MPI/WARP模块把翘曲分为两种形 式,见图1。 1)稳定翘曲(图1a):翘曲变形与收缩应变成正 比。 2)非稳定翘曲(图1b):翘曲变形是由于制品弯 曲而产生的。在这种情况下,收缩应变表现为平面应(a) 稳定翘曲(b) 非稳定翘曲变,由于平面应变过大导致制品失稳而弯曲。一般,图1 翘曲分类 这种翘曲变形很大。 2 翘曲产生的原因 注塑过程中,翘曲是由于制品收缩率不均匀而产生的。收缩率不均匀表现在以下几方面:1)制品不同部位的收缩率不一样; 2)沿制品厚度方向收缩率不同; 3)与分子取向平行和垂直方向的收缩率不同。 MPI/W ARP把翘曲产生的原因归结为以下三点: 1)冷却不均匀; 2)收缩不均匀; 3)分子取向不一致。 因此,MPI/W ARP模块的主要目的是确定制品翘曲变形的结果是否满足设计要求,如果不能满足设计要求,给出产生翘曲的主要原因。 二翘曲分析步骤 1 分析流程的确定 进行翘曲分析之前,冷却、流动分析必须已经完成。在选择分析流程时(菜单命令Analysis下的Set Analysis Sequence命令),有两种分析流程Cool - Flow - Warp (简称CFW)和Flow - Cool - Flow - Warp (简称FCFW)。CFW在进行冷却分析时假设熔体的前沿温度
翘曲及处理
翘曲是指注塑制品的形状偏离了模具型腔的形状,它是塑料制品常见的缺陷之一。随着塑料工业的发展,人们对塑料制品的外观和使用性能要求越来越高,翘曲变形程度作为评定产品质量的重要指标之一也越来越多地受到模具设计者的关注与重视。模具设计者希望在设计阶段预测出塑料件可能产生翘曲的原因,以便加以优化设计,从而提高注塑生产的效率和质量,缩短模具设计周期,降低成本。 一.模具的结构对注塑制品翘曲变形的影响 1.浇注系统的设计 注塑模具浇口的位置、形式和浇口的数量将影响塑料在模具型腔内的填充状态,从而导致塑件产生变形。 流动距离越长,由冻结层与中心流动层之间流动和补缩引起的内应力越大;反之,流动距离越短,从浇口到制件流动末端的流动时间越短,充模时冻结层厚度减薄,内应力降低,翘曲变形也会因此大为减少。大型平板形塑件,如果只使用一个中心浇口或一个侧浇口,因直径方向上的收缩率大于圆周方向上的收缩率,成型后的塑件会产生扭曲变形;若改用多个点浇口或薄膜型浇口,则可有效地防止翘曲变形。 当采用点浇进行成型时,同样由于塑料收缩的异向性,浇口的位置、数量都对塑件的变形程度有很大的影响;实验表明,浇口位置具很重要,但并非浇口数目越多越好。 另外,多浇口的使用还能使塑料的流动比(L/t)缩短,从而使模腔内物料密度更趋均匀,收缩更均匀。同时,整个塑件能在较小的注塑压力下充满。而较小的注射压力可减少塑料的分子取向倾向,降低其内应力,因而可减少塑件的变形。 2.冷却系统的设计 在注射过程中,塑件冷却速度的不均匀也将形成塑件收缩的不均匀,这种收缩差别导致弯曲力矩的产生而使塑件发生翘曲。 如果在注射成型平板形塑件时所用的模具型腔、型芯的温度相差过大,由于贴近冷模腔面的熔体很快冷却下来,而贴近热模腔面的料层则会继续收缩,收缩的不均匀将使塑件翘曲。因此,注塑模的冷却应当注意型腔、型芯的温度趋于平衡,两者的温差不能太大。 除了考虑塑件内外表面的温度趋于平衡外,还应考虑塑件各侧的温度一致,即模具冷却时要尽量保持型腔、型芯各处温度均匀一致,使塑件各处的冷却速度均衡,从而使各处的收缩更趋均匀,有效地防止变形的产生。因此,模具上冷却水孔的布置至关重要。在管壁至型腔表面距离确定后,应尽可能使冷却水孔之间的距离小,才能保证型腔壁的温度均匀一致。同时,由于冷却介质的温度随冷却水道长度的增加而上升,使模具的型腔、型芯沿水道产生温差。因此,要求每个冷却回路的水道长度小于2m。在大型模具中应设置数条冷却回路,一条回路的进口位于另一条回路的出口附近。对于长条形塑件,应采用均行冷却回路,减少冷却回路的长度,即减少模具的温差,从而保证塑件均匀冷却。 3.顶出系统的设计 顶出系统的设计也直接影响塑件的变形。如果顶出系统布置不平衡,将造成顶出力的不平衡而使塑件变形。因此,在设计顶出系统时应力求与脱模阻力相平衡。另外,顶出杆的截面积不能太小,以防塑件单位面积受力过大(尤其在脱模温度太高时)而使塑件产生变形。顶杆的布置应尽量靠近脱模阻力大的部位。在不影响塑件质量(包括使用要求、尺寸精度与外观等)的前提下,应尽可能多设顶杆以减少塑件的总体变形。 用软质塑料来生产大型深腔薄壁的塑件时,由于脱模阻力较大,而材料又较软,如果完全采用单一的机械式顶出方式,将使塑件产生变形,甚至顶穿或产生折叠而造成塑件报废,如改用多元件联合或气(液)压与机械式顶出相结合的方式效果会更好。 二.塑化阶段对制品翘曲变形的影响
带钢在连续退火过程中的板形屈曲变形原因分析
带钢在连续退火过程中的板形屈曲变形原因分析 张清东 刘 周晓敏(北京科技大学机械工程学院,北京100083) 邹玉贤 黄夏兰 彭 俊 (宝钢股份公司冷轧厂) 【摘要】 现场跟踪发现,带钢经过连续退火炉的板形变化复杂多样,而且其程度不亚于轧制过程。为此运用带钢的板形屈曲及后屈曲理论,分析了退火炉内高温态下带钢的板形屈曲临界条件,结合板形生成理论,指出退火炉内带钢板形发生变化的原因和主要相关因素。 【关键词】 连续退火 带钢 板形 屈曲/后屈曲 RESEARCH ON STRIP PROFI L E BUCK LING DEFORMATION D URING CONTINUOUS ANNEALING PROCESS Zhang Qingdong Liu Y unyun Zhou X iaomin (Mechanical Engineering School,UST Beijing) Z ou Y uxian Huang X ialan Peng Jun (Baoshan Iron&Steel C o.,Ltd.) 【Abstract】 According to the examining data from a C AP L in Baosteel,the strip shape varied com plicatedly and markedly while passing through the continuous annealing furnace,nearly to the extent of the rolling process.The buckling criteria of the strip profile deformation at high tem perature in the continuous annealing furnace was analyzed by the theories of strip buckling and post2buckling;the reas on and correlative influencing factors of the strip shape variation in continuous annealing furnace were presented on the basis of the shape creation principle. 【K ey Words】 C ontinuous Annealing,Strip,Shape,Buckling/P ost2Buckling 1 引言 连续退火机组集带钢的清洗、退火、平整、精整等工艺于一体,具有生产效率高、成本低、质量高、品种多样化等许多优点。但生产中经常出现带钢经过退火炉时板形从一种浪形形态变为另一种完全不同甚至相反的浪形形态,变化复杂多样且显著,对板形控制和生产稳定都构成严重挑战。 2 带钢板形变化现场跟踪 在现场跟踪了某连续退火机组生产的大量钢卷,通过分类统计定量说明这种板形变化的普遍、剧烈和大致规律[1]。 带钢从连续退火炉前到炉后的板形变化的分类统计见表1,从中可以看出各种规格的带钢在连续退火机组炉前炉后板形的对应性较差,能对应的只占总体的4719%,确存在板形的大小和形态的明显变化。 表1 炉前后板形变化与浪形关系概率 板形变化类型概率塑性延伸部位概率 浪形一致719%无局部塑性延伸4719% 双边浪变平 平变中浪 1215% 1014% 带钢中部2219% 单边浪变平 单边浪换侧 412% 1215% 带钢单侧边部1617% 中浪变平 中浪变边浪 613% 613% 带钢双侧边部1216% 根据数据统计和分析,带钢板形在退火炉发生了永久变化,也即带钢在退火炉中可能发生了塑性变形,尤其是局部宽度的塑性拉伸变形,见表1;此机组退火炉中存在着能使带钢板形发生变化的因素和力学过程,而且其变形较常温态板形屈曲更为复杂。 第27卷 第4期上 海 金 属V ol127,N o14 27 2005年7月SH ANG H AI MET A LS July,2005
塑料制品的翘曲变形分析
一、引言 翘曲变形是指注塑制品的形状偏离了模具型腔的形状,它是塑料制品常见的缺陷之一。随着塑料工业的发展,人们对塑料制品的外观和使用性能要求越来越高,翘曲变形程度作为评定产品质量的重要指标之一也越来越多地受到模具设计者的关注与重视。模具设计者希望在设计阶段预测出塑料件可能产生翘曲的原因,以便加以优化设计,从而提高注塑生产的效率和质量,缩短模具设计周期,降低成本。 本文主要对在注塑模具设计过程中影响注塑制品翘曲变形的因素加以分析。 二、模具的结构对注塑制品翘曲变形的影响 在模具设计方面,影响塑件变形的因素主要有浇注系统、冷却系统与顶出系统等。 1.浇注系统的设计 注塑模具浇口的位置、形式和浇口的数量将影响塑料在模具型腔内的填充状态,从而导致塑件产生变形。 流动距离越长,由冻结层与中心流动层之间流动和补缩引起的内应力越大;反之,流动距离越短,从浇口到制件流动末端的流动时间越短,充模时冻结层厚度减薄,内应力降低,翘曲变形也会因此大为减少。图1为大型平板形塑件,如果只使用一个中心浇口(如图1a所示)或一个侧浇口(如图1b所示),因直径方向上的收缩率大于圆周方向上的收缩率,成型后的塑件会产生扭曲变形;若改用多个点浇口(如图1c所示)或薄膜型浇口(如图1d所示),则 可有效地防止翘曲变形。 a)中心浇口 b) 侧浇口 c)多点浇口 d) 薄膜型浇口 图 1 浇口形式对塑料件变形的影响 当采用点浇进行成型时,同样由于塑料收缩的异向性,浇口的位置、数量都对塑件的变形程度有 很大的影响。图2为一箱形制件在不同浇口数目与分 布下的试验图。 a)直浇口 b)10个点浇口 c)8个点浇口 d)4个点浇口 e) 6个点浇口 f) 4个点浇口 图2 实验浇口的设置 由于采用的是30%玻璃纤维增强PA6,而得到的是重量为4.95kg的大型注塑件,因此沿四周壁流动方向上设有许多加强肋,这样,对各个浇口都能获得充分的平衡。实验结果表明,按图f设置浇口具有较好的效果。但并非浇口数目越多越好。实验证 注塑制品的翘曲变形分析
MDF板件翘曲变形原因分析
MDF板件翘曲变形原因分析 在板式家其制造中,保证板件平整不翘曲变形是十分重要的。但是在用MDF刨花板等人造板制造板式家具中要完全避免翘曲变形却不是一件容易的事。笔者曾对温州地区的几家家具公司就MDF在家具制造中出现的翘曲变形问题进行了调查,试图找出翘曲变形的原因及防治的办法。 被调查的几家家具公司均采用在MDF上贴薄叶纸(30g/m2)后进行涂饰的加工工艺。MDF来源比较广, 广东产、福建产、江苏产、上海产、黑龙江产的MDF都用过。几家公司都出示了已变形的柜门、搁板、床帮、柜顶板、镜板、电视线压条等部件,要求探明翘曲变形的原因。笔者详细询问和考察了各公司加工工艺: MDF板件存放情况及所用MDF的情况。认为板件翘曲变形的原因主要有几下几个方面。 (一)MDF未经调质处理,含水率偏低。温州地区属海洋性气候,空气湿度较大,MDF的平均含水率相应也较高,但所使用的MDF含水率都偏低。人造板厂在制造MDF过程中,MDF出热压机时含水率一般都偏低,表层仅2-3%,芯层仅6-7%。低含水率的MDF在相对湿度较大的环境中加工或存放,必然会吸湿,如板内存在含水率不均等问题,板件便容易产生翘曲变形。有一家企业反映,从广东购进的MDF,运至温州,在使用过程中还有一定温度,尚未完全冷却。这些板在加工过程中极易吸湿变形,但放久了又会渐趋平整。为防止变形,MDF在使用前应进行调质处理, 使其含水率均匀化,并提高到8%左右。调质处理可以在人造板厂进行,也可在家具制造板厂进行。但一般如家具制造厂对MDF的含水率提出明确要求的话,人造板厂将提供进行调质处理过的MDF。 (二)板件未采用二面对称的加工工艺,板件结构不对称。 据了解,几家家私公司对家具的主要部件如柜门、台面、床帮等的正面都采用了比较精细的加工工艺,MDF基材先进行处理(精砂、封纸、涂底漆、砂光)然后再购薄叶纸,贴纸后再进行涂饰处理(二道底漆、干砂、水砂、一道面漆),涂饰后表面平滑,光亮如镜,但背面一般只进行简单的封底处理,或即使贴薄叶纸,涂饰的道数也相应减少,背面能观察到明显的纤维吸湿膨胀的痕迹。有的公司把镜子与MDF直接粘合在一起,造成镜子破碎或镜板严重变曲变形。以上这样处理的板件由于其正反二面对空气中湿气的吸湿能力不同,吸湿速度不同,而极易造成板件的变形。因此板件在贴面和涂饰加工中要注意二面对称,使其结构对称、平衡, 这很重要的。二种性能完全不同的材料,如镜子和MDF不能采用胶合的方式复合,应采用螺钉结合,并留有伸缩余地。 (三)MDF密度偏低 MDF的密度偏低造成加工面不光滑,且易吸湿变形,一般用于家具制造的MDF密度在厚度方向的分布应均匀,表芯层密度差异过大的MDF不适宜做家具,平均密度在0.75g/m3左右比较合适。 (四)MDF防水性较差 用于家具制造的MDF应具有一定的防火性能,否则易吸湿变形。通常MDF的防水性能以吸水厚度膨胀率来表示,用于家具制造的MDF的吸水厚度膨胀率应小于6%较为合适。(五)贮存条件较差 MDF基板或板件应平整堆放,不能竖放,而且应存放在干燥通风的环境中,如存放在潮湿的环境中则易吸湿变形,甚至发霉。